The Hard Boiled Machine: Mechanisms in Industry
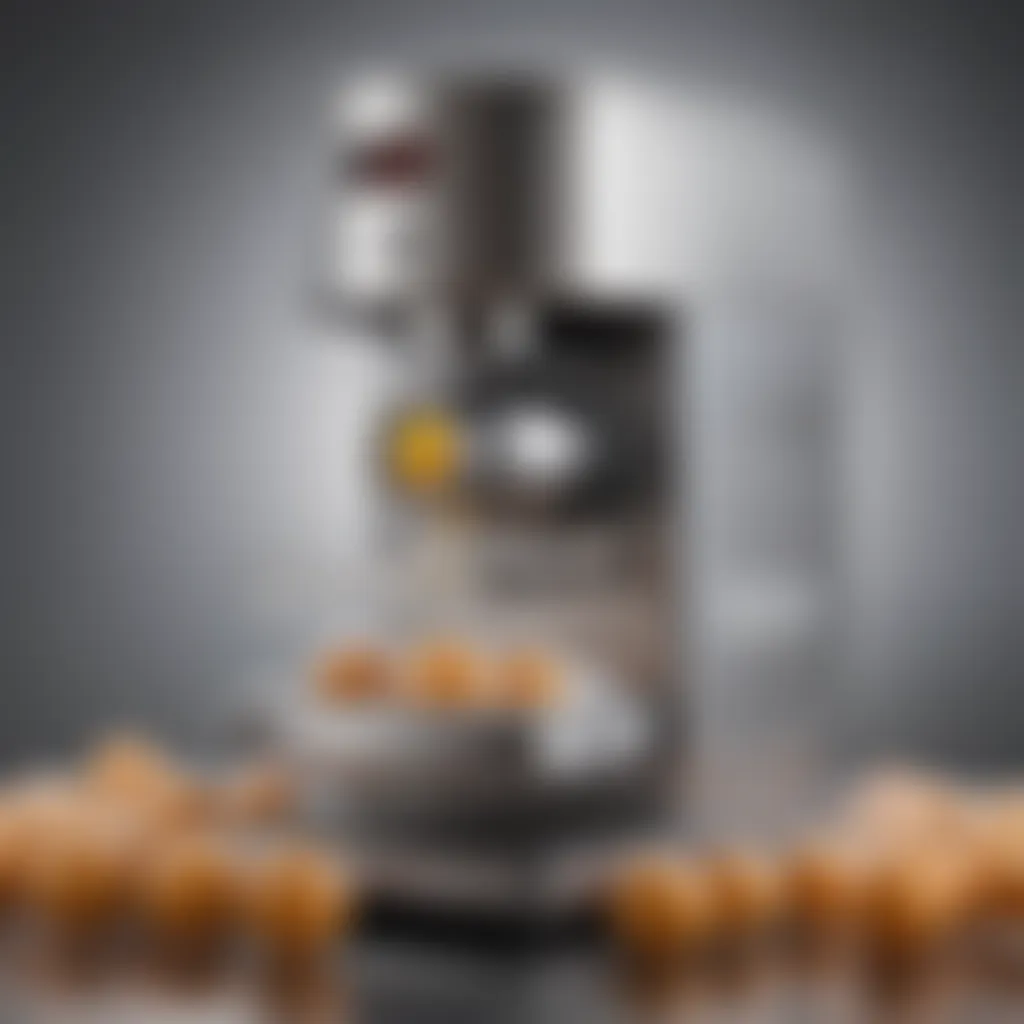
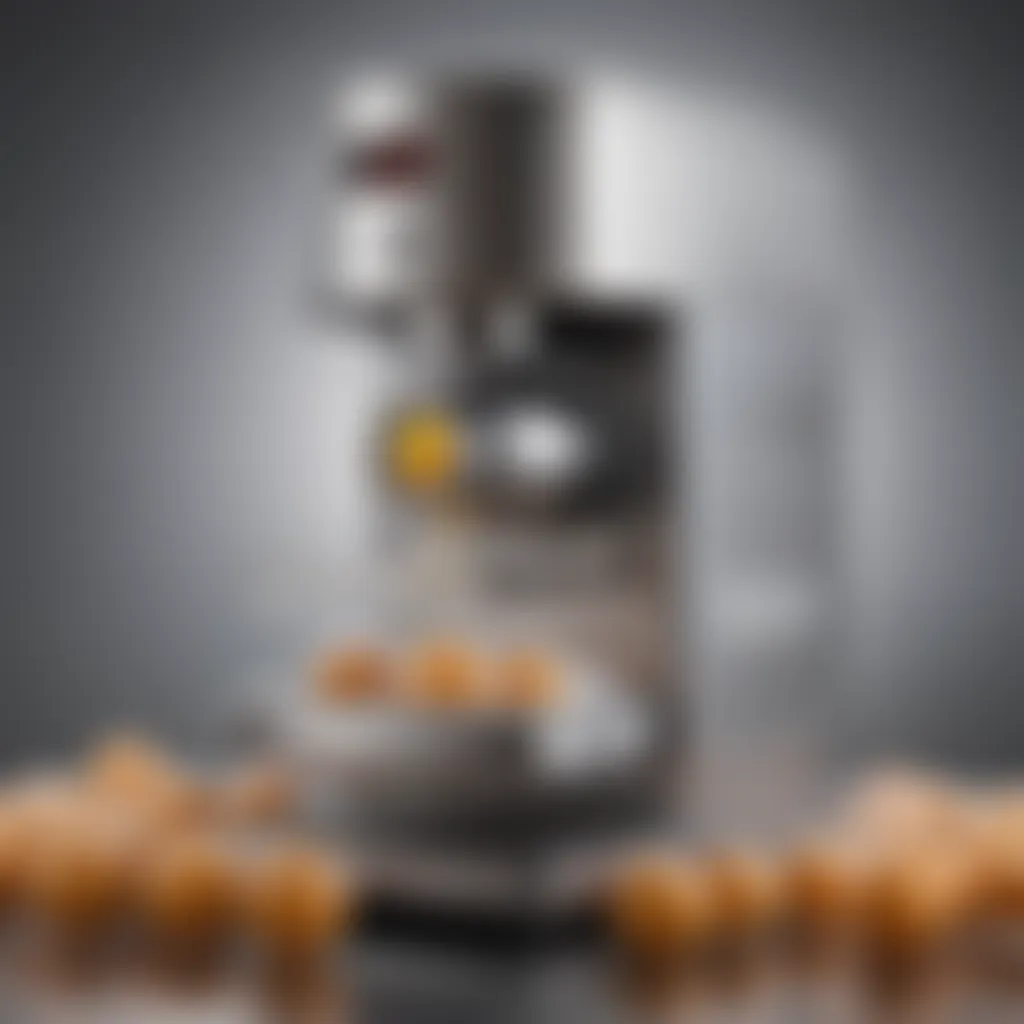
Intro
The exploration of hard boiled machines offers significant insights into their mechanisms and the implications they hold for modern industry. This examination involves understanding how these machines operate at their core, their application in various sectors, and the broader socio-economic factors that govern their deployment.
Understanding these machines is essential. They are not merely tools; they embody the complexity of modern manufacturing. Hard boiled machines stand at the intersection of efficiency, design, and technology. With their applications ranging widely, from food processing to automotive assembly, they demonstrate a remarkable ability to adapt and thrive in diverse environments.
Moreover, as industries worldwide face challenges in sustainability and innovation, the role of hard boiled machines becomes increasingly relevant. Their integration into production lines raises questions not just about efficiency, but also about their long-term implications on labor, environment, and overall economic health.
This article aims to clarify these aspects, inviting you to delve deeper into how these machines function, their impact on modern industry, and the pathways they create for future innovations.
Foreword to Hard Boiled Machines
Understanding hard boiled machines is crucial in todayโs intricate industrial landscape. These machines have become essential tools in various sectors, streamlining processes and enhancing productivity. Their presence signifies a shift towards greater automation and efficiency, responding to the demands of modern production environments. In this article, we will explore their functionalities, design principles, and significant implications in contemporary industry. The benefits of hard boiled machines extend beyond just operational effectiveness; they also influence economic factors and social dimensions.
Definition and Overview
Hard boiled machines are engineered systems that perform specific tasks with high efficiency and precision. They often involve automated processes, utilizing various technologies for optimal performance. The term 'hard boiled' reflects the robustness and reliability characteristic of these machines. Key features generally include durability, high-speed operation, and specialized functionality that cater to industry needs. A diverse range of sectors, such as manufacturing, food processing, and pharmaceuticals, relies on such machines. Their effectiveness makes them integral for achieving production targets while maintaining quality standards.
Historical Development
The evolution of hard boiled machines can be traced back to significant technological advancements in the industrial revolution. Early manufacturing relied heavily on manual labor and rudimentary devices. The introduction of steam power shifted production capabilities, allowing for more complex machinery. As industries advanced, so did the machines; electrical innovations paved the way for automation. Over time, as computational technology emerged, hard boiled machines adapted, integrating sophisticated software and feedback systems to enhance functionality. Today, these machines exemplify the convergence of engineering, technology, and design, reflecting decades of progress and innovation.
Mechanics and Design
Mechanics and design are crucial elements in understanding hard boiled machines, as they form the foundation upon which functionality and performance are built. The design of these machines not only influences their efficiency but also their ability to adapt to various industrial contexts. This exploration will articulate key components, engineering principles, and material considerations that transform a basic concept into a functional piece of machinery.
Key Components of Hard Boiled Machines
The effectiveness of hard boiled machines hinges on several key components. These include:
- Boilers: They generate steam or hot water that drives the entire process. A well-designed boiler ensures optimal heat transfer.
- Heating Elements: These are critical for maintaining consistent temperatures. Various types, such as electric or gas-powered, may be employed depending on the application.
- Control Systems: Modern machines feature sophisticated control systems that allow operators to monitor and adjust settings in real-time, ensuring precision in cooking or processing.
- Safety Features: Protection devices are essential to prevent accidents. These can include pressure gauges, automatic shut-off valves, and temperature sensors.
These components work in harmony to achieve desired outcomes in production settings.
Engineering Principles Involved
Understanding the engineering principles behind hard boiled machines can lead to improved designs and functionalities. Some principles include:
- Thermodynamics: This is the study of heat transfer and energy conversion. Knowledge in this area allows engineers to optimize machines for better energy efficiency.
- Fluid Dynamics: This principle examines how fluids (like steam or water) behave under various conditions. Applications of fluid dynamics improve the precision and efficiency of heating elements and boilers.
- Mechanical Advantage: This concept refers to the ratio of output to input force in machines. By optimizing mechanical advantage, machines can work more efficiently, saving both time and resources.
A thorough understanding of these principles leads to proficient design and operation of hard boiled machines.
Material Considerations
The materials used in constructing hard boiled machines significantly influence their durability and effectiveness. Factors to consider include:
- Heat Resistance: Materials must withstand high temperatures without degrading. Stainless steel is commonly used because of its ability to resist corrosion and handle extreme heat.
- Insulation: Insulating materials are vital to maintain heat within the machine and enhance energy efficiency. Proper insulation can reduce energy costs over time.
- Maintenance Requirements: The ease of cleaning and maintaining materials is important for long-term operation. Non-porous, smooth surfaces are preferable to prevent buildup of residues.
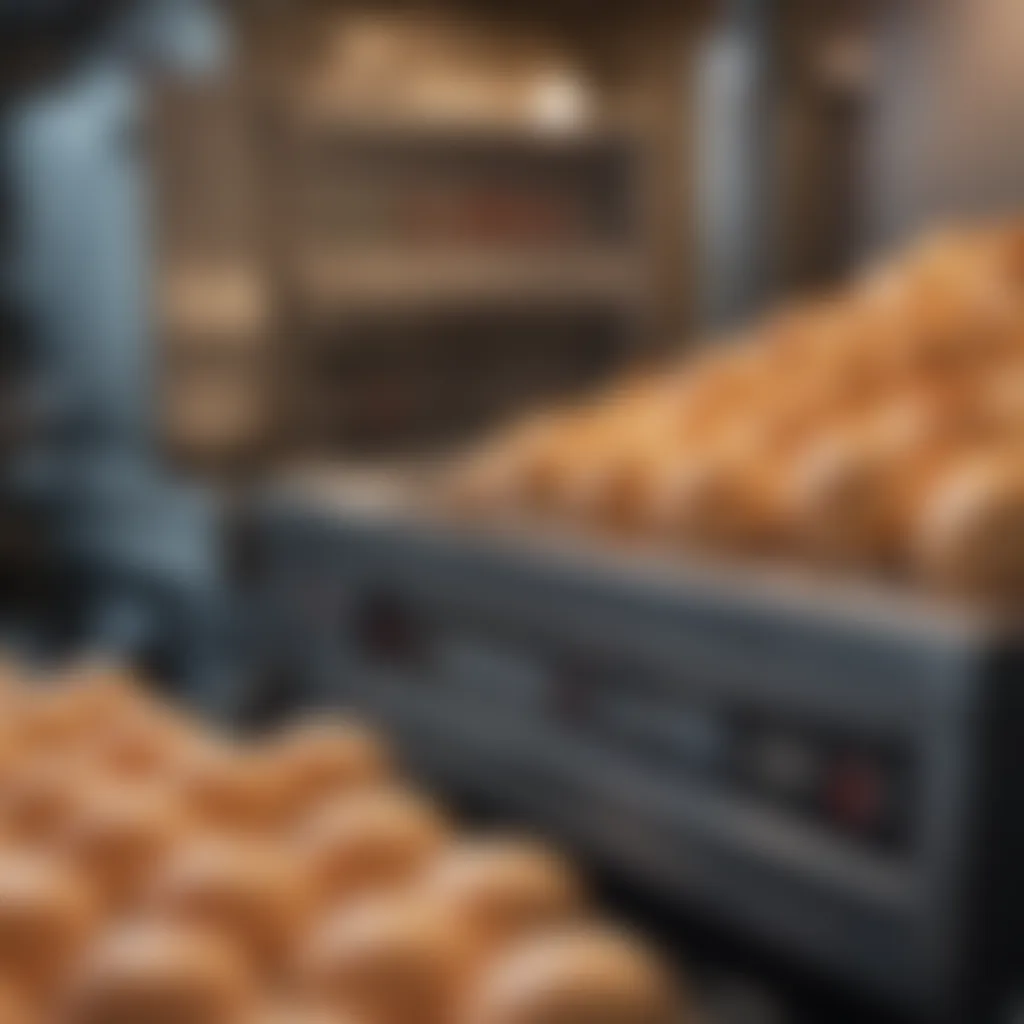
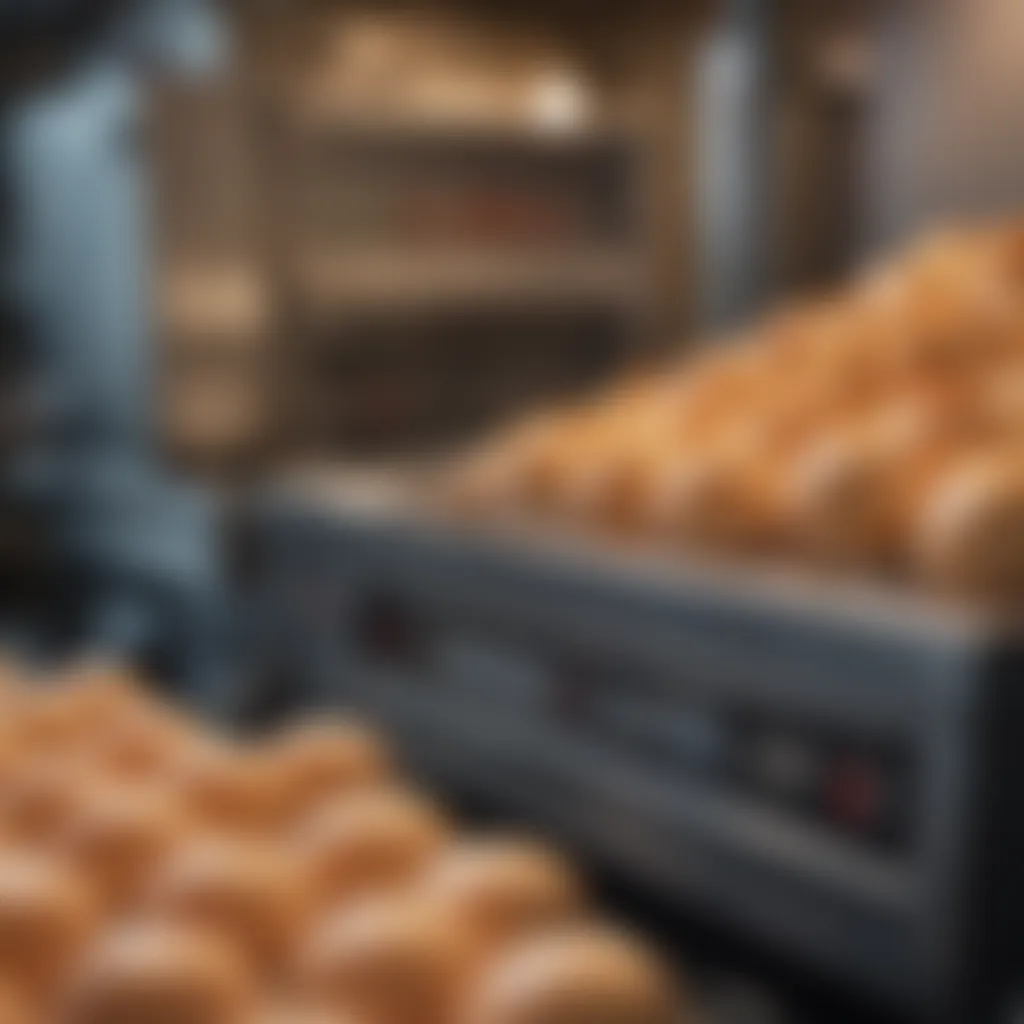
Applications Across Industries
The application of hard boiled machines spans many sectors, making them significant in today's industrial landscape. Each industry leverages these machines differently, emphasizing their adaptability and critical role in enhancing operational efficiency. Understanding these applications provides valuable insights into how hard boiled machines influence productivity, quality, and economic viability.
Manufacturing Sector
In the manufacturing sector, hard boiled machines are essential for streamlining production processes. They automate tasks previously performed by humans, which minimizes errors and increases output. Their accuracy aids in maintaining consistent quality standards, reducing waste of materials. Manufacturers often integrate these machines into assembly lines, allowing for increased speed and efficiency.
"Automation shapes the future of manufacturing. Understanding hard boiled machines is vital to staying competitive."
The machinesโ role in aiding Just-In-Time (JIT) production systems is notable. With reliable machines, manufacturers can maintain low inventory levels, optimizing storage costs and improving workflow.
Food Processing
The food processing industry benefits from hard boiled machines in various ways. They facilitate the cooking, packaging, and preservation of food products while adhering to safety and quality regulations. Machines designed for consistency are crucial in ensuring that food maintains its intended taste and nutritional value.
In this sector, speed is also essential. Hard boiled machines can drastically reduce production time. This capacity enables companies to meet rising consumer demand, particularly in a world increasingly focused on efficiency and reduction of food waste.
Pharmaceutical Industry
In the pharmaceutical field, the precision of hard boiled machines becomes a critical asset. These machines are employed in creating a variety of products, from medications to vaccines. They ensure that formulations are mixed precisely, adhering to stringent safety protocols.
Batch consistency is imperative in pharmaceuticals; therefore, the machines provide essential tracking and monitoring features. This allows manufacturers to ensure compliance with regulatory standards and fulfill quality requirements, making them indispensable.
Textile Production
Textile production utilizes hard boiled machines mainly for weaving, dyeing, and finishing fabrics. The speed at which these machines operate contributes to the mass production of textiles. As fashion trends change rapidly, the ability to produce materials quickly gives manufacturers a competitive edge.
Moreover, advanced machines can handle various fabric types, enhancing versatility. They also allow for the precise application of dyes and treatments, ensuring uniformity in product quality.
Efficiency and Performance Metrics
Efficiency and performance metrics are crucial in evaluating hard boiled machines within industrial settings. These measurements are not just numbers; they reflect the effectiveness of machinery in optimizing production processes. By focusing on specific elements such as operational efficiency standards and energy consumption, companies can make informed decisions that enhance productivity and sustainability.
High-efficiency standards contribute directly to productivity. When machines operate effectively, the output increases significantly while minimizing downtime. This leads to shorter production cycles and better resource allocation. Moreover, by carefully analyzing performance metrics, manufacturers can pinpoint weaknesses in the operational workflow. This insight enables them to adjust processes and equipment to achieve superior performance.
The benefits of monitoring efficiency and performance include:
- Cost Reduction: Improved efficiency lowers overhead costs associated with labor and energy consumption.
- Increased Output: Optimal performance can lead to higher production volumes.
- Enhanced Product Quality: Consistent performance improves the quality of the end product, as variations in machinery function can lead to defects.
In addition, focusing on these metrics supports a culture of continuous improvement. It encourages organizations to strive for excellence and embrace innovative practices.
"Efficiency does not merely increase productivity; it lays the foundation for sustainable practices in production."
Understanding efficiency and performance metrics is thus not just beneficial but vital for any organization aiming for success in the competitive landscape of modern industry.
Operational Efficiency Standards
Operational efficiency standards serve as benchmarks for assessing the effectiveness of hard boiled machines. These standards incorporate various factors, including throughput, cycle times, and equipment reliability. By setting clear targets, companies can evaluate their current operations against ideal performance levels.
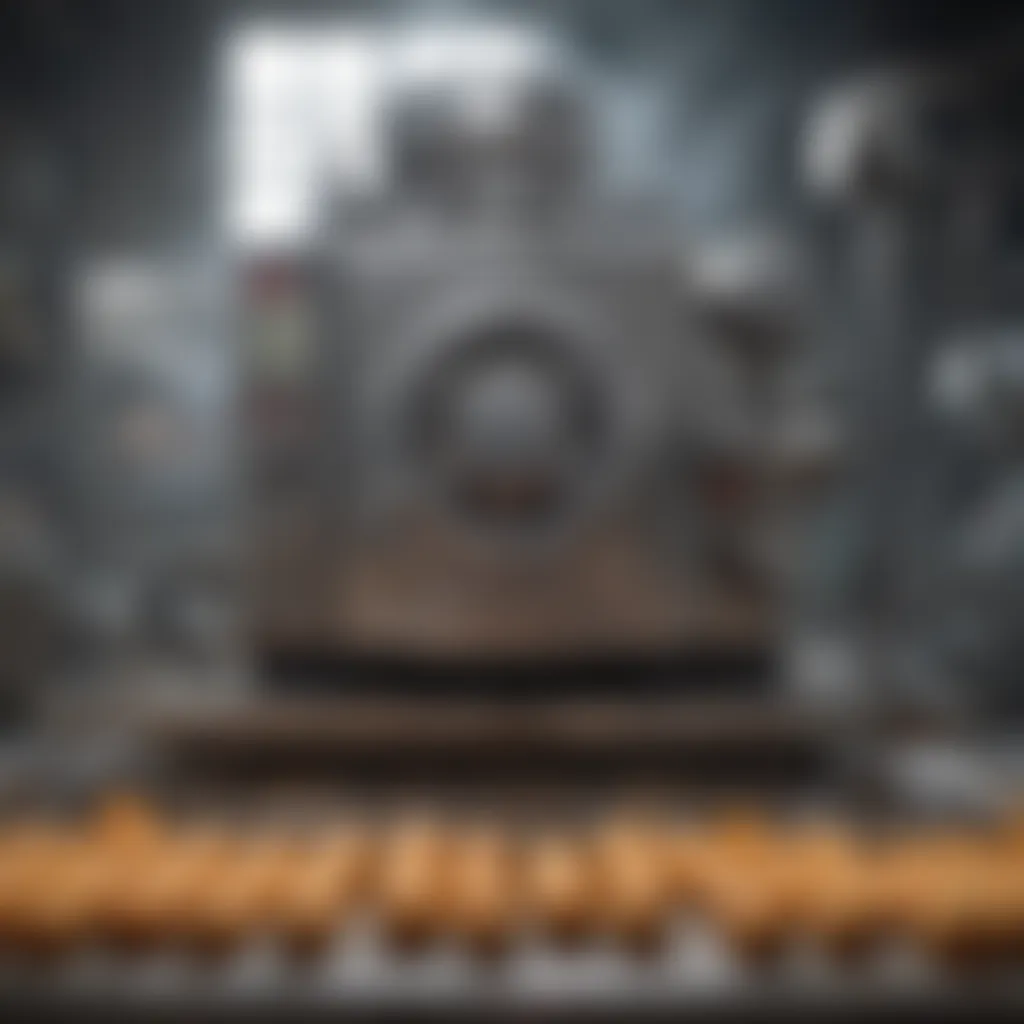
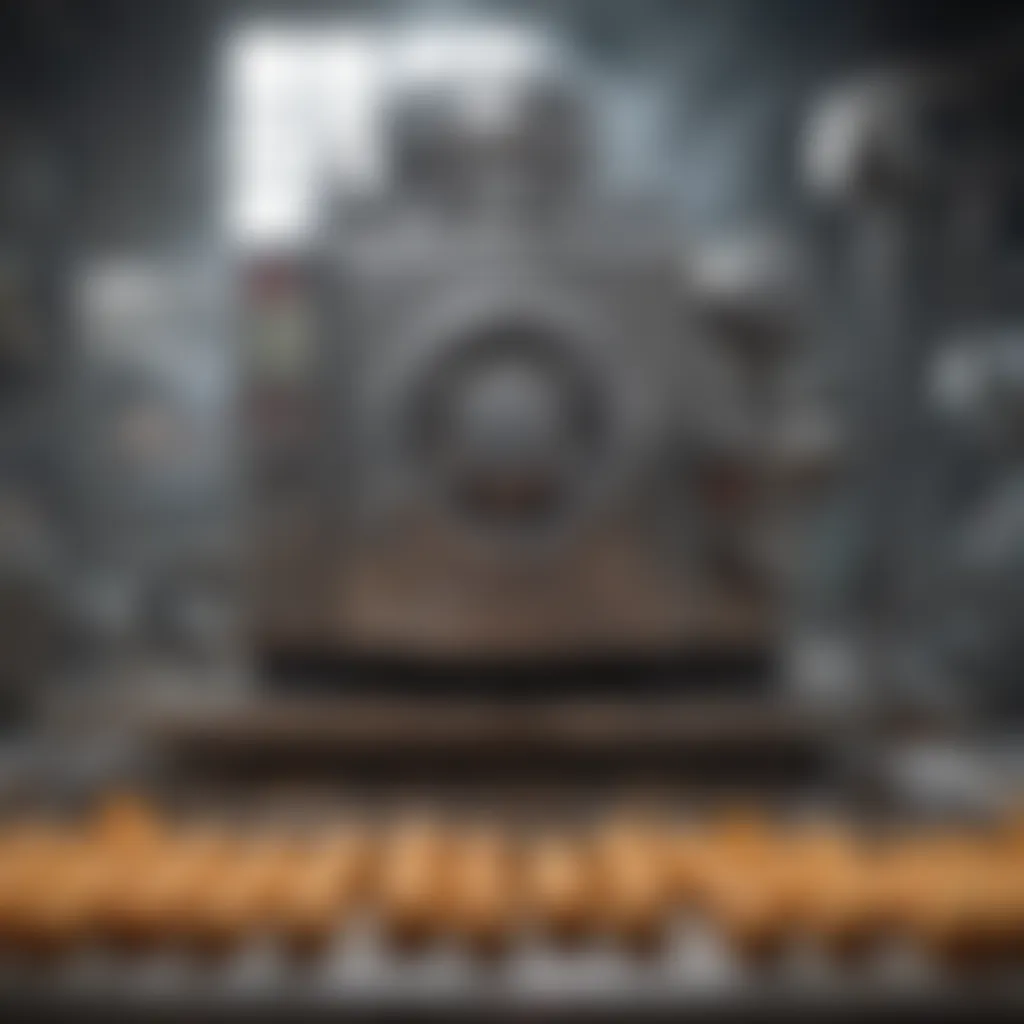
To establish these standards, several baseline metrics can be considered:
- Throughput Rate: This measures the quantity of output over a specific period.
- Downtime: Tracking both scheduled and unscheduled downtime helps identify areas needing attention.
- Quality Control: Examining the rates of defected products ensures that machines meet quality expectations.
Regularly reviewing these standards can help companies maximize efficiency. Adjustments based on real-time data can lead to more productive operations.
Energy Consumption Analysis
Energy consumption analysis is a vital component of efficiency metrics. As industries focus on sustainability, understanding energy use becomes increasingly important. The analysis not only highlights the energy required by each machine but also identifies opportunities for reductions.
Key elements in energy consumption analysis include:
- Energy Use Intensity (EUI): This metric assesses the amount of energy used relative to production output.
- Peak Energy Demand: Identifying times of high energy use helps in planning and can lead to cost savings.
- Renewable Energy Sources: Examining the potential for integrating solar panels or wind energy can further enhance sustainability efforts.
By analyzing energy consumption, firms can develop strategies to improve their environmental footprint. These strategies can range from optimizing equipment usage to investing in energy-efficient technologies. The impact not only aids in compliance with regulations but also resonates positively with consumers increasingly concerned about sustainability.
Challenges and Limitations
The discussion of challenges and limitations within hard boiled machines plays a crucial role in understanding their integration into modern industrial settings. Recognizing these obstacles helps industry professionals manage their ongoing expectations and maintain optimal functionality. This section emphasizes specific elements, benefits, and considerations concerning the various challenges these machines face throughout their operation.
Common Operational Issues
Operating hard boiled machines can involve various issues that disrupt productivity. Common operational issues might include irregular heating patterns, mechanical failures, or software malfunctions. These failures could lead to delays in production schedules or even complete halts in the manufacturing process.
Regular monitoring and diagnostics can address many of these issues. For example, temperature fluctuations might occur due to sensor malfunctions or inadequate calibration. Training staff to recognize these signs can mitigate risks and ensure a seamless operational flow. Additionally, frequent wear and tear on components can lead to unexpected breakdowns, making timely interventions vital.
Maintenance Challenges
Maintenance challenges present another aspect to consider. Unlike simpler machines, hard boiled machines involve intricate engineering that often requires specialized knowledge for effective upkeep. Routine maintenance not only ensures longevity but also enhances consistent performance. However, the complexity of these systems can necessitate trained technicians, leading to dependency on expert services.
Operational downtime for maintenance can be detrimental. It is essential for companies to establish a proactive maintenance schedule that includes regular check-ups and replacements of parts. As advancements in technology continue, incorporating predictive maintenance through IoT devices and software could vastly improve efficiency.
Cost Factors
Cost is a pervasive consideration in any industrial endeavor. Cost factors related to hard boiled machines include initial investment, ongoing maintenance expenses, and potential downtime costs. The upfront cost of acquiring advanced machines can be substantial, often requiring financial forecasting and careful budgeting. Moreover, higher-end models may promise improved performance but can also increase maintenance and repair costs.
Businesses must evaluate long-term financial implications, including potential savings from increased efficiency versus the initial expenditure. Understanding the breakeven point when investing in newer technology is vital for informed decision-making. Regular cost analysis can guide businesses in determining the most economical options for their operations.
Effective management of challenges and limitations can transform potential obstacles into opportunities for growth and development.
In summary, addressing the challenges faced by hard boiled machines requires diligence and a multifaceted approach. By understanding and actively managing these challenges, industries can not only enhance the longevity of their machines but also achieve sustained operational efficiency.
Future Trends in Hard Boiled Machines
The examination of future trends in hard boiled machines is essential as industries evolve rapidly. These machines are redefined by technological advancements and increasing demands for efficiency. By understanding the upcoming innovations, stakeholders can anticipate shifts in operational strategies and maintain competitive advantages. The integration of these trends directly affects production capabilities and sustainable practices.
Advancements in Technology
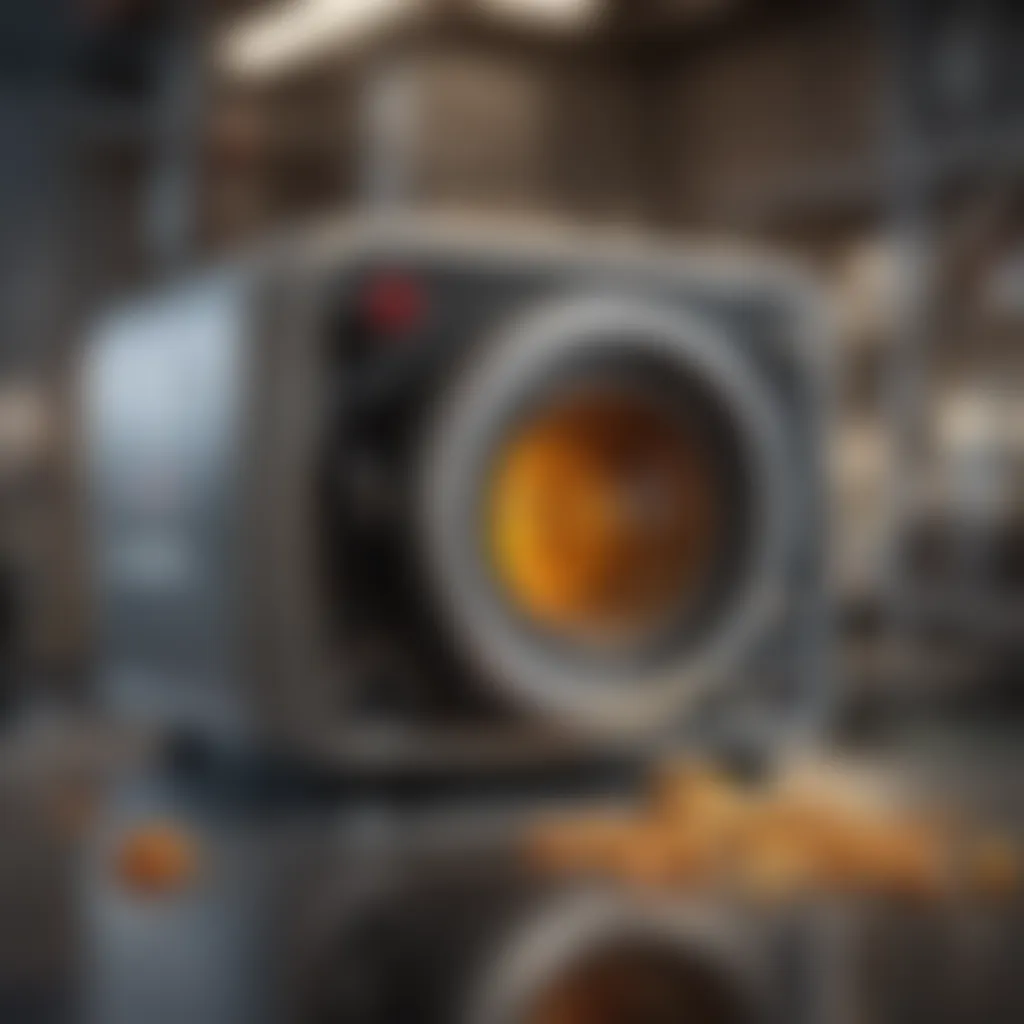
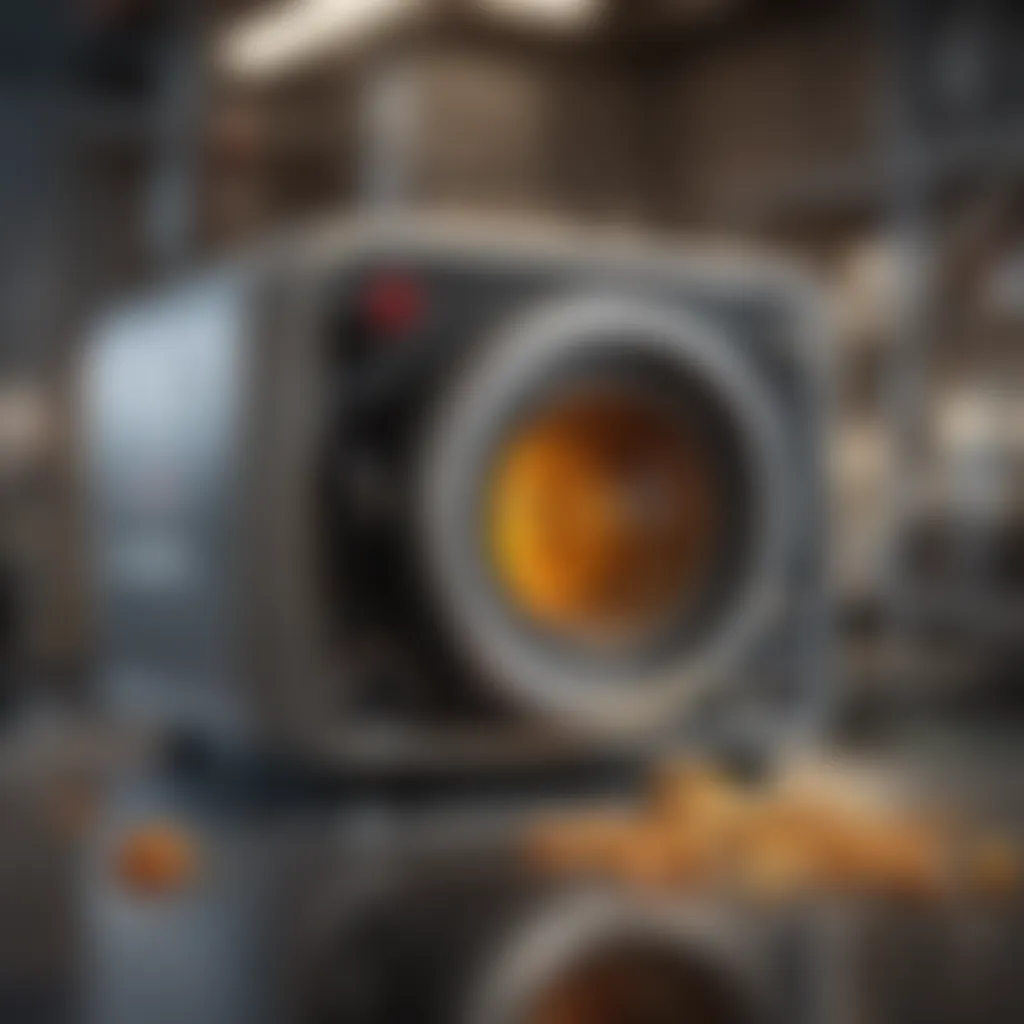
Technological advancements play a crucial role in enhancing the functionality of hard boiled machines. For example, the introduction of powerful software tools for monitoring processes helps in real-time data analysis. Such tools allow companies to track machine performance, ultimately leading to improved operations.
Innovative materials are also making a significant impact. The use of lighter and stronger materials leads to more lasting machines. This increases durability while reducing energy consumption. Emerging technologies, such as IoT (Internet of Things), enable machines to communicate and function in smarter ways. This connectivity can lead to predictive maintenance, reducing downtime and enhancing productivity.
Automation and Robotics
Automation continues to be a pivotal trend in the realm of hard boiled machines. The implementation of advanced robotics allows for precision and speed that manual labor cannot match. With robots handling repetitive tasks, human workers can focus on higher-level decision making. This shift strains the workforce dynamics; however, it leads to improved operational efficiency.
Moreover, developments like collaborative robots, or cobots, enable a safer working environment. They work alongside human operators, reducing risks of accidents while optimizing productivity. As industries look toward enhancing their productions, the investment in automation and robotics proves essential.
Sustainability Considerations
In today's industrial landscape, sustainability is not just a trend; it's a necessity. Hard boiled machines are increasingly designed with environmental impact in mind. Manufacturers are working towards creating energy-efficient machines to minimize ecological footprints. By employing recyclable materials and reducing waste, production can align with global sustainability goals.
Moreover, energy-saving features are becoming a standard in new machines. This might include smarter controls that adjust energy consumption based on workload. As companies engage in greener practices, they improve their brand image and comply with regulations.
Embracing sustainability helps industries not only to fulfill legal requirements but also to appeal to a growing clientele that values environmental considerations.
Case Studies
Case studies play a vital role in understanding the practical applications and real-world implications of hard boiled machines. Through the examination of specific instances, readers can grasp the nuances of how these machines integrate into various industries. This section will explore successful implementations and offer a comparative analysis of different models. The breadth of detail in case studies highlights key strategies and outcomes that contribute to informed decision-making.
Successful Implementation in Industry
Successful implementation of hard boiled machines in industry illustrates their potential to enhance production techniques. One notable example can be found in the food processing sector. A bakery in Germany adopted a hard boiled machine to optimize its dough mixing process. The result was a 30% increase in efficiency. By streamlining operations, the bakery reduced labor costs and improved product consistency. At the same time, the machine minimized waste by ensuring precise ingredient measurements.
In the pharmaceutical industry, another successful case is the application of these machines in the production of aseptic packaging. A major pharmaceutical company implemented hard boiled machines that significantly decreased contamination risks. By automating key sterilization processes, they not only met regulatory standards but also boosted their production capacity by around 25%. These examples demonstrate how strategic use of hard boiled machines can lead to visible improvements in efficiency and quality control across sectors.
Comparative Analysis of Different Models
Comparative analysis of different models of hard boiled machines elucidates their varying capabilities and applications. For instance, the difference between the electric and steam-powered models is significant. Electric models, such as those from the brand KitchenAid, tend to provide precise temperature control, making them ideal for delicate tasks like sous-vide cooking. On the other hand, steam-powered machines, such as those from the brand Cuisinart, offer rapid cooking abilities suitable for large-scale food production.
When evaluating performance metrics, factors like energy efficiency and time efficiency also come into play. For example, the Hamilton Beach model operates with lower energy consumption compared to a similar product from Breville. These differences highlight the importance of selecting the right machine based on specific needs, from domestic cooking to industrial applications.
The nuances revealed by comparative analysis empower consumers and manufacturers alike. Understanding the strengths and weaknesses of different models allows for more strategic investments and operational decisions.
"Informed choices in machine selection can significantly impact productivity and operational costs."
In summary, case studies offer tangible evidence of the effectiveness of hard boiled machines while comparative analysis fosters a deeper understanding of the options available. Those insights are particularly beneficial for industry decision-makers and home cooks alike.
The End and Insights
The discussion surrounding hard boiled machines reaches a crucial point in understanding their multifaceted impact on modern industry. This conclusion serves to synthesize insights from previous sections, highlighting how these machines serve as pivotal components in enhancing production efficiency, addressing challenges, and facilitating innovation. As industries evolve, hard boiled machines are becoming ever more significant, shaping both operational workflows and socio-economic conditions.
Summary of Findings
Several key findings emerge from this exploration:
- Operational Efficiency: Hard boiled machines streamline processes, thereby reducing waste and optimizing resource utilization. Their precision in manufacturing enhances overall productivity.
- Technological Advancements: Advancements in design and engineering have led to improved performance metrics. The integration of robotics and automation has transformed traditional approaches, pushing the boundaries of capability.
- Sustainability Efforts: The shift towards sustainable practices necessitates that machines are not only efficient but also environmentally sound. Materials and energy consumption are critical areas of focus, prompting industry leaders to innovate.
- Challenges and Limitations: Despite the benefits, operational issues persist, such as maintenance and initial investment costs. The importance of addressing these challenges cannot be overstated, as they can heavily influence the adoption and performance of these machines.
Final Thoughts on Hard Boiled Machines
Hard boiled machines embody a blend of innovation and necessity in the current industrial landscape. Their ability to adapt and improve is critical for businesses aiming to stay competitive. As industries proliferate, the relevance of these machines will likely increase, further emphasizing their role in both production and broader economic contexts. The continual adaptation of hard boiled machines will be essential to meet future demands.
"Innovation is not a goal; it is a journey that necessitates constant adaptation to changing needs and environments."