Crafting the Ideal RCF Recipe: Your Complete Guide
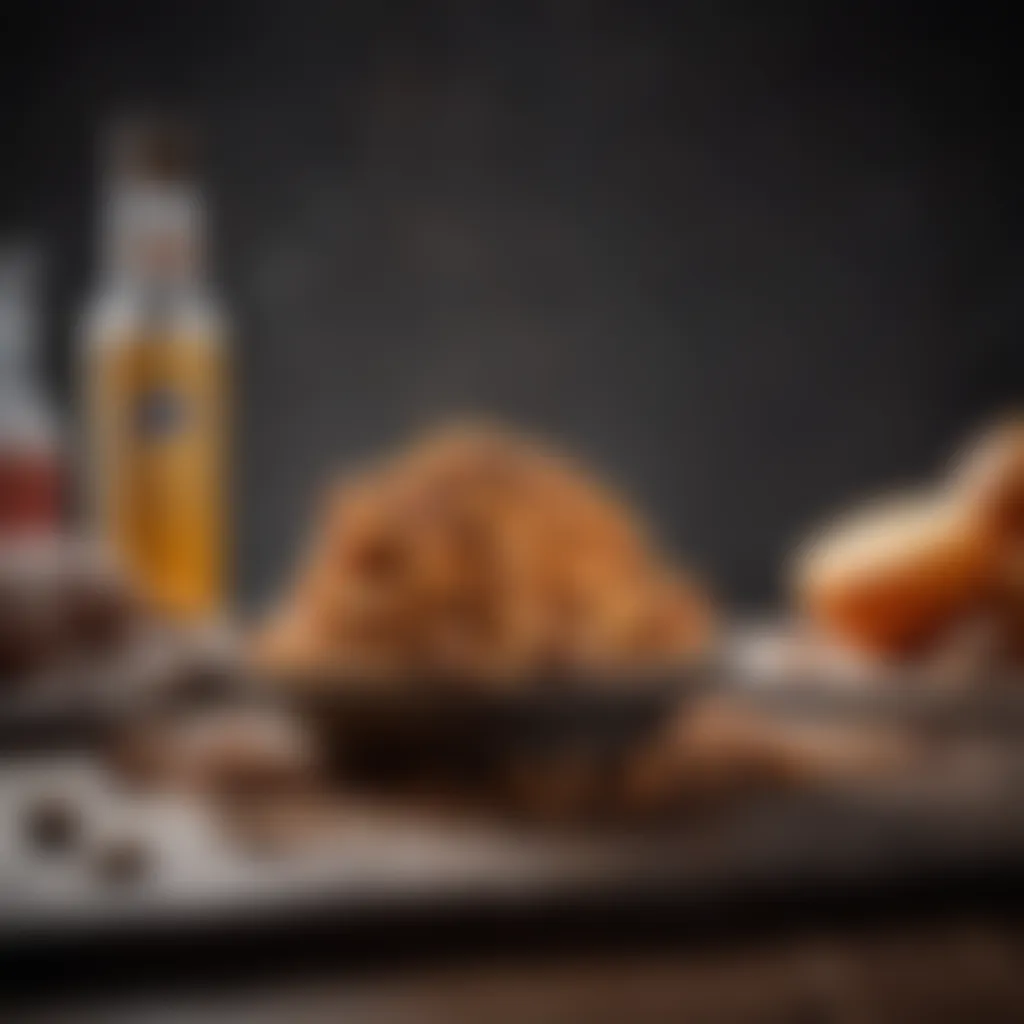
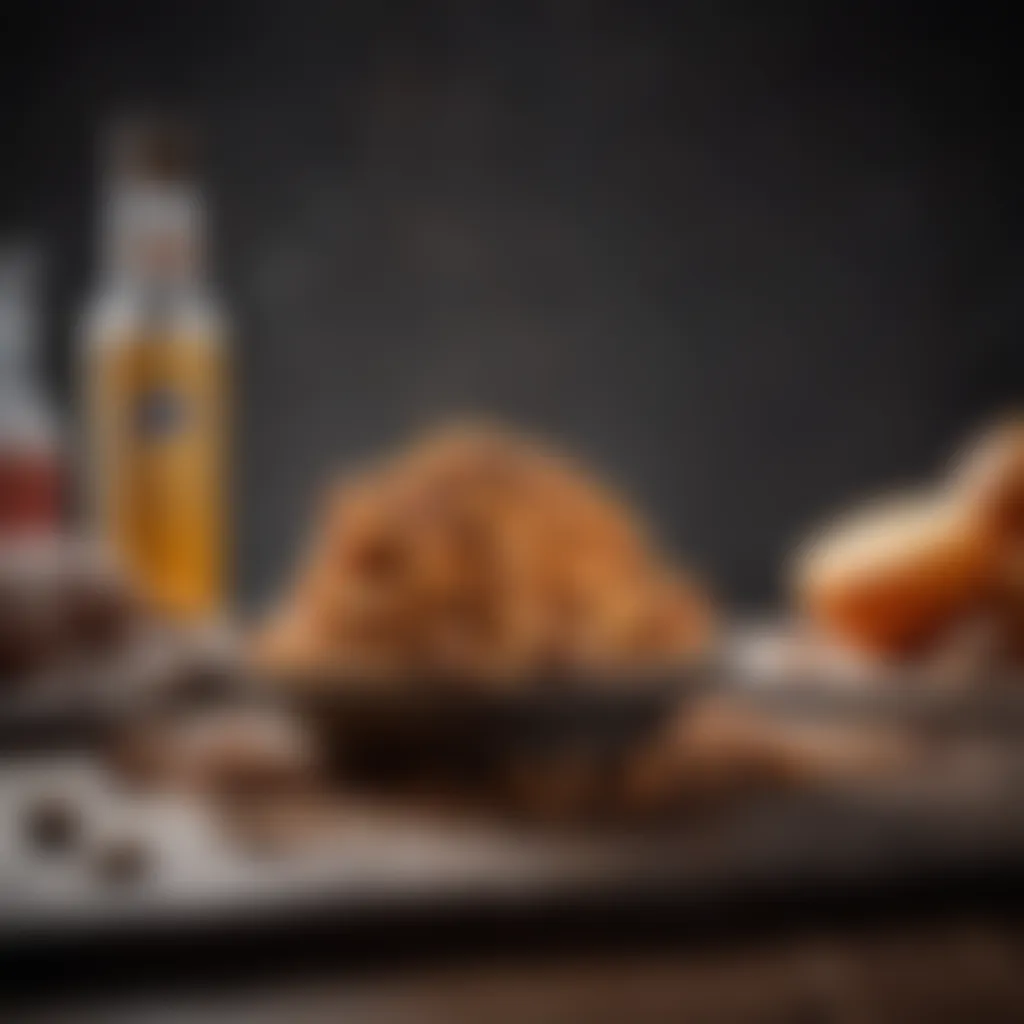
Intro
Creating a Reinforced Concrete Frame (RCF) recipe isn't just about throwing in a few ingredients and hoping for the best. It’s an intricate dance of materials and techniques, and for those deeply involved in construction, mastering this art is crucial. Whether you’re a seasoned builder or a novice housewife trying to wrap your head around the details, understanding RCF can transform your approach to construction projects, making them stronger and more efficient. In this guide, you’ll navigate through the essential components of crafting a perfect RCF recipe, from gathering the right materials to applying precise techniques that ensure the final product stands the test of time.
Ingredients:
To whip up a successful RCF, you’ll need a selection of materials that each play a vital role in the outcome. Here’s what you need:
- Cement: 300 kilograms
- Fine Aggregate (Sand): 600 kilograms
- Coarse Aggregate (Gravel): 1200 kilograms
- Water: 180 liters
- Reinforcement Bars: 20 pieces of 12mm diameter (length depending on structure)
- Additives (if needed): 2.5% of total cement weight
Make sure to choose high-quality materials, as they will significantly affect the overall strength and durability of your RCF. It’s like cooking with fresh ingredients—your end dish really depends on what went into it!
Preparation Steps:
Detailed Instructions
- Measure and Weigh Ingredients: Start by carefully measuring out all your ingredients. Precision matters here; too much or too little can throw off the balance.
- Mix the Dry Ingredients: In a large mixing container, combine the cement, fine aggregate, and coarse aggregate. This step ensures an even blend of the primary ingredients. Consider using a concrete mixer to save time and ensure a uniform mixture.
- Prepare Reinforcement Bars: Cut the reinforcement bars to the required length for your specific application. It’s critical that these are prepared ahead of mixing to prevent delays.
- Add Water Gradually: Slowly pour in the water while mixing continuously. This gradual addition allows for better control over the consistency of the mixture. Aim for a workable mix that isn’t too runny.
- Incorporate Additives: If you’re using additives, mix them in now. These can enhance properties like workability, strength, or curing time depending on your project’s needs.
Technical Aspects:
Temperature Settings and Timing
- Temperature: It’s best to work within a temperature range of 10°C to 30°C. Lower temperatures can slow down curing while higher can lead to quick setting times that aren’t ideal.
- Timing: Allow your mix to sit for about 15-30 minutes after mixing to let the ingredients blend. Once poured, the mix should cure for at least 28 days for optimal strength, with periodic misting if you’re in a hot environment to prevent premature drying.
Cooking Process:
Sequential Steps
- Pouring the Mixture: Once your mixture is ready, carefully pour it into the formwork where the reinforcement bars have been pre-positioned.
- Leveling the Surface: Use a trowel to smooth the top surface of the wet mix, ensuring it is level and free of air pockets. This step is crucial for the aesthetics and strength of your frame.
- Reinforcing the Setup: Ensure the reinforcement bars remain in place while the concrete is being poured. They need to be submerged well within the mix for optimal bonding.
- Curing Period: After pouring, protect the RCF from harsh environments. Cover it with damp burlap or plastic sheets to maintain moisture levels.
Troubleshooting Tips:
Even the best chefs run into issues. Here are solutions for some common problems you may encounter:
- Mix Too Runny: If your mixture is too watery, add small amounts of dry ingredients carefully to achieve the desired consistency.
- Air Bubbles: If you see air bubbles after pouring, lightly tapping the formwork can help dislodge them. Use a vibrating tool if necessary.
Remember: Quality comes before quantity. Always prioritize the right mix and technique over fast results to achieve that perfect RCF every time.
By following each of these steps carefully, you’ll be well on your way to crafting exceptional RCF recipes that bring your construction projects to life.
Preface to RCF Recipes
Understanding the subtleties behind Reinforced Concrete Frame (RCF) recipes is essential in the construction industry. This section serves as the stepping stone into a world where precise formulations dictate the durability and reliability of structures.
Understanding RCF
At its core, RCF combines concrete with steel reinforcement to create structures that can withstand both vertical and lateral loads. The concrete provides compressive strength, while steel adds tensile strength. Getting to grips with the makeup of RCF allows one to recognize the necessity for a well-crafted recipe. Think of it as a well-balanced dish, where each ingredient plays a vital role in creating the final flavor. Without the right ratios or quality, the whole thing can fall apart—literally.
Not only does mastering RCF recipes help in achieving structural integrity, but it also enables designers and builders to optimize costs and resources. Just like a carefully designed meal can yield maximum satisfaction with minimal ingredients, a well-formed RCF recipe can ensure robust structures without unnecessarily overloading them with materials. This foundational understanding is crucial, providing the necessary context for why we delve into the details of crafting these recipes.
Importance of a Well-Crafted Recipe
A well-crafted RCF recipe is akin to the very foundation of a house—it underpins the entire project. When every ingredient is measured and mixed with care, the resulting structure can greatly enhance safety and longevity. Each element of the recipe, from concrete types to reinforcement selection, contributes to the outcome.
Here are some key reasons why getting this right is indispensable:
- Safety: Subpar formulations can lead to catastrophic failures, resulting in loss of life or property.
- Cost Efficiency: Using optimal quantities reduces waste and can save substantial material costs.
- Performance: Each project is different; a tailored recipe addresses specific site conditions and uses better than a generic one.
To sum it up, a well-crafted RCF recipe isn’t merely a checklist of materials and proportions; it’s a carefully considered plan that evolves based on the nuances of each project. Those involved in the process must appreciate not only the how but also the why behind their choices. This insight can significantly elevate the quality and success of construction endeavors.
A well-crafted recipe holds the power to transform ordinary designs into extraordinary structures, offering safety and efficiency hand-in-hand.
Basic Components of RCF Recipes
Understanding the basic components of RCF recipes is crucial for anyone involved in the construction process. It serves as the backbone, dictating the strength, durability, and overall efficacy of the structure being built. A flawed foundation in this stage could lead to catastrophic failures down the line. There’s a rhyme and reason to why every ingredient in a recipe counts. Let's break down the essential materials that come into play, each contributing to the general stability and longevity of the reinforced concrete frame.
Key Materials Involved
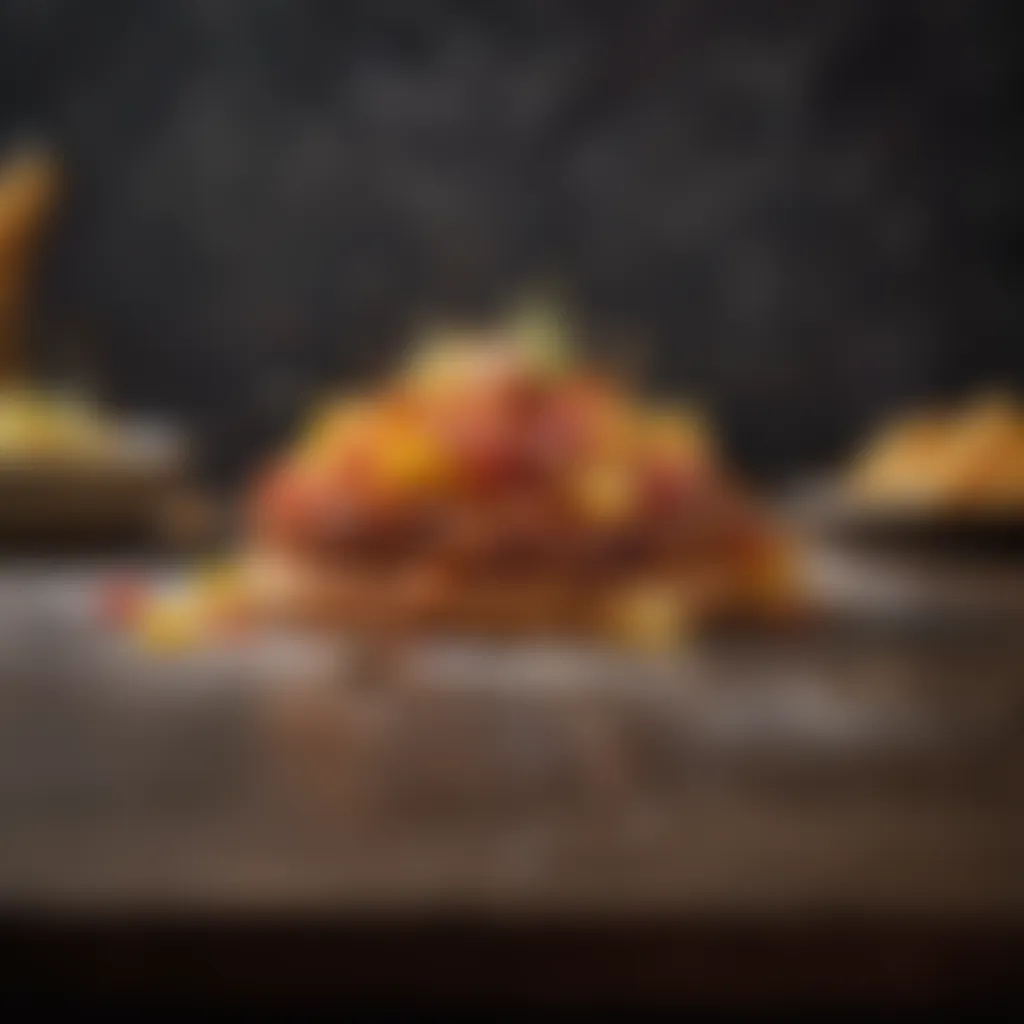
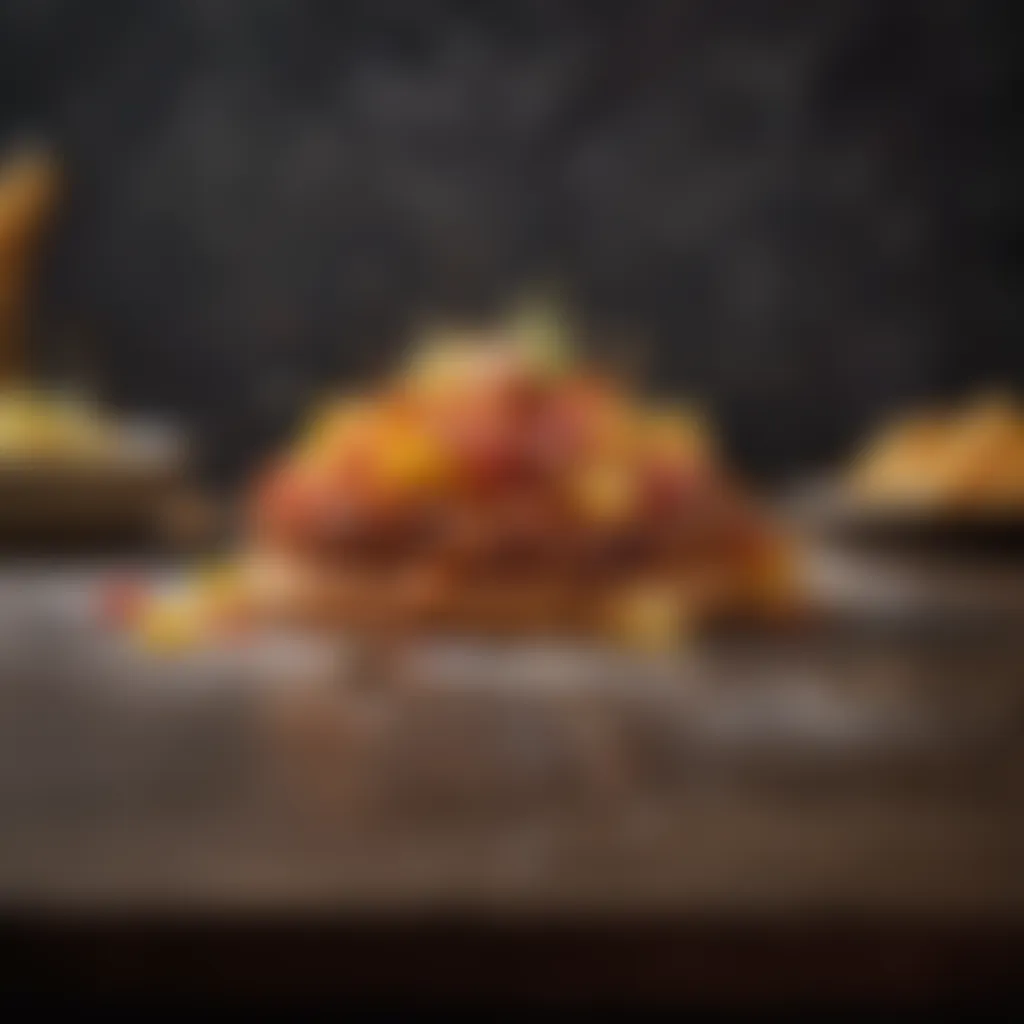
Concrete Types
Concrete is not just concrete. It comes with different varieties, each boasting unique characteristics that influence the final product. Regular concrete, which includes types like ordinary Portland cement, is popular due to its affordability and ease of use. However, high-performance concrete steps into the spotlight when looking for exceptional strength and durability, often becoming a go-to for structures subject to heavy loads or harsh conditions. Among the standout qualities, one cannot overlook the workability and curing time, which are crucial factors for achieving the desired finish and structural integrity.
With high-strength concrete, for instance, one may find that it offers excellent compressive strength, making it suitable for high-rise buildings. But, its unique setting properties can also mean it's not always the easiest to manage in small-scale applications. Thus, understanding what kind of concrete to use is not just a trivial choice; it’s an integral part of crafting a reliable recipe.
Steel Reinforcement Elements
Steel reinforcement elements, often referred to as rebar, play a pivotal role in increasing the tensile strength of concrete structures. Given that concrete tends to be strong in compression but weak in tension, incorporating steel helps to bridge this gap. Steel’s key characteristic lies in its ductility, which allows structures to absorb and redistribute loads during unexpected stress events, such as earthquakes or high winds.
A major advantage of using rebar is its corrosion resistance when coated properly, allowing it to endure various environmental factors. Conversely, improper placement or poor quality materials can lead to uneven stress distribution and weaken the overall structure. That’s why knowing your steel’s grade and suitability for the project is essential, as it contributes significantly to the ultimate performance of the RCF.
Additives and Their Functions
Additives can be the secret sauce in achieving a top-notch concrete mix. They're added to enhance specific attributes of concrete, whether that’s improving workability, reducing water content, or accelerating curing time. Plasticizers, for example, help achieve a smoother finish and increase flowability without adding excess water. They allow for denser mixes, minimizing the voids within the concrete.
Another popular choice is superplasticizers, which can significantly enhance workability without the need for extra water. While beneficial, it’s vital to use them in moderation; too much can lead to separation of materials. Choosing the right additives can make a world of difference, allowing for better mixing and placement, especially in complex forms where precision is key.
Proportioning Techniques
Now that we have looked into the materials, let's explore how to properly proportion them to create a balanced and effective mix. In construction, the right ratios can mean the difference between a solid structure and a crumbling one. It's not just about throwing materials together; there's more to it than that.
Standard Ratios
Standard ratios provide a foundational guideline in formulating your mixture, ensuring a blend that maintains performance and integrity. Typically, the conventional mix might follow a ratio of 1:2:3, translating to one part cement, two parts sand, and three parts gravel. This ratio works well for general applications and provides a robust framework to build upon. However, these numbers can shift based on specific project requirements, like durability and exposure conditions.
When working with different concrete types, these ratios will vary. For example, a mix intended for high-strength concrete might include a lower water-cement ratio to achieve maximum strength. Yet, it's essential to have both experience and concrete knowledge, as straying too far from established ratios could lead to issues down the line.
Variability in Mix Design
Every project is unique, and sometimes the cookie-cutter approach doesn’t cut it. Variability in mix design allows for adjustments based on the specific site conditions, material availability, and desired performance characteristics. One important aspect is environmental conditions; for instance, a mix might require more additives if placed in colder temperatures to ensure proper curing.
This adaptability makes it important not to shy away from tweaking the mix. However, one must be cautious, as over-adjusting can lead to unforeseen consequences like shrinkage cracks or compromised strength. Having a foundational understanding of materials and their interactions is key to making necessary adjustments while keeping quality high.
Understand this: successful RCF recipe crafting gives you the flexibility to adapt while respecting the fundamental properties of your materials.
In summary, mastering the basic components of RCF recipes is not merely about knowing what's involved; it’s about understanding how each element contributes to the final outcome. Whether it's concrete types, reinforcement options, or specific additives, each plays its role, and through careful proportioning, one can achieve a successful blend that stands the test of time.
Mixing Process
Mixing forms the backbone of the RCF recipe. It’s where all the magic happens, turning raw materials into a cohesive blend that ensures strength and durability. Without an adequate mixing process, even the best materials can fall short, leading to weaknesses in the finished product. Effectively mixing the components allows for uniform distribution, creating a solid base conducive to long-lasting structures. This section will discuss the significance of uniform mixing as well as the different equipment involved in the mixing process.
The Importance of Uniform Mixing
Uniform mixing is essential in achieving a project’s desired performance. When all the materials, like cement, aggregates, and additives, are mixed evenly, they work together to provide the required strength and stability. Think of it as baking a cake; if the ingredients aren't blended well, you may end up with a half-baked result. In the realm of RCF, poor mixing can lead to issues such as cracking, reduced structural integrity, and a myriad of other complications.
Key Benefits of Uniform Mixing:
- Consistent Strength: A homogeneous mix ensures that every part of the frame is equally strong, which is vital for load-bearing.
- Improved Workability: Even mixing enhances the ease of application, making it simpler to pour and shape the concrete.
- Enhanced Durability: A well-mixed formula helps in reducing porosity, resulting in a more robust material against weathering and other environmental factors.
Equipment Used in Mixing
The mixers you choose can make or break the whole process. Each type of mixer serves a specific purpose, and understanding their strengths will help you make an informed choice. Below are the two main types utilized in mixing RCF:
Drum Mixers
Drum mixers are widely recognized for their reliability in mixing concrete. The unique aspect of a drum mixer lies in its rotating drum that combines materials during operation. This method is effective for larger batches, making it a go-to for many contractors.
Key Characteristics and Benefits:
- Efficiency: Drum mixers can handle large quantities at once, saving time on big jobs.
- Continuous Mixing: They can keep mixing without the need for frequent stops, ensuring that every batch remains uniform.
However, it's worth noting that drum mixers may require more attention when it comes to maintaining the right mixing time. Too short, and the result could be uneven; too long, and you might risk overworking the mixture.
Batch Mixers
On the other hand, batch mixers focus on smaller quantities, typically mixing one batch at a time. This equipment is quite popular in projects where bespoke formulas are necessary.
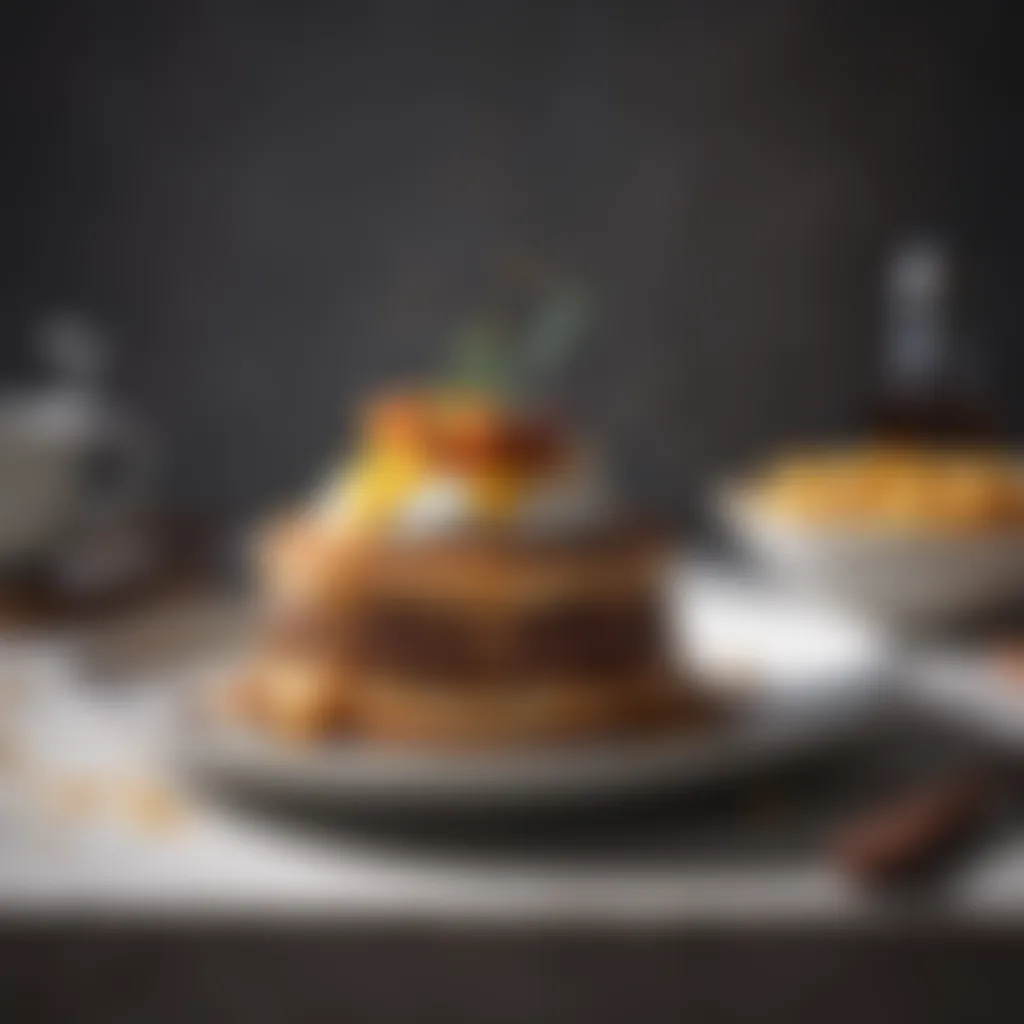

Key Characteristics and Benefits:
- Custom Mixes: Batch mixers allow for meticulous adjustments to the mixture, ensuring the specific requirements of a job are met.
- Quality Control: With each batch being mixed separately, it’s easier to monitor each mix's consistency and quality.
Yet, batch mixers may not be as efficient for larger projects due to their limited capacity. It's a tug-of-war between volume and precision.
In summary, selecting the right mixer can lead to superior results in an RCF recipe, balancing both uniformity and efficiency. Each equipment choice comes with its own set of advantages and disadvantages, but understanding the specifics can guide you towards mastering the art of mixing.
Quality Control Measures
Quality control measures in the realm of RCF recipes stand as the unsung heroes of constructing robust infrastructure. Without these measures, you’re essentially playing a game of chance, where the stakes are high, and the costs of error can be monumental. Ensuring that all ingredients and processes adhere to stringent quality standards translates directly into the durability and safety of the final product. A well-executed quality control regime doesn’t just bolster the integrity of the structure; it enhances the overall operational efficiency of the project.
Assessing Material Quality
The first pillar of quality control is assessing the quality of materials utilized in the recipe. This step cannot be overstated, as the raw materials form the backbone of any construction undertaking. Factors such as the grade of concrete, the tensile strength of steel reinforcement, and even the type of additives can critically influence the outcome.
For instance, selecting high-grade Portland cement with a low percentage of impurities can markedly increase the longevity of the structure. Additionally, performing preliminary checks on all materials coming into the site protects against hidden deficiencies that might go unnoticed at first glance. This might involve sampling and laboratory tests designed to evaluate things like hardness, density, and water absorption rates. Regular monitoring of the inbound materials leads to a more consistent and superior mix.
Testing for Consistency and Strength
After ensuring that material quality is honed to perfection, the next logical step comprises rigorous testing for consistency and strength. Two standard tests that emerge in this context are the slump test and the compression test. Each serves to measure different yet equally crucial attributes of the concrete mix.
Slump Test
The slump test assesses the workability of fresh concrete. By measuring the vertical settlement of a concrete cone, you can determine if the concrete has the right consistency for pouring. It's a simple and effective method that's been commonly used in the industry. The primary characteristic of the slump test is its simplicity and speed; it doesn’t require elaborate equipment, just a slump cone and a ruler. Its popularity arises because it gives immediate feedback about the mix's usability—perfect for on-site evaluations.
However, while helpful, the slump test has its limitations. It mainly indicates workability rather than strength, and in some cases, an excessively high slump might suggest an overabundance of water, which could lead to weakened concrete over time.
Compression Test
On the other hand, the compression test dives deeper into the essential property of the concrete mix: its strength. By subjecting concrete specimens to a compressive force until failure, you get a clear, quantifiable metric indicating how much load the concrete can withstand. The key feature of the compression test is that it gives a solid measure of the mix's durability over time, which is crucial for design considerations.
This test is a bit more complex, often requiring laboratory conditions to ensure accurate results. However, it pays off, as engineers can confidently predict structural performance based on these findings. Yet, it's worth noting that while compression tests provide vital data, they require time to conduct—typically only yielding results days after the concrete has set.
"Effective quality control in RCF recipes is not just a choice; it’s a necessity. It ensures longevity and maintains the integrity of structures that people depend on daily."
In summary, quality control measures represent a critical layer of defense in the pursuit of crafting an effective RCF recipe. From material assessment to rigorous testing, each step forms part of an interconnected web that ultimately ensures the success of construction endeavors.
Application Techniques
Application techniques play a crucial role in the success of any RCF recipe. They determine how well the constructed element integrates into the broader construction framework. A proper application ensures the desired strength, durability, and overall integrity of the reinforced concrete frame, and this involves precise strategies for placement and curing. This section reveals specific methodologies and considerations, providing a roadmap for effective application that resonates with seasoned contractors and newer entrants alike.
Placement Methods
Formwork Considerations
Formwork serves as the mold that shapes the concrete before it sets, making it a fundamental aspect in the placement of reinforced concrete. The use of formwork is not merely about containing the mix; it also significantly influences the overall stability and structural integrity of the setup. One key characteristic of formwork is its versatility; it can be made from various materials including wood, metal, or plastic, each serving different purposes tailored to unique project requirements.
Considerations for selecting the right formwork include:
- Cost: Certain materials like wood are cheaper but may offer less durability.
- Accessibility: The method of arrangement affects labor efficiency.
- Finish Quality: Options vary widely; plastic formwork may offer better surface finishes compared to traditional wood.
A unique feature of formwork is the potential for reusability. Many construction teams opt for systems that can be dismantled and reused in future projects, reducing waste and costs in subsequent jobs. However, this comes with the disadvantage of requiring additional planning to ensure that the reused formwork still meets the necessary strength and safety standards.
Vibration Techniques
The next critical aspect when applying your RCF recipe is vibration techniques. Vibration is essential to achieving a uniform mix and removing air pockets that can weaken the structure. The key characteristic of vibration is that it ensures a thorough consolidating process. When concrete is vibrated properly, it flows into every corner of the formwork, eliminating weak points and forming a uniform mixture.
Options for vibration methods typically include:
- Internal vibration: Using vibrators inserted into the concrete.
- External vibration: Placing vibrators on the formwork itself.
The unique edge provided by vibration is its ability to enhance the strength of cured concrete by improving density. However, excessive vibration can lead to segregation of materials, which can become counterproductive. Achieving the right level of vibration is crucial: too little leads to poor quality; too much can create additional issues.
Curing and Drying Procedures
Curing is another essential part of the application process, ensuring that the poured concrete achieves its full potential strength. Proper curing also helps in preventing cracking and surface damage, making it critical for successful project outcomes. Two necessary components of curing are timeframes and moisture control.
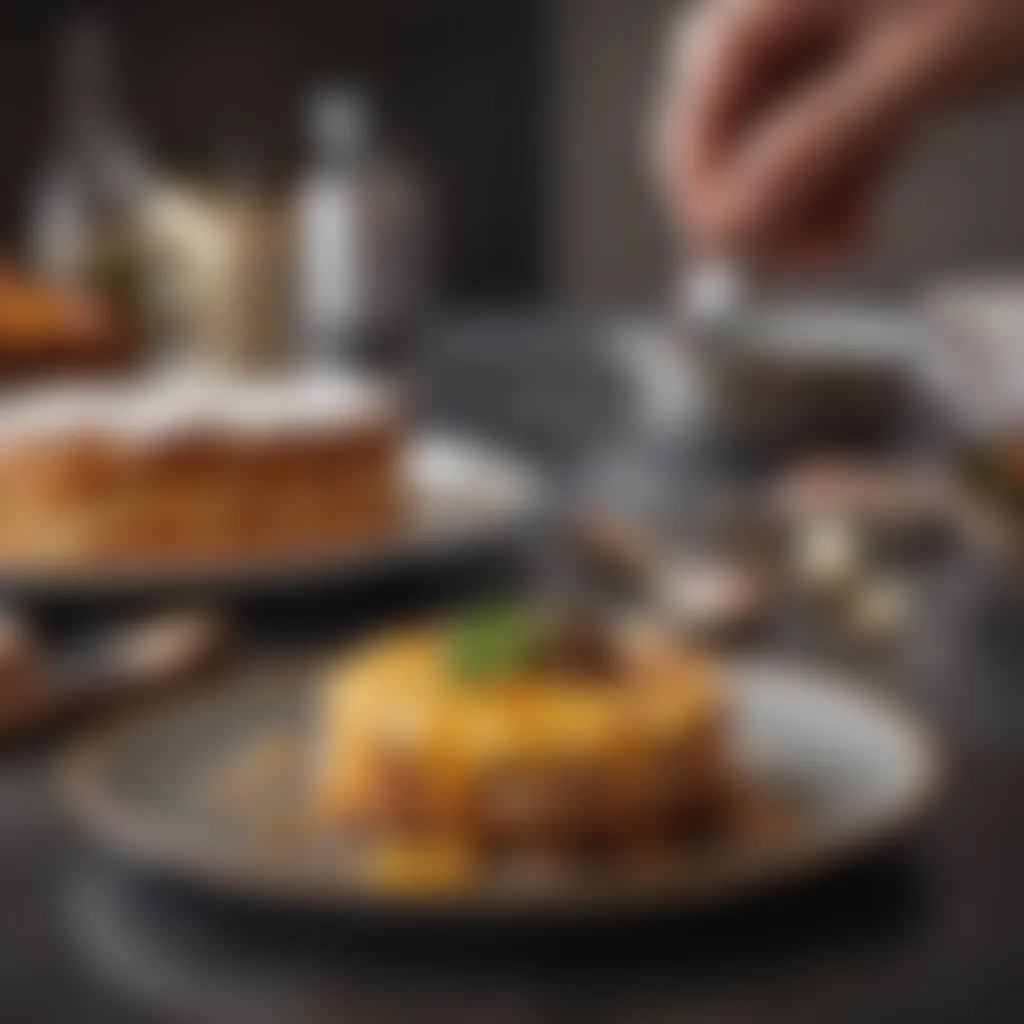
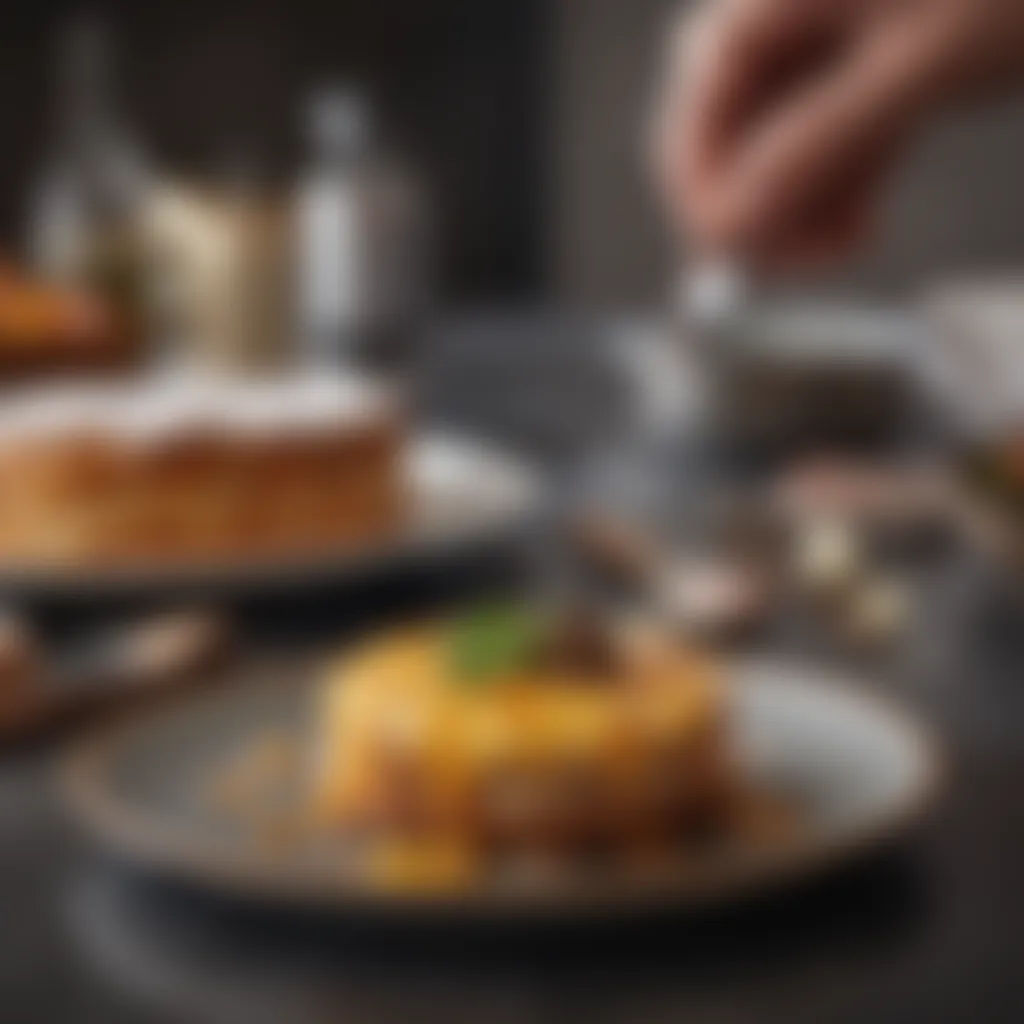
Timeframes
Timeframes refer to the duration that concrete needs to cure properly, impacting its ultimate performance. The standard curing period ranges from 7 to 28 days depending on environmental conditions and mix design. A critical aspect of these timeframes is the relationship between temperature and curing duration; warm weather can speed up setting but may require additional care.
- Short curing may lead to chemical reactions occurring too quickly.
- Extended curing improves strength but requires longer management of resources.
This balance makes timeframe consideration an essential aspect for project managers. A unique feature relating to timeframes is monitoring conditions; using moisture retention methods in the early days of curing can yield beneficial results.
Moisture Control
Moisture control is a key aspect of the curing process. Maintaining adequate moisture helps facilitate the hydration of cement particles, which is crucial for developing strength in the concrete. A significant consideration here is to prevent moisture loss due to environmental factors like strong winds or direct sunlight.
Some typical methods for moisture control include:
- Covering with wet burlap or plastic sheets.
- Using curing compounds that form a moisture-retaining film.
The unique advantage of proper moisture control is that it enhances both the durability and the long-term strength of the concrete. However, controlling moisture can be labor and resource-intensive, requiring detailed planning and execution.
By understanding these elements within application techniques, one can significantly increase the probability of achieving a successful RCF project outcome. This knowledge is invaluable for those looking to elevate their construction practices.
Addressing Common Challenges
In any intricate field, especially in construction, obstacles are bound to arise. Addressing Common Challenges in the crafting of RCF recipes highlights how crucial it is to recognize and rectify these hurdles early. As the saying goes, "A stitch in time saves nine," meaning that the sooner you address issues, the less daunting they become. In the world of reinforced concrete, identifying issues can lead to a smoother process and an overall enhancement in the final quality of your construction.
Understanding these challenges not only benefits the overall project but also fosters a proactive mindset that encourages innovation and efficiency. Preparing for potential pitfalls allows for adjustments and refinements in real-time, thus ensuring that the final product meets or exceeds expectations. It’s not just about following a recipe, but perfecting it under the pressures of real-world conditions.
Identifying Issues in Mixing
Mixing is the heart of any RCF recipe, and problems here can ripple through the entire project. Some of the common issues include inconsistencies in material quality, incorrect ratios of ingredients, and inadequate mixing techniques. Knowing how to spot these issues early on is key. For instance, if you notice an unusually dry mix or lumps in the concrete, it can be a signal that something's off. Also, inconsistent texture can hint at improper mixing techniques or materials that simply don't gel well together.
Awareness and vigilance are essential; keep an eye out for anything that doesn’t look or feel right during this critical process, as it can signal bigger problems down the line.
Solutions for Poor Quality
Revisiting Material Source
One solution to ensuring quality in reinforced concrete recipes is Revisiting Material Source. This is about going back to the beginning and examining where your materials come from. By selecting high-quality concrete types and reliable suppliers, you can mitigate the risks of using subpar ingredients. The characteristic of revising your source means you'd not only focus on quality but also dependability. This route can save you headaches later.
A notable advantage of this strategy is the traceability it offers. Knowing where each ingredient comes from can ensure consistent results. However, if you become too reliant on one supplier, there could be issues if they fail to deliver. Balance is crucial, and diversifying your material sources may very well provide a safety net.
Adjusting Proportions
Once you've identified that material quality might be an issue, consider Adjusting Proportions. This involves fine-tuning the ratios of your concrete mix to improve overall integrity. A fundamental understanding of standard ratios can help in manipulating proportions to find the sweet spot for your specific needs.
The ability to adjust proportions allows for flexibility. If you find certain additives improve the strength of your mix, feel free to lean into that. That said, tinkering too much can lead to instability, so any alterations should be approached cautiously. The learning curve with proportions might present some challenges, but it’s also a valuable opportunity for growth in your crafting abilities.
The End: Ensuring Recipe Efficacy
Crafting a perfect recipe for RCF is not merely an exercise in following steps but an intricate dance of understanding materials, techniques, and outcomes. The conclusion to this discussion is pivotal as it distills the chaos of concrete knowledge into actionable insights. The efficiency of an RCF recipe hinges on careful consideration of every element discussed throughout this guide.
One significant aspect to consider is how a well-performing RCF recipe directly impacts the durability and safety of construction projects. This, in itself, is a compelling reason to prioritize efficacy. Every time a recipe is crafted, one should ponder: Is this going to yield a strong structure that withstands the test of time? Keeping this question at the forefront ensures that one does not lose sight of the ultimate goal - a reliable, resilient, and effective concrete frame.
"A recipe is only as good as the sum of its parts."
Furthermore, adhering to quality control measures and ensuring that materials are sourced from reputable suppliers can greatly enhance the final outcome. This emphasis on quality will not only improve the immediate results but also foster a sustainable approach within the industry.
Recapping Key Insights
As we wrap up our exploration, it’s essential to revisit the core components that contribute to a successful RCF recipe. Here's a summarized recap:
- Material Selection: Understanding the right types of concrete and additives is crucial. Choosing the right materials influences strength and longevity.
- Proper Mixing Techniques: Uniform mixing avoids weak points in the concrete that could lead to potential structural failures.
- Quality Assurance Measures: Regular testing like the slump and compression tests are vital. They help ascertain the consistency and strength of the mix.
- Application Techniques: Effective placement and curing methods, including moisture control, are indispensable for achieving desired results.
By keeping these elements in mind, individuals can ensure that they are on the right path to crafting an RCF recipe that is not just efficient but also results in high-quality structures capable of standing firm against time.
Future Directions in RCF Recipe Development
Looking ahead, the future of RCF recipe development offers exciting opportunities. Advances in technology, like artificial intelligence and blockchain, could streamline ingredient sourcing and auditing processes, ensuring premium material selection and traceability. This could potentially lead to the development of smarter recipes, tailored specifically for geographic and climate conditions.
Moreover, innovating with sustainable materials will likely reshape the landscape of concrete production. The shift towards more eco-friendly additives and recycled materials prepares the industry for a greener future. There’s a growing demand for RCF recipes that not only meet conventional performance standards but also minimize environmental impact.
In addition, embracing automation in mixing and application processes can enhance efficiency. This could lead to better consistency and less human error, ultimately refining the craftsmanship of RCF recipes.
As the industry evolves, those who stay ahead of these trends will find themselves in a favorable position. Exploring new methodologies and remaining adaptable will be key for any professional looking to master RCF recipes in the years to come.