Mastering APCP: A Detailed Step-by-Step Guide
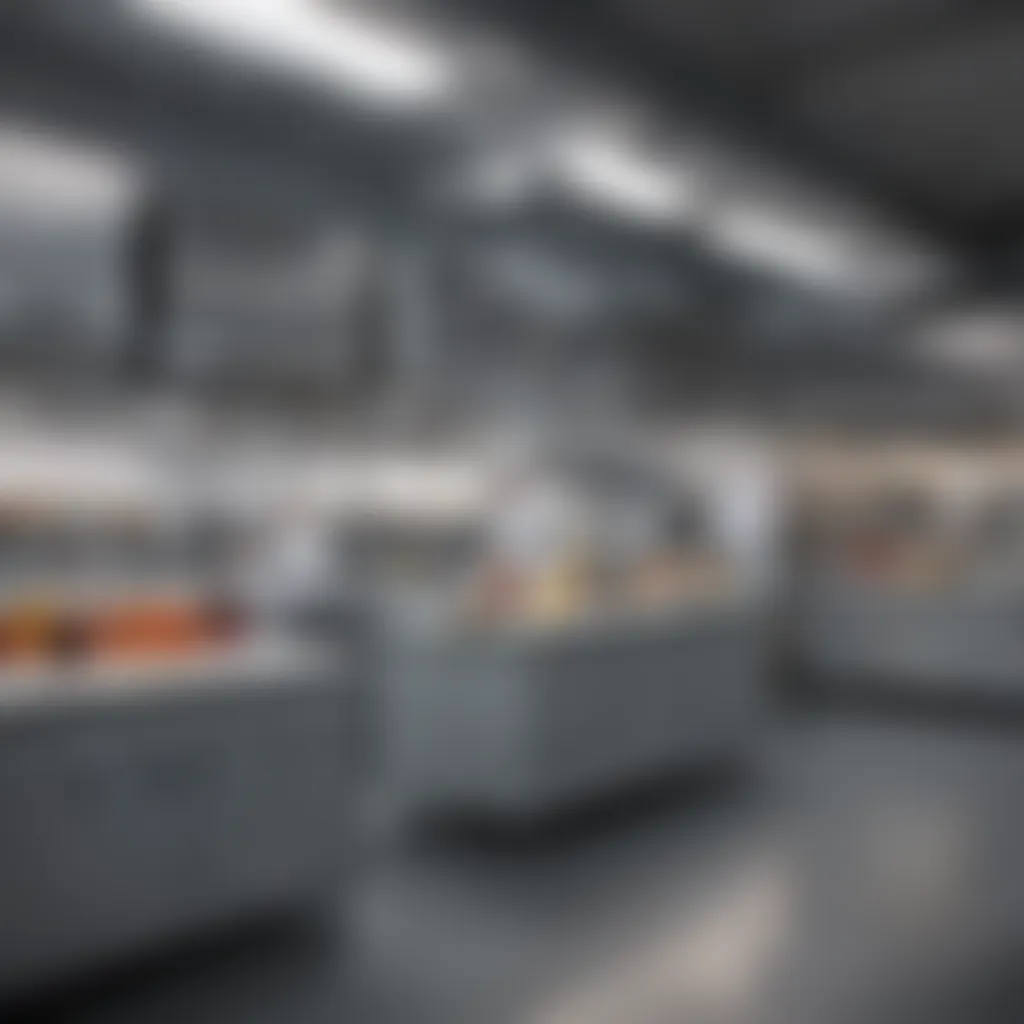
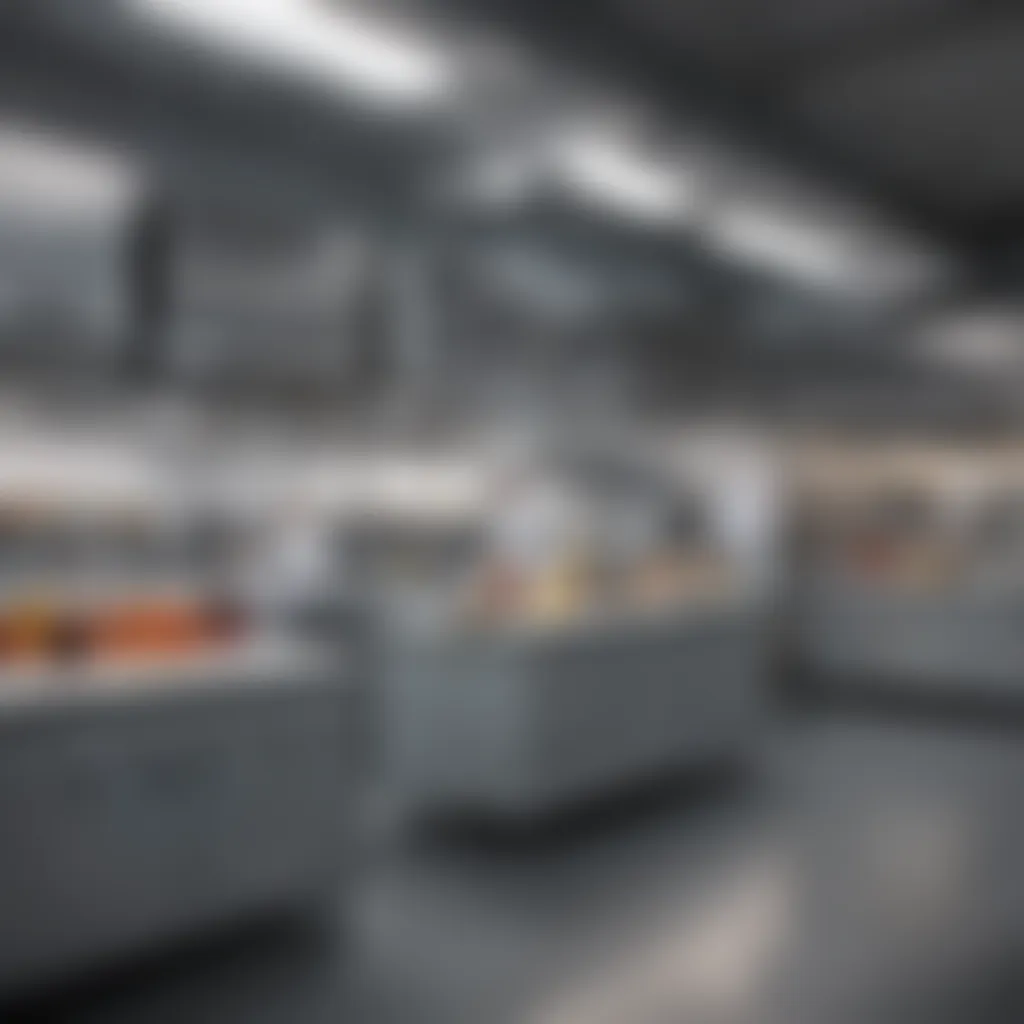
Intro
In todayās complex and rapidly evolving landscape of industry, crafting Advanced Process Control Procedures (APCP) is no trivial task. Yet, it's a vital skill for anyone looking to optimize operations and enhance efficiency. This guide is tailored for those who cherish practical knowledge, especially homemakers who might find themselves navigating this intricate domain.
Understanding APCP isn't just about theoretical concepts; itās about applying the right knowledge at the right time. As you embark on this journey, itās important to remember that each step lays the groundwork for the success of the subsequent stages, ensuring smooth operation from initial analysis to full implementation.
Letās begin to peel the layers of this multifaceted process, unraveling each component required for effective execution.
Ingredients:
Crafting a robust APCP involves several key ingredients, much like preparing a gourmet dish. Below is a concise list of essential components:
- Objective Statement: Clearly defined goals.
- Process Maps: Diagrammatic representation of processes.
- Data Collection Methods: Techniques for gathering data.
- Control Strategy: Outline of the control mechanisms to be employed.
- Training Materials: Resources for personnel education.
- Validation Criteria: Benchmarks for measuring success.
Preparation Steps:
With the ingredients at hand, itās time to prepare. Hereās a breakdown of the crucial steps to undertake:
- Define Objectives: Establish clear objectives that align with overall operational goals.
- Map Processes: Create detailed process maps to visualize each step involved.
- Choose Data Collection Methods: Select suitable methods for data gathering, considering variations in process demands.
- Design Control Strategy: Identify the strategies for process control tailored to your specific needs.
- Develop Training Materials: Create educational materials for training the relevant personnel.
- Set Validation Criteria: Develop criteria that will help assess the effectiveness of your APCP.
Technical Aspects:
Here, we dive into the nitty-gritty details that ensure a successful create and execution of APCP:
- Temperature Settings: Depending on your specific processes, adjust temperature as necessary for optimal performance.
- Timing Specifics: Each step should have outlined time duration. For instance, monitor processes regularly and be ready to adapt.
- Critical Techniques: Understanding the nuances of statistical methods can elevate control strategies significantly.
Cooking Process:
Just like cooking, the implementation of APCP involves a precise sequence of steps:
- Implementation of Process Maps: Begin by putting the visual maps into action, ensuring all roles in the organization are clear.
- Data Collection Phase: Gather data systematically, adhering closely to your established methods.
- Implement Control Strategy: Apply your control strategies, monitoring them through the process.
- Train Personnel: Conduct regular training sessions to familiarize all involved with the procedures and equipment.
- Validation and Assessment: At predetermined intervals, validate your methods against the set benchmarks.
Troubleshooting Tips:
Even with a meticulous plan, bumps can occur along the road. Here are some common pitfalls to avoid:
- Insufficient Data Collection: If data is missing or inadequate, results can be skewed. Always double-check your data inputs.
- Undervaluing Training: Never underestimate the importance of personnel training. Continuous education is crucial.
- Ignoring Validation Steps: Skipping validation can lead to blind spots. Regularly reassess and refocus on your validation criteria.
Remember: A successful APCP evolves over time. Be adaptive and open to refining your strategies as you learn more about your processes.
Preamble to Advanced Process Control Procedures
In todayās fast-paced industrial landscape, the mastery of Advanced Process Control Procedures (APCP) stands out as a critical competency. The significance of this topic cannot be overstated; it forms the backbone of efficient operations in various sectors, including manufacturing, chemical processing, and even food production. The relevance of a well-crafted APCP is not only in optimizing processes but also in ensuring safety and compliance with industry standards.
Defining Advanced Process Control
Advanced Process Control (APC) consists of sophisticated techniques employed to control processes more effectively than traditional methods. While standard control systems may suffice for basic operations, they often lack the adaptability required for complex or variable processes. APC encompasses a range of methodologies, including model predictive control, fuzzy logic, and adaptive control. These are crafted to react, preemptively adjust, and optimize process variables, leading to improved throughput and reduced waste.
A simple analogy can make this clearer: think of standard control systems like a basic thermostat in a home. It turns the heat on or off at fixed intervals. In contrast, APC is like a smart thermostat that learns patterns and adjusts the temperature in real time based on your activities and preferences. This level of sophistication allows facilities to respond to fluctuations and maintain a consistent output under varying conditions.
Importance of APCP in Industry
The role of APCP in industry is similar to having a well-oiled machine; it ensures smooth and efficient operation while reducing the chance of errors and downtime. Here are some critical points to consider:
- Improved Efficiency: By optimizing the control strategy, APC reduces variability in production processes, leading to significant boosts in output.
- Cost Reduction: Better control translates into less waste and lower energy consumption, which are vital for improving the bottom line.
- Increased Safety: Controlling process dynamics accurately minimizes the likelihood of accidents, protecting not only the equipment but also the workforce.
- Regulatory Compliance: Industries often face strict regulations. APCP helps maintain standards needed to comply with various environmental and safety regulations.
"Without the art of control, production tends to operate at the mercy of uncontrollable variables."
Foundational Concepts of APCP
In the realm of Advanced Process Control Procedures (APCP), a strong foundation is paramount. It is akin to constructing a house; without a solid base, the walls will surely crumble. Understanding the foundational concepts of APCP equips professionals with the necessary tools to develop and maintain effective control strategies. This segment will explore the key elements of APCP while shedding light on how it diverges from traditional control methods. This understanding is not just beneficial; it's critical for achieving sustained operational efficiency.
Key Elements of APCP
A look into the key elements of APCP reveals what makes it effective and efficient:
- Process Models: At the heart of APCP lies mathematical and simulation models that represent real-world processes. These models enable a precise understanding and prediction of system behavior under various conditions. It's like having a map; it guides decisions and operations.
- Control Algorithms: These are the rules or mechanisms used to maintain system performance. By utilizing algorithms, one can automate decision-making processes that ensure the desired outcomes are met.
- Feedback Loops: Feedback systems are essential in APCP. They monitor outputs and compare them to desired results, enabling necessary adjustments to be made in real time. Think of it as a thermostat in your home; it keeps everything in check without constant oversight.
- Data Analysis: In todayās data-driven world, analyzing feedback data is crucial. It is here that one finds trends, identifies issues, and stipulates improvement areas. Having a robust way to dissect this information provides a clearer picture of overall performance.
"The ability to analyze data and adapt processes accordingly is where operational excellence thrives."
- Human Element: While technology drives APCP, the role of human operators remains indispensable. Their insights and experiences can interpret data that a machine may not fully grasp. Hence, fostering a culture that leverages both technological and human strengths is vital.
Understanding each of these elements allows professionals to craft effective APCPs. They must see how these elements interconnect, which ultimately ensures a smooth operational flow.
Differentiating APCP from Traditional Control Methods
It often seems like comparing apples to oranges when discussing APCP versus traditional control methods. While both aim for optimal process performance, the approaches are markedly different:
- Proactivity vs. Reactivity: Traditional methods often react to process disruptions post-incident, while APCP takes a proactive stance, anticipating changes and acting before problems manifest.
- Complexity Handling: APCP is designed to handle more complex and nonlinear processes. Traditional methods might struggle with intricate interdependencies, leaving gaps that APCP can bridge with ease.
- Automation Levels: The automation in APCP is significantly higher, utilizing algorithms that can operate independently. In contrast, traditional approaches may require more manual inputs for adjustments.
- Performance Metrics: APCP emphasizes continuous improvement tracking through specific and measurable performance metrics, leading to better adaptive strategies over time. Traditional methods may not place the same level of scrutiny on metric-driven performance.
This differentiation emphasizes the importance of embracing APCP as a modern solution for achieving operational efficiency. It's not merely about control; it's about mastering the dynamics of processes and leveraging them for optimum results. Employing these advanced methods creates a direct pathway to operational excellenceātransforming challenges into opportunities.
The Role of Data in Crafting APCP
When it comes to Advanced Process Control Procedures, data acts like the butter in a finely tuned biscuitāessential for cohesion and flavor. Without proper handling of data, your efforts in crafting APCP can crumble like a cookie left in the rain. This section delves into the vital role data plays in both the formulation and successful execution of APCPs.
Data is the bedrock on which you build control strategies. It encompasses everything from raw measurements obtained from processes to the analytics that inform decision-making. In the realm of APCP, data not only highlights existing issues but also points towards possible enhancements. Good data helps organizations set benchmarks, recognize trends, and establish clear performance metrics, steering operations towards excellence.
Data Collection Techniques
Every feast starts with ingredients, and data collection is where you gather those ingredients. A variety of techniques can be utilized, depending on the specifics of the industrial environment.
- Sensor-Based Measurement: This is akin to having an honest friend who tells you what's happening in real-time. By deploying sensors that track various variables like temperature, pressure, and flow rate, you can gather crucial data continuously.
- Surveys and Questionnaires: Just like family recipes, sometimes itās best to ask how things are going. Engaging personnel through surveys can surface insights that raw numbers may miss. This qualitative data complements the quantitative data for a more rounded view.
- Historical Data Analysis: Think of this as using grandmaās recipe to perfect your new dish. Historical data offers valuable insights into past performance trends that can inform current decision-making. By evaluating archived information, you see patterns of behavior.


Utilizing a mix of these techniques can provide a comprehensive data set that not only serves to initiate the crafting of APCP, but enriches it with deeper insights.
Data Quality Assurance
Once youāve gathered your data, the next step is to ensure itās fit for consumption. Data quality assurance resembles sifting flour for lumps; if you donāt do it, your final product might have those unwanted bits spoiling the texture.
- Data Accuracy: First and foremost, the data needs to be accurate. If your sensors are off by a degree, the entire APCP could be jeopardized. Regular calibration of measuring devices is necessary to maintain this accuracy.
- Data Integrity: Another aspect to keep in mind is the integrity of the data. You need to ensure that your data isnāt tampered with or corrupted. Encryption and access controls can help protect sensitive information from unauthorized changes.
- Regular Audits: This is like routinely checking the pantry for expired goods. Periodic reviews of data collection processes and data itself will help identify any discrepancies or areas needing improvement.
In summary, the role of data in crafting a successful APCP cannot be understated. Implementing scrupulous data collection techniques coupled with rigorous quality assurance will pave the way for effective process control, minimizing errors and maximizing efficiency.
"Without data, you're just another person with an opinion."
Data-driven decisions steer you clear of guesswork and into a realm where performance enhances and evolves continuously. It's the silent player that informs every aspect of your Advanced Process Control Procedures.
Analyzing Process Dynamics
Analyzing process dynamics is the bedrock for anybody wanting to get their head around Advanced Process Control Procedures (APCP). Without diving into the nitty-gritty of how processes behave under various conditions, itās like trying to bake a cake without knowing how the ingredients interact. It doesn't matter if it's a high-performance manufacturing setup or a more traditional process; understanding the dynamics can make a world of difference in optimizing operations.
The heart of process dynamics lies in the relationships between variables. By dissecting these interactions, one gains valuable insights into how changes can influence the system as a whole. This analysis helps in identifying potential bottlenecks and inefficiencies that might otherwise go unnoticed. Moreover, being aware of these factors can also lead to better decision-making when it comes time to implement control strategies.
Identifying Key Variables
This step involves pinpointing the various parameters that affect your process. You might ask, what are these variables? They could include things like pressure, temperature, and flow rates, among others. Each of these elements plays a vital role in determining the end product's quality. If you're operating in, say, the food industry, then understanding how temperature affects flavor during cooking is crucial. Similarly, in a chemical plant, knowing how pressure variations can affect reactions can save a lot of headaches.
When identifying these key variables, consideration should be given to historical data as well. For instance, doing a quick analysis of past performance can shed light on which variables have the most significant effect on the overall process dynamics. Hereās a handy little checklist you might consider:
- Gather Data: Historical records can provide invaluable insights.
- Consult Stakeholders: Engaging with multidisciplinary teams can unearth seldom-discussed factors.
- Monitor Trends: Keep an eye on the changes over time to understand relationships better.
"To capture the essence of dynamic processes, one must first embrace complexity before simplifying it."
Understanding Process Behavior
Understanding how processes behave means looking at patterns and trends that emerge over time. Itās akin to being an observer of nature; you begin to notice variables interacting in unique ways. By analyzing this behavior, you can spot potential issues before they escalate into significant problems. This proactive approach can be particularly beneficial in avoiding unscheduled downtimes or product defects.
One effective method to grasp process behavior is through the use of simulation models. These models allow you to visualize how changes will affect different variables. By tweaking one element, you can forecast its repercussions throughout the entire system. Also, involving tools such as control charts or time series analysis can give a clearer picture of longtime patterns.
Additionally, consider the following:
- Feedback Loops: Understand how changes in one aspect can create a ripple effect.
- Stability Assessment: Determine if the system operates within acceptable limits.
- Response Characteristics: Pay attention to how quickly or slowly the process reacts to changes.
In summary, diving deeper into the dynamics at play in any process not only enhances your understanding but also lays the groundwork for informed decision-making. By identifying key variables and understanding their behaviors, you prepare yourself to design a more effective APCP that stands the test of time.
Modeling for APCP
In the realm of Advanced Process Control Procedures (APCP), modeling is nothing short of a backbone ā it holds everything together. Letās face it; without an effective model, any attempt at creating an APCP is like sailing a ship without a map. Itās essential to grasp the specific nuances of process dynamics and leverage these insights to optimize operations effectively.
A well-constructed model serves multiple purposes: it helps clarify the relationships between various process variables, aids in forecasting outcomes, and supports the design of control strategies. Engaging with models not only clarifies expectations but also reduces the risk of costly errors down the line. Plus, it facilitates communication among team members, allowing them to share a common understanding of how the process behaves.
Types of Models Used in APCP
When it comes to modeling, one size definitely does not fit all. Hereās a peek into the common types of models utilized in APCP:
- Static Models: These are the simplest forms, representing systems at rest or average conditions. They provide a snapshot but lack the dynamic flavors required for most process control tasks.
- Dynamic Models: Unlike their static counterparts, dynamic models take into account time-based changes, capturing system behavior over time. These are critical in understanding how processes respond under varying conditions.
- Empirical Models: Derived from experimental data, these models identify patterns and relationships without delving into the underlying physics of the process. Theyāre often used when the system is too complex to model analytically.
- First Principles Models: This type harkens back to basic physics and chemistry principles, creating comprehensive equations that describe the process. These models are typically the most accurate but also the most challenging to develop.
Each model has its strengths and weaknesses, but the right choice largely depends on the specific context and goals of the APCP.
Model Validation Techniques
Now, just building a model isnāt enough; it must be validated. Ensuring that your model behaves in a way that mirrors reality is crucial. Validation techniques often include:
- Data Comparison: This involves comparing the modelās predictions against actual process data. If the model accurately predicts outcomes under various scenarios, itās likely on the right track.
- Sensitivity Analysis: By tweaking input variables within the model and observing changes in output, you can determine which variables have the most impact on overall behavior. This helps refine both the model and control strategies.
- Cross-Validation: Utilizing different sets of data to test the model helps assess its predictive power and robustness. This gives an extra layer of confidence.
- Peer Review: Getting a second (or third) pair of eyes can illuminate potential flaws in the model. Engaging experts to review and critique ensures that no stone is left unturned.
"Validating your model is not just a chore; it's an essential step to ensure your process won't go down the rabbit hole during implementation."
In essence, investing the time and resources into solid modeling and validation not only smooths the path for APCP development but also lays the groundwork for successful operational practices. With the demand for precision in process control ever-increasing, one must prioritize modeling as a fundamental aspect of crafting effective APCPs.
Control Strategies in APCP
When it comes to crafting Advanced Process Control Procedures (APCP), control strategies serve as the backbone of effective execution and optimization. These strategies not only facilitate the automated regulation of process variables but also enhance overall operational efficiency. By selecting and implementing the right control methods, organizations can maintain product quality, conserve energy, and minimize waste, which is increasingly crucial in todayās competitive landscape.
A proper understanding of control strategies allows stakeholders to make informed decisions that directly impact production performance. Therefore, it is essential to explore both general overviews of these strategies and the nuances of selecting the most appropriate ones for specific industry needs.
Overview of Control Strategies
Control strategies can be likened to the recipe that guides chefs in their kitchens. Just as different dishes require various ingredients and techniques, each process in industry needs tailored control strategies. Hereās a basic rundown of some predominant types of control strategies commonly employed in APCP:
- Feedback Control: This is the bread and butter of process control. It involves measuring the output, comparing it with a desired set point, and making necessary adjustments. For example, you might have a thermostat that regulates heat by reacting to temperature variations in a room.
- Feedforward Control: Unlike feedback, feedforward control anticipates changes to maintain stability. If a raw material's quality fluctuates, adjustments are made beforehand to prevent output variations. Think of it as cooking with fresh ingredients rather than stale, instead of waiting for the dish to turn sour.
- Cascade Control: This method involves multiple control loops, where the output of one controller becomes the input for another. This strategy allows for a more precise control of interdependent processes, much like managing various cooking temperatures for complex dishes.
"Understanding and choosing the right control strategy is analogous to knowing when to sautƩ, simmer, or bake. Each technique plays a significant role in achieving the perfect outcome."
Each of these strategies carries its own unique advantages and challenges. Thus, identifying the most fitting one for your particular application is exactly where the āartā in mastering APCP comes into play.
Selecting Appropriate Control Methods
Selecting control methods in APCP is akin to choosing the right tools for a craftāeach has its own merits and intended uses. Hereās a practical approach to aid in this selection:
- Assessment of Process Dynamics: Understanding the behavior of your process is crucial. Does it respond quickly or is it sluggish? Knowing these characteristics will help in choosing a control strategy that complements the processās dynamics.
- Determining Control Objectives: Establish clear objectives. Are you looking to minimize variance, optimize throughput, or reduce costs? Different goals may necessitate different control approaches.
- Analyzing Costs and Benefits: Consider both the initial implementation costs and the long-term operational benefits. Sometimes the cheapest option upfront isnāt necessarily the most economical in the long run.
- Integration with Existing Systems: Whatever method you choose should seamlessly integrate with current systems. If adopting a new blend of control methods complicates existing processes, it may lead to inefficiencies.
- Consulting Expertise: Sometimes it pays to get a second opinion or even a third. Involving professionals with a wealth of experience can shed light on previously overlooked factors or techniques.
By following these steps, stakeholders can confidently select the appropriate control methods that align with their specific operational goals and constraints. Taking the time to make informed choices often pays off in enhanced operational efficiency and effective process management.
Step-by-Step Guide to Crafting an APCP
Creating an Advanced Process Control Procedure (APCP) stands out as a pivotal task in ensuring efficiency and effectiveness in industrial operations. This section aims to demystify the seemingly complex process of crafting an APCP into manageable chunks, guiding readers through each stage and clarifying why this structured approach pays off.
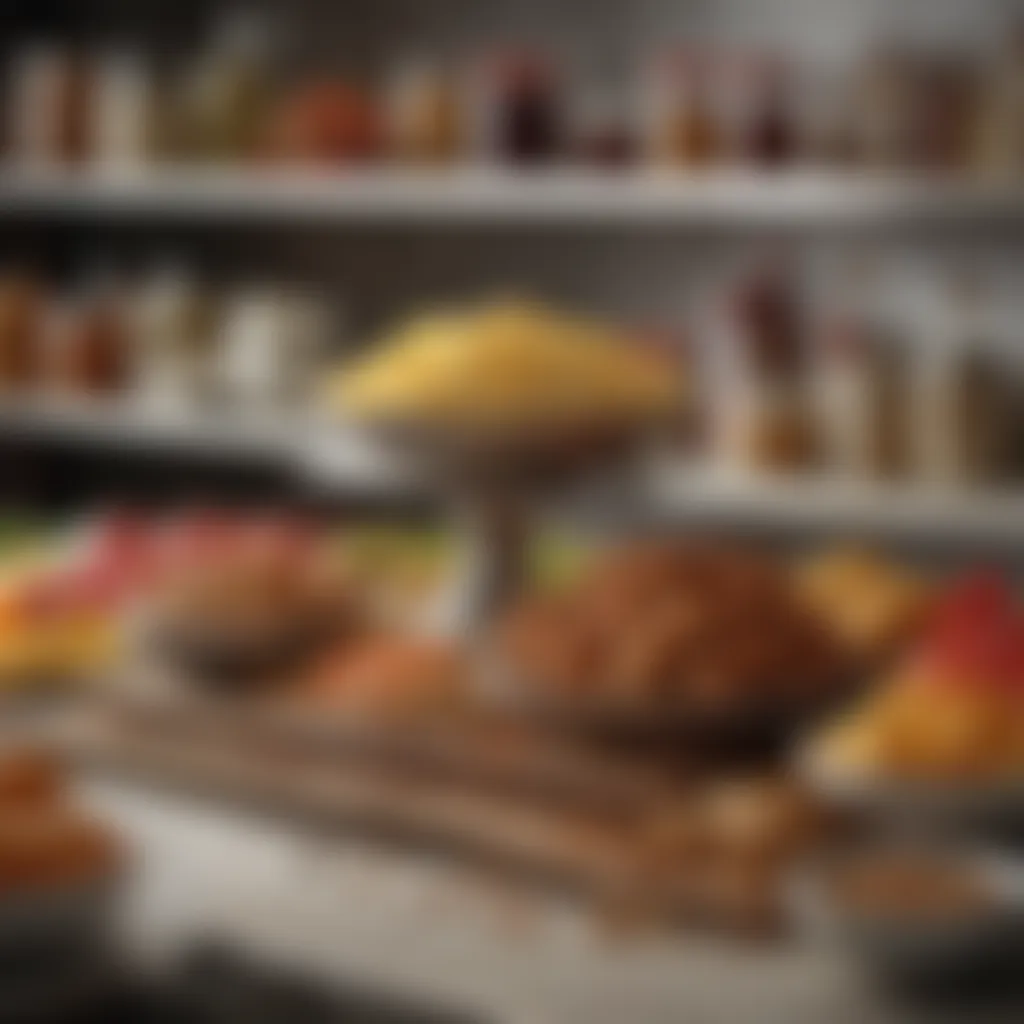
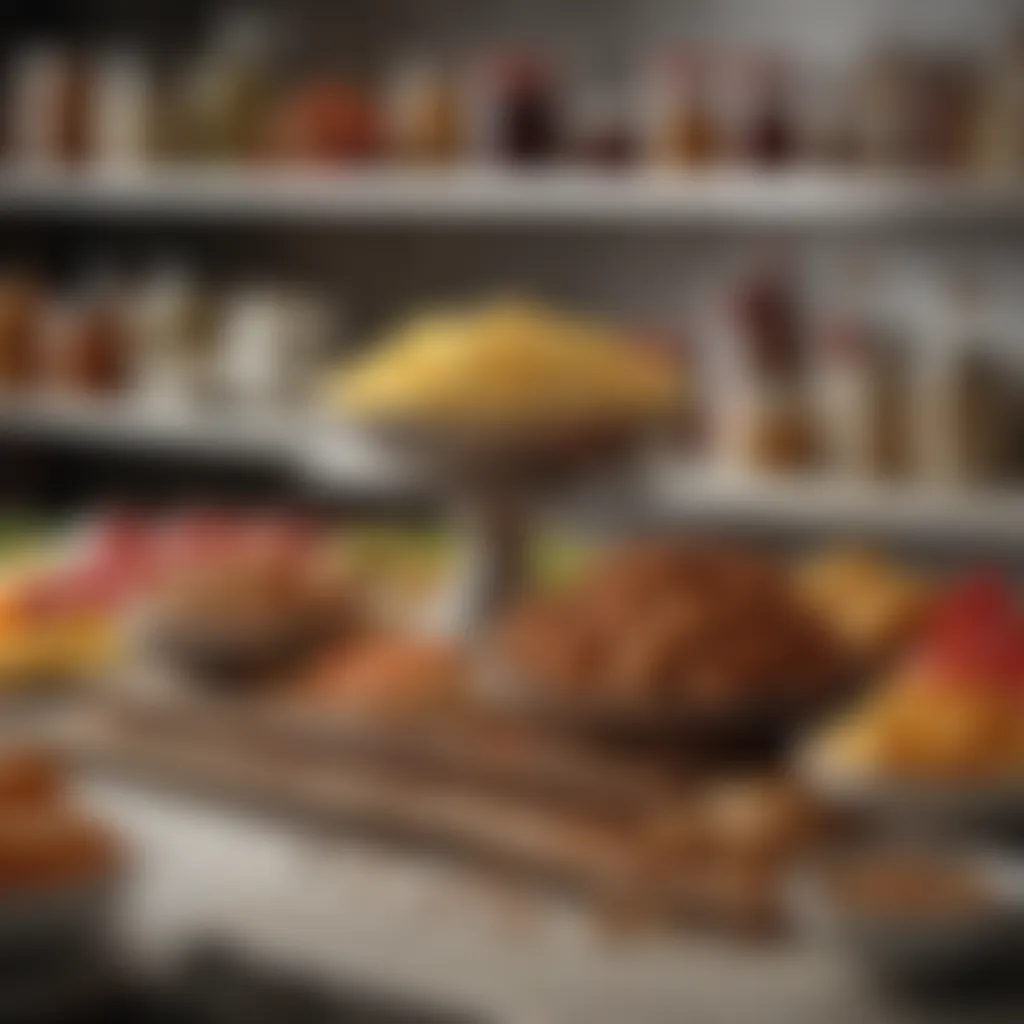
When businesses prioritize a step-by-step guide, they position themselves for success. A systematic methodology minimizes the chances of overlooking significant factors, leading to a more robust control system that enhances productivity and reduces costs. Moreover, such frameworks foster consistency, enabling teams of diverse backgrounds to operate using a shared understanding and strategy.
In the following subsections, weāll delve further into each of the critical steps, showcasing the importance of initiating the process properly, developing a solid framework, and testing the constructed APCP.
Initiating the Process
The initiation of an APCP is like laying the foundation for a house: if itās not right, the entire structure can come crashing down. Itās crucial to assess the current state of operations and understand the specific needs of the process at hand. Begin by gathering all stakeholders for discussion, ensuring every voice is heard. This could include engineers, operators, and management. The collective insights aid in pinpointing major areas that could benefit from advanced control strategies.
Also, take time to identify the goalsāwhat do you aim to achieve with the APCP? It could be anything from reducing overshoot in temperature controls to improving yield. Drafting clear objectives allows everyone to align their efforts towards a common purpose.
Key Considerations in Initiating
- Stakeholder Engagement: Donāt underestimate the value of collaboration. It nurtures a sense of ownership amongst the team.
- Goal Clarity: Establish Specific, Measurable, Achievable, Relevant, and Time-bound (SMART) objectives for the project.
- Preliminary Data Assessment: Look for existing data that might inform your strategy. It can save considerable time and resources.
Developing the APCP Framework
Once the groundwork has been laid, itās time to construct the APCP framework. This phase is where concepts are turned into tangible structures and processes, mapping out how the APCP will operate. A well-developed framework serves as a blueprint for the control procedures, detailing the essential components, such as feedback loops, control algorithms, and monitoring strategies.
Donāt forget to include contingency plans. You should develop protocols for unforeseen situations or discrepancies in data. Naturally, drafting a flexible framework allows you to pivot with changing conditions or new insights.
Important Elements of Framework Development
- Control Algorithms: Decide on the types of algorithms youāll employ, e.g., PID controllers.
- Feedback Mechanisms: Design processes for continuous data collection and analysis to identify performance against objectives.
- Documentation: Keep thorough records at every stage. Theyāll be indispensable for troubleshooting and future training.
Testing the APCP
With the APCP framework in place, the next step is testing. This phase is crucial. Testing ensures that your strategies function as intended under real-world conditions. Initial trials may reveal defects that can be resolved before rolling out full implementation.
Create a testing schedule and collect telemetry data to evaluate the effectiveness of the control strategies. It's wise to start small. Consider a pilot project that allows you to monitor performance without causing significant disruptions.
Testing Strategies
- Simulations: Run simulations of your APCP to predict performance prior to live testing.
- Iterative Testing: Allow for cycles of testing and revision. Each loop should refine the APCP based on observed outcomes.
- Feedback Analysis: Hold debrief sessions to analyze telemetry data and gather insights from team members.
"The journey of a thousand miles begins with one step." - Lao Tzu
Initiating the process with careful thought sets the course for success in APCP development.
In summary, crafting an APCP involves a series of focused steps that require joint effort, careful planning, and rigorous testing. By initiating the process effectively, developing a thorough framework, and conducting extensive tests, organizations can enhance their system's operational prowess in the competitive industrial landscape.
Implementation Considerations
Implementing Advanced Process Control Procedures (APCP) is a critical phase that can define the success or failure of an operation. Without careful thought into how these procedures will fit within an organization, even the best-designed plans can fall flat. Key considerations during implementation can greatly enhance both efficiency and effectiveness. Understanding organizational readiness and the need for training and support are vital elements in this transformative journey.
Organizational Readiness
Before diving into the implementation of APCP, itās important to evaluate the readiness of the organization. This means determining whether the current systems, culture, and resources align with the goals set forth for APCP.
A few critical aspects to assess include:
- Existing Infrastructure: Is the current technology capable of supporting new procedures? This encompasses both hardware and software systems.
- Cultural Alignment: Does the organizational culture embrace change? If employees resist new methods, the best procedures can sputter.
- Resource Availability: Are there sufficient financial, human, and technological resources allocated to support the implementation?
To get a real on readiness, organizations can conduct surveys or workshops to gauge staff sentiment. This helps in establishing a collaborative approach right from the get-go, making all parts of the machine run smoother together.
Training and Support
Training isnāt just a box to tick off when rolling out new procedures. Itās an essential element that transforms theoretical understanding into practical application. Investing in comprehensive training and support can make a world of difference in how readily employees adapt to APCP.
Consider these training facets:
- Tailored Programs: Rather than a one-size-fits-all approach, develop training modules that address the specific needs of different departments.
- Hands-On Learning: Encourage experiential learning through simulations or hands-on workshops to help employees feel the mechanics of APCP in action.
- Ongoing Support: Provide access to resources, whether through an internal knowledge base or a mentorship program, to help staff continually improve their skills.
"Training is not just about learning new skills; itās about aligning everyoneās vision towards achieving organizational excellence."
In keeping with the organizational readiness assessment, this training allows employees to understand their roles within the framework of APCP, fostering a sense of ownership and motivation.
Monitoring and Evaluation of APCP
Monitoring and evaluation (M&E) are more than just buzzwords in the realm of Advanced Process Control Procedures (APCP). They act as the compass that guides organizations through the murky waters of operational performance. Why is this crucial? Simply put, it ensures that the APCP is functioning as intended, helping to identify issues before they snowball into bigger problems.
The importance of M&E cannot be overstated. They serve as the backbone for both accountability and improvement in processes. With proper monitoring techniques in place, deviations from expected performance can be detected swiftly, allowing for timely interventions. When you regularly evaluate the performance of your APCP, you can figure out what's working, what's not, and where adjustments are necessary.
Performance Metrics
Performance metrics are at the heart of any effective monitoring strategy. They give organizations measurable values that can be tracked over time. Consider this as the report card for your APCP.
Hereās a list of key performance metrics to focus on:
- Efficiency: Measures how well a process utilizes resources.
- Quality: Evaluates the rate of defects or failures relative to output.
- Throughput: Assesses how much product is processed in a given time.
- Cost: Looks at how much it costs to produce an item and how that compares to revenue.
- Cycle Time: The total time from the start to the finish of a process.
Successful organizations manage their performance metrics through established data collection and analytics techniques. By regularly gathering and analyzing data on these metrics, they can make informed decisions that refine and optimize their APCP.
"Monitoring is not a one-time event; itās a continuous journey of discovery and improvement."
Continuous Improvement Processes
Continuous improvement processes correlate closely with monitoring strategies. Once you have gathered data through performance metrics, it's imperative to use that information to drive enhancements. This approach is sometimes referred to as the Plan-Do-Check-Act (PDCA) cycle, an ongoing effort to improve products, services, or processes.
Here's a simplified breakdown of how you can implement continuous improvement:
- Plan: Identify an opportunity for improvement and plan for change.
- Do: Implement the change on a small scale to test its effects.
- Check: Monitor and evaluate the results of the test.
- Act: If successful, implement the change on a larger scale; if not, refine the plan and repeat the process.
This ongoing cycle transforms the APCP into a living, breathing entity that adapts to both internal and external changes. It not just focuses on short-term fixes but nurtures long-term operational excellence.
Common Challenges in APCP Development
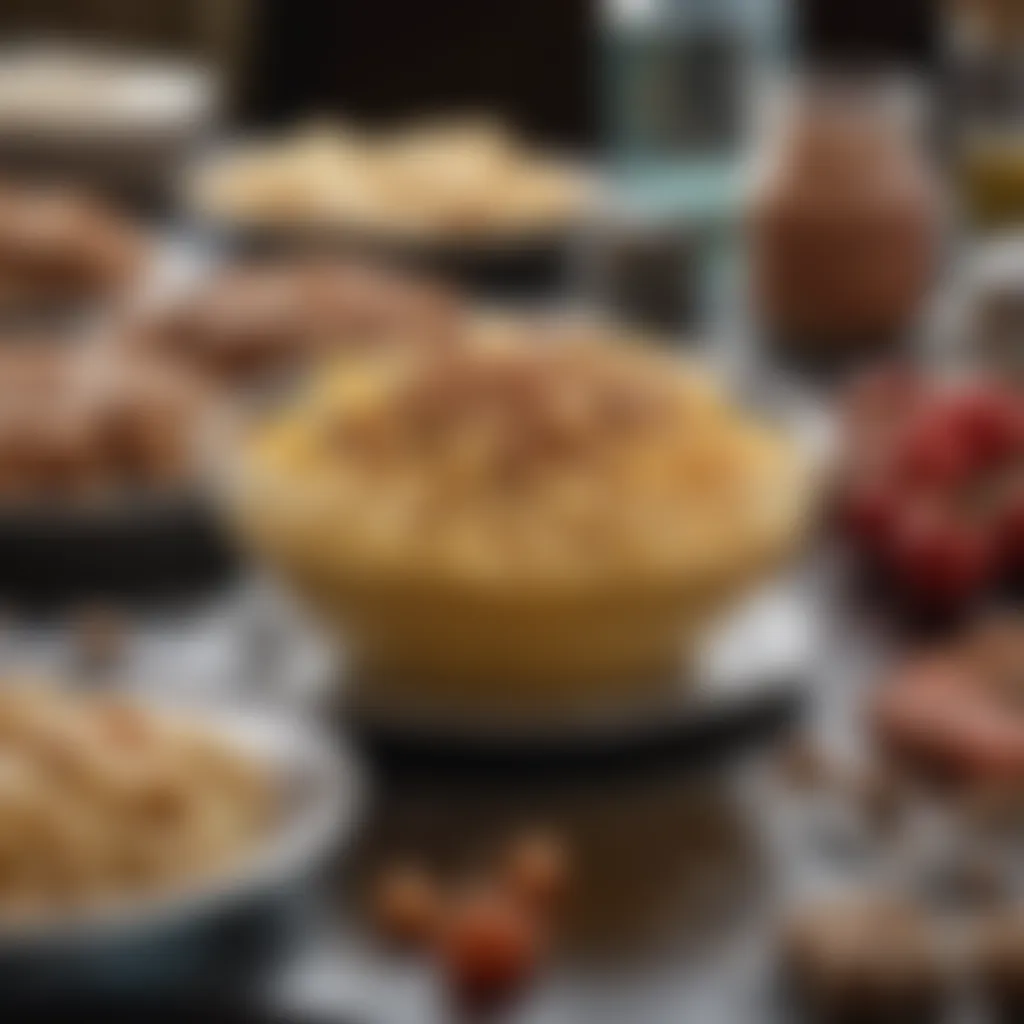
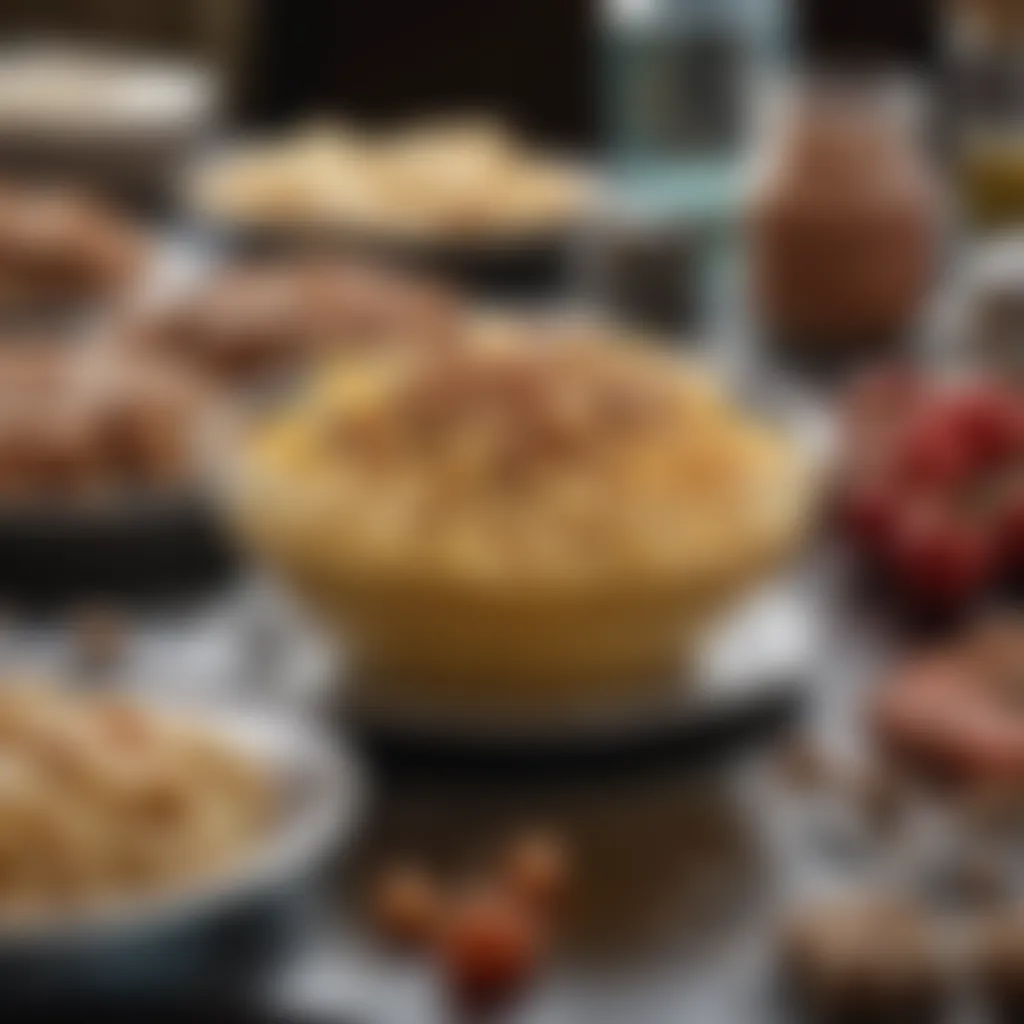
Advanced Process Control Procedures (APCP) are vital for optimizing industrial processes. However, developing these procedures isnāt all sunshine and rainbows. Understanding the challenges involved is half the battle, and navigating these treacherous waters can make a significant difference in the success of your initiatives.
Technical Challenges
While the excitement of venturing into Advanced Process Control might be palpable, the technical hurdles can be quite daunting. These challenges often emerge from technology limitations, data inconsistencies, and process complexities.
- Data Integration Issues: Compatibility between various data systems can lead to hurdles in accessing needed information. Imagine trying to bake a cake when your oven can't reach the required temperatureāsimilar frustrations arise when integrating data sources.
- Modeling Inaccuracies: The need for reliable models is paramount. Unreliable models can misguide control decisions. If you think youāre mixing the right ingredients based on a flawed recipe, the end product won't be tasty.
- Sensor Reliability: Sensors are the ears and eyes of your process. If they falter, your control strategies can take a nosedive. A malfunctioning sensor is akin to a recipe calling for salt but you mistakenly using sugarādefinitely not the outcome you want.
Technical challenges are not just bumps in the road; they require ongoing monitoring and maintenance. Staying adaptable and addressing these issues promptly can set you on the right path.
Human Factors and Resistance to Change
Another notable challenge is the human element involved. Change is hard for many individuals, and some may resist new processes or technology.
- Fear of Job Loss: Employees may worry that automation through APCP could replace them. This fear is a major roadblock to implementation.
- Training Deficiencies: If your team isn't equipped with the proper training, confusion will inevitably arise. Itās like handing someone a new kitchen gadget without instruction but expecting them to whip up a culinary masterpiece.
- Cultural Barriers: Every organization has its culture that may clash with the new changes being proposed. People often cling to the familiar, fearing what they donāt know, similar to a housewife sticking to her grandmotherās age-old recipe even when she discovers an easier method of making it.
By acknowledging these human factors and addressing them requires an approach tailored to engage and reassure staff. Building a sense of stability amidst change, perhaps by involving employees in the planning and implementation phase, can help break down those barriers.
"Change is inevitable. Growth is optional."
Case Studies in APCP Implementation
Examining case studies in the realm of Advanced Process Control Procedures (APCP) is not merely an academic exercise; it's akin to sifting through a treasure trove of insights. Each case tells a different story, demonstrating the practical applications of APCP across various sectors. Understanding these narratives can note significant advantages for practitioners, bridging the gap between theory and application.
The value of case studies lies in their ability to showcase real-world scenarios where APCP has been meticulously crafted and implemented. These examples help elucidate the various elements and benefits of APCP, offering practical lessons that are much more digestible than concepts alone. Through these case studies, readers can grasp how different organizations have navigated their unique challenges, learned from their successes and failures, and improved their operations. This critical analysis makes the theoretical frameworks come alive, transforming abstract principles into tangible outcomes.
Successful APCP Applications
When it comes to successful applications of APCP, one cannot overlook the approach taken by defunct plants in the chemical industry. In one notable case, a chemical manufacturing facility successfully implemented an APCP that streamlined its production rate while significantly reducing waste. They realized that not only did they need to control the temperature and pressure, but the entire process dynamics required careful monitoring and adjustment. The team introduced enhanced feedback loops that responded in real-time, leading to a reduction in inconsistencies and rework.
Benefits of this successful implementation:
- Enhanced Efficiency: Reduction in production time by 20%.
- Cost Savings: Lower operational costs due to reduced material waste.
- Improved Product Quality: Consistent product specifications, allowing for fewer returns and complaints.
This case exemplifies how a well-crafted APCP can result in operational excellence, transforming an underperforming facility into a paragon of efficiency. Another excellent example is in food processing, where a dairy plant applied advanced control strategies to enhance the pasteurization process. By utilizing real-time data and predictive analytics, they achieved improved safety and consistency in their products, building a stronger reputation in the market.
Lessons Learned from Failures
Every coin has two sides, and case studies also show that not every effort to implement APCP springs to life without hiccups. A notable instance of failure occurred at a pharmaceutical company that struggled with a poorly designed APCP. The original plan was riddled with gaps in data integration, leading to inconsistent results and a compromised product line.
The key lessons from this blunder include:
- Prioritize Data Quality: The company learned that accurate and reliable data is the backbone of any control procedure. Without it, any intervention is akin to building a house on sand.
- Interdepartmental Collaboration: Successful APCP demands efforts from various departments. Lack of communication led to silos, preventing a smooth implementation process.
- Iterative Development: The failure highlighted the necessity for iterative testing and refining of processes before full-scale implementation.
These examples underscore the importance of a meticulous approach and serve as cautionary tales for others embarking on their APCP journey. Engaging with such success stories and cautionary notes can provide nuanced insights that inform better practices in future scenarios.
Future Trends in APCP
As we venture into the realm of Advanced Process Control Procedures (APCP), understanding future trends becomes crucial. This awareness not only equips professionals to stay ahead but also ensures the long-term viability of their methods. The world of process control is ever-evolving, driven by advancements in technology and shifting industry practices. Grasping these trends provides insights into improving processes, enhancing efficiency, and adapting to changes in market demands.
Advancements in Technology
The rapid evolution of technology plays a pivotal role in shaping future APCP trends. Innovations, such as predictive analytics, machine learning, and the Internet of Things (IoT), have transformed how data is collected and analyzed. The integration of smart sensorsāwhich reliably gather real-time dataāenables tighter control over processes. For example, industries are increasingly utilizing IoT devices to monitor systems continuously, helping them identify potential failures before they escalate, thus saving time and money.
More importantly, the utilization of cloud computing offers flexibility in handling massive datasets. Facilities can now analyze data streaming from various sources, leading to more accurate modeling of systems. This aids in optimizing control strategies and enhances decision-making capabilities. To further illustrate:
- Data Visualization Tools: Enhanced graphical representations of data help teams easily understand trends and outliers.
- AI-Driven Algorithms: They analyze historical data to predict future outcomes, aiding in proactive decision-making.
- Simulation Software: Such tools allow for testing different scenarios without risking actual processes, thus improving safety and efficiency.
By embracing these technological advancements, industries can significantly improve operational efficiency, reduce downtime, and promote sustainable practices.
Shifts in Industry Practices
As technology advances, shifts in industry practices become necessary. Traditional methods are giving way to agile frameworks that prioritize responsiveness and adaptability. Companies are increasingly recognizing the need for integrated systems that provide end-to-end visibility across operations. Instead of siloed departments, collaborative approaches are now favored, encouraging communication and cooperation.
Another notable trend is the emphasis on sustainability. More industries are pivoting toward practices that minimize environmental impact and promote circular economy principles. This not only aligns with regulatory demands but resonates with consumers who prioritize environmentally responsible businesses.
Here are a few shifts that are shaping the future landscape of APCP:
- Emphasis on Data-Driven Decision Making: Organizations are moving towards a model where data informs every decision, reducing reliance on gut feelings.
- Increased Focus on Employee Training: To handle advanced technologies, companies prioritize upskilling their workforce.
- Adoption of Agile Methodologies: Flexibility and rapid iteration now dictate the pace of projects, allowing teams to adapt to changes more readily.
In summary, both advancements in technology and shifting industry practices are not just trends; they signify a transformation in how process control is managed. By keeping a keen eye on these developments, organizations can successfully navigate the complexities of crafting effective APCP.
Epilogue
In the realm of Advanced Process Control Procedures (APCP), the conclusion serves as a crucial touchpoint for consolidating your journey through the intricate landscape of effective control methodologies. Itās the final chapter in a story that unfolds from the initial seed of an idea to the blossoming of a fully realized framework. This section emphasizes not only a recapitulation of essential elements but also invites readers to reflect on the multitude of benefits inherent in a well-implemented APCP.
By bringing together the varied threads discussed throughout this article, one can clearly see how comprehensive understanding impacts operational excellence. Through the lens of this guide, it becomes evident that an APCP isn't merely a set of procedures. Rather, it is an evolving mechanism that enhances productivity, minimizes variability, and ultimately leads to smoother workflows. The operational enhancements gained through meticulous planning and execution can significantly reduce costs and improve quality, thereby reinforcing the importance of adhering to APCP methodologies in any industry setting.
Considerations include:
- The necessity for continuous adaptation and review of processes.
- The paramount role of training and support in ensuring all team members are aligned with the procedures.
- An emphasis on the integration of technological advancements which can drive further efficiency.
"With a clear conclusion, the emotional journey transitions from uncertainty to confidence, allowing organizations to stride forward knowing they possess the tools to adapt and thrive."
In summary, a solid conclusion not only highlights the pressing need for diligence in APCP but also encourages organizations to embrace a mindset of perpetual improvement. Each step reaffirms the roadmap towards excellence, prompting teams to recommit to the ongoing evolution of their processes.
Summary of Key Points
Reflecting on the discussion we've traversed, it's essential to distill the core elements that drive the efficiency of APCP:
- Foundation of Understanding: Gaining a clear grasp of APCP structures acts as the backbone for successful implementation.
- Data-Driven Decisions: Reliable data fuels the ability to predict outcomes and refine control processes.
- Adaptability and Flexibility: The ability to pivot and adjust strategies expands an organizationās capacity to meet dynamic market demands.
- Stakeholder Engagement: Continuous involvement from team members fosters a culture of shared responsibility and commitment to APCP.
- Performance Metrics: Regular evaluation using defined metrics keeps the APCP on a path of progress and continuous improvement.
Encouraging Future Exploration
As the world advances, so too does the framework within which Advanced Process Control Procedures operate. Encouraging future exploration involves staying abreast of the latest developments and embracing innovation. The landscape of process control is not static; it is dynamic and ever-evolving.
Organizations should endeavor to:
- Research Emerging Technologies: Understanding how AI and machine learning can enhance control processes opens avenues for operational excellence.
- Engage with Industry Communities: Platforms like Reddit or Facebook offer excellent ways to connect with like-minded professionals and exchange ideas on best practices.
- Participate in Forums and Conferences: Networking with industry leaders fosters inspiration and collaborative growth.
Investing time in these explorations not only aids in refining current practices but also equips teams with the insights needed to navigate the complexities of tomorrowās industrial landscapes. Ultimately, the pursuit of knowledge and adaptation is what will keep your APCP relevant and effective in a world that never stops changing.