Transforming Industries with Automated Guided Vehicles

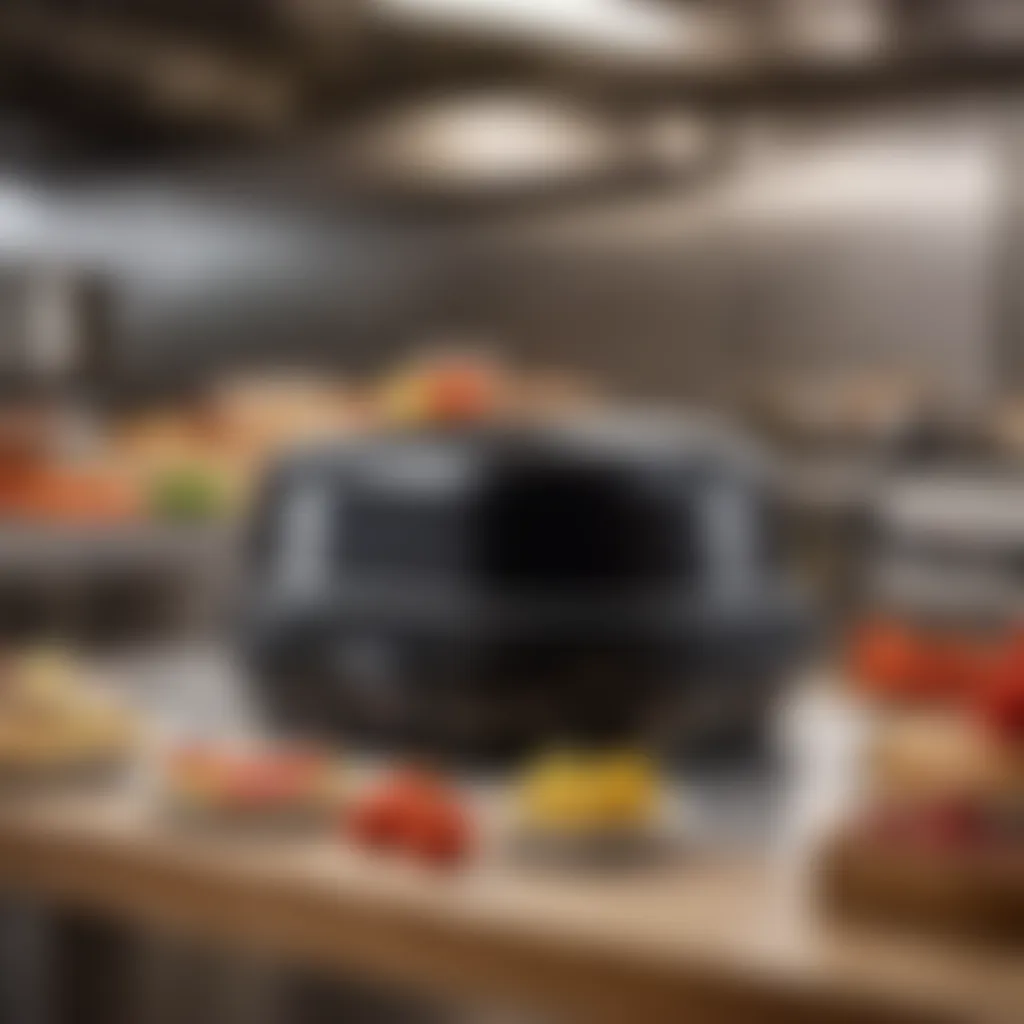
Intro
In recent years, the landscape of industry has undergone significant transformations. Central to this evolution lies the advancement and adoption of Automated Guided Vehicles (AGVs). These machines are not merely futuristic gadgets; they are robust solutions that enhance productivity and efficiency within industrial operations. As we delve into this comprehensive analysis, the focus will be on the pivotal role these vehicles play in the industrial framework, the improvements they bring to processes, and the hurdles organizations face while integrating this technology.
AGVs have become more prevalent in sectors ranging from manufacturing to logistics. With the rise of automation, companies are recognizing the necessity to keep pace with technological advances to maintain competitiveness. To truly understand the impact of AGVs, it’s essential to dissect their functionality and explore how they have reshaped traditional operational strategies.
Through this article, we will uncover how the evolution of AGVs unfolds step by step, from the initial technological breakthroughs to ongoing innovations that promise a bright future. But first, let's set the stage by defining what exactly AGVs are and how they operate in various settings.
Preface to Automated Guided Vehicles
Automated Guided Vehicles, often known simply as AGVs, are becoming increasingly pivotal in the way industries operate. Their main purpose is to move materials around a factory or warehouse without human intervention. This not only boosts productivity but also ensures safety throughout the operational processes.
Imagine a busy warehouse where materials are constantly being transported from one point to another. Traditionally, this process involves a lot of manual labor, leading to inefficiencies and potential for accidents. AGVs step in here, transforming these operations by using preset paths to navigate autonomously. These vehicles are equipped with various technologies that allow them to avoid obstacles, communicate with other machines, and even learn from their environments.
In this article, we will dive deeper into the specifics of AGVs, examining how they function, their evolution, and their impact on different industries. Understanding the nuts and bolts of AGVs is essential in grasping why they’re seen as the game-changer in modern industrial practices. Let’s journey into the world of AGVs and discover what they bring to the table.
Definition and Functionality of AGVs
At its core, an Automated Guided Vehicle is a mobile robot that follows markers or wires in the floor, or uses vision, magnets, or lasers for navigation. These vehicles can come in various shapes and sizes, tailored to transport different types of loads.
The primary functions of AGVs cover a wide array of tasks including:
- Material Transport: AGVs can seamlessly transfer products from one location to another, significantly reducing the time and labor required for such operations.
- Inventory Management: They can also contribute to efficient storage solutions by moving goods to and from storage locations.
- Order Fulfillment: Many businesses use AGVs in packaging and shipping areas, streamlining the order fulfillment process.
Due to their versatility, AGVs are suitable for countless applications within factories, warehouses, and even healthcare facilities. Their advantage lies in their ability to operate continuously, making them a reliable choice in a landscape where operational efficiency is key.
Historical Context and Evolution
The concept of AGVs is not entirely new; it has a history that stretches back several decades. Initially, in the 1950s, AGVs were rudimentary, relying solely on fixed paths and magnetic tapes. As technology progressed, so did the capabilities of these vehicles.
By now, AGVs have evolved dramatically. New developments in sensor technology, artificial intelligence, and computing power have led to smarter, more flexible AGVs. Changes that have occurred include:
- Introduction of Navigation Technologies: Earlier forms of AGVs depended on simplistic navigation. Today's AGVs utilize laser scanning or vision-based systems to navigate complex environments.
- Increased Flexibility: Modern AGVs can adapt to changes within the working environment, making them suitable for dynamic production lines.
The evolution of AGVs is a testament to the industrial sector's pursuit of efficiency and safety. Continuous improvements in these vehicles pave the way for their broader adoption across numerous industries, setting the stage for a future where they could become even more integral to everyday operations.
Types of Automated Guided Vehicles
Understanding the Types of Automated Guided Vehicles plays a crucial role in appreciating how these systems enhance efficiency in various industrial operations. When businesses look at automation, they often focus on the functionality and adaptability of the vehicles suited to their unique needs. Knowing the different types of AGVs allows companies to choose the right fit for their specific workflows, leading to improved productivity, lower operational costs, and enhanced safety measures.
Towed and Trolley AGVs
Towed and trolley AGVs are often used in environments where goods must move from one point to another with minimal human intervention. These vehicles typically consist of a towing unit linked to one or more carts, enabling them to transport materials efficiently. The simplicity of their design can be a real advantage as they require less maintenance compared to more complex systems.
For example, in a large manufacturing facility, a towed AGV can eliminate the need for a human operator to manually push heavy carts filled with parts. This not only alleviates physical strain on workers but also ensures that production lines keep moving smoothly without interruptions. The versatility of trolley AGVs also means they can adapt to different payloads easily, which is a significant consideration for businesses experiencing fluctuating demands.
Forklift AGVs
Forklift AGVs are specifically designed for lifting and transporting palletized materials. They are especially useful in warehouses and factories where inventory management is crucial. Unlike traditional forklifts that require skilled operators, these automated systems can navigate through narrow aisles and tight corners with precision.
Their significance shines during peak times when human resources are stretched thin. For instance, during high-demand seasons, businesses can employ these AGVs to keep operations running at full throttle without compromising safety. With advanced sensors and navigation systems, they can avoid obstacles and efficiently stack or retrieve items, saving valuable time and reducing the likelihood of accidents.
Unit Load AGVs
Unit load AGVs are versatile vehicles that accommodate a wide range of items, from small parts to large pallets. Their primary advantage lies in their ability to streamline operations that involve transporting bulk materials. These vehicles are particularly beneficial in places like distribution centers, where various products need to be moved between different sections frequently.
A great example would be a logistics company that employs unit load AGVs to optimize their sorting process. By automating the transfer of goods, they can significantly cut down on manual labor and errors associated with human handling. Their design allows for modular payloads, meaning that businesses can configure these AGVs to suit their specific load requirements.
Hybrid AGVs
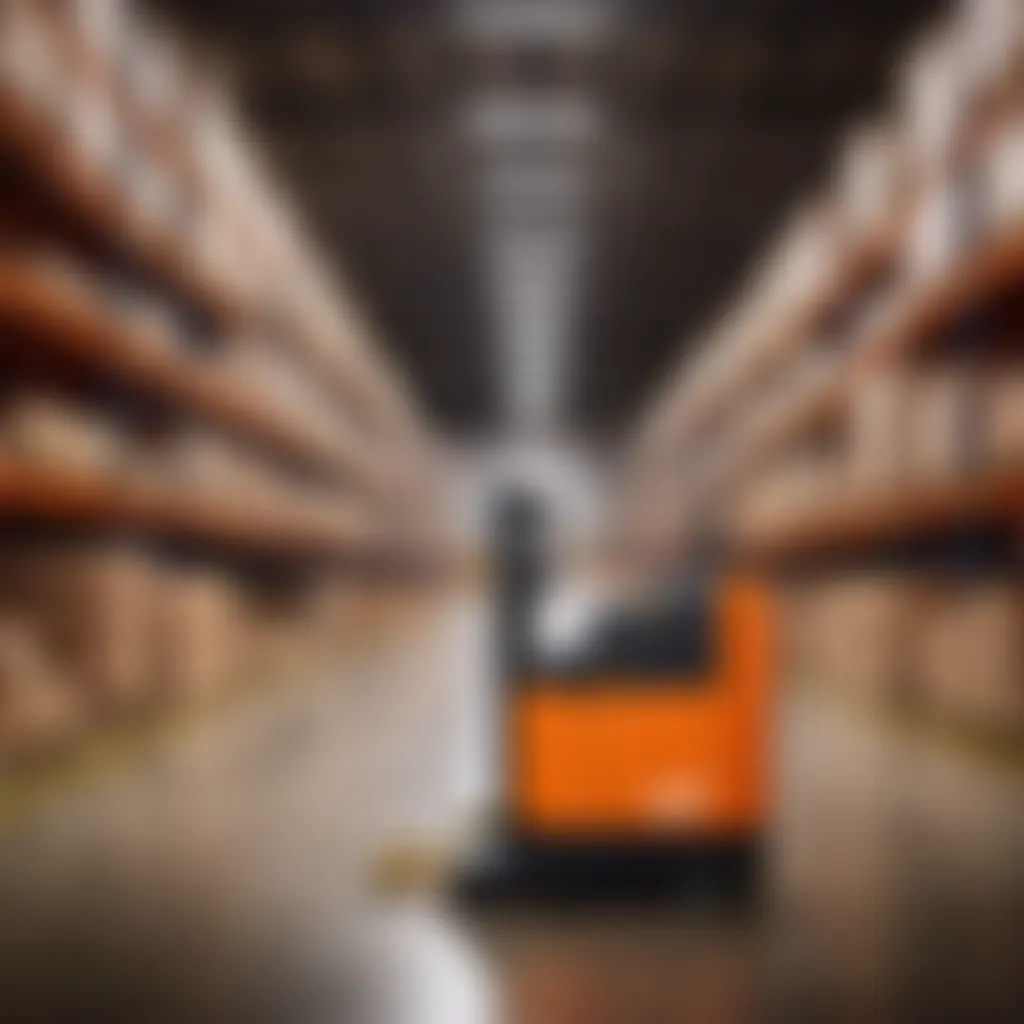
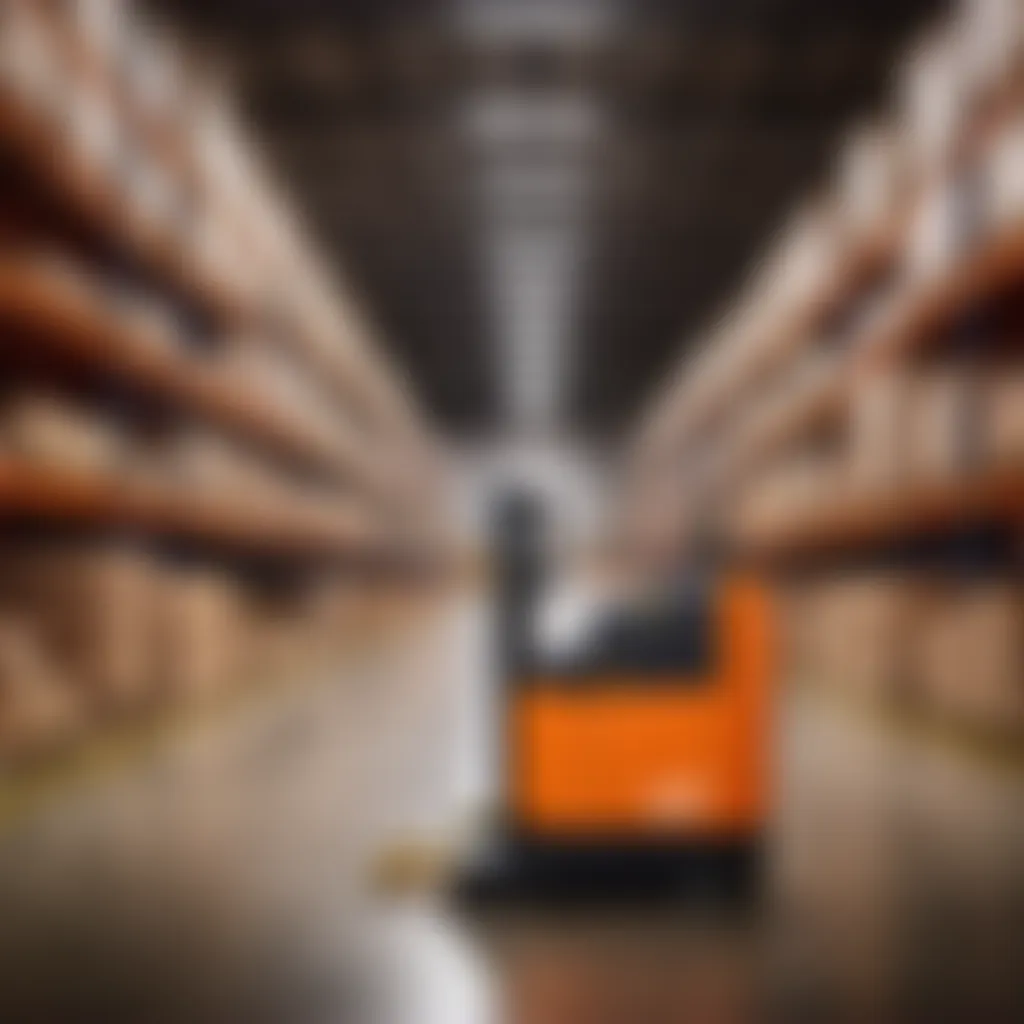
Hybrid AGVs represent a convergence of the various technologies available in the AGV landscape. They combine features from both traditional and robotic systems, resulting in increased versatility and adaptation to complex tasks. For instance, a hybrid AGV can operate both indoors and outdoors, making it suitable for companies with diverse operational environments.
One could visualize a manufacturing organization that requires units to manage both raw materials and finished products across multiple facilities. By utilizing hybrid AGVs, they can maximize efficiency, ensuring their operations are continuous and smooth. This not only leads to faster processing times but also provides flexibility in responding to changing demands.
In summary, selecting the appropriate type of AGV is not merely a technical choice; it reflects a strategic decision that can influence productivity and operational efficiency significantly. The deeper businesses understand the distinct characteristics and advantages of each AGV type, the better they can tailor their solutions to meet their unique industrial challenges.
Technological Advancements in AGVs
In the realm of industrial automation, technological advancements in Automated Guided Vehicles (AGVs) play a pivotal role, acting as the muscle behind seamless operations. These innovations not only boost productivity but also redefine the ways businesses operate. Their growing prominence stems from the push for operational efficiency and the need for acute precision in various sectors. This part of the article aims to shed light on some key navigation technologies and control systems that enhance AGV functionality, ultimately driving their integration across diverse industrial landscapes.
Navigation Technologies
Navigating through complex environments is crucial for AGVs. Several technologies come into play here, allowing for smarter movement within facilities. Below, we discuss three main navigation methods: vision-based systems, laser scanning, and magnetic tape.
Vision-based Systems
One prominent characteristic of vision-based systems is their reliance on visual inputs to guide AGVs. Equipped with cameras and intelligent software, these systems allow AGVs to perceive their surroundings much like humans do. This capability contributes significantly to autonomous navigation.
The unique feature that sets vision-based systems apart is their adaptability; they can recognize objects and dynamically adjust their paths. This flexibility makes them particularly beneficial in variable environments where obstacles frequently change, such as warehouse floors.
However, there are downside aspects to these systems. For example, they might struggle in poor lighting or with reflective surfaces, potentially leading to navigation errors. Yet, when utilized in the right environments, they can significantly enhance the efficiency of material handling operations.
Laser Scanning
Laser scanning employs lasers to create a detailed depth map of the surrounding area. The key characteristic of this technology is its high precision. By bouncing light off objects, these systems build a comprehensive 3D representation of the environment, which AGVs use to navigate safely.
This method's uniqueness lies in its ability to operate well in various lighting conditions, making it a reliable choice for all-day use. The primary benefits include improved obstacle detection and collision avoidance strategies, allowing for safer operations.
That said, laser scanning can also have its challenges. The initial cost of setting up such systems may be steep, especially for smaller enterprises aiming to integrate AGVs. Nevertheless, for those who can make the investment, the long-term safety and operational benefits are worth considering.
Magnetic Tape
The magnetic tape navigation method involves laying down a magnetic strip on the ground for the AGVs to follow. The main trait here is its simplicity—once the tape is installed, the AGVs can run efficiently along the designated path.
This approach's unique feature is its cost-effectiveness and low maintenance requirements. For factories and warehouses with set pathways, magnetic tape is a straightforward solution helping to control traffic flow within spaces.
However, the downside is that it limits flexibility; any changes in the layout require physical modifications to the tape. This rigidity can be a hindrance in dynamic environments where layout adjustments are frequently needed.
Control Systems and Software Integration
Control systems are the brains behind AGVs, allowing for seamless coordination and communication among the vehicles. Effective software integration is paramount, enabling real-time data processing, which helps AGVs respond to changing conditions efficiently. Integrating these systems often proves challenging. However, doing so can lead to significant enhancements in operational efficiency, ensuring AGVs seamlessly complement existing workflows.
Benefits of Implementing AGVs in Industrial Settings
The introduction of Automated Guided Vehicles (AGVs) into industrial environments has changed the game in various ways. These machines aren't just shiny gadgets lining the factory floor; they bring a host of advantages that are critical for enhancing operations. Companies today face increasingly competitive markets, which makes operational efficiency, safety, and cost-effectiveness lifesavers. Embracing AGVs helps snatch these benefits, making them an asset in the quest for sustainability and growth.
Increased Efficiency and Productivity
When it comes to boosting operational efficiency, AGVs score high. Picture a warehouse bustling with activity; orders are racing through the system as AGVs glide seamlessly along marked paths. These vehicles can work around the clock without the fatigue that humans face. This means faster order fulfillment, which invariably leads to greater productivity.
For instance, AGVs can transport materials from one point to another without human interaction. This cuts out transit delays that often pop up in manual processes. The vehicles can be custom programmed to follow optimal routes and schedules, ensuring they make the most of their time. Over time, this efficient movement directly contributes to a leaner manufacturing process.
Some nerdy statistics even back this up. Studies have shown that companies integrating AGVs see productivity improvements of anywhere between 20-40%. Imagine the potential for output increase; it's like adding extra overtime hours without the hassle of scheduling!
Improved Safety and Risk Reduction
Safety in industrial settings is paramount, and AGVs play a pivotal role here. These little workhorses can navigate complex environments without the risk of human error. They use advanced navigation technologies to prevent collisions and avoid obstacles, ensuring a smoother operation. In a world where workplace accidents can lead to hefty fines and serious injuries, implementing AGVs can dramatically lower those risks.
Moreover, AGVs help minimize human contact with hazardous materials. In scenarios where operators might encounter dangerous substances or heavy machinery, keeping human workers at a safer distance can only be a plus. With AGVs handling the heavy lifting, there are fewer chances for accidents to occur.
One striking example is in metal fabrication plants where heavy metal plates are moved around. The risk of injury is substantial when humans are involved in such tasks. The AGVs handle these plates effortlessly, shifting the risk away from the workforce.
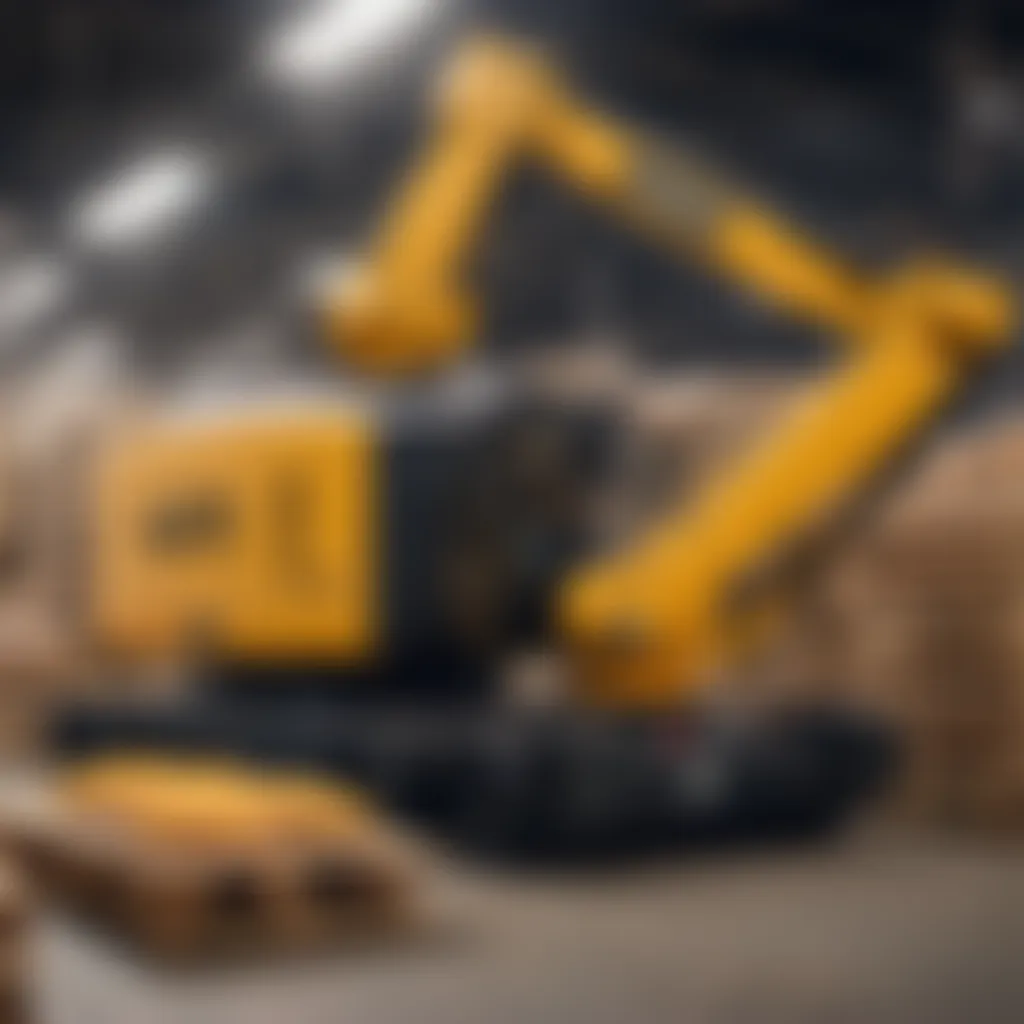
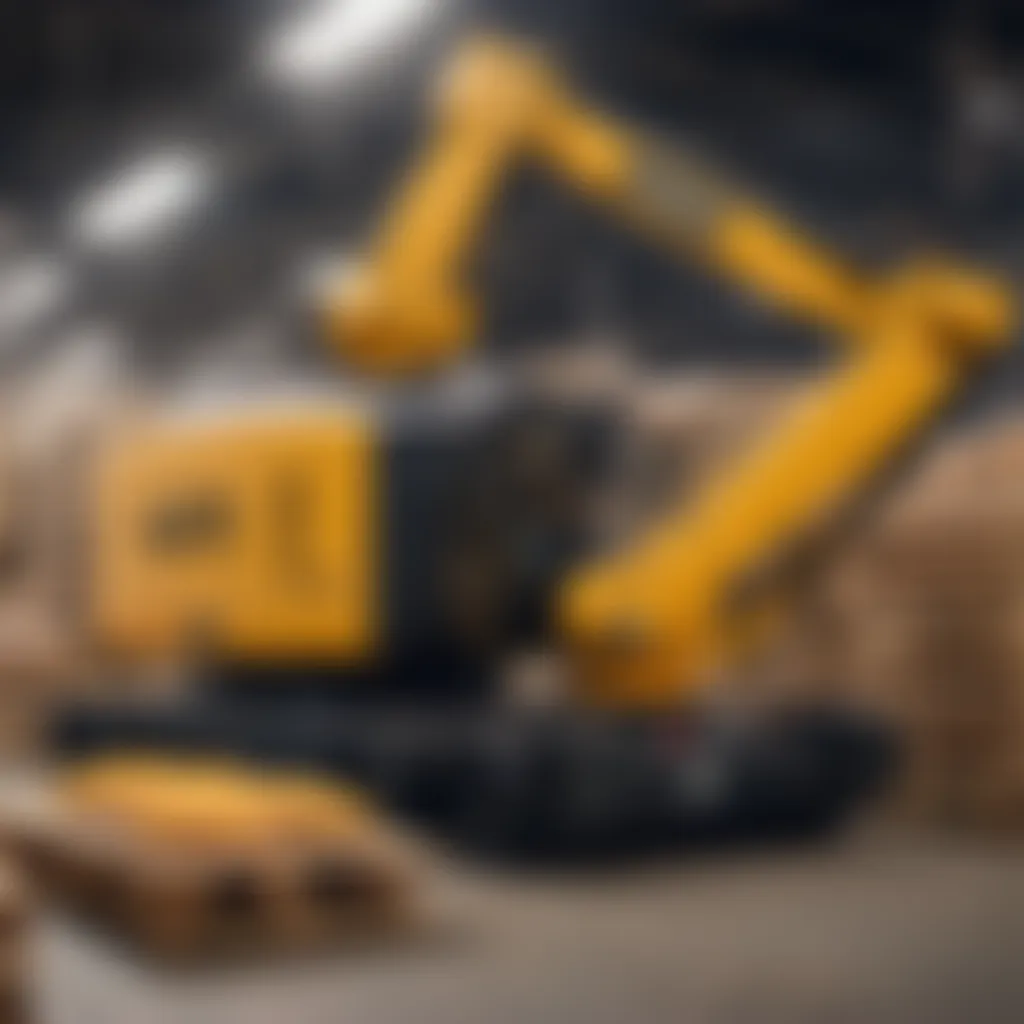
"Safety isn't just a priority; it's a fundamental right. Implementing AGVs significantly reduces the probability of accidents in the workplace."
Cost-Effectiveness and ROI
Now, let’s talk money – who wouldn't want to save a few bucks in today’s economy? While the initial investment in AGVs might give your wallet a bit of a pinch, the long-term savings can be substantial. Think about it this way: AGVs reduce labor costs since fewer manual workers are required to move goods. This doesn't mean totally cutting jobs but reallocating human resources to areas where they're needed most.
Furthermore, AGVs are generally low-maintenance and can help cut down on other operational costs. For example, delivery times shrink, which can enhance customer satisfaction and retention. With world-class reliability and upkeep that requires next to nothing, the savings on maintenance can stack up.
When organizations conduct a thorough return on investment analysis for AGVs, many find that they can achieve a break-even point in as little as a year. Not to mention, the reduced downtime and fewer accidents save companies from costly reassessments and delays.
In summary, adopting AGVs in industrial settings isn't merely a fleeting trend; it’s a strategic decision with enduring benefits. By improving efficiency, enhancing safety, and providing cost savings, AGVs hold the potential to boost overall operational effectiveness significantly.
Challenges in AGV Adoption
Adopting Automated Guided Vehicles (AGVs) isn't just plug and play. Many organizations encounter bumps along the road when integrating these systems. The challenges can seem like a tall mountain to climb, yet understanding these issues is crucial for ensuring a smooth transition.
Integration with Existing Systems
When companies begin to implement AGVs, one of the first hurdles they face is the integration with existing systems. Manufacturing processes, inventory management, and human resources often already have set protocols in place. Attempting to weave AGVs into an already intricate web of systems requires meticulous planning and sometimes significant adjustments.
Moreover, incompatibility might arise; older systems may not communicate well with new technologies, causing delays and confusion.
Ensure compatibility by conducting thorough assessments of existing systems and AGV capabilities. Figuring out the best way to marry old and new technology can be a daunting task, but with a strategic approach, organizations can create a cohesive workflow that leverages both AGVs and their existing setups effectively.
Initial Investment and Financial Constraints
While the long-term benefits of AGVs can be compelling, the up-front costs can leave many organizations pausing for thought. Initial investments can cover not only the purchase of the vehicles but also installation and necessary upgrades to infrastructure.
Some businesses might feel like they're standing at the edge of a precipice when considering these costs—it's a gamble that needs careful calculation.
"It's important to assess the return on investment (ROI) over the coming years. Understanding projected gains in efficiency and reductions in labor costs can help justify the initial outlay."
Organizations need to weigh the short-term financial impact against the potential for increased productivity, reduced labor costs, and enhanced safety. A detailed cost-benefit analysis could illuminate the path forward, offering clarity amid uncertainty.
Training and Skill Development Requirements
Another dimension of the AGV adoption challenge lies in the human element. Staff might need new skills to operate, troubleshoot, or maintain AGVs effectively. Training isn't just a one-time activity; it can be an ongoing process as technologies evolve.
When companies introduce new machinery or software, the learning curve can resemble climbing a steep hill. Proper training sessions foster a culture of confidence and competence in using AGVs, significantly reducing resistance to new processes.
Continuous professional development in AGV technology helps ensure a workforce that is skilled and agile. Business leaders must prioritize training to not only address current needs but also pave the way for future technological advancements.
Case Studies of AGV Implementation
The exploration of case studies in AGV implementation serves as a fundamental piece of understanding the real-world efficacy of Automated Guided Vehicles in various industries. Observing actual applications sketches a vivid picture of how AGVs function, the challenges faced during integration, and the significant benefits achieved in productivity, cost savings, and operational safety. Each case showcases unique considerations that companies have to account for when contemplating AGV adoptation, ultimately offering valuable insights that inform potential future implementations.
Manufacturing Sector
In the manufacturing sector, the use of AGVs shines brightly, especially in environments where material handling is a daily necessity. A notable example can be found at Ford’s manufacturing plants, where AGVs transport components between assembly lines. The initiative not only eliminated bottlenecks but also significantly reduced labor hours dedicated to material handling.
Key points to consider:
- Efficiency Gains: With AGVs, Ford reported a 30% improvement in throughput. This showcases not just speed but reliability in logistics management.
- Flexibility: The AGVs can be reprogrammed to adapt to different products introduced on assembly lines, showcasing remarkable adaptability to changing demands.
"In the world of manufacturing, time is money. Implementing AGVs streamlines processes, helping businesses meet production targets more efficiently than ever."
This case outlines how AGVs offer the scalability that many producers need to accommodate shifting product lines while maintaining high output.
Warehousing and Logistics
The warehousing domain provides a shining example of AGVs optimizing processes. Take, for instance, the implementation at Amazon fulfillment centers. Here, AGVs assist in moving goods from storage to packing stations, which drastically quickens order fulfillment.
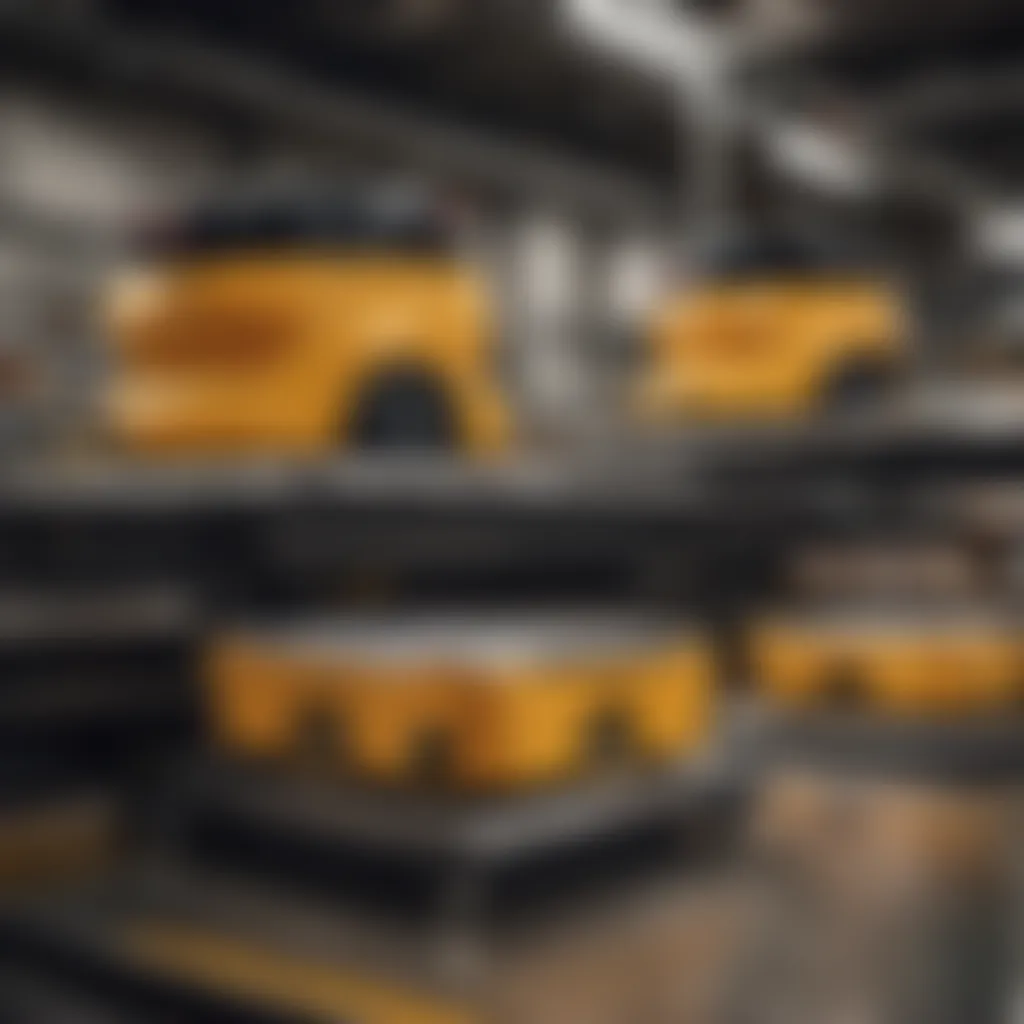
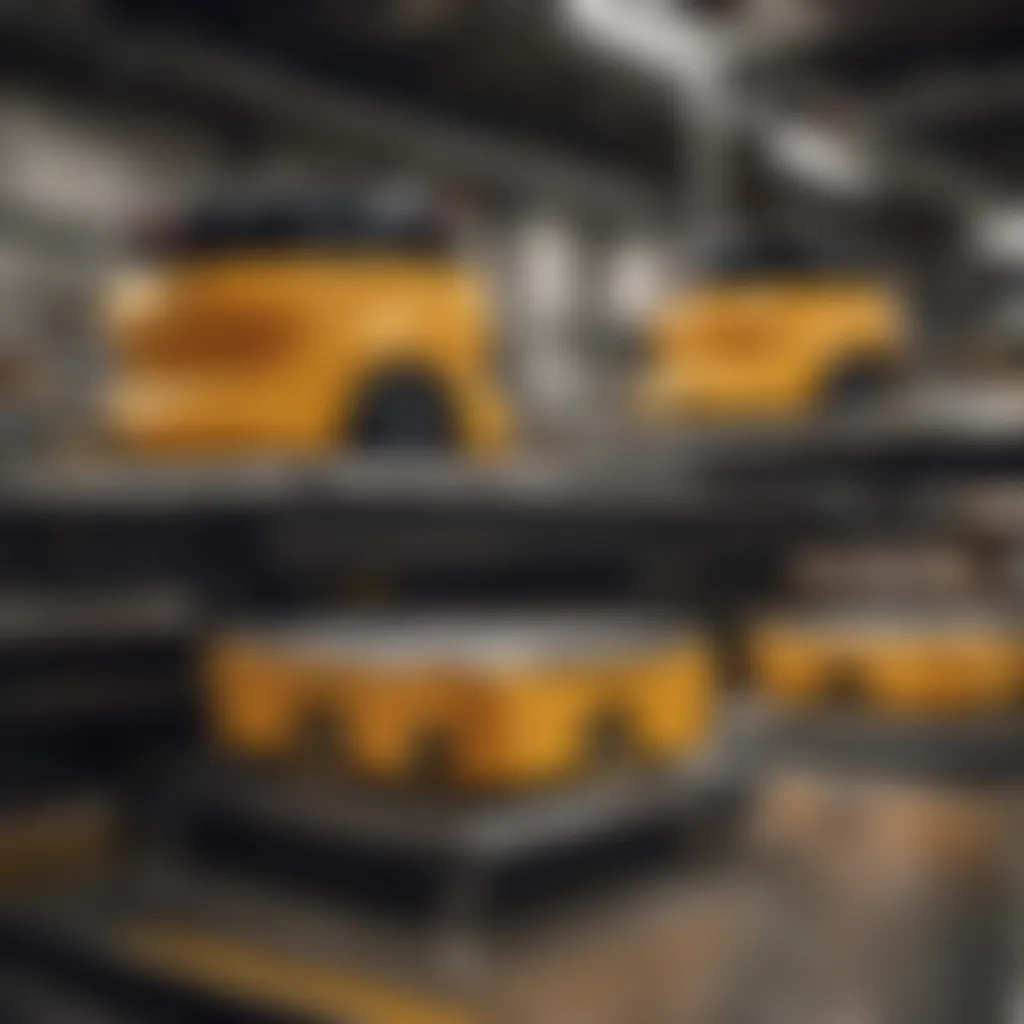
Benefits of AGVs in this sector include:
- Reduced Labor Costs: AGVs alleviate the need for a large workforce dedicated solely to moving items. This, in turn, trims labor expenses significantly.
- Increased Storage Efficiency: With AGVs operating efficiently, warehouses can design layouts that maximize space, permitting denser storage than traditional methods allow.
The agility of AGVs permits swift navigation through crowded aisles, distinguishing them from static systems. Therefore, agility combined with precision becomes a game changer in logistics operations, enabling firms to respond to market demands promptly.
Healthcare Applications
In healthcare, the implications of AGVs are profound, impacting how facilities manage time-sensitive tasks. Hospitals, for instance, have introduced AGVs to deliver medications and laboratory specimens, minimizing the risk of human error and delays. One such implementation was observed at the Cleveland Clinic.
Noteworthy elements include:
- Enhanced Safety: AGVs reduce the need for staff to navigate busy corridors carrying potentially hazardous materials, thus enhancing safety for both healthcare personnel and patients.
- Streamlined Operations: By automating transport, healthcare workers can focus on patient care rather than logistical challenges, thereby improving service quality.
Through these examples, it's clear that AGVs have a substantial role in ensuring operational efficiency and safety in high-stakes environments like healthcare. This not only frees up resources but also leads to better patient outcomes, highlighting yet another layer of AGV value in industrial applications.
Finale
Each of these case studies illustrates the transformative power of AGVs across different sectors. As businesses look to improve operational efficiency and safety, the specifics drawn from these examples offer invaluable guidance and inspiration. AGVs not only enhance productivity but also redefine workflows, making them indispensable in today’s fast-paced industrial landscape.
Future Trends in AGV Technology
As industries continue to evolve, the role of Automated Guided Vehicles (AGVs) is set to expand exponentially. Future trends in AGV technology are essential, not just for manufacturers, but for anyone looking at the broader picture of automation affecting industrial processes. Looking ahead, the advancement of AGVs is not merely about robots moving materials; it is about creating a cohesive ecosystem that integrates humans, machines, and software to maximize productivity and efficiency.
Advancements in Artificial Intelligence and Machine Learning
The integration of artificial intelligence (AI) and machine learning (ML) into AGV technology is like adding a brain to an otherwise mechanical body. These advancements permit AGVs to learn from their environments, adapt their behaviors, and optimize routes dynamically. Imagine a warehouse where AGVs can analyze traffic patterns and adjust their operations accordingly, significantly reducing delays and enhancing throughput.
Moreover, AI and ML facilitate predictive maintenance. With the ability to predict when an AGV is likely to run into issues, companies can avoid long downtimes, saving both time and money. It's much like how a savvy cook checks their ingredients ahead of time to ensure a smooth meal preparation.
"The future of AGVs is not in just automation, but in intelligent automation."
Increased Autonomy and Decision-Making Capabilities
Future AGVs are poised to become more autonomous, which means they'll require even less human intervention. This increased autonomy stems from enhanced sensing technologies and smarter algorithms, allowing AGVs to make real-time decisions based on their immediate surroundings.
Consider a bustling factory floor: AGVs equipped with advanced sensors can detect obstacles, calculate safe paths, and even make decisions about when to speed up or slow down, all without waiting for human commands. This level of decision-making can lead to reduced operational costs and improved safety.
Additionally, with such advancements, AGVs can serve not only to transport loads but also to gather data from the environment they operate in. This data can be turned into actionable insights for better process optimization, making businesses sharper and more competitive in the market.
Collaborative Robots and AGVs
The future also promises a collaborative environment where AGVs work alongside humans, referred to as cobots. Unlike traditional robots that operate in isolation, cobots are designed to work hand-in-hand with humans, sharing tasks in ways that enhance efficiency and safety.
For instance, imagine a scenario in a distribution center where a human employee picks items off the shelf, while an AGV follows closely behind, ready to transport those items. This type of teamwork minimizes time lost between tasks and allows workers to focus on higher-level activities that require critical thinking.
The integration of AGVs with cobots represents a huge leap towards a more efficient workspace. As collaborative robots become more commonplace, we can expect to see a blending of human touch with robotic precision, resulting in smoother operations and higher employee satisfaction.
Finale
In wrapping up a discussion on Automated Guided Vehicles (AGVs) and their role in modern industry, it's essential to synthesize the key points that paint a vivid picture of their significance. AGVs are not just a passing trend but instead represent a leap into the future of manufacturing, warehousing, and logistics. They can be likened to the trusty bicycle that once transformed simple travel; these vehicles have a profound impact on how goods move and how tasks get done.
Recapitulation of Key Insights
To better understand the nuances surrounding AGVs, let’s revisit the critical insights garnered from our analysis:
- Efficiency and Productivity: AGVs drastically enhance operational efficiency. By automating transportation tasks within facilities, they allow employees to focus on value-added activities, ultimately leading to higher productivity levels. This is reminiscent of how dishwashers freed up time for people, allowing them to enjoy their meals without the constant worry about cleaning.
- Cost-Effectiveness: While there may be initial costs associated with adopting AGVs, the long-term savings can be significant. Reduction in labor costs, minimized accidents, and lower error rates contribute to an impressive return on investment over time.
- Safety: One cannot underestimate the importance of improved safety protocols. AGVs reduce human interaction in high-risk areas, which contributes to fewer accidents and a healthier workforce.
- Challenges of Integration: Despite these benefits, one must acknowledge the hurdles companies face when incorporating AGVs into their existing frameworks. The complexity of intertwining new technology with established processes requires careful planning.
- Future Trends: As we look ahead, the integration of AI and machine learning could further revolutionize AGVs, creating smarter systems that can collaborate more seamlessly with human workers.
"The transformation brought by AGVs is not just about technology; it is a shift towards smarter and safer industrial operations."
Final Thoughts on AGVs in Industry
Thinking about AGVs, it’s clear they represent a significant turning point in industrial operations. For industries now considering this technology, it might feel overwhelming, just like diving into a new recipe that involves unfamiliar ingredients. However, with thoughtful consideration and strategy, the outcome can be equally rewarding.
These vehicles are more than mere machines; they are pivotal in ushering in a new era of efficiency, safety, and operational ease. As workplaces adapt to these innovations, keeping an eye on future developments will be vital. The path forward is not just about navigating challenges but also embracing opportunities.
For businesses, investing in AGVs is an investment in the future—one where industries can thrive in a competitive landscape. As with any transformative process, it’s crucial to learn, adapt, and evolve, ensuring that every step taken leads to fruitful results well worth the effort.