Understanding D3 Stainless Steel: Properties and Uses
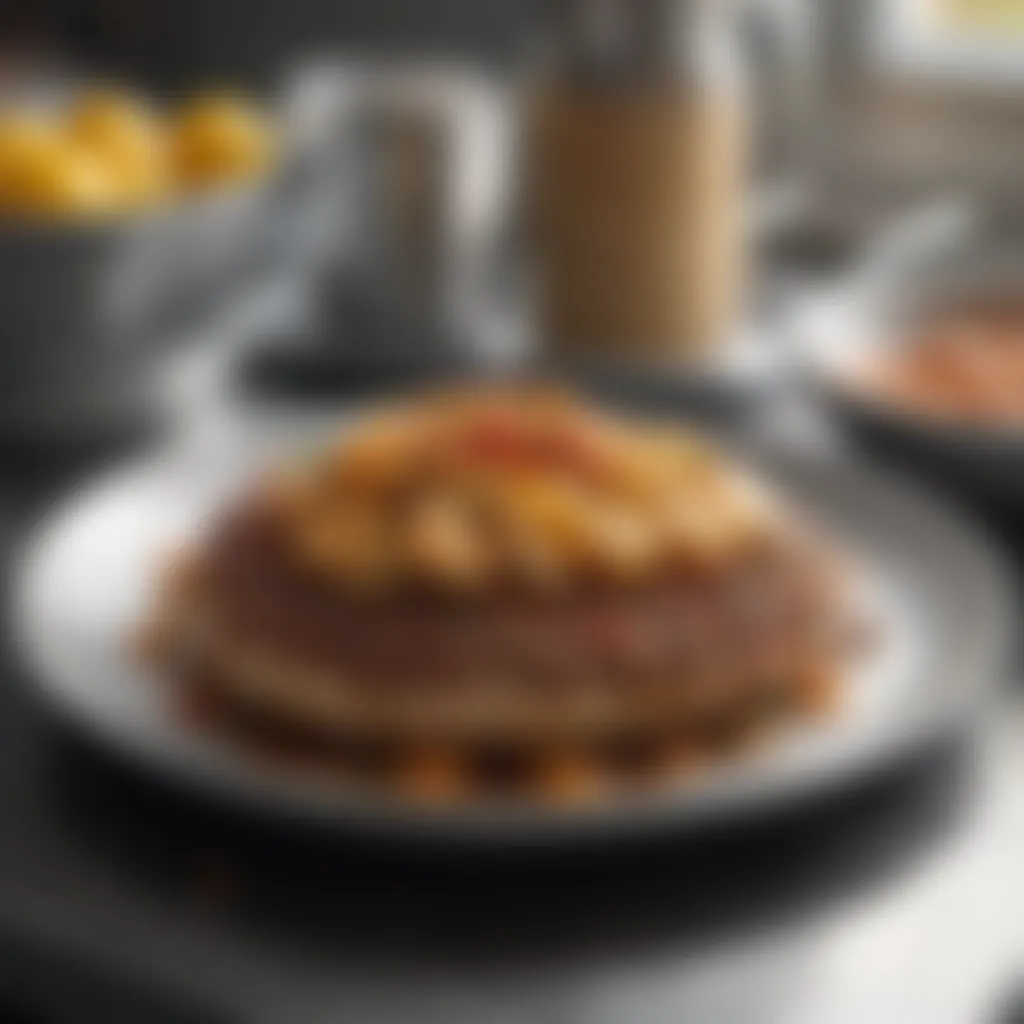
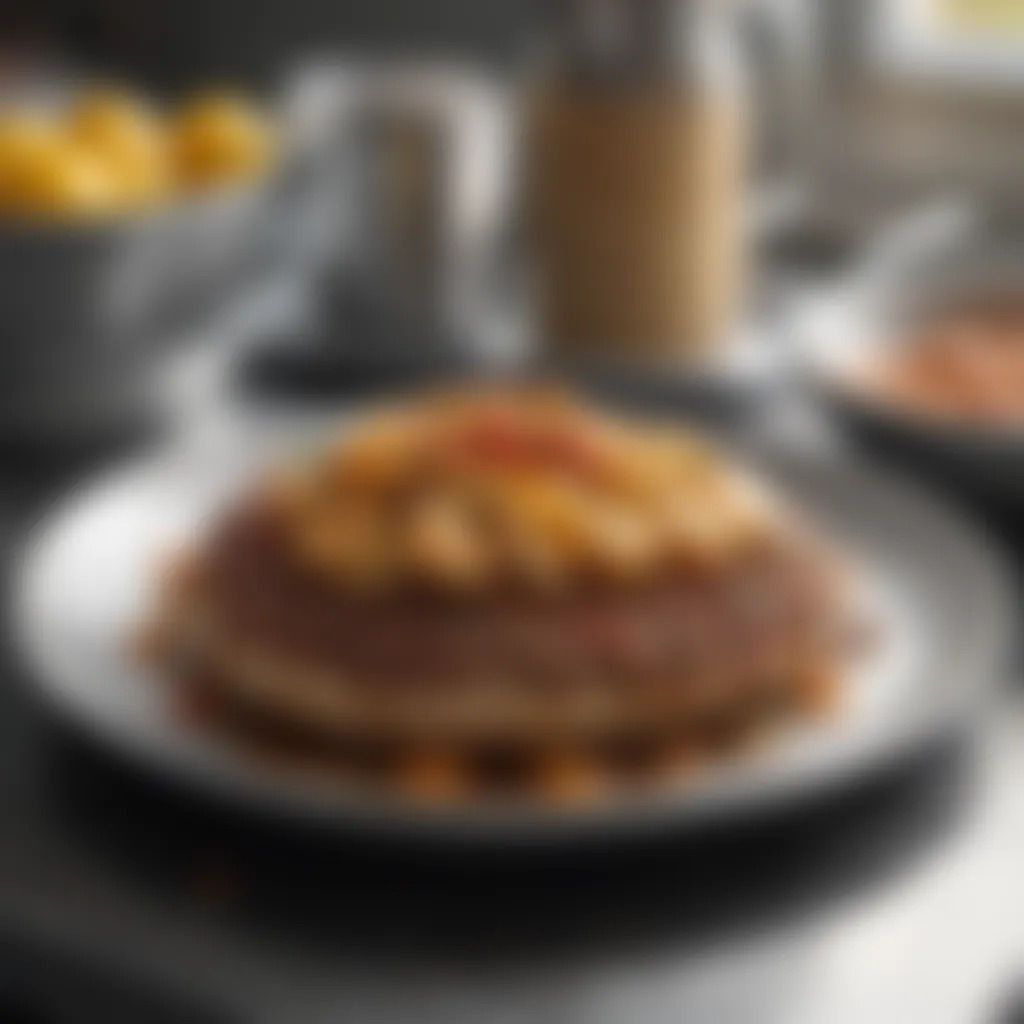
Intro
When talking about materials in the world of metallurgy, not all metals are created equal. Among the assortment of options, D3 stainless steel stands out for its distinctive blend of resilience and versatility. This type of steel, known for its unique attributes, finds its place in a variety of industrial applications, from manufacturing to construction. Understanding what makes D3 stainless steel tick can help professionals make informed decisions that affect both safety and performance in engineering projects.
D3 stainless steel, part of the high-carbon steel family, is often noted for its balance of hardness and ductility. But what does that really mean for its application? To navigate the spectrum of properties and uses, let's first take a closer look at the composition that gives D3 its characteristic traits.
Intro to D3 Stainless Steel
D3 stainless steel has increasingly become a material of choice in various industrial applications due to its distinct properties. Understanding this alloy can illuminate its benefits, uses, and importance in contemporary metallurgy. For anyone even slightly involved in manufacturing or engineering, grasping the essence of D3 stainless steel is paramount.
Definition and Classification
D3 stainless steel falls under the category of high-carbon, cold work tool steels. It’s a medium carbon steel enriched with chromium, which lends it excellent hardenability. This set of properties makes D3 particularly suited for manufacturing tools and dies. In practical terms, it’s like having a knight in shining armor for jobs requiring durability!
This steel is often classified as a high-hardness material, boasting hardness levels that can reach up to 60 HRC after appropriate heat treatment. Such characteristics enable its use in the sophisticated machinery needed in industries ranging from manufacturing to construction. It’s these qualities of high tensile strength and wear resistance that define D3’s classification, setting it apart from its peers in the stainless steel family.
Historical Background
The emergence of D3 stainless steel is deeply rooted in advancements in metallurgical science. Initially popularized in the mid-20th century, this alloy became a game-changer in tooling. The demand for materials that could withstand extreme wear and demands led to the need for superior alloys. D3 came along as a response to that need, marrying durability with versatility.
From the onset, the historical significance cannot be overstated. As industries evolved, so did the requirements for better materials, thus propelling D3 stainless steel into mainstream use. Many can credit the development of D3 to the introspection of metallurgists who aimed to push the boundaries of what steel can achieve.
“D3 has become synonymous with reliability in tool-making, illustrating how innovation and necessity often drive advancements in metal production.”
D3 stainless steel, with its intricate composition and remarkable characteristics, represents more than just a metal; it's the product of decades of refinement and research, leading us to explore its myriad applications alongside its standout properties.
Chemical Composition of D3 Stainless Steel
The importance of chemical composition in D3 stainless steel cannot be understated. It lays the groundwork for the steel's distinctive properties and performance in various applications. Understanding the chemical makeup allows users to anticipate the behavior of D3 steel under different conditions, such as heat, pressure, and exposure to corrosive environments. Moreover, specific alloying elements enhance the material's overall durability and functionality, making it a favored choice in industries requiring robust steel solutions.
Alloying Elements
D3 stainless steel is primarily composed of iron, with a significant amount of carbon, making it a high-carbon tool steel. The specific percentages can vary, but typically, the carbon content ranges around 1.4% to 2.0%. This high carbon content plays a crucial role in the steel's hardness. The other key elements in D3 stainless steel include:
- Chromium: Usually around 11% to 13%, chromium contributes to the steel's corrosion resistance and hardness.
- Molybdenum: At about 0.5% to 1.0%, it enhances strength and improves resistance to pitting.
- Vanadium: This element, found in smaller quantities, boosts toughness and wear resistance.
The interplay of these elements leads to a unique balance; for instance, the chromium and carbon levels help form a protective oxide layer, which is vital for corrosion resistance. This particular composition allows D3 stainless steel to excel in demanding environments while maintaining its structural integrity.
Impact of Composition on Properties
The chemical composition of D3 stainless steel directly affects its mechanical properties, shaping how it performs in real-world applications.
- Hardness: The high carbon content is the star of the show here, endowing D3 with exceptional hardness. This makes it suitable for tools that experience significant wear, such as cutting tools and dies.
- Ductility and Toughness: While high hardness is beneficial, D3 stainless steel is also designed to maintain a level of ductility. Though it is not as ductile as lower carbon steels, its balance allows it to withstand some deformation without fracturing. This aspect is critical in applications where shock resistance is required.
- Wear Resistance: The alloying elements, especially chromium and molybdenum, contribute to enhanced wear resistance. Tools and components made from D3 can endure the rigors of continual use, making them more cost-effective in the long run due to less frequent replacements.
D3 stainless steel’s ability to hold an edge after many uses is a testament to its chemistry. This steel, while hard, manages to stay resilient in various applications—from manufacturing machinery parts to creating intricate molds.
The right chemical makeup can transform ordinary materials into extraordinary ones.
In summation, the composition dictates the functionality of D3 stainless steel, making it an essential consideration for those seeking reliable and high-performing materials. Understanding these intricacies not only informs better choices but also enables improved engineering solutions tailored to specific industrial challenges.
Mechanical Properties of D3 Stainless Steel
The mechanical properties of D3 stainless steel play a significant role in determining its suitability for various applications. Understanding these properties is vital as they directly influence performance, longevity, and the conditions under which this material can be effectively used. D3 stainless steel is known for its unique balance of hardness and toughness, making it an ideal choice for parts that require strength and wear resistance. It stands out in a crowded field of materials due to its robust performance across a variety of environments, especially where high durability is required. Successful applications rely heavily on these mechanical characteristics, underscoring the importance of selecting the right materials based on their properties.
Tensile Strength
Tensile strength refers to the maximum amount of tensile (stretching) stress that a material can withstand before failure. D3 stainless steel exhibits impressive tensile strength, typically exceeding 1,000 MPa. This quality makes it effective for heavy-duty applications, such as manufacturing cutting tools and dies.
The high tensile strength is largely due to its composition, which includes elements like carbon and chromium that enhance its resistance to deformation. For instance, its ability to maintain structural integrity under stress makes it a favorite in industries ranging from automotive to aerospace.
When looking at tensile strength, one must also consider factors like temperature and environmental conditions. For example, while D3 steel performs admirably at room temperature, its strength can fluctuate at elevated temperatures. Therefore, understanding the specific application environment is key to determining if D3 stainless steel is the right choice.
Hardness and Wear Resistance
Hardness is another crucial property of D3 stainless steel. The material is typically rated between 58 and 66 HRC (Rockwell Hardness Scale), indicating a high level of resistance to indentation and deformation. This hardness is particularly useful in applications where parts are subject to high wear, such as in machinery and tooling.
Furthermore, D3's wear resistance can be attributed to its fine microstructure, which helps it resist the abrasion and erosion encountered in demanding work environments. Keep this in mind when choosing materials for projects that involve frequent friction or impact—D3 stainless steel not only holds its own but often outperforms alternatives.
One important consideration, however, is that while higher hardness can improve wear resistance, it may also make the material more brittle. Careful design and stress analysis are necessary to ensure that components made from D3 do not fail under extreme conditions.
Ductility and Toughness
Ductility is the capacity of a material to undergo significant plastic deformation before rupture or failure. While D3 stainless steel excels in hardness and tensile strength, it’s worth noting that its ductility is somewhat lower in comparison. This means it may not stretch or deform in the same way as softer metals, which can be a disadvantage in certain applications.
However, D3 steel compensates for this with toughness, defined as the ability to absorb energy and plastically deform without fracturing. Toughness is critical for components that endure high shock loads or impact stresses. For example, tools made from D3 need to not only cut efficiently but also endure the sudden forces of striking materials without shattering.
In practical terms, the toughness of D3 stainless steel typically allows it to be used in demanding environments without facing catastrophic failure. It remains resilient in applications, which is a significant viewpoint for engineers assessing material qualities.
Thermal and Electrical Properties
Understanding the thermal and electrical properties of D3 stainless steel is essential for anyone interested in metallurgy and its applications. These properties significantly influence how this material behaves under various conditions, making them crucial in determining its suitability for specific applications. By understanding the implications of thermal and electrical conductivity, one can appreciate the benefits D3 stainless steel provides in both industrial and consumer contexts.
Thermal Conductivity
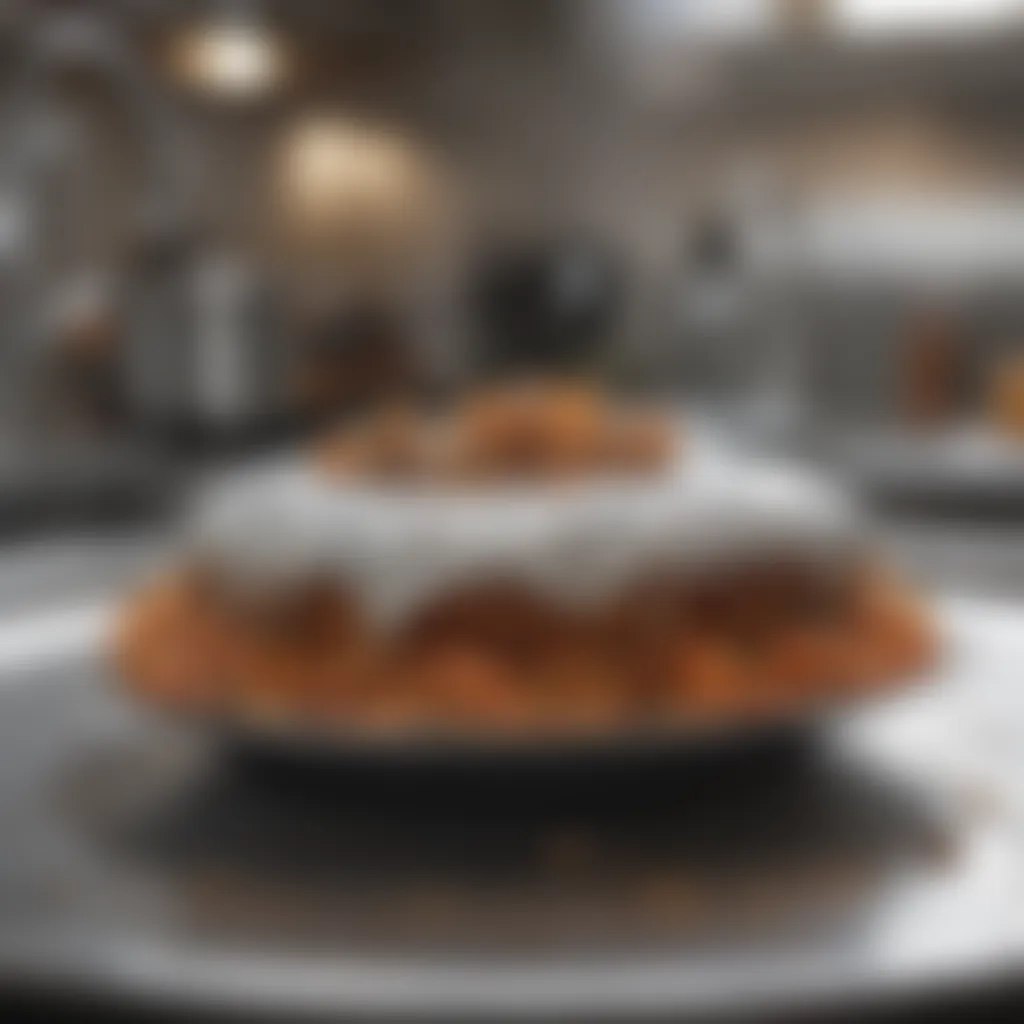
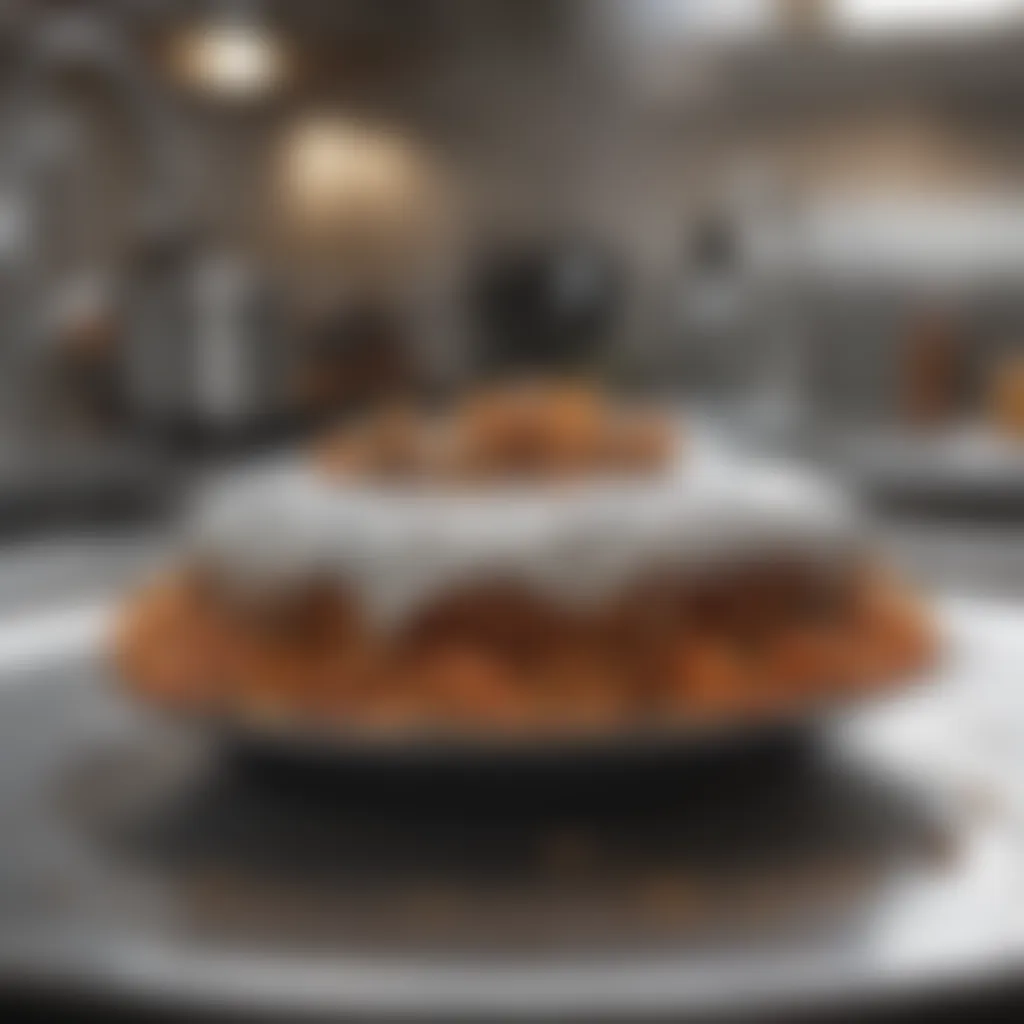
D3 stainless steel is known for its relatively low thermal conductivity when compared to other metals like copper or aluminum. This property can be a double-edged sword; on one hand, a lower thermal conductivity ensures that it doesn't heat up too fast, which can be beneficial in applications subject to sudden temperature fluctuations. For instance, in the manufacturing of cutting tools, this characteristic helps maintain temperature stability during operation, reducing the risk of thermal shock or distortion.
On the other hand, this lower conductivity might not suit applications requiring rapid heat dissipation. Consider the use of D3 steel in various types of machinery. If heat builds up too quickly without sufficient dissipation, it could lead to premature wear or failure. It's essential to weigh the benefits of thermal stability against the need for heat management in the design of components made from D3 stainless steel.
Some key attributes of thermal conductivity in D3 stainless steel include:
- Temperature Resistance: D3 can withstand high temperatures without losing its mechanical integrity, important in high-heat industrial environments.
- Heat Treatment: This alloy's response to various heat treatments also affects its thermal properties. Proper heat treatment can enhance its performance, making it more suitable for varied uses.
- Thermal Expansion: The thermal expansion coefficient of D3 is relatively low, which means it maintains shape well under thermal stress, a crucial factor for precision tools.
"Choosing materials like D3 stainless steel involves understanding how they react to heat and how that can affect the overall performance in the intended application."
Electrical Conductivity
While D3 stainless steel is not commonly used for electrical applications due to its low electrical conductivity, the nuances of this property are worth exploring. Electrical conductivity refers to how easily electrons can flow through a material. In the context of D3 stainless steel, it has a significantly lower conductivity than materials like copper or aluminum.
This low electrical conductivity can be advantageous. For instance, in applications where electrical insulation is more critical than conduction, such as in the fabrication of certain mechanical components, D3 excels. The reduced flow of electricity minimizes the risk of unwanted sparking or overheating in operational settings, especially in environments exposed to various electrical stresses.
Key points regarding electrical conductivity in D3 stainless steel include:
- Shielding from Electromagnetic Interference (EMI): In certain applications, the material acts as a barrier against EMI, which can be beneficial in sensitive electronic components.
- Corrosion Resistance in Electrical Applications: The alloy's inherent corrosion resistance also plays a vital role in extending the life of electrical components that may be exposed to harsh environments.
- Low Heat Generation: Due to its poor conductive nature, D3 stainless steel tends to generate less heat during electrical operations, offering a potential safety advantage in specific applications.
In summary, comprehending the thermal and electrical properties of D3 stainless steel brings clarity to its applications and limitations. By taking these properties into account, one can make informed decisions about employing D3 in a myriad of industrial and consumer products.
Corrosion Resistance Characteristics
When we talk about the resilience of materials, corrosion resistance often takes center stage, especially for those in fields that demand durability and longevity. In this segment, we’ll explore corrosion resistance characteristics of D3 stainless steel in detail.
Corrosion resistance is crucial as it determines how well a material can hold its ground against deteriorating elements. It’s not just about appearance; corrosion can lead to material weakening, product failure, and ultimately, safety hazards. Using materials like D3 stainless steel that boast superior corrosion resistance not only enhances product lifespan but also reduces maintenance costs and safety risks in various applications.
Resistance to Acids and Bases
D3 stainless steel's robustness in acidic and basic environments is one of the stellar characteristics that set it apart from other alloys. This resistance comes from the unique alloying elements within D3 that enhance its protective passive film. When this film forms, it acts like an invisible shield against aggressive chemicals.
The workhorse applications of D3 steel often reside in industries such as chemical processing and food production, where exposure to acidic substances may be a daily affair. Imagine a factory where pickle brine or vinegar is splashed around—using regular steel here could spell trouble. However, D3 handles it with grace.
Here are some notable points about D3’s performance in these environments:
- The high chromium content contributes to outstanding resistance to oxidizing acids.
- It maintains structural integrity when exposed to moderate corrosive concentrations.
- Less frequent maintenance translates to sustainable operations and lower overall costs.
Resistance to Chlorides
Chlorides are notorious villains in the world of corrosion, particularly in environments like coastal areas or in applications involving de-icing salts. However, D3 stainless steel isn’t easily deterred. Its unique combination of alloying elements helps mitigate the risks associated with chloride-induced stress corrosion cracking.
In practical terms, consider a marine vessel or an offshore platform where exposure to salty air is inevitable. Using D3 stainless steel in these settings bolsters the structure against corrosion while reducing the risk of pitting. Let's not forget that pitting can occur when a localized area becomes vulnerable—the last thing you want when depends on structural reliability.
Key benefits of D3's performance against chlorides include:
- Longevity in harsh environments, maintaining structural soundness over time.
- Lower maintenance demands due to improved performance in chloride-laden environments.
- Increased safety, ensuring that structures do not succumb to failure from hidden corrosion spots.
"Choosing the right material is half the battle won; understanding its properties makes you a warrior in your trade."
In summary, D3 stainless steel shines in corrosive environments, whether battling acids, bases, or chlorides. Its innate ability to resist such elements not only ensures product performance but also safeguards the investments made in manufacturing and construction.
Let's face it: whether you’re a professional or a discerning enthusiast, knowing the ins and outs of corrosion resistance gives you a leg up in making smart choices when it comes to materials.
Manufacturing Processes of D3 Stainless Steel
Understanding the manufacturing processes of D3 stainless steel is crucial due to its direct impact on the material’s properties and applications. Each step in the production chain, from melting to machining, can enhance or detract from the characteristics that make D3 stainless steel so valuable. By grasping these processes, you gain insight into how D3 can meet specific industrial needs and what considerations should be taken into account during manufacturing.
Melting and Casting Techniques
The melting and casting process is the very first step in producing D3 stainless steel, and it lays the groundwork for everything that follows. In this stage, raw materials are heated to high temperatures to form a molten state.
Typically, electric arc furnaces or induction furnaces are used to achieve the required heat. This method allows for precise control over temperature and atmosphere, minimizing impurities that could compromise the final product.
Once melted, the steel is cast into various forms, depending on what the end product will be. Continuous casting is a prevalent method because it produces high yields and reduces waste. The molten steel is poured into molds, where it cools and solidifies into a usable shape.
"The melting and casting procedures significantly determine the microstructure of D3 stainless steel, which in turn affects its hardness and wear resistance."
This initial phase is not just about heating and cooling; it’s about ensuring a uniform composition. Any inconsistencies during this can lead to weak spots in the final product. It's also important to consider the inclusion of alloying elements like chromium and molybdenum, which are added during the melting phase to enhance properties.
Forming and Machining
Once the stainless steel is cast into its desired shape, the next hurdle is forming and machining it into a final product. This phase encompasses various processes, including forging, rolling, and cutting.
Forming typically involves reshaping the initial cast material while it is still above its yield strength. Forging is particularly common for producing high-strength parts, as the mechanical deformation helps to refine the grain structure and increase toughness.
After forming comes machining, where precision tools cut, drill, or grind the material into exact specifications. D3 stainless steel is known for its toughness, which presents some challenges. Both forming and machining require careful handling to avoid excessive tool wear and ensure dimensional accuracy.
Moreover, lubrication plays an essential role during machining to minimize friction and heat, thus prolonging tool life.
Key Considerations in Manufacturing
- Material Integrity: Ensuring the final product adheres to specified requirements involves close supervision throughout the melting, casting, and machining processes.
- Quality Control: Rigorous testing standards must be applied to ensure that D3 stainless steel meets regulatory requirements and possesses the necessary properties for its intended use.
- Cost Factors: The choice of techniques can also influence overall production cost, from energy consumption during melting to tool wear in machining operations.
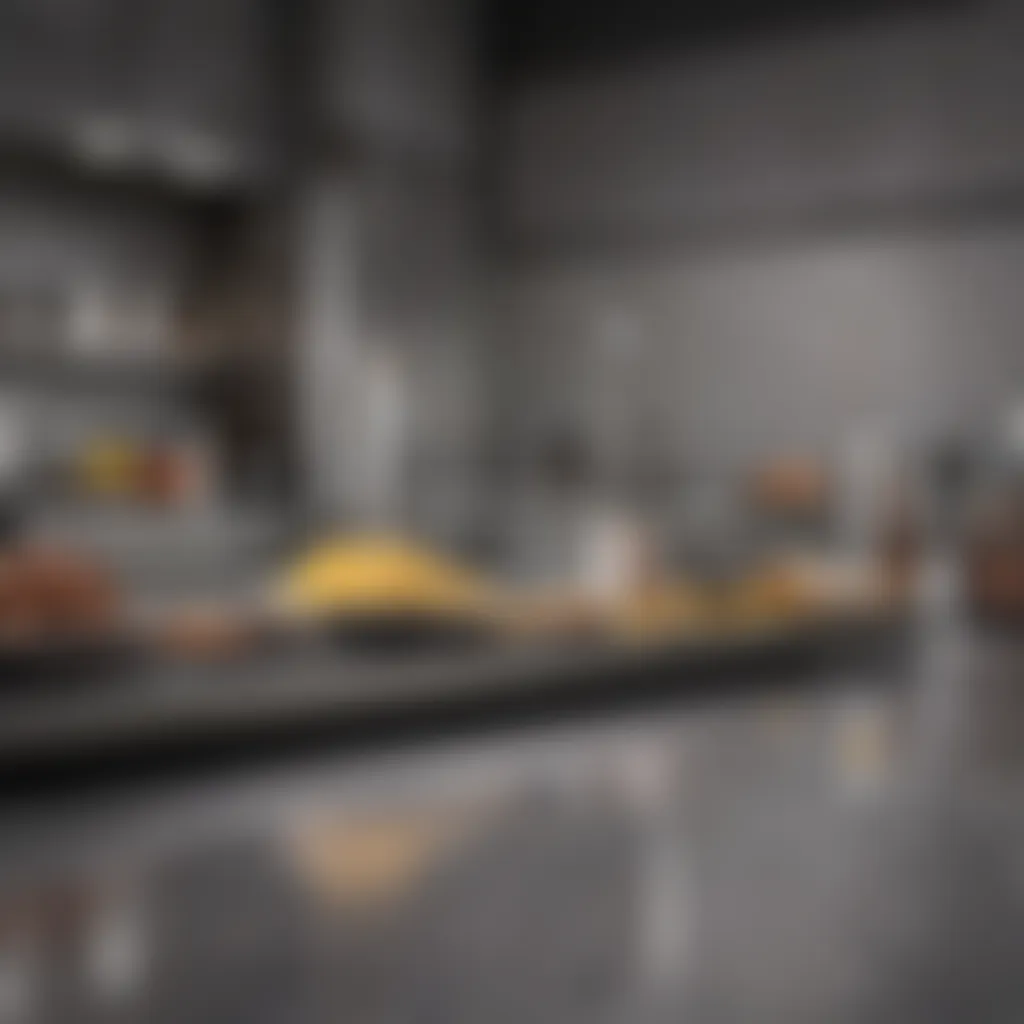

In summary, the manufacturing processes of D3 stainless steel are foundational to its performance and applications. Melting and casting create a starting point that defines the steel's properties, while forming and machining refine the material into practical, high-quality products suitable for various applications. Understanding this chain not only helps manufacturers optimize production but also aids end-users in selecting the right materials for their needs.
Applications of D3 Stainless Steel
The applications of D3 stainless steel are diverse and reflect its unique attributes, making it a vital material in various sectors. Understanding these applications not only showcases its importance in industry but also highlights the benefits and considerations that come with using this specific alloy. D3 stainless steel stands out for its hardness, corrosion resistance, and overall durability. These characteristics make it ideal for applications that require wear resistance and strength without compromising performance.
Industrial Uses
When it comes to industrial settings, D3 stainless steel is a go-to choice for numerous applications. Its exceptional hardness, often compared to that of tool steels, allows it to withstand significant wear and tear without losing its structural integrity. Often, D3 steel can be found in:
- Tooling: Various tools like cutting dies, molds, and other manufacturing tools benefit enormously from D3 steel's robustness, providing a longer service life, reducing downtime and maintenance expenditures.
- Agricultural Equipment: Many farmers rely on D3 steel for parts of equipment that require high resistance against abrasion, like seed drills and tillage tools. The reliability of these tools can be linked back to the strength of the materials used in their construction.
- Automotive Components: In the automotive industry, parts made from D3 stainless steel can endure harsh conditions, thus increasing their effectiveness and longevity.
Consumer Products
Beyond industrial applications, D3 stainless steel makes its way into everyday consumer products. Its aesthetic appeal combined with utility creates a balance that's hard to dismiss. Consider the following uses:
- Kitchen Utensils: Knives and other kitchen gadgets made from D3 stainless steel are not only sharp and effective but are also easy to clean, making them suitable for the modern kitchen. Households can rely on their durability for day-to-day tasks.
- DIY Tools: For those who enjoy home improvement projects, having reliable tools is crucial. Many hand tools, such as pliers and hammers, utilize D3 stainless steel for its inherent strength, allowing DIY enthusiasts to accomplish a variety of tasks without fear of tool failure.
- Outdoor Gear: Camping and hiking gear that uses D3 stainless steel benefits from its corrosion resistance, ensuring that items remain functional despite exposure to the elements.
Medical Instruments
In the medical field, the stringent standards for safety and effectiveness make D3 stainless steel a critical element. This alloy is widely used in:
- Surgical Instruments: Precision tools such as scalpels and forceps must maintain their sharpness and integrity, and D3 steel fits the bill perfectly. The ability to withstand sterilization processes ensures that these instruments are both safe and reliable.
- Dental Tools: Dentists often utilize D3 stainless steel instruments due to their long-lasting sharpness and resistance to corrosion, ensuring effective and efficient dental care.
D3 stainless steel is not just another alloy; its applications serve to enhance functionality across industries, ranging from heavy-duty equipment to everyday household items.
Comparison with Other Stainless Steels
When diving into the properties of D3 stainless steel, it stands out as a unique alloy in the world of metallurgy. Understanding how it measures up against other stainless steels is not just interesting; it’s essential for anyone involved in industries reliant on these materials. This comparison highlights specific elements, benefits, and considerations of using D3 over its counterparts.
Comparative Analysis of Mechanical Properties
In the realm of mechanical properties, D3 often strikes a remarkable balance between hardness and toughness. It generally exhibits excellent tensile strength, which is crucial in applications requiring high resistance to deformation. When placed alongside other stainless steels like AISI 304 or 316, D3 shows its mettle in wear resistance, particularly for tools or components subject to constant friction.
- Tensile Strength: For D3, this typically ranges around 1,500 MPa, which surpasses what many general-purpose stainless grades offer.
- Hardness: D3 can be hardened effectively through heat treatement, achieving hardness levels that make it an ideal candidate for cutting tools and molds. Hot rolled and cold worked states often yield a Rockwell hardness in the high 50s HRC.
- Ductility: While it provides substantial hardness, D3 does face some limitations in ductility compared to more alloyed stainless steels, leading to potential risks of cracking in severe conditions where flexibility is key.
In summary, if you’re in the market for a stainless steel that provides robust wear and abrasion resistance, D3 holds its own remarkably well.
Cost Effectiveness
Cost is a significant factor that can't be ignored when selecting a material. In comparison with other stainless steels, D3 offers a blend of performance and affordability.
- Material Costs: D3 typically costs less than premium grades like AISI 440C or 18/8 stainless steel due to its simpler alloying elements and abundant raw materials. This makes it desirable for projects that do not compromise on quality but are mindful of budget constraints.
- Longevity and Maintenance: Although it may require specific handling due to its brittleness, D3’s durability often translates into a longer lifecycle for products made from this steel. This means lower replacement costs over time, making the initial investment worthwhile.
- Efficiency in Manufacturing: Utilizing D3 can lead to reduced processing times in production, which ultimately lowers labor costs associated with machining and shaping the steel into final forms.
Investing in D3 stainless steel can be seen as a savvy strategy for companies looking to balance performance with financial prudence, which can't be understated.
"Choosing the right stainless steel is like picking the right tools for a job. It's all about matching the material to your specific needs and budgets on hand."
D3 stainless steel's mechanical properties and cost-effectiveness make it a super contender in many industrial realms, ensuring that it remains a go-to choice for both emerging and established manufacturers.
Future Trends in D3 Stainless Steel Production
The production of D3 stainless steel is at a juncture filled with opportunities for advancement. As industries continuously push for improved materials that can withstand the rigors of modern applications, understanding the future trends in D3 stainless steel production becomes paramount. This discussion reveals how innovations and sustainable practices are shaping the future of this highly regarded material, underscoring its significance in today's manufacturing realm.
Innovations in Alloying Techniques
The landscape of alloying in the production of D3 stainless steel is ever-evolving. One trend that has gained momentum is the use of advanced alloying compositions to enhance properties such as hardness, toughness, and corrosion resistance. A significant focus is on the incorporation of elements like nickel, chromium, and molybdenum, which have been historically utilized but are now being optimized through new techniques.
Research into nanostructuring is paving the way for improved mechanical properties. By modifying the microstructure at a nano-level, manufacturers can achieve a finer distribution of particles within the alloy. This can lead to a considerable improvement in strength without sacrificing ductility. Additionally, additive manufacturing, commonly known as 3D printing, has entered the conversation, enabling designers to create complex geometries and structures which were previously unattainable with traditional casting methods.
Potential benefits of these innovations include:
- Enhanced Performance: Better mechanical properties could lead to longer-lasting components in high-stress environments.
- Reduced Costs: Efficient alloying processes may lower overall material costs due to less waste and energy expenditure.
- Tailored Solutions: Customized alloy compositions to meet specific industrial requirements.
Sustainability Practices
As global awareness regarding environmental concerns rises, sustainability is becoming integral to the production of D3 stainless steel. Metal recycling, particularly the recycling of stainless steel, is one prominent practice that is gaining traction. Emphasizing the circular economy, manufacturers are increasingly relying on recycled materials to produce new stainless steel, reducing the need for raw materials and minimizing environmental impact.
Moreover, some facilities are now implementing energy-efficient technologies to lessen carbon footprints during production. This includes recovering heat from production processes and utilizing renewable energy sources to power operations. Such practices not only help in conserving resources but also align with stricter international standards aimed at promoting environmental stewardship.
Considerations surrounding sustainability in D3 stainless steel production include:
- Reduction in Resource Exploitation: Utilizing recycled materials lessens the dependency on mining.
- Lower Energy Consumption: Implementing newer technologies can dramatically reduce the energy needed for steelmaking.
- Compliance with Regulations: Staying ahead of emissions standards can prevent costly penalties and enhance corporate image.
Taking these steps helps in assuring consumers and industries that D3 stainless steel is not just a durable and reliable material but also a responsible choice in a world increasingly focused on sustainability.
"The future of D3 stainless steel manufacturing isn't just about strength and durability; it's about crafting a more sustainable and efficient path forward."
Challenges in D3 Stainless Steel Usage
D3 stainless steel is widely appreciated for its hardness and strength, making it a preferred choice in various industrial applications. However, like a coin has two sides, this material also comes with its own set of challenges that users must navigate. Understanding these challenges not only aids in decision-making but also helps in optimizing the usage and maintenance of D3 stainless steel in real-world scenarios.
The importance of addressing these challenges lies in ensuring that D3 stainless steel is utilized effectively, known to many in the metallurgy field. This section highlights two main hurdles: thermal expansion issues and machining difficulties. A careful examination can provide indispensable insights for engineers and manufacturers alike.
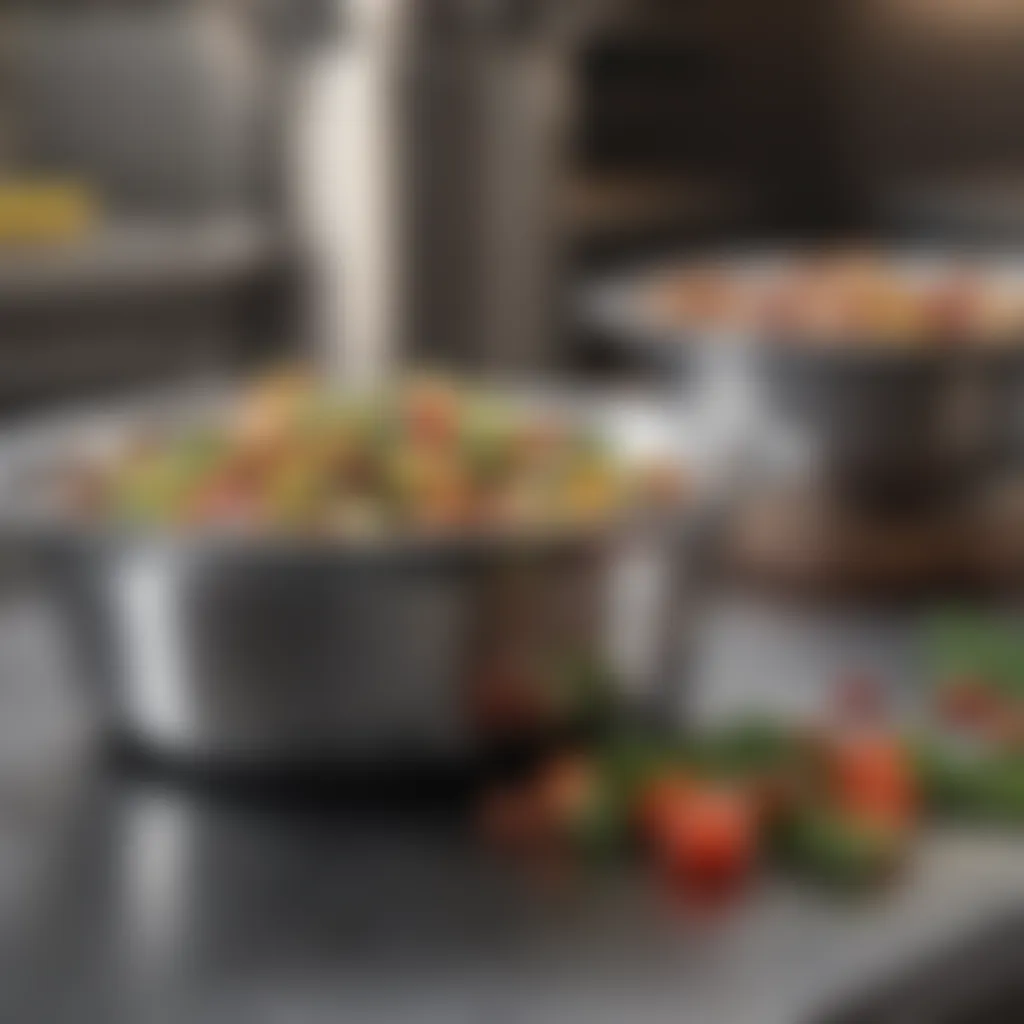
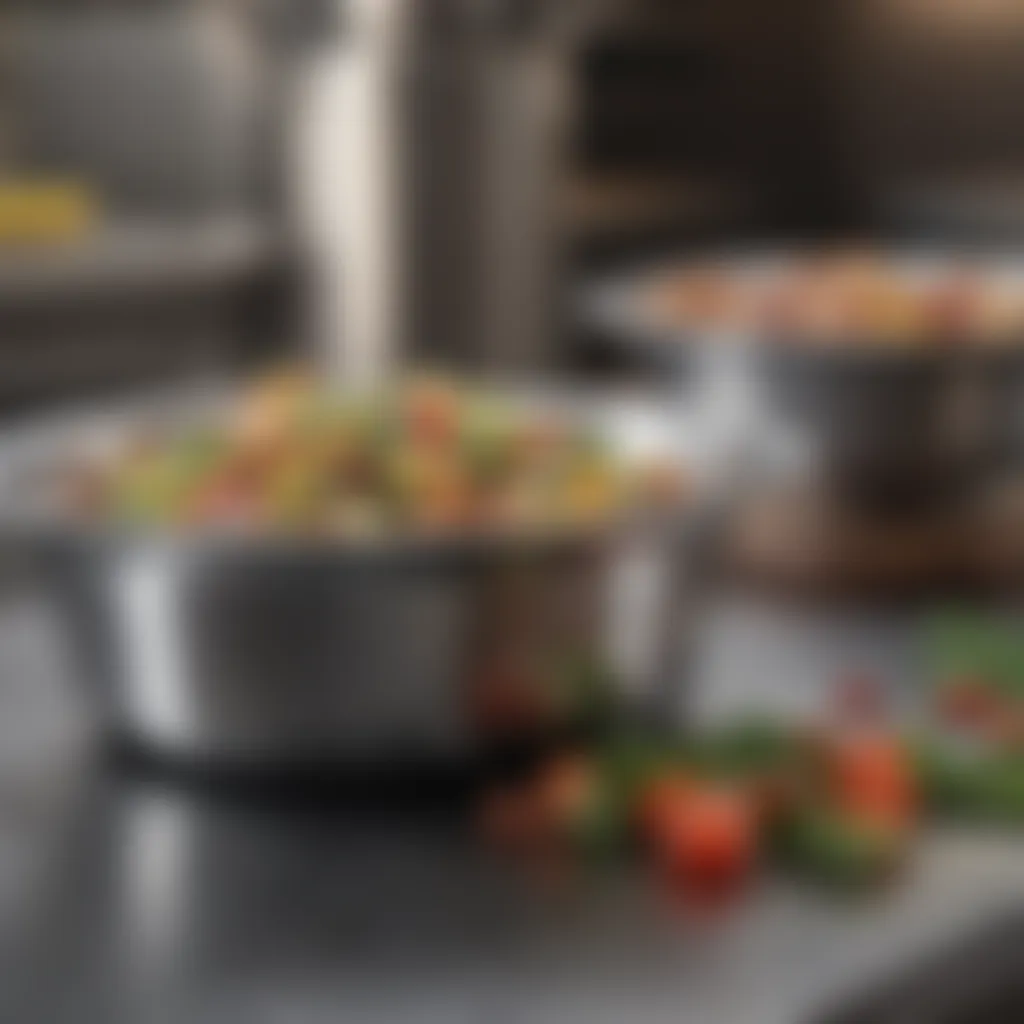
Thermal Expansion Issues
One notable challenge with D3 stainless steel is its tendency to expand when exposed to heat. Thermal expansion in materials is a common phenomenon, yet it poses unique difficulties in the case of D3 stainless steel due to its specific composition and properties. As the temperature rises, this steel can expand in size, which might create problems in tightly fitted assemblies or precision applications.
Key points to consider:
- Dimensional Changes: The expansion can lead to misalignments in mechanical assemblies. This misalignment can affect the performance and longevity of the equipment in use. Therefore, consideration of the thermal tolerances during design is essential.
- Selection of Fasteners: When using D3 stainless steel, particular care is required in selecting fasteners and fittings that can accommodate such expansion. If not, one risks premature failure or complications during operations.
- Heat Treatment: Implementing effective heat treatment methods can mitigate some of the challenges related to thermal expansion. However, this requires careful monitoring to prevent adverse effects on the material properties.
In essence, thermal expansion issues must be factored into planning stages. The correlation between temperature fluctuations and the steel's mechanical integrity cannot be understated.
Machining Difficulties
Machining D3 stainless steel can provide its own set of challenges as well. Although the hardness of D3 is an advantage in many applications, it makes cutting and shaping the steel a daunting task. Many who deal in this material understand that precision is key, and the machining process should be planned meticulously.
Points to note about machining difficulties:
- Tool Wear: The material’s hardness can lead to rapid wear and tear on tools. High-speed steel or carbide tools are often recommended, but they can come at a higher cost and require careful handling.
- Cutting speed and feed: Finding the right cutting speed and feed rates is essential to prevent overheating and ensure a smooth finish. Getting this wrong can lead to chipping or breaking of cutting tools, further complicating the machining process.
- Chip Formation: The way chips form when machining D3 stainless steel can also present challenges. Poor chip removal can lead to workpiece damage and hinder productivity.
Overall, while D3 stainless steel offers durability and strength, it comes with specific hurdles during machining that can impact production timelines and costs. Awareness of these challenges and proper strategies can help overcome many of the potential pitfalls. The careful balance of utilizing its best qualities, while being mindful of its limitations, can lead to greater efficiency and success in applications.
"Understanding the nature of any material is the first step toward mastering it. D3 stainless steel is no different."
Environmental Considerations
In today’s world, where climate change and sustainability are at the forefront of global discussions, environmental considerations in metallurgical practices have taken on new importance. D3 stainless steel, which is recognized for its specific properties, also embodies significant aspects that make it stand out in terms of its environmental impact. The recyclability of D3 stainless steel and the environmental effects of its production processes are two key elements that deserve closer attention. By understanding these factors, consumers and manufacturers alike can make more informed choices.
Recyclability of D3 Stainless Steel
D3 stainless steel shines when it comes to its recyclability. Unlike many materials that become waste after their initial use, D3 can be recycled multiple times without losing its intrinsic qualities. This feature significantly reduces its environmental footprint. For instance:
- Resource Conservation: Recycling D3 stainless steel requires less energy compared to producing new steel from raw materials. This process conserves natural resources like iron ore and decreases the need to mine additional resources.
- Waste Reduction: By recycling, we cut down the amount of waste that ends up in landfills. Furthermore, recycled D3 stainless steel can be used in new applications, which not only alleviates landfill issues but also fosters a circular economy.
- Lower Emissions: The energy saved during the recycling process also translates to fewer greenhouse gas emissions. Switching gears from traditional steel production to using recycled materials can be a game-changer in reducing overall environmental impact.
Additionally, many companies are now focusing on closed-loop recycling systems where waste materials that are generated during production are reused, leading to even less waste being produced.
Environmental Impact of Production Processes
The production processes for D3 stainless steel, while effective in creating a resilient product, are not without their challenges regarding environmental safety. A few key points to consider include:
- Energy Intensive: The manufacturing of D3 stainless steel often requires significant amounts of energy, primarily derived from fossil fuels. This reliance can lead to a larger carbon footprint, which is a major area of concern for advocates of clean energy sources.
- Chemical Usage: Various chemicals are involved in the production process, which can pose environmental hazards when not managed correctly. Ensuring that these substances do not contaminate air or water is critical for sustainable production practices.
- Sustainable Innovations: On a positive note, there are ongoing innovations in production methodologies aimed at minimizing environmental damage. For example, new technologies are being developed for energy-efficient melting and the use of renewable energy sources. These efforts not only stabilize the industry's impact on the environment but may also reduce production costs in the long term.
"It's essential for industries to evolve and adapt their processes to safeguard our planet while meeting rising demands for materials such as D3 stainless steel."
Safety Standards and Regulations
Understanding safety standards and regulations in the context of D3 stainless steel is crucial, especially given the material’s extensive applications in various industries. These standards not only ensure that the products made from D3 stainless steel meet specific safety criteria, but they also play a significant role in maintaining the overall quality and performance of the material throughout its lifecycle.
The importance of adhering to safety standards lies in the protection it provides, both to the end-user and to the manufacturers. By following established guidelines, companies can ensure that their products do not pose risks to health or safety when used as intended. This is particularly vital when considering that D3 stainless steel is often employed in high-stakes environments like medical instruments, food processing, and heavy machinery. The potential for accidents stemming from defective materials can have serious ramifications, making compliance all the more pressing.
International Standards for Alloy Use
International standards for alloy use are established by organizations such as the American Society for Testing and Materials (ASTM) and the International Organization for Standardization (ISO). These bodies create comprehensive guidelines that outline the requirements for alloy compositions, performance evaluations, and testing procedures. For D3 stainless steel, following these international standards ensures that the alloy performs its functions reliably across different environments.
- ASTM A681 specifies the chemical composition, mechanical properties, and heat treatment specifications for tool steels, including D3, emphasizing its applications in high-wear situations.
- ISO 683-1 deals with heat-treatable steels, outlining the necessary controls for preparing steel intended for various uses, favoring D3 in scenarios where strength is paramount.
Compliance with these standards also facilitates global trade. When products meet international criteria, they become more competitive, allowing manufacturers to access wider markets and ensure their products are acceptable in different regions.
"Standardization increases quality assurance and reduces the potential for variability in manufacturing processes."
Compliance and Quality Control
Compliance and quality control are two sides of the same coin in ensuring that D3 stainless steel maintains its integrity throughout production and use. Quality control measures must be diligently implemented in all stages of the supply chain. From raw material selection to final inspection, each step matters.
Manufacturers often utilize the following methods to ensure compliance and quality:
- Regular audits: These ensure that existing processes align with safety regulations and standards.
- Material testing: Including tensile tests, hardness tests, and corrosion resistance tests help ensure the D3 stainless steel meets or exceeds quality benchmarks.
- Documenting and tracking: Every aspect of production should be documented, tracking any deviations from standard practices or specifications.
When companies prioritize quality control, they minimize the risk of producing defective products, fostering a reputation for reliability. Ultimately, this adherence to standards translates into customer trust and satisfaction, essential elements for any business operating in competitive markets.
End
Concluding anything requires careful thought, especially when it comes to something as intricate as D3 stainless steel. Throughout this article, we've peeled back the layers on its properties and real-world applications, and that it’s become clear how its unique attributes cater to varying needs.
To summarize, D3 stainless steel stands out mainly due to its combinations of hardness, tensile strength, and corrosion resistance. From industrial settings to household uses, its resilience makes it a go-to choice for professionals in metallurgy and engineering. Its ability to withstand demanding operational requirements not only enhances product longevity but also minimizes the frequency of replacements, ultimately leading to cost savings and greater efficiency in production environments.
Apart from its impressive technical capabilities, understanding D3 through a lens of sustainability is equally crucial. As industries lean more into eco-friendly practices, the recyclability of D3 stainless steel presents an advantage that can’t be ignored. This aspect ties back into broader environmental considerations and serves as a benefit for both manufacturers and consumers looking to make greener choices.
Furthermore, adhering to safety regulations not only creates a safe workspace but also sharpens the focus on quality control throughout the manufacturing processes. As discussed, the compliance with international standards not only builds trust but also creates confidence among users.
In closing, the exploration of D3 stainless steel in this comprehensive piece offers more than just insights into material properties. It emphasizes the balance of performance, cost-effectiveness, and environmental responsibility, demonstrating that solid choices in material can yield substantial benefits.
"Understanding the materials we use leads to better decisions and ultimately, better outcomes in our everyday lives."
Summary of Key Insights
- D3 stainless steel is known for high hardness and excellent wear resistance.
- Key components of its composition significantly impact its mechanical properties.
- The steel's usage spans from industrial applications to consumer goods, highlighting its versatility.
- Sustainability in the production process contributes to its long-term appeal.
- Adherence to safety standards reassures users regarding quality and reliability.
Final Thoughts on D3 Stainless Steel
In light of all the discussed points, D3 stainless steel isn't just another material; it brings thoughtful advantages to various sectors. With its famed strength and durability, it fulfills not only physical needs but also aligns with growing environmental consciousness. It’s a choice that pays off, both performance-wise and ethically.
As households increasingly seek durable products, understanding materials like D3 stainless steel offers a deeper appreciation of what goes into items we often take for granted. Each pot, blade, and tool crafted from D3 serves as a testament to the thoughtful engineering and meticulous attention to detail that goes into steel production. It's not just about making a choice; it's about making the right choice.