Creating Cyclonite: A Comprehensive Guide
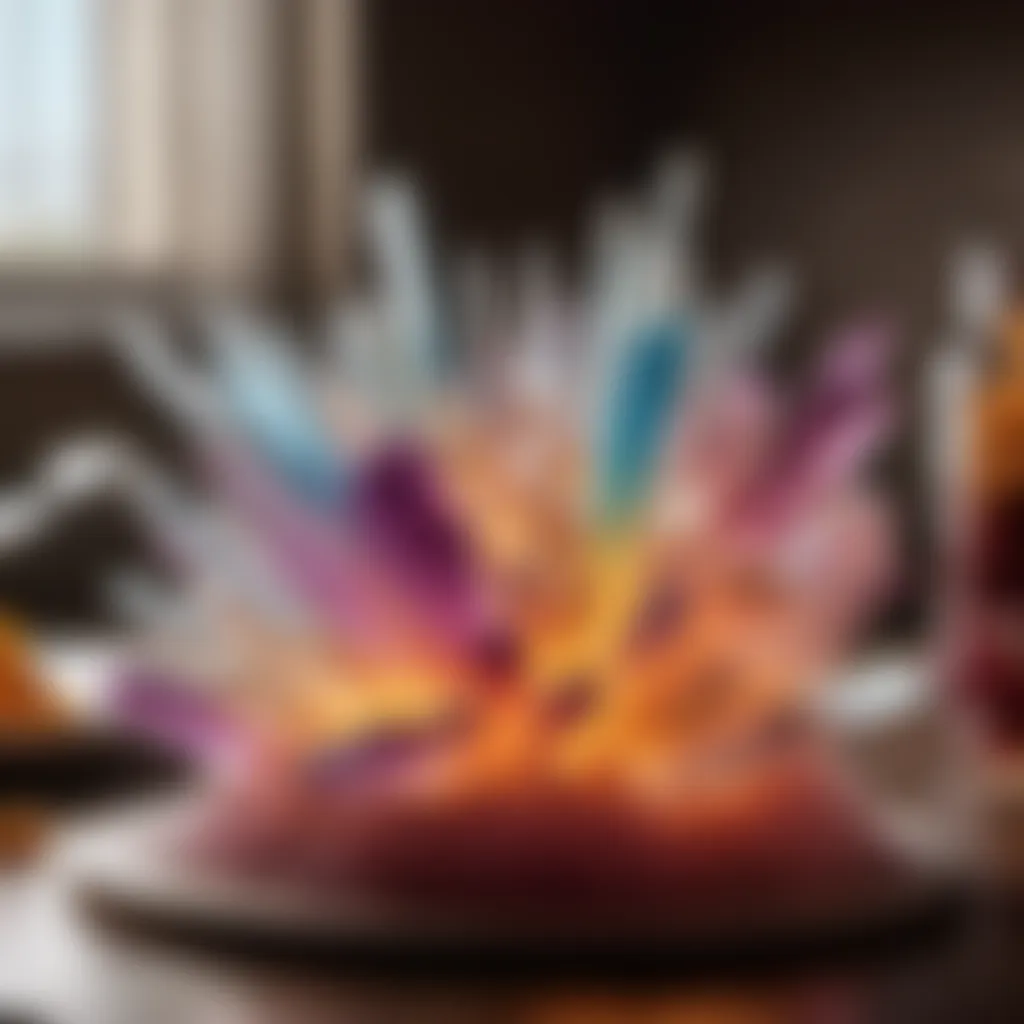
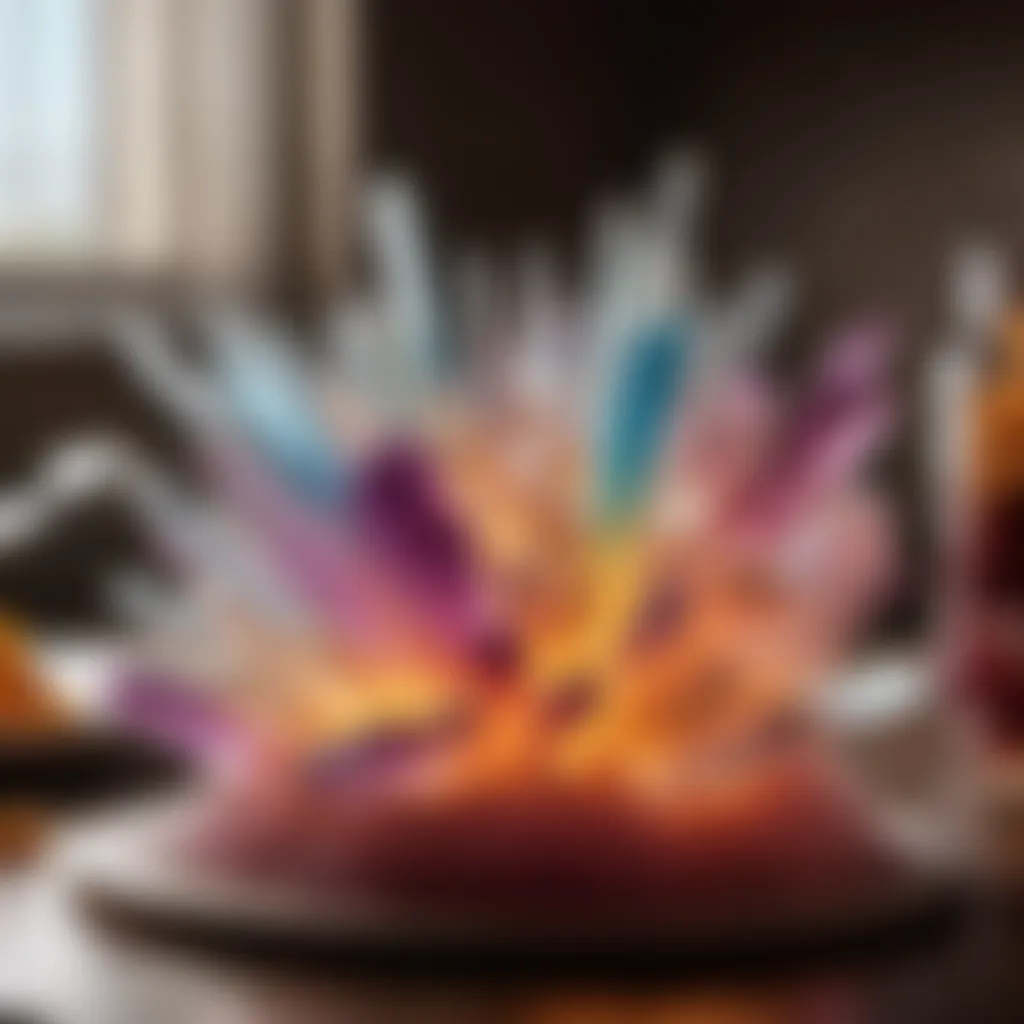
Intro
The process of creating cyclonite is not just a straightforward dump-and-mix affair; it’s a meticulous journey that requires precision and responsibility. Cyclonite, also known as RDX, is a widely recognized explosive that boasts reliability in numerous applications, ranging from military operations to civil engineering projects. Understanding its creation is crucial for those intrigued by the chemistry behind explosives, especially in contexts demanding safety and efficacy.
In this article, we will break down the intricate steps involved in crafting cyclonite, delving into the essential ingredients, preparation guidance, technical aspects, and cooking processes. Our aim is to equip you with the knowledge you need, whether you're a professional in the field or simply curious about how such explosives are manufactured. Let's embark on this detailed exploration, taking a responsible approach while keeping safety at the forefront.
Ingredients:
Creating cyclonite requires a careful selection of chemical compounds. The following list details the necessary ingredients along with their exact measurements. Always prioritize safety when handling these materials:
- Hexamine: 100 grams
- Nitric Acid (HNO₃, concentrated): 300 milliliters
- Sulfuric Acid (H₂SO₄, concentrated): 100 milliliters
- Water: 200 milliliters
- Ammonium Nitrate: 200 grams
It’s essential to note that these ingredients should be stored in a well-ventilated area, away from any ignition sources. Protective gear like gloves and goggles must be worn throughout the process.
Preparation Steps:
Detailed Instructions:
- Setting Up Your Workspace: Ensure your workspace is tidy and free of clutter. Gather all ingredients and safety equipment.
- Mixing Acid Solutions: In a fume hood, carefully combine the concentrated nitric acid and sulfuric acid in a beaker. Stir gently and let it cool to room temperature.
- Dissolving Hexamine: Add the hexamine into the cooled acid mixture. Stir continuously until fully dissolved.
- Combining Ammonium Nitrate: Carefully, add ammonium nitrate to this mixture while stirring for an additional five minutes. Controlling the temperature is paramount here.
- Water Addition: Add water slowly while continuing to stir. This helps in creating a uniform mixture conducive for cyclonite synthesis.
Important Note: Always add acid to water, not the other way around, to prevent exothermic reactions that may cause splashes or spills.
Technical Aspects:
Understanding the technical aspects behind cyclonite production is key to mastering this craft. Here are a few critical parameters to follow:
- Temperature Settings: Maintain a temperature around 18–25°C during the dissolving process.
- Timing Specifics: Ensure that each mixing step lasts at least five to ten minutes to promote thorough integrations of the compounds.
- Critical Techniques: Gentle stirring is crucial; too vigorous stirring may lead to unwanted reactions.
Cooking Process:
Sequential Steps:
- Initial Reaction: After combining all ingredients, allow the mixture to stand undisturbed for one hour. This time is vital for the chemical reaction to occur adequately.
- Cool Down Phase: Post reaction, the solution must be cooled in an ice bath to solidify the cyclonite formed.
- Crystallization: After cooling, filter the resulting mixture through fine gauze to collect cyclonite crystals.
- Washing Crystals: Rinse the collected crystals using distilled water to remove any residual acids. This step ensures purity.
- Drying: Spread the washed crystals on a clean surface and allow them to air dry completely before storage.
Troubleshooting Tips:
- If the solution doesn’t crystallize after cooling, ensure the temperature was maintained throughout the mixing process. Insufficient cooling can hinder crystallization.
- If you notice excessive fuming during mixing, it may indicate a reaction gone awry; cease operations and ventilate the area immediately.
In summary, the creation of cyclonite encompasses detailed processes requiring strict adherence to safety and precise measurements. By mastering these aspects, one not only learns the method but also the importance of handling such materials responsibly.
Prologue to Cyclonite
Understanding cyclonite begins with recognizing its significance in various applications, particularly in military and industrial sectors. Cyclonite, a high-performing explosive known for its stability, has made a notable mark due to its effectiveness. This section unpacks the fundamental aspects surrounding cyclonite, zeroing in on its definition and importance, along with a brief look at historical context.
Definition and Importance
Cyclonite is a type of explosive that falls within the category of nitramine explosives. Specifically, its chemical formula, C₆H₈N₄O₆, points to a complex structure that contributes to its high energy output compared to traditional explosives. The importance of cyclonite in contemporary usage cannot be overstated. Its characteristics allow for a wide range of applications—from military use in munitions to applications within the oil and gas industry for demolition purposes.
Cyclonite's stability in transportation and storage makes it a preferred choice over other, more volatile explosives. In a world where safety is paramount, the ability to handle such powerful materials without unintended detonation offers peace of mind to professionals working in hazardous environments. The controlled energy release during reactions is a game-changer for end-users, which leads to precise outcomes during implementation.
If you think about it, cyclonite acts like the reliable friend who shows up on time—never underdelivering when it's needed most. Its role in ensuring effective blast performance in diverse scenarios resonates with the importance of meticulous attention in crafting explosives. Thus, comprehending cyclonite is not just about its ingredients or processes; it is about appreciating its invaluable role across various industries.
Historical Background
To fully grasp the essence of cyclonite, we can take a brief detour into its history. Developed during World War I, cyclonite was a breakthrough that transformed explosives technology. Initially derived from the desire for materials that would deliver a punch without a rapid decomposition rate, it swiftly proved itself as an essential component in military arsenals.
In the early days, scientists sought alternatives to the unstable nitroglycerin. The formulation of cyclonite arose from these efforts, backed by rigorous research and experimentation. Fast-forward to the present day, and we find cyclonite prominently featured not just in combat scenarios but also in construction and mining.
The development and understanding of its chemical properties took decades, leading to regulations and manufacturing standards that we adhere to today. It's fascinating how something so complex started from a need in warfare, evolving over the years into a varied, regulated compound.
In summary, cyclonite represents both an evolution in explosive material design and a concerted effort to balance effectiveness with safety. This historical context sets the stage for deeper insights that will follow in subsequent sections surrounding its chemical composition, synthesis methodologies, and safety considerations.
Chemical Composition of Cyclonite
Understanding the chemical composition of cyclonite is like reading the secret recipe book for one of nature's most intricate substances. It's a mixture that can either explode into chaos or achieve remarkable stability, depending on how its ingredients are combined and treated. The foundational elements of cyclonite not only lend it its explosive capabilities but also inform its applications across different industries. Specifying what goes in and why it matters makes this section a key pillar of the article.
Key Ingredients
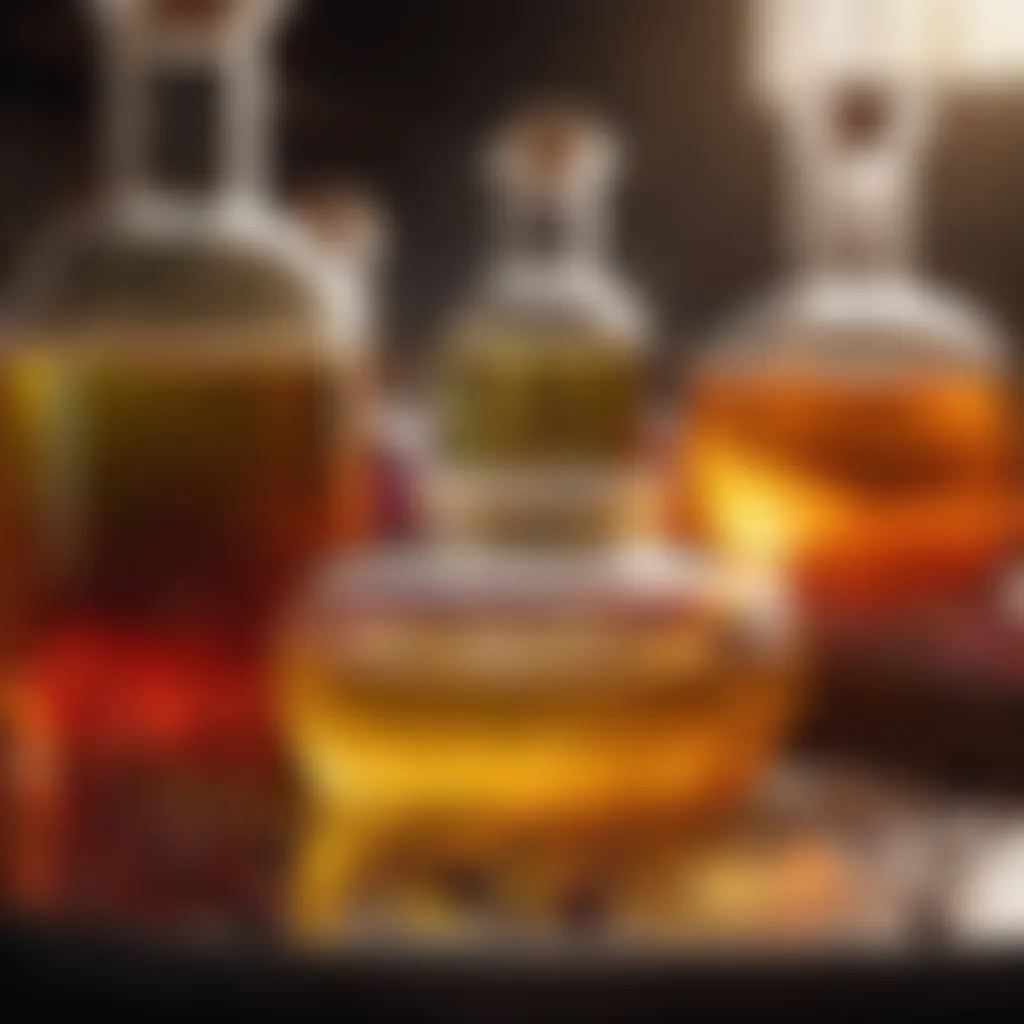
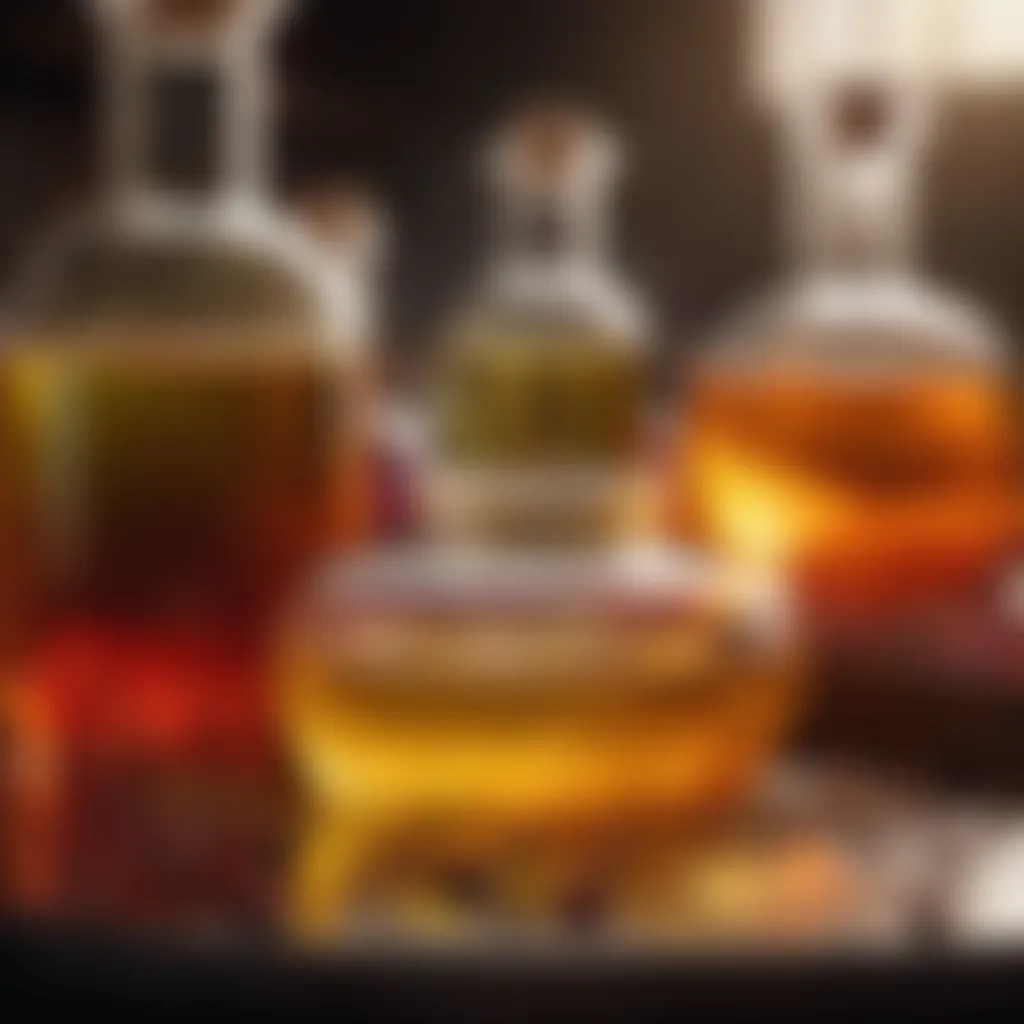
When discussing cyclonite, we can't sidestep the essential components that bring this explosive to life. Here are the primary ingredients that shape its production:
- Hexogen (RDX): This is the heavy hitter of the bunch, serving as the primary explosive ingredient. It's renowned for its high detonation velocity and thermal stability.
- Nitroglycerin: Often included as a modifier, nitroglycerin enhances the sensitivity of cyclonite while also contributing to its overall explosiveness. Too much, however, can be dangerous.
- Other Additives: Various stabilizers and solvents like paraffin wax may be used to help manage properties like sensitivity and handling characteristics.
Each ingredient serves a unique role, and their combined chemistry outlines the backbone of cyclonite's performance. When accurately measured and mixed, these components create a powerful and reliable explosive that is both effective and relatively stable when handled properly. Attention must be paid to the proportions, as the line between stability and instability can be thin.
"It's not just about having the right ingredients; it's about knowing how they work together."
Chemical Properties
The chemical properties of cyclonite are paramount to the understanding of its functionality. Here are the most critical properties that make it stand out:
- Detonation Velocity: Cyclonite boasts a high detonation velocity, which is crucial for its effectiveness in applications requiring rapid energy release.
- Density: The density of cyclonite contributes to its energy concentration, impacting how it's employed in military and industrial settings.
- Sensitivity: The response of cyclonite to heat, shock, or friction can vary significantly based on its chemical composition. The presence of additives like nitroglycerin can either boost or mitigate this sensitivity.
- Thermal Stability: A vital characteristic that determines how cyclonite behaves under different temperature conditions. High stability ensures it doesn't accidentally detonate under pressure but still performs when required.
Understanding these properties allows for better handling and application. Each property not only informs the ingredient list but also paints a picture of how cyclonite functions in real-world scenarios, from military operations to construction jobs. Attention to detail in its composition can mitigate risks while enhancing performance, making it an innovative product in explosive manufacturing.
Synthesis Methodology
Understanding the synthesis methodology is paramount to mastering the creation of cyclonite. This process not only encompasses the technical aspects of mixing and creating but also ensures quality and safety throughout. The right methodology guarantees consistency, which is critical in explosive manufacturing. Achieving a high-quality product relies on being meticulous at each step of the synthesis process.
Equipment Required
To synthesize cyclonite, certain tools and materials are essential. Below are the key pieces of equipment you’ll need:
- Fume Hood: Provides a safe workspace by ventilating toxic fumes.
- Glass Stirring Rod: Used for precise mixing of chemical compounds without contamination.
- Digital Scale: For accurate measurement of materials. Precision is non-negotiable here.
- Heat Source: A controlled heat source is crucial for specific chemical reactions; hot plates are preferable.
- Reagents: Ensure high purity and quality for reliable results, specifically hexamine and nitric acid.
Having the proper equipment not only enhances safety but aids in achieving the desired reaction while minimizing risks.
Step-by-Step Procedure
- Preparation: Begin by thoroughly cleaning your workspace and assembling your materials. Safety should always be the first thought.
- Mixing Ingredients: In a fume hood, combine hexamine with nitric acid in a glass container. Stir gently, maintaining a controlled environment to prevent any abrupt reactions.
- Control Temperature: Heat the mixture gradually. Utilize your digital thermometer to ensure you don’t exceed the critical temperature thresholds.
- Reaction Monitoring: As the mixture reacts, maintain close observation. The color and texture changes are indicators of the process.
- Final Crystallization: Once the reaction slows, cool the mixture, allowing crystals to form. This stage is where the quality of your cyclonite begins to take shape.
- Harvesting: Gently extract the crystals and avoid forceful actions that may destabilize them.
Each of these steps calls for a keen eye and a steady hand. Skipping or rushing through them can lead to subpar products and potentially dangerous situations.
Quality Control Measures
Quality must be a constant concern during the synthesis of cyclonite. Implementing stringent quality control measures assures that each batch meets safety and performance standards.
- Batch Testing: Regularly sample your produced material and test for purity. Ensure it aligns with expected chemical properties.
- Documentation: Keep meticulous records of your processes and results. Such data serves as a foundation for refining methods in the future.
- Visual Inspection: Examine the final product for uniformity in size and consistency. Any irregularities may signify a problem earlier in the synthesis.
“In the world of synthesis, it’s not just about achieving a result; it’s about ensuring that the result is consistent and safe.”
Integrating these quality control measures will not only bolster the integrity of your product but also enhance credibility within the industry. It’s vital that every step of synthesis methodology is respected as part of a larger picture in explosive manufacturing.
Safety Considerations
When dealing with the creation of cyclonite, it is crucial to highlight the safety considerations involved in the entire process. The nature of explosives necessitates a high level of caution and awareness to prevent accidents and ensure a safe working environment. An integral part of this undertaking is understanding the specific hazards associated with various materials and processes involved.
Not only does this ensure the safety of the personnel involved, but it also minimizes risks to surrounding environments and communities. Recognizing potential hazards and instituting effective protective measures can save lives and prevent significant property damage. Therefore, prioritizing safety protocols is not merely a regulatory obligation; it serves as the backbone of responsible explosive manufacturing.
Hazard Identification
Identifying hazards is the first step in safeguarding against potential risks when creating cyclonite. The process encompasses several key stages where dangers may arise, and these include:
- Chemical Exposure: Chemicals used in the production of cyclonite, such as liquid nitroglycerin, can be highly toxic or irritative. Direct interaction or inhalation is a significant risk.
- Physical Risks: The mixing, transporting, and storing of volatile materials can lead to accidents if strict procedures are not adhered to.
- Environmental Hazards: Any spillage or uncontrolled reaction may have dire consequences on local ecosystems.
"A stitch in time saves nine." Identifying hazards before they escalate is a wise strategy.
By adopting a meticulous approach to hazard identification, one can intervene proactively. Regular training and thorough assessments enable personnel to stay aware of their immediate environment and the materials they handle.
Risk Mitigation Strategies
After identifying hazards, establishing effective risk mitigation strategies is essential to manage and minimize these dangers. This involves implementing organized procedures and guidelines, such as:
- Personal Protective Equipment (PPE): Use appropriate gear like gloves, goggles, and masks at all times to safeguard against chemical exposure.
- Proper Ventilation: Ensuring that workspaces are well-ventilated can dilute harmful fumes and reduce the risk of inhalation.
- Emergency Protocols: Outlining clear emergency response procedures, in case of spills or unexpected reactions, can save valuable time and potentially lives.
- Training Programs: Regular drills and training sessions create an informed workforce able to respond accurately to any risky situation.
- Regular Inspections: Consistent checks of equipment and materials can help identify wear and tear, taking preventive measures before they lead to incidents.
By prioritizing these fundamental aspects of safety, the manufacturing of cyclonite can be performed with minimized risk, providing a stable foundation for high-quality production.
Regulations and Compliance
In the realm of explosives, especially regarding cyclonite, regulations and compliance form the backbone of responsible practice. The production of explosives is no laughing matter—there are strict guidelines that must be followed to ensure safety and legality. Ignoring regulations could lead to disastrous consequences, not just for the individuals involved but also for the broader community. One small misstep can trigger a series of events that escalate far beyond what was initially intended.
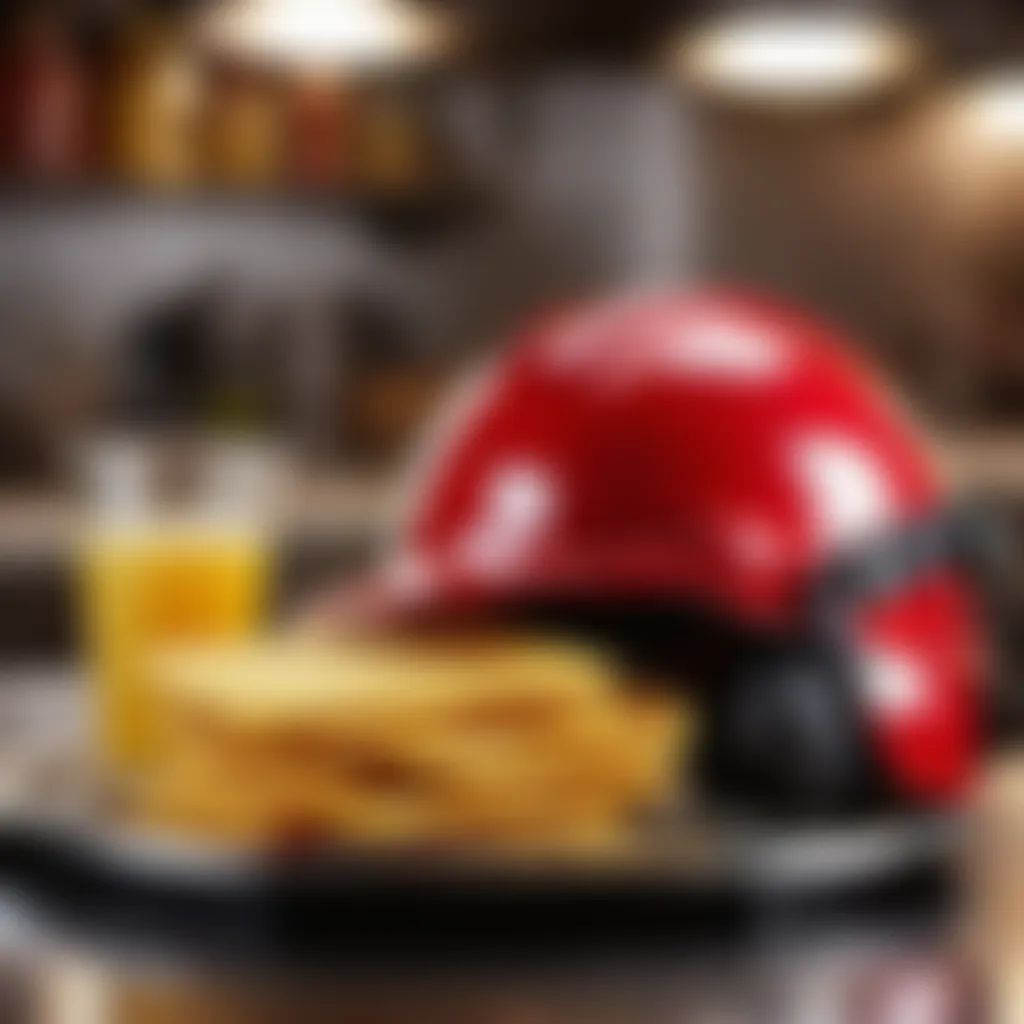
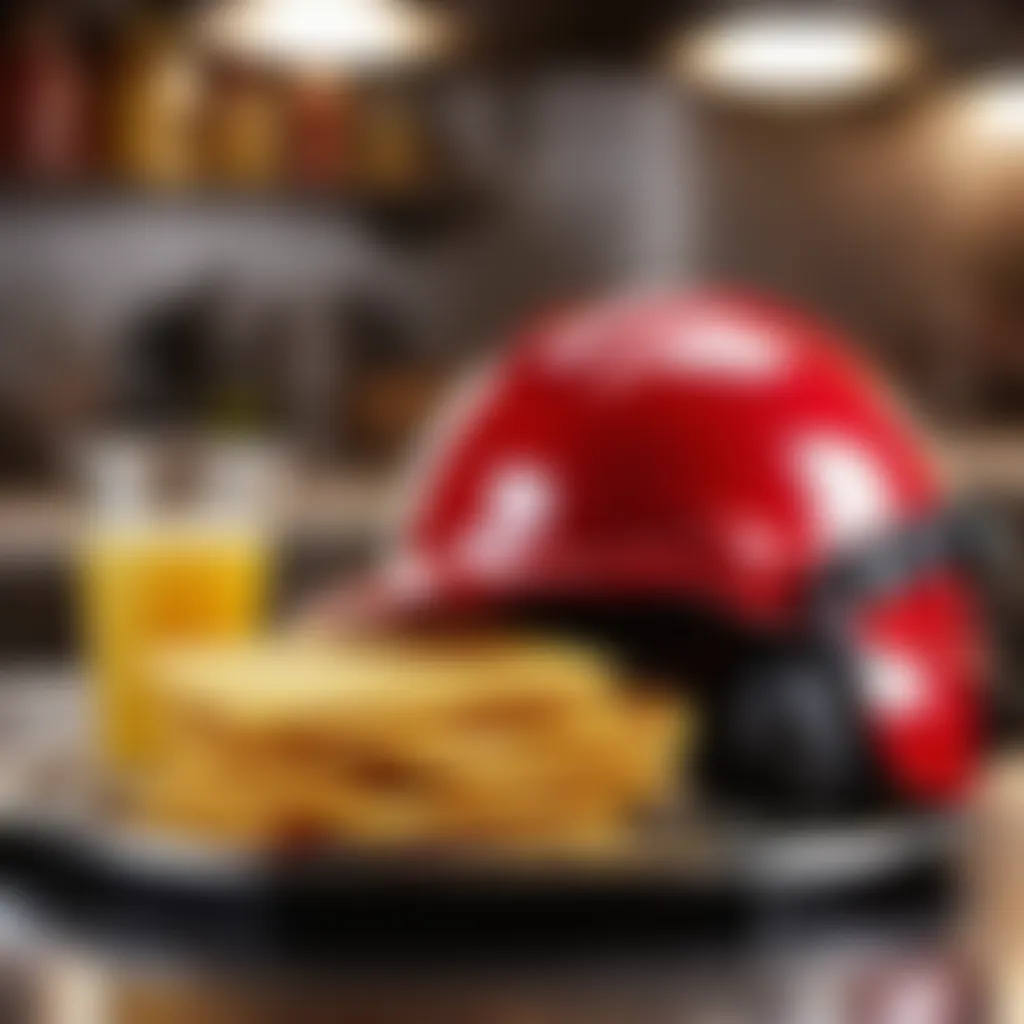
The importance of adhering to these regulations cannot be overstated. Not only do they protect people and the environment, but they also ensure that the products being created meet specific quality and performance standards. Regulatory bodies often set frameworks that govern every stage of production, from raw material sourcing to the final product's usage. These standards are designed to minimize risks and promote safety, essential factors when dealing with explosive substances.
Furthermore, compliance with regulations can enhance a company’s reputation. When a manufacturer is known to adhere strictly to lawful practices, it not only garners trust from customers but also builds relationships with regulatory agencies. This leads to a smoother operational process, reducing potential roadblocks due to legal issues or safety violations.
National and International Guidelines
Both national and international guidelines play a critical role in shaping policies for cyclonite production, helping standardize practices across borders. In the United States, organizations like the Bureau of Alcohol, Tobacco, Firearms and Explosives (ATF) and the Occupational Safety and Health Administration (OSHA) set forth strict guidelines that manufacturers must follow. These cover everything from storage practices to marketing and sale conditions.
On the international stage, treaties and agreements such as the Convention on Certain Conventional Weapons aim to ensure that explosives don’t fall into the wrong hands and that their use is regulated. Countries must align their local laws with these international guidelines, creating a global framework that enhances safety and security. Some might say it’s the glue that holds various national regulations together, creating a cohesive approach to explosive materials.
Key National Guidelines Include:
- Licensing: Obtain necessary licenses for production and distribution.
- Storage Protocols: Ensure storage facilities meet safety requirements.
- Personnel Training: Workers must have proper training in handling explosives.
Important International Standards:
- ISO Standards: The International Organization for Standardization sets quality management standards applicable globally.
- Import/Export Controls: Regulations that govern the movement of explosive materials across borders.
Documentation and Reporting
Documentation and reporting provide transparency and traceability in the explosive manufacturing process. It’s not just about having files tucked neatly away. Proper documentation ensures compliance with regulations and serves as a legal safeguard. Should any issues arise, an accurate log of operations provides a clear trail that can help assess responsibility and determine corrective actions.
Each stage of production should be documented, from material sourcing to the final testing of the explosives. This includes records of inspections, personnel training, and safety measures implemented. Not only does this foster a culture of accountability, it also aids in ongoing training and process improvements. Incorporating a robust system for documentation can prevent future mishaps and support continuous improvement initiatives within the organization.
"The best way to ensure compliance is through clear, consistent documentation that adheres to established guidelines."
Key aspects of effective documentation and reporting include:
- Audit Trails: Rigorously maintain records that detail every step taken during production.
- Incident Reports: Document any incidents or near-misses to improve future safety measures.
- Compliance Checklists: Regularly review and update checklists to align with evolving regulations.
Overall, keeping abreast of regulatory compliance and ensuring meticulous documentation is fundamental for those involved in the cyclonite manufacturing process. They not only ensure legality and safety but also enhance operational performance and community trust.
Performance Evaluation
Evaluating the performance of cyclonite is critical to its effective use across various applications. Performance evaluation encompasses several aspects, including testing procedures, analysis of results, and overall effectiveness. This process not only ensures that the explosive meets specific operational standards but also identifies its reliability and stability under diverse conditions.
The significance of performance evaluation cannot be overstated. It serves as a benchmark for comparing cyclonite with other explosives, highlighting its strengths and weaknesses. Accurate performance testing leads to improved formulations and applications, ultimately enhancing safety and effectiveness in its use.
Testing Procedures
Testing procedures for cyclonite involve a meticulous approach to ensure accuracy and reliability. The goal is to gauge its explosive potential under controlled conditions. Here are some common testing methods utilized:
- Impact Sensitivity Tests: This evaluates how easily cyclonite can be detonated through impact. A sample is subjected to a controlled weight drop, measuring the threshold energy needed for detonation.
- Thermal Stability Tests: Understanding how cyclonite behaves under varying temperatures is imperative. Samples may be subjected to heat exposure to assess decomposition rates and stability.
- Velocity of Detonation (VOD) Tests: This measures how fast the detonation wave travels through cyclonite, providing insights into its efficiency and energy output.
- Subjection to Shock Waves: By exposing cyclonite to shock waves, testers can observe how it reacts, which is particularly useful for military applications.
These testing procedures are carefully documented and analyzed, ensuring that the final product meets stringent standards. Each test plays a crucial role in understanding the explosive's behavior and potential hazards.
Analysis of Results
Once testing procedures are completed, analyzing the results forms the backbone of performance evaluation. This analysis offers insights into various aspects of cyclonite, such as:
- Reliability: Evaluating how consistent cyclonite performs compared to other explosives helps determine its utility in different situations.
- Stability under Pressure: Results from tests that diminish the risk of accidental detonation under pressure provide essential data for safe use.
- Comparative Assessment: Analyzing data in relation to similar explosives allows users to make informed decisions regarding cyclonite's application.
To derive meaningful insights from the data, specialists often utilize statistical methods and software tools for thorough analysis. This ensures that conclusions drawn are not only data-driven but also backed by rigorous methodologies.
Performance evaluation is pivotal, enabling manufacturers and users to refine and optimize cyclonite for its intended applications.
In summary, the effectiveness of cyclonite relies significantly on systematic performance evaluations. Thorough testing and result analyses are essential, as they lead to informed methodologies and improved formulations, ensuring that this energetic material operates at its peak efficiency.
Applications of Cyclonite
The applications of cyclonite are a fundamental aspect of its significance in contemporary explosive technology. Understanding these uses sheds light on its versatility, which goes beyond mere construction into military strengths and industrial transformations. Cyclonite, recognized for its impressive stability and performance, finds a place in various scenarios that require reliable detonation beyond traditional explosives.
Military Use
Cyclonite, often found in military settings, plays a critical role due to its capability as a high-performance explosive. The military depends on its properties for various applications, such as demolitions, munitions, and even certain types of propellants. The importance of cyclonite in military operations ranges from its use in bombs to specialized munitions.
- Demolition: In combat scenarios, precision demolition can lead to strategically advantageous positions. Cyclonite provides the necessary power while maintaining control over explosive effects.
- Munitions: The reliability of cyclonite makes it a favored choice in crafting munitions, enhancing their effectiveness and safety.
- Propellants: Its low sensitivity and stability under various conditions mean that cyclonite can be used effectively in propellants needed for guided munitions or artillery shells.
Cyclonite's effectiveness is not just in its power but in how it can be engineered for specific operational needs, providing essential flexibility on the battlefield.
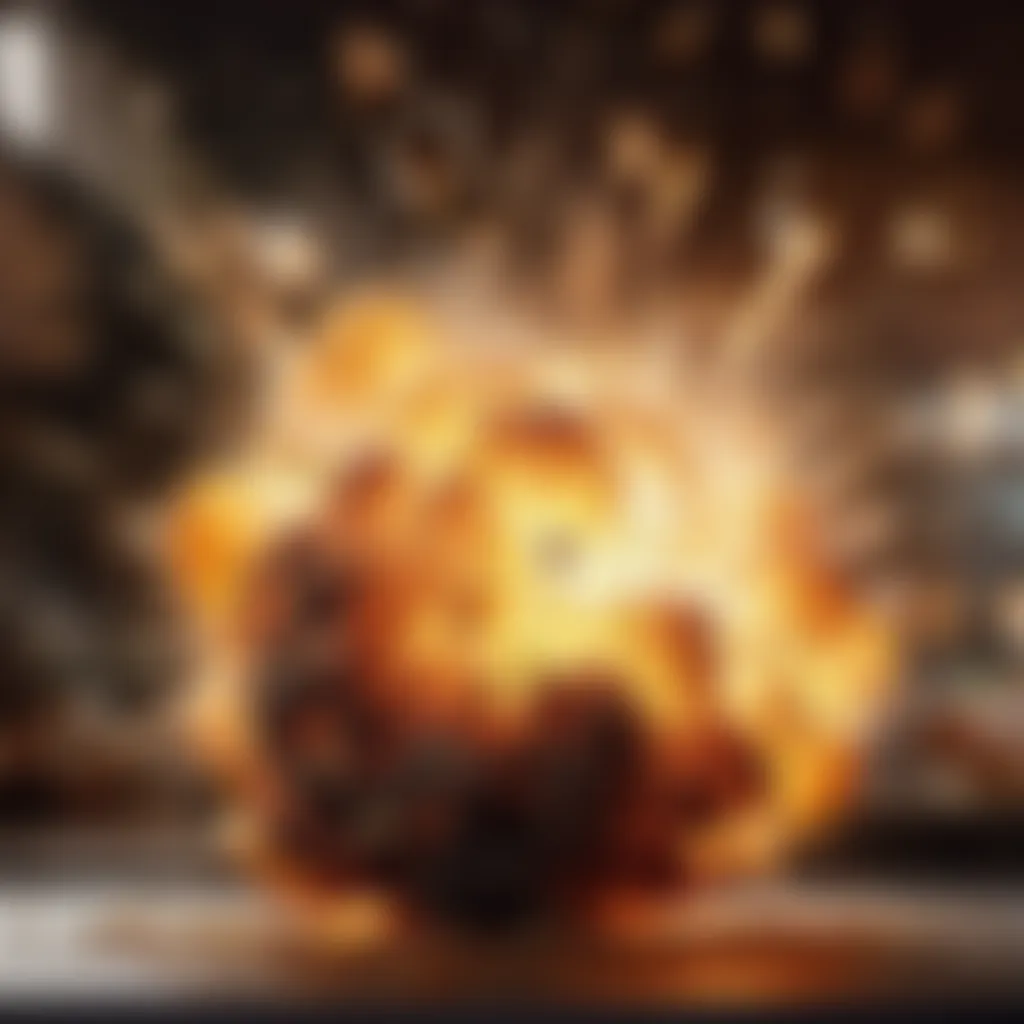
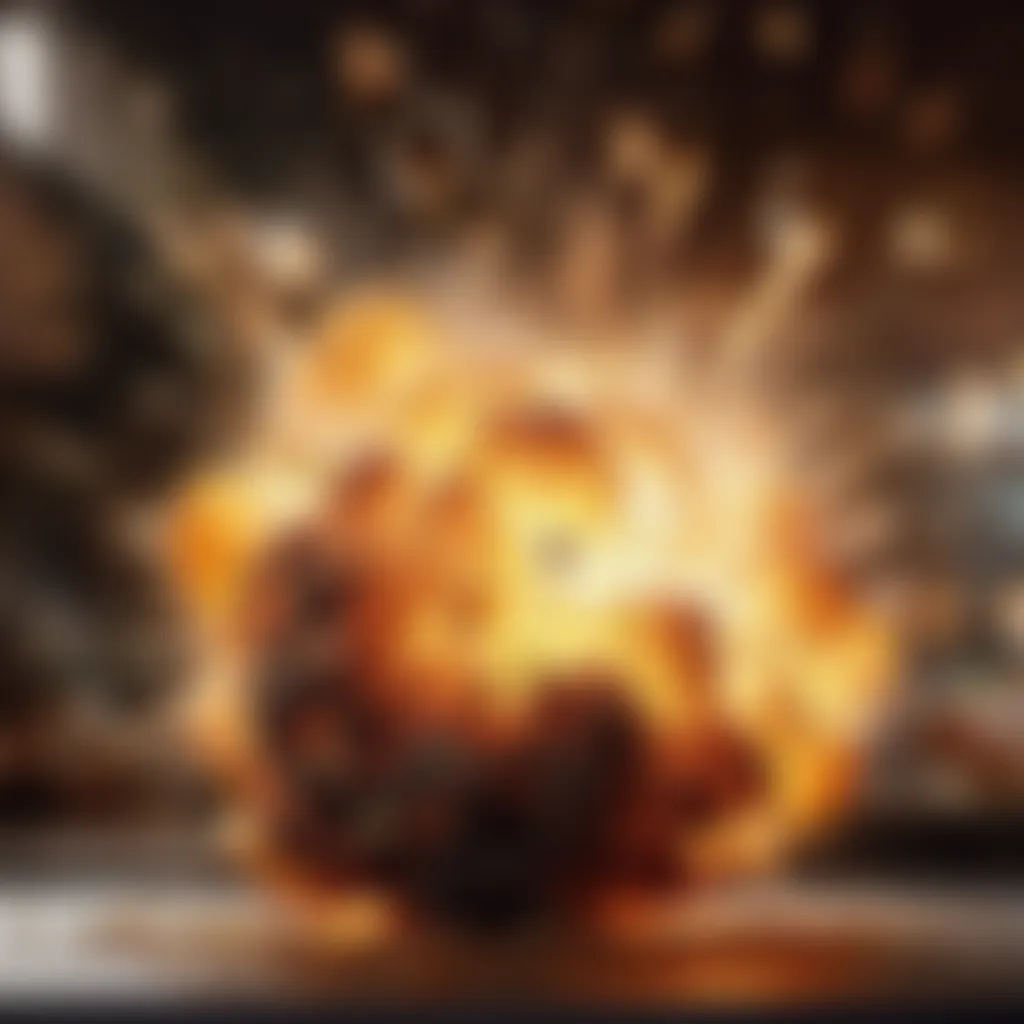
Industrial Applications
The use of cyclonite is not limited to military contexts; it also has vital industrial applications. Industries rely on its characteristics for construction, mining, and demolition processes, highlighting its broader utility beyond warfare.
- Construction: In heavy construction, cyclonite helps to break down obstructions like boulders or concrete. Its ability to create controlled blasts facilitates building projects without excessive disruption.
- Mining: In mining operations, cyclonite caters to blasting needs, proving crucial for the extraction of minerals. Its predictable performance ensures that additional costs and risks are minimized.
- Demolition: It’s not just about breaking ground; cyclonite also finds use in controlled demolitions of old structures. This control mitigates risks associated with traditional blasting methods and improves safety.
- Quarrying: The quarrying industry benefits from cyclonite for shaping rock formations and excavating materials efficiently.
As cyclonite continues to evolve, its applications expand, fostering advancements in how we harness explosive technology for various industries.
Each of these applications underscores cyclonite’s role as a versatile explosive, vital to both military and civilian sectors. The balance it strikes between power, stability, and versatility cements its importance in the field of explosive manufacture.
Environmental Impact
The impact of cyclonite production on the environment is a crucial aspect that cannot be overlooked. As the world becomes more aware of environmental issues, it is mandatory to evaluate how explosive manufacturing, specifically cyclonite, interacts with our ecosystem. Understanding pollution concerns and adopting sustainable practices are essential for minimizing negative effects while ensuring that the production of this explosive remains efficient and safe.
Pollution Concerns
One of the main worries surrounding cyclonite production is the potential pollution created during its manufacture. The processes involved often lead to the release of hazardous waste materials. These can include chemical solvents and byproducts that, if not managed carefully, can seep into waterways or contaminate the soil.
Moreover, the process of synthesis can sometimes produce emissions that contribute to air pollution, posing risks to both human health and wildlife. Thus, it is essential for producers to:
- Conduct thorough assessments of potential pollutants.
- Implement rigorous waste management strategies to prevent run-off.
- Explore alternative materials that could minimize harmful emissions.
Advantages can be gained from awareness and proactive measures: not only do they protect the environment, but they also enhance the reputations of producers by showcasing responsible practices.
Sustainable Practices
Transitioning to sustainable practices in the production of cyclonite can create a win-win situation. By modifying methods and materials, manufacturers can significantly reduce their environmental footprint while maintaining high product quality. Here are some methods to consider:
- Using eco-friendly solvents: Switching to biodegradable solvents can decrease harmful emissions during production.
- Recycling water: Having a closed-loop water system can ensure that water waste is minimized, reducing environmental stress.
- Conducting regular audits: Frequent examinations of facilities for compliance with environmental standards can keep production in check and reduce risks.
Not only does adopting these practices have immediate benefits for the environment, but it also aligns with increasing regulatory pressures from governments and the public. By approaching production with an environmental mindset, the industry can ensure long-term viability and sustainability.
Addressing pollution concerns and integrating sustainable practices into cyclonite production is more than a regulatory necessity; it's a commitment to the future of both the industry and the Earth itself.
As the explosive industry evolves, so does the responsibility to mitigate its impact on the environment. Exploring these elements illustrates the complexities and the potential for growth towards a more sustainable future.
Future Trends in Explosive Manufacturing
The landscape of explosive manufacturing is evolving at a breathtaking pace. As we look toward the future, several trends can be observed that promise to reshape the industry. The importance of these trends cannot be overstated, as they impact everything from safety protocols to environmental considerations and production efficiency. For anyone involved in the effective production of materials like cyclonite, staying abreast of these changes is essential. These shifts do not merely refine existing practices; they can revolutionize how explosives are designed, produced, and utilized across various sectors.
Innovations in Chemistry
One of the most compelling directions in explosive manufacturing is found in the innovations in chemistry. Advances in material science and chemical engineering are leading to the creation of more stable and efficient compounds. For example, the development of new binder materials can enhance the performance of explosives while reducing their sensitivity to shock or heat.
- Advanced Catalysts: Research shows utilzation of advanced catalysts in the manufacturing process can lead to more efficient reactions, cutting down on production times.
- Green Chemistry Techniques: There's also a push towards utilizing green chemistry principles that not only improve the safety profile of explosives but also minimize toxic by-products. Techniques like solvent-free reactions are gaining traction, reducing the environmental footprint considerably.
These innovations can lead to the formulation of cyclonite with a much higher degree of accuracy and efficiency in the synthesis process. Familial producers may notice that the consistency of quality improves dramatically, leading to fewer defects and higher overall efficacy of the explosive.
Market Developments
Shifting focus to market developments, it's key to acknowledge how the demand for safer, more stable explosives is altering the landscape. Companies must adapt to an evolving clientele that increasingly values not only performance but also environmental responsibility.
- Emerging Markets: The rise of emerging markets in Asia and Africa is changing the game for explosive manufacturers. With increased demand for infrastructure and mining activities, these regions are becoming focal points for growth in the explosives sector.
- Regulatory Pressures: Tighter regulations globally are pushing manufacturers to explore new formulations and production methods that comply with stricter safety standards. This often leads to increased research and development budgets as companies strive for compliance while maintaining profitability.
"The future of explosives hinges not just on what they can do, but how they impact the world around us. As consumer preferences shift, so must our approaches to manufacturing."
Culmination
As we draw the curtain on the exploration of cyclonite, it's vital to reflect on the substantial points we've covered. The conclusion encapsulates the essence of the entire article, shedding light on why understanding cyclonite, a high-grade explosive, is crucial in today’s context.
Summary of Key Points
To summarize, we have traversed a wide landscape:
- Definition and Importance: Cyclonite is not just another explosive. It's a reliable and stable substance that holds significance across various sectors, from military to industrial applications.
- Chemical Composition: We detailed the specific ingredients that make cyclonite potent and effective, emphasizing the nuanced balance of each component.
- Synthesis Methodology: The manufacturing process requires deliberate adherence to safety protocols and quality control measures, ensuring a product that meets rigorous standards.
- Safety Considerations: The article highlighted risks and mitigation strategies, underscoring the paramount importance of safety in handling explosives.
- Regulatory Compliance: Insight into national and international guidelines serves to remind us of the legal frameworks governing the use and production of explosives.
This condensation of our discourse provides a clear roadmap for any professional seeking to understand the landscape of explosive materials better.
Final Thoughts
In closing, the conversation surrounding cyclonite is far from trivial. The intricate balance of chemistry, safety, and regulation shapes not only the effectiveness of the explosive but also its acceptance in society. Recognizing the responsibility that comes with such knowledge is essential. The synthesis of cyclonite is not merely a technical process; it’s a commitment to ethical considerations and adherence to regulations.
The ongoing advancements in this field signal a future where innovations may lead to even safer and more efficient explosive materials. Thus, both seasoned professionals and newcomers alike should stay informed, ensuring a path forward that aligns with safety and responsibility.
Ultimately, understanding cyclonite prepares one for the responsibilities of the craft, contributing positively to the landscape of explosive manufacturing.