Crafting Your Own Cyan Dye: A Complete Guide
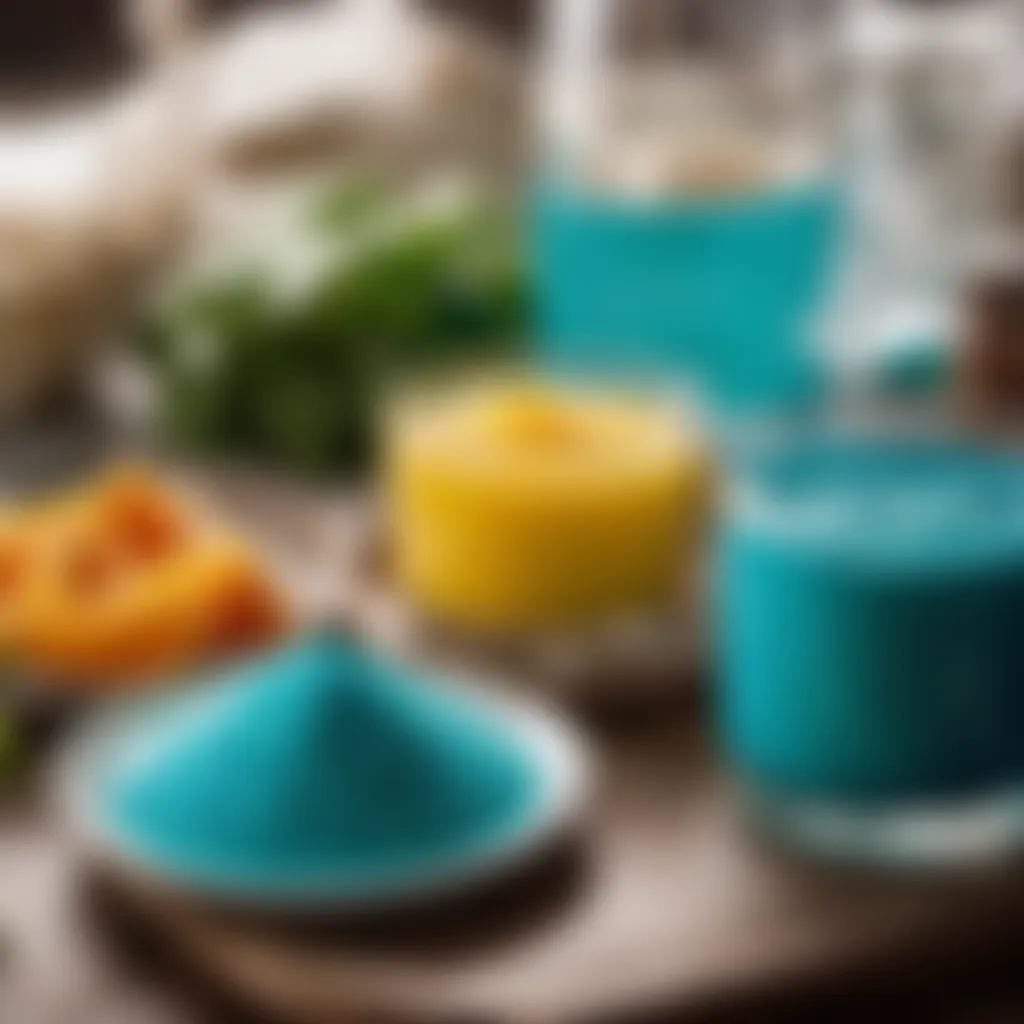
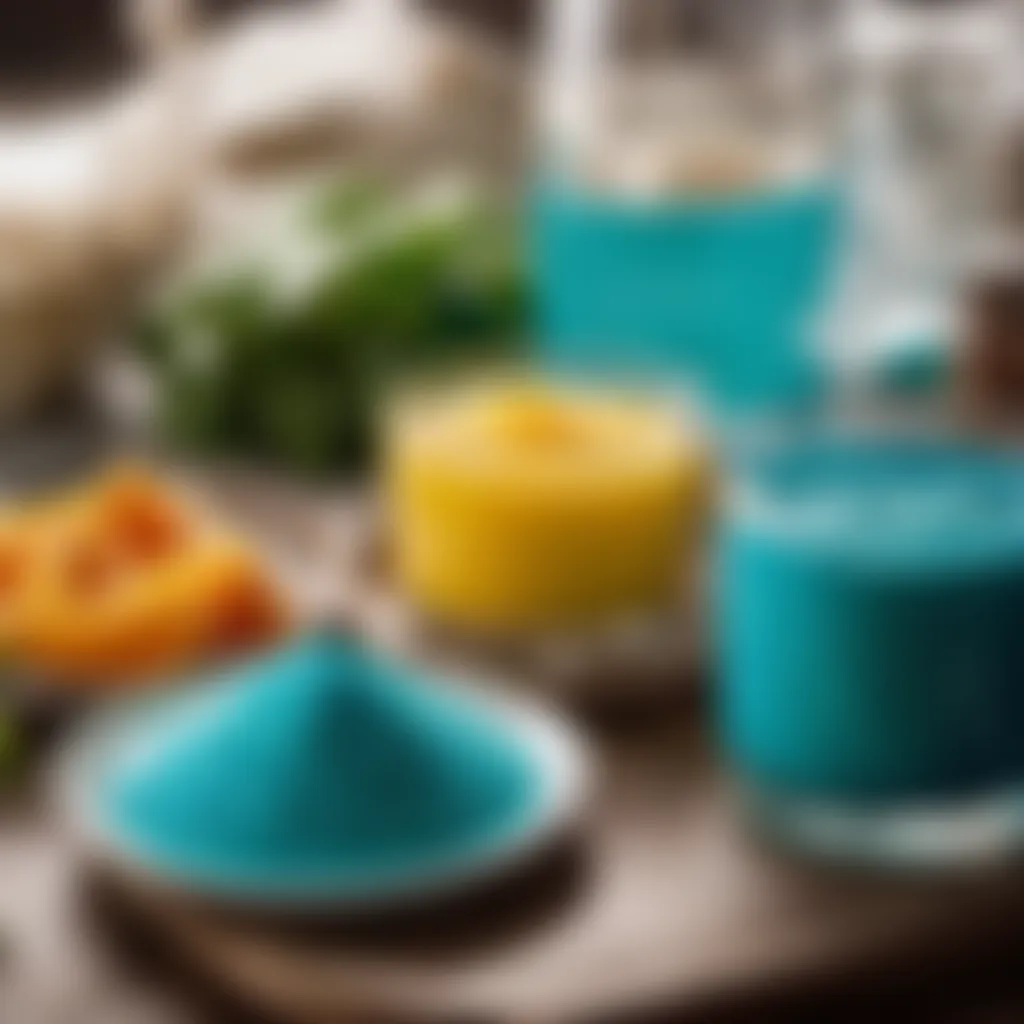
Intro
Crafting your own cyan dye can feel like a daunting task at first. But fear not! With a little guidance and a dash of patience, you can achieve stunning results. This guide is designed specifically for enthusiasts who wish to explore the fascinating world of dye making from the comfort of their kitchens. Whether you're interested in dyeing fabrics, adding color to art projects, or just curious about the process, everything you need to know is packed into the following sections.
From gathering materials to the delicate balancing act of mixing and applying, each step is laid out clearly. So, grab your apron, and let's dive into the intricate yet rewarding journey of creating cyan dye!
Ingredients:
In this section, we’ll list all the ingredients you’ll need to concoct your cyan dye. Precision is key! Even minor deviations can impact the final color, so measuring accurately is a must. Here’s what you need:
- Water: 1 liter
- Magnesium sulfate (Epsom salt): 100 grams
- Cyanidin (natural dye): 10 grams (you can extract this from blueberries or black rice)
- Lemon juice: 50 milliliters (to help fix the dye)
- White vinegar: 100 milliliters (this will also fix the dye and enhance its vibrancy)
- Fibers (fabric or yarn): 200 grams (cotton or silk works best)
Make sure to gather all these ingredients before moving on. Having everything in one place will keep you organized and make the process smoother.
Detailed Instructions:
Step 1: Prepare Your Materials
Start by pre-soaking your fabric. This allows the fibers to absorb more dye later. Fill a bowl with warm water and add a splash of white vinegar. Soak the fabric for about 30 minutes, then wring it out gently.
Step 2: Extracting Dye from Source
If you’re using blueberries or black rice, combine them with 600ml of water in a saucepan. Bring to a slow boil, then let it simmer for 15-20 minutes. The liquid will turn a deep, rich color. Strain the solids and keep the liquid, which is packed with color potential.
Step 3: Mix the Dye
In a separate pot, combine the strained liquid with 100 grams of magnesium sulfate and 50 milliliters of lemon juice. Stir it well until everything dissolves. Once the mixture is homogeneous, bring it to a gentle heat (not boiling!) and maintain it for about 10 minutes. This step enhances the color extraction.
Step 4: Dyeing Process
After heating, add your pre-soaked fabric into the pot. Stir gently to ensure even dye distribution. Turn down the heat and let it simmer for about 30-45 minutes, stirring occasionally. You will notice the fabric absorbing the dye, gradually turning a vibrant cyan shade.
Technical Aspects:
Keep in mind the following:
- Temperature settings: Always avoid boiling when dyeing; maintain a low simmer.
- Timing specifics: The longer you leave the fabric in the dye bath, the more intense the color will be. However, be cautious, as over-dyeing can lead to uneven patches.
Key Techniques:
- Always stir the mixture gently to prevent fabric from clumping.
- Test the color on a small fabric piece before dyeing the main material.
Sequential Steps:
- Gather all materials and prepare your workstation.
- Pre-soak fabric in a vinegar-water mixture.
- Extract the dye from your source of choice.
- Combine the dye with magnesium sulfate and lemon juice, then heat carefully.
- Add the fabric into the dye pot and simmer for the required time.
Troubleshooting Tips:
If things don't go as planned, don’t worry!
- If the dye isn’t dark enough, you can always repeat the dyeing process.
- Should your fabric seem too vibrant, rinse it under cold water until the color lightens to your liking.
"Remember, creating art takes practice—don't be disheartened by initial failures. Each attempt is a step closer to mastering the technique."
Once you've finished the dyeing, allow your fabric to cool before rinsing it gently with cold water. Let it dry in a shaded area to preserve the vibrant hue without fading in direct sunlight.
By now, you should have all the tools and knowledge to create your own cyan dye. Good luck!
Intro to Cyan Dye
Cyan dye is not just a color; it's a vibrant part of our cultural and artistic history that has evolved over centuries. Understanding cyan dye is essential, because it connects the past with the present, showcasing the chemistry that invites both creativity and technical know-how. This section sets the stage for those keen on crafting their own cyan dye, providing insights into its significant history and modern applications. The craft of dyeing can feel daunting, but with a solid background on cyan's importance, we can ease into the process with confidence.
Historical Significance of Cyan Dye
Cyan dye has roots deeply entwined in various cultures worldwide, with historical records pointing to its use long before modernity crept in. The ancient Egyptians, for example, harnessed cyan colors for their textiles, often associating them with prosperity and abundance. This dye was more than just an aesthetic choice; it held cultural symbolism. The ancient Chinese also created stunning fabrics dyed in shades of blue and cyan.
For many centuries, the journey of this dye involved intricate methods of extraction from plants like woad and indigo. These early artisans were pioneers, experimenting with natural resources available to them. Their legacy continues, reminding us that cyan dye is steeped in tradition, always being used to adorn garments, tapestries, and paintings.
Contemporary Uses of Cyan Dye
Fast forward to today, cyan dye finds its way into various sectors, from textiles to graphic design. In fashion, it's lauded for its refreshing appearance and versatility, easily blending with other colors to create striking combinations. In home decor, cyan serves as a popular choice for curtains, upholstery, and decorative pieces, providing a vibrant pop without overwhelming the senses.
Additionally, cyan dye is now essential in the world of printing - notably in inks. Its enduring charm has earned it a spot in graphic design, where its vibrant hue brings life to posters and digital media. Interestingly, these uses of cyan dye are not just about aesthetic appeal; they often spark conversations around sustainability and eco-friendly practices as the dye industry explores natural sourcing techniques.
"In the tapestry of dye history, cyan is a thread that weaves together the past and the present, binding cultures and artisans across time and space."
Cyan dye is not merely a product; it is a story waiting to be told, one that highlights human creativity and resourcefulness - a compelling reason to dive deeper into dyeing craft.
Understanding Dye Chemistry
To grasp the nuances of creating a cyan dye, one must first delve into the realm of dye chemistry. This area is crucial as it informs the dyer about how dyes interact with different fabrics and substrates. Understanding the chemical reactions can mean the difference between vibrant, lasting colors and dull, fleeting results. By engaging with the principles of dye chemistry, the dyer can achieve more control over the outcomes of their projects, which ultimately leads to greater satisfaction and success in the dyeing process.
Chemical Composition of Cyan Dyes
At the heart of any dyeing process is its chemical composition. Cyan dyes are primarily composed of specific compounds that contain chromophores, which are responsible for color production. These chromophores absorb certain wavelengths of light while reflecting others, creating the visible color we associate with cyan. The stability of these chromophoric structures under various environmental conditions determines how well the color will hold up over time.
Another important element in the chemical makeup is the affinity of the dye for the material being dyed. Different fibers, whether natural or synthetic, have varying chemical properties that can react differently with cyan dye, impacting the final result. For a successful dyeing experience, one must choose the appropriate type of cyan dye tailored to the fabric's composition.
Types of Cyan Dyes
When exploring the world of cyan dyes, it’s essential to differentiate between the various types available.
Natural vs. Synthetic Dyes
Natural dyes have been used for centuries, often derived from plants, minerals, or insects. The intriguing aspect of natural dyes is their environmental friendliness. They are seen as a beneficial choice for those looking to create sustainable products. However, they can sometimes be less predictable in color outcome and may fade more quickly than their synthetic counterparts. Synthetic dyes, on the flip side, offer a consistent palette and more vibrant shades. They are often more popular due to their long-lasting characteristics, albeit at the cost of using chemical processes that may not always be eco-friendly.
The choice between natural and synthetic dyes often reflects the values and objectives of the dyer. While natural dyes respect traditional methods and promote sustainability, synthetic dyes provide reliability and brilliance in color that many find appealing.
Dyes Derived from Plants
Dyes derived from plants exhibit unique kitchen chemistry. For instance, indigo is a well-known plant-derived dye that, while not cyan itself, shares some characteristics with cyan dyes in terms of its chemical makeup. The extraction process from plant sources requires a bit of know-how, often involving boiling parts of the plant to release their dye properties into a solution.
What makes plant-derived dyes attractive is their connection to tradition and biodiversity. They foster a deeper relationship with nature. However, the process can be labor-intensive, and achieving the desired intensity consistently can be more challenging compared to synthetic options. Still, many artisans are drawn to the charm of working with materials that have a history and a story.
"Embracing the natural routes in dyeing not only creates beautiful art but also connects you to centuries of tradition."
Essential Materials and Tools
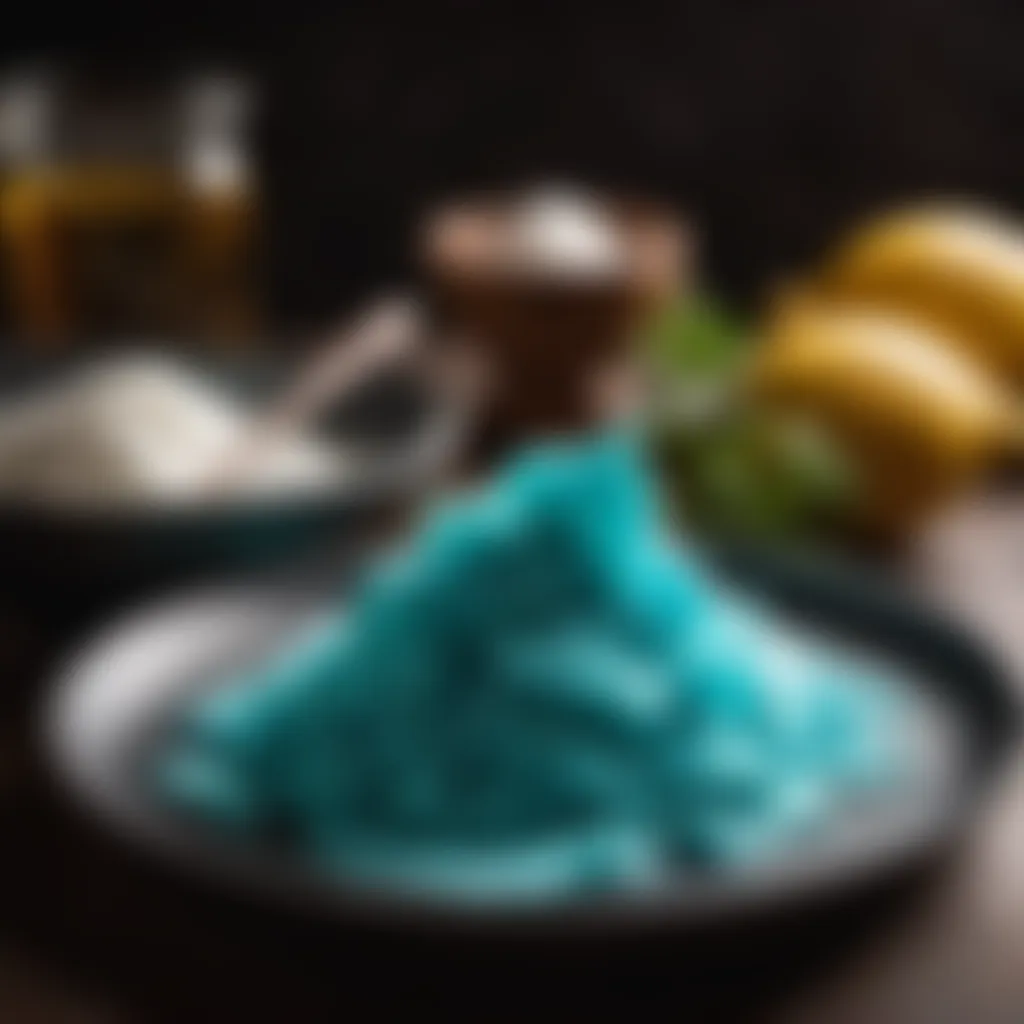
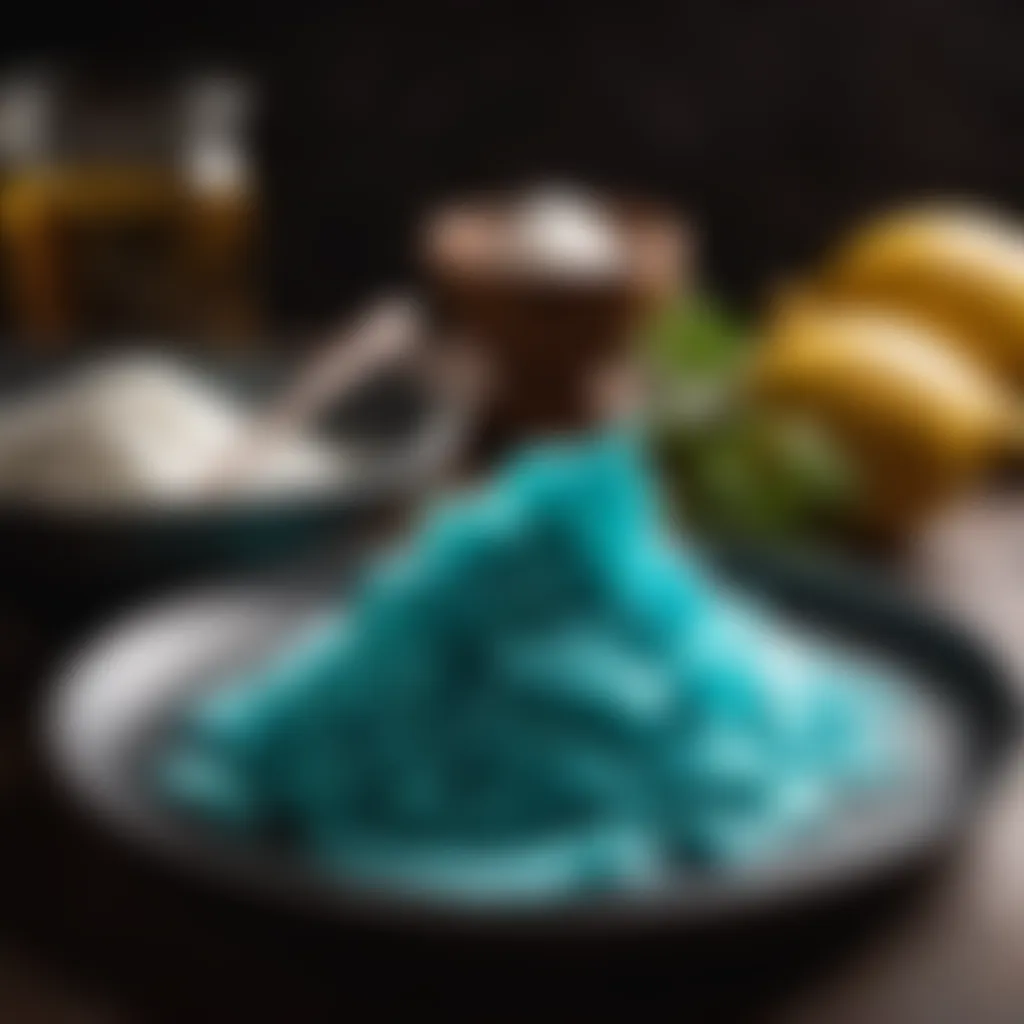
When it comes to crafting your very own cyan dye, having the right materials and tools at your disposal is crucial. These elements not only enhance the dyeing process, but also ensure its safety and effectiveness. Comprehending the necessity of these components shapes how you'll approach dye creation. Starting with solid foundations can mean the difference between a vibrant success and a disappointing muddle.
Required Chemicals for Cyan Dye
The chemicals you will need for producing cyan dye play a pivotal role in its final color and quality. Typically, the most common chemical used is indigo, which, despite being known for its deep blue hue, can be manipulated in a manner that yields shades of cyan when combined with specific additives.
Another key ingredient can be thiourea dioxide, a reducing agent that helps to facilitate the dyeing reaction. Both of these chemicals interact in ways that are foundational to the dyeing process, resulting in the rich, nuanced tones that one would expect from a well-crafted cyan dye.
Consider the purity of these chemicals. Using high-quality, reputable sources for your chemicals ensures consistency and reliability in your outcomes. Impurities can be unpredictable and could ruin even the best thought-out dyeing experiment.
Tools Needed for Dye Production
The tools you select are equally as important as the chemicals. They serve various roles from preparation to application and can significantly impact the efficiency of your dyeing project.
Safety Equipment
Safety equipment is an absolute must. The art of dyeing comes with risks, notably from the chemicals involved, which can irritate skin or eyes. Wearing gloves is essential to avoid direct contact. Moreover, using goggles can be a wise preventative measure against splashes. Even a simple face mask can protect against the inhalation of dust or fumes when dealing with powdered substances.
The key characteristic of proper safety gear lies in its barrier function. Its presence is not only a recommended practice but a lifeline for ensuring a secure atmosphere during your dyeing sessions. For instance, nitrile gloves are a popular choice as they are both flexible and resistant to various chemicals, contributing to a seamless experience.
Measuring Instruments
Accurate measuring instruments are indispensable for achieving the desired results in dye creation. Whether you are using digital scales for weight or volumetric flasks for liquid measurement, precision is non-negotiable. This fidelity ensures consistency, which is vital in any chemical endeavor.
One common choice is the digital scale, which often comes with features to measure in grams or ounces, allowing for flexibility in formulation. A unique feature of these scales is their ability to hold weight while you add substances to avoid recalibrating with each new ingredient. This is especially advantageous for novice dyers who might find constant adjustments cumbersome.
In summary, thorough preparation with the right materials and tools can make all the difference in crafting an excellent cyan dye. Not only does it set the stage for practical application, but it also fosters an environment of safety and precision, which are critical for any successful artistic endeavor.
Preparing Your Workspace
Creating your own cyan dye is a rewarding venture, but it requires a workspace that fosters safety and efficiency. The workspace is not just a physical area, it's the foundation that can make or break your dyeing experience. The benefits of a well-prepared workspace go beyond mere aesthetics; they include safety and the overall quality of your dyeing projects.
A clean, organized space minimizes the likelihood of errors and accidents. You'll need ample room to spread out your materials and tools, as a cramped workspace can lead to mishaps—spill dye, mixed chemicals, or worse. Plus, when you're making something as intricate as dye, a peaceful environment helps you focus. You want to keep distractions at bay so you can put your whole heart into the process.
Optimal Workspace Conditions
When setting up your workspace, think about a few key elements:
- Lighting: Good lighting is a must. Natural light is ideal, but if that's not possible, ensure you have bright, white artificial lighting. You want to see every detail.
- Ventilation: Dyeing can release strong odors, especially if you're working with certain chemicals. A well-ventilated area ensures that harmful fumes dissipate quickly. Open windows or a fan can work wonders.
- Surfaces: Use surfaces that are easy to clean, preferably non-porous. This will help you manage any accidental spills without leaving permanent stains. A dedicated workspace mat can be beneficial.
- Organization: Keep all your tools and materials within arm's reach. Utilizing shelves, bins, or caddies can help you store items logically and efficiently, avoiding a chaotic search mid-project.
"A well-prepared workspace is the unsung hero of any creative process. It might seem mundane, but it's the stepping stone to successful results."
Safety Precautions and Best Practices
Safety first! Working with dyes means handling chemicals, and some can present risks if not treated with respect. Here’s how you can safeguard yourself:
- Personal Protective Equipment (PPE): Always wear gloves to protect your skin from irritation. Goggles are also advisable, especially if you're mixing certain compounds. An apron can keep you clean.
- Emergency Preparedness: Have a First Aid kit nearby. Should an accident happen, it’s best to act fast. Know the emergency numbers by heart.
- Material Safety Data Sheets (MSDS): Familiarize yourself with the dyes and chemicals you are using. Most come with guides on how to handle them safely.
- Work Alone: If possible, try to have your dyeing sessions when you can work undisturbed. Not only does this encourage focus, but it reduces risks associated with distractions.
- Disposal Practices: Understand how to properly dispose of excess dye and chemicals. Improper disposal can harm the environment and may even be illegal in some areas.
In summary, a conscientious approach to preparing your workspace sets the stage for an enjoyable and productive dyeing experience. You’re not just making dye; you’re crafting something valuable.
For more safety tips and information on workspace organization, consider visiting Wikipedia or Britannica for guidance.
Creating the Cyan Dye Solution
Developing a cyan dye solution is more than simply combining ingredients; it’s a delicate blend of precision and chemistry that lays the foundation for successful dyeing. The process involves critical choices regarding the materials, ratios, and techniques, which can ultimately influence the vibrancy and longevity of the color achieved. This section emphasizes the importance of this stage in the dye-making journey, helping readers to grasp both the benefits and considerations that impact their final results.
Creating a successful solution of cyan dye is a skill that balances creativity with science. When approached correctly, the resulting color can not only satisfy aesthetic desires but also hold sustainable qualities that are environmentally friendly. Understanding this balance leads to better outcomes and a deeper appreciation for the art of dye-making.
Step-by-Step Instructions
Measuring Ingredients
In the world of dye-making, measuring ingredients accurately is crucial. Miscalculating amounts can lead to disastrous results, such as an unexpected shade of green rather than the desired cyan. For many, precise measurement is the backbone of quality dye—ensuring that the color comes out just right.
A key characteristic of measuring ingredients is consistency in technique. Using scales or graduated measuring cups promotes uniformity, which is a major advantage for sequential dye projects. When you grasp the delicate balance of ingredient amounts, you can achieve results that you can replicate time and again.
However, one unique feature of measuring ingredients is the potential for variance in the source materials. For example, if a plant-based dye ingredient is sourced from different harvests, the potency might change. This variability can influence how much is necessary in each individual batch, leading to different outcomes. Thus, this might cause some to find measuring tedious, yet it’s essential for mastering the craft.
Mixing the Solutions
Once the ingredients are accurately measured, the next vital step is mixing the solutions. This phase allows you to symbolize the fusion of components into one coherent dye. Thoughtful mixing ensures even distribution of color throughout any substance the dye is applied to, enhancing the application experience.
Mixing is particularly beneficial as it allows for customization in dye strength and depth. Whether you aim for a pastel or a rich, deep shade of cyan, this part of the process empowers you to bring your artistic vision to life. Stir at a measured pace, as vigorous mixing can possibly introduce air bubbles, undermining the overall visual quality of the dye solution.
However, keep in mind the unique feature of temperature during mixing. Warmer temperatures generally enhance solubility, allowing colors to develop more vibrantly. Yet, too much heat may cause some ingredients to break down, losing those beautiful dye characteristics. The right balance of warmth can mean the difference between a successful solution and a muddy color.
Common Mistakes to Avoid
Even seasoned dyers may trip over a few pitfalls when creating their cyan dye solutions. Here are a few common mistakes:
- Neglecting to Pre-Wash Fabric: Fabric should be clean to best absorb dye.
- Incorrect Ratios: Not adhering correctly to recommended ingredient amounts can lead to unexpected colors.
- Forgetting to Test: Always test on scrap fabric before going all in.
By staying mindful of these areas, dyers can refine their techniques and bolster their outcomes, ultimately crafting a cyan dye solution worth showcasing.
Testing the Dye
Testing the dye is a pivotal phase in the dyeing process. It’s not merely an afterthought; rather, it is a cornerstone that gives you confidence in the quality and longevity of your textile art. Think of it as the litmus test for your labor and creativity. By ensuring that the colors you’ve worked hard for hold their ground against time and other elements, you elevate your work from simple craft to a durable piece of art that you can cherish and showcase.
Methods for Testing Color Fastness
When it comes to testing color fastness, there are various methods available, each tailored to mimic real-life conditions your dyed fabric will endure. The idea here is to simulate wear and tear to predict how well your colors will hold up. Here are some methods to consider:
- Light Fastness Test: Cut a small piece of your dyed fabric and expose it to sunlight for several hours. Compare the exposed area to an area that was protected from the light. If you notice fading in the exposed area, the dye may not be lightfast and will fade quickly if used in bright environments.
- Wash Fastness Test: Create a small sample that you can wash. Launder it under the same conditions you’d normally use for your textiles, and pay attention to the color change. If noticeable fading occurs, it might be a sign to rethink your dye process or the materials used.
- Rubbing Test: This is a simple yet effective test. Rub a damp white cloth or cotton ball against the dyed fabric. If color transfers onto the cloth, your dye may not be set adequately, suggesting the need for a fixative or a change in dyeing technique.
It's good to run these tests early in your dyeing practice; they can save a lot of heartache in future projects.
Adjusting Dye Characteristics
Adjusting the dye characteristics is just as crucial as testing for color fastness. Once you've tested your dye, you often find that you may want to make alterations for better outcome. This is where your understanding of the dyeing process truly shines. Here are some factors that you might adjust:
- Concentration of Dye: Sometimes the color is either too pale or too intense. Diluting the dye solution with water can lighten the shade, while adding more dye can deepen it.
- pH Levels: The acidity or alkalinity of the dye bath can dramatically affect the final colors. This can be adjusted with vinegar for acidity, or baking soda for alkalinity. Not all dyes react the same way to pH shifts, so knowing your specific dye’s behavior is essential.
- Temperature Control: Some dyes require a specific temperature range to develop their full color potential. Keeping your dye bath at the right temperature will yield consistent results.
"The beauty of dyeing is in the experimentation—don't hesitate to mix, adjust, and modify until you find that sweet spot that resonates with your artistic vision!"
When you take the time to test and adjust, you're not just avoiding mishaps; you're actively engaging in the alchemical process of transforming fabric into something uniquely expressive. Understanding these methods empowers you as a dyer, paving the way to unlock the full potential of your cyan dye adventures.
Application Techniques
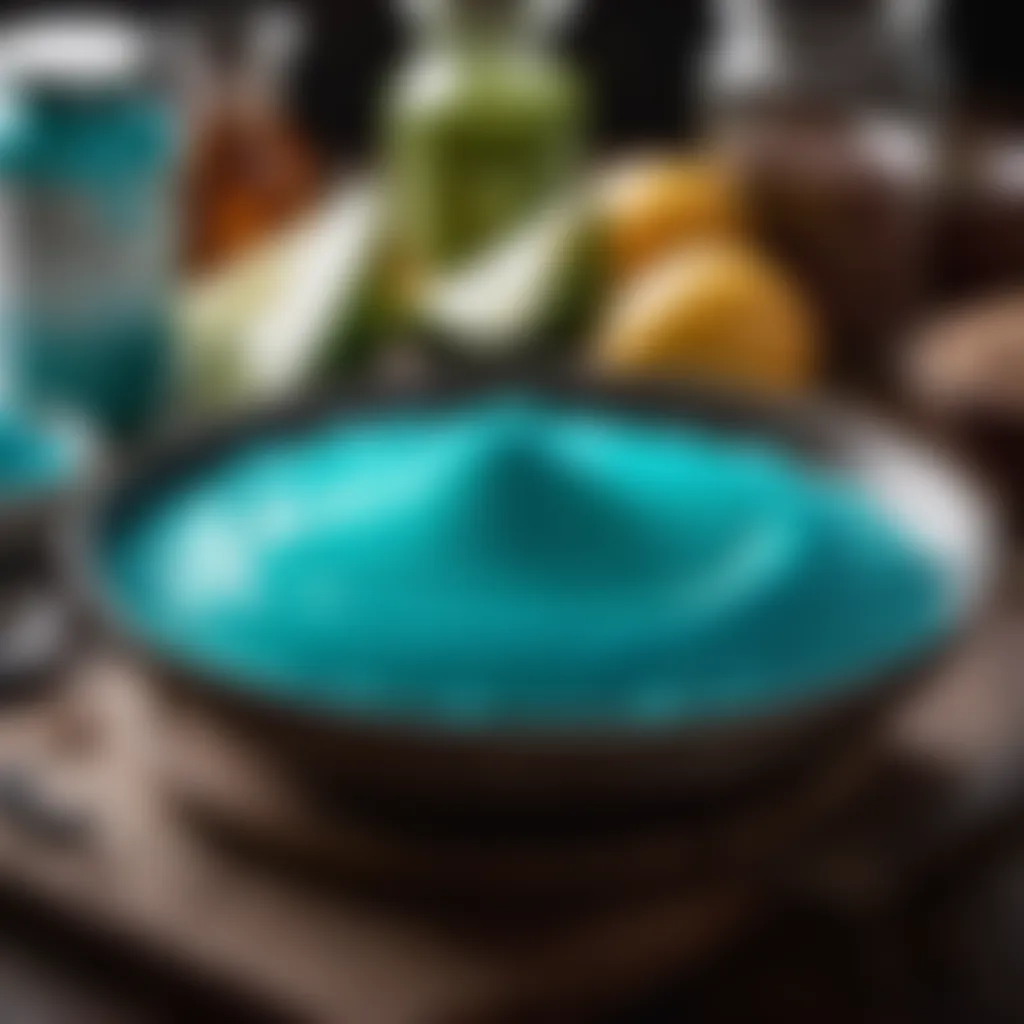
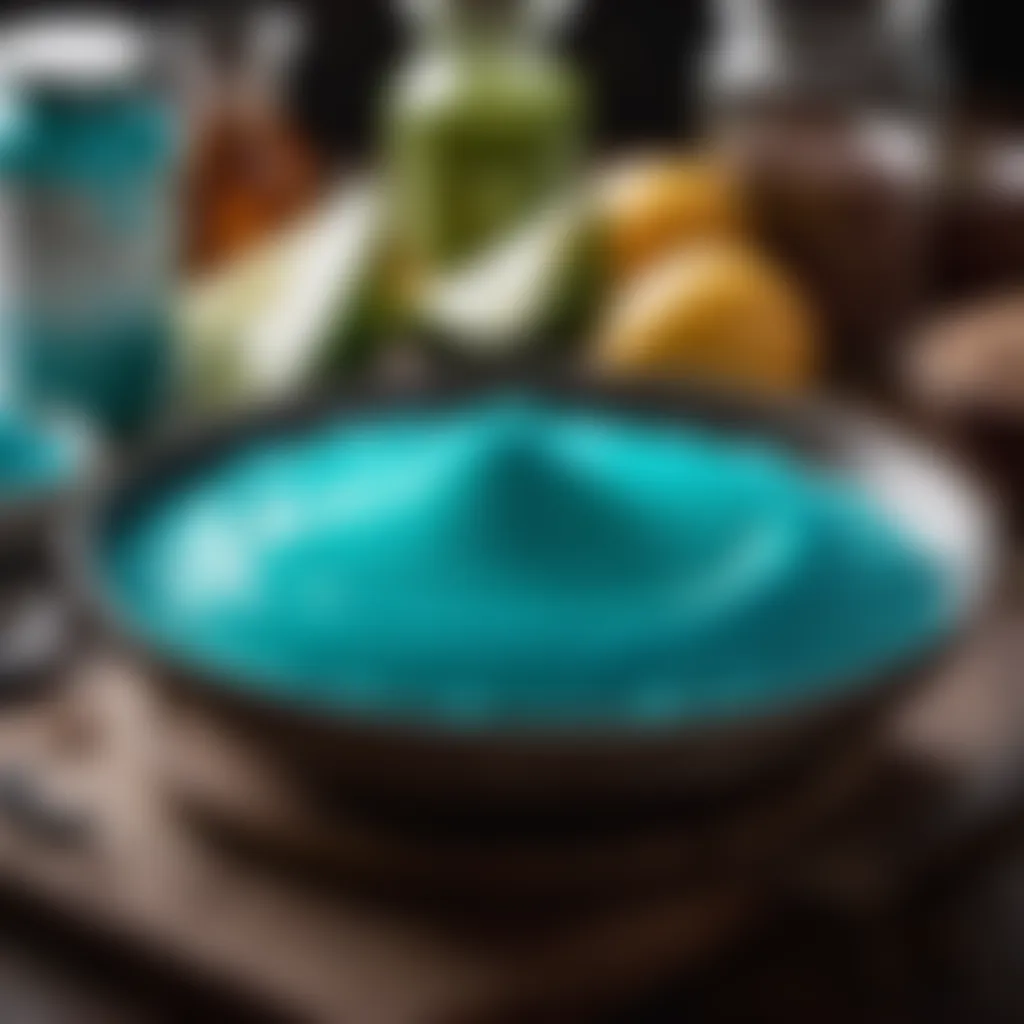
Application techniques are the backbone of successful dyeing processes, acting as the bridge between your elegantly crafted cyan dye and the final, vibrant result on fabric or material. Understanding these methods is crucial, as each technique offers its own unique advantages and challenges that can greatly influence the outcome of your dyeing project. In this section, we will delve into two popular techniques: immersion dyeing and direct application, explore their distinct qualities, and discuss the importance of post-dye treatments to ensure the longevity and brightness of your results.
Recommended Dyeing Methods
Immersion Dyeing
Immersion dyeing is a classic method that involves submerging the entire piece of fabric in a dye bath. This technique allows for an even and consistent application of dye, which is vital when one aims for uniform color saturation. One of the standout characteristics of immersion dyeing is that it tends to produce richer, deeper shades, which is particularly appealing when working with cyan dye. The method is favored, especially in larger batches, making it an excellent choice for creating multiple items at once.
- Key Characteristics: This method requires a larger vessel and a good quantity of dye solution, facilitating a thorough dye process.
- Benefits: Immersion dyeing allows for more predictable color results as the entire fabric interacts with the dye equally. The gradual absorption also enables the fibers to soak up harder-to-dye colors effectively.
- Considerations: On the downside, ensuring an even color may require some agitation and monitoring, which could be time-consuming.
This could be the way to go if you're looking to create striking pieces, as the gradual immersion leads to an even color distribution that leaves fabric evenly dyed from edge to edge.
Direct Application
Direct application, on the other hand, is a more controlled approach. This technique involves applying the dye directly onto the fabric's surface, typically using brushes or spray bottles. The appeal of direct application lies in the ability to create unique patterns and ombre effects with relative ease.
- Key Characteristics: This method is more versatile for those experimenting with designs, as you can easily manipulate where and how much dye is applied.
- Benefits: With direct application, one can achieve intricate designs or soft transitions between colors. It is a perfect method when creating artistic and tailored pieces, giving the dyer significant creative control.
- Drawbacks: However, one must be cautious, as uneven application can lead to patchiness or unpredictable results, especially if one isn’t careful with measuring the quantities.
Direct application offers friendliness in terms of design possibilities but requires a practiced hand to ensure that the end result is as intended.
Post-Dye Treatment for Best Results
After applying dye, proper post-dye treatment is essential for setting the color and ensuring durability.
Here are some common steps to consider:
- Washing: Gently wash the dyed fabric using cold water and a mild detergent. This helps remove any excess dye still clinging to the surface.
- Fixative: Consider using a dye fixative to enhance colorfastness, especially for lighter fabrics. This step can help prevent colors from running in the wash.
- Drying: Air drying is often preferred to ensure that the fabric retains its shape and colors. Avoid direct sunlight during this phase to prevent fading.
Proper post-dye treatment preserves the vibrant colors and extends the life of your dyed fabrics—don't skip this step!
Overall, mastering these application techniques will enable you to lean into your creativity with the cyan dye creation process. Whether you prefer the thorough approach of immersion dyeing or enjoy the artistic freedom of direct application, each method contributes profoundly to crafting a strikingly appealing outcome.
Troubleshooting Dye Issues
When embarking on the journey of creating your own cyan dye, not everything goes according to plan. No matter how experienced you might be, encountering issues during the dyeing process is a given. Troubleshooting dye issues forms a critical part of ensuring that your dyeing adventure ends on a high note. If the colors don’t quite match what you envisioned or if you run into unexpected results, knowing how to address these troubles can make all the difference.
Understanding potential problems before they arise is essential. It allows you to prepare for any hiccups down the line while providing a sense of reassurance. This section aims to equip you with the know-how to address these common challenges effectively, ensuring that your fabric turns out just as you imagined.
Identifying Common Problems
During dyeing, one might face various setbacks that can ruin the final product if not fixed promptly. Here are a few common problems you may encounter:
- Uneven Color Distribution: One of the most notable issues is the dye appearing unevenly across the fabric. Different fabric types absorb dye differently, which can lead to spots or streaks.
- Faded or Dull Colors: After dyeing, your vibrant cyan may turn out to be more muted than expected. This fading can stem from inadequate dye concentration or improper fixation methods.
- Bleeding: If the color runs when your dyed fabric is rinsed or when it's washed later, it indicates poor dye adhesion.
- Incomplete Dyeing: Sometimes, sections of the fabric may remain undyed or lighter than you intended. This can happen if the fabric wasn't thoroughly submerged or if the dye solution was too weak.
"A stitch in time saves nine." It's beneficial to address these issues as soon as they appear, rather than waiting for a more convenient moment.
Recognizing these problems as soon as they arise can save you from greater frustration. Further identifying the root causes will guide you to appropriate solutions.
Solutions and Adjustments
Once you've spotted the issues, it’s time to take action. Here are some strategies that can help you resolve dyeing problems:
- For Uneven Color Distribution: To combat this, ensure even stirring while mixing the dye and completely submerge the fabric in the dye bath. Adjusting the fabric’s position occasionally during the dyeing process can also help.
- For Faded or Dull Colors: If your colors aren't as lively as you'd like, consider increasing the dye concentration. You can also experiment with the fixation process, using more effective mordants that help bond the dye to the fabric.
- Tackling Bleeding Colors: To prevent bleeding, thorough rinsing after dyeing is essential. Adding a fixative to the rinse water can further ensure that colors stay put.
- Addressing Incomplete Dyeing: If certain areas remain undyed, ensure the fabric is fully immersed in the dye solution for enough time. Examining the amount of dye solution can also help ensure it’s sufficient for the fabric's size.
Being proactive and having the right adjustment techniques in your toolkit can steer you clear of the more troublesome outcomes. With these tips at your disposal, you won’t just troubleshoot your dyeing it can also enhance your dyeing technique over time.
Cleaning Up After Dyeing
Cleaning up after dyeing might not be the most thrilling part of the whole process, but it’s absolutely an essential step that shouldn’t be overlooked. Think of it like washing dishes after a great meal; it's not glamorous, but it's vital for keeping everything in order. Proper cleanup ensures your workspace remains safe and functional, while also preventing any unwanted chemical reactions or stains.
In dyeing, especially with something as bold as cyan, messes can happen quicker than you might expect. Spills and residue from dyes can linger and cause issues later on if not tended to correctly. Besides just aesthetics, some dyes can be toxic or harmful to the environment. So, this is where knowing how to clean up properly really shines.
"A clean workspace is a happy workspace—where creativity can thrive and safety is a priority."
Proper Disposal of Dye Materials
When dealing with dye materials, disposal is key. It's not just about tossing things in the trash; it's about being mindful of the materials you used. Many dye substances can have adverse effects on the environment if not disposed of correctly. Here’s a quick guide to get you started:
- Check Local Guidelines: Always refer to your local waste disposal regulations. Some places have specific instructions on how to dispose of hazardous materials like dyes.
- Avoid Pouring Down the Drain: Unless you’re absolutely certain that your dye is safe and biodegradable, avoid pouring it down the sink. This can lead to plumbing issues and environmental harm.
- Use a Sealed Container: For any leftover dye solution or chemical products, store them in a tightly sealed container. Label it clearly to avoid confusion in the future.
- Consider Recycling: If the materials are recyclable and clean, check with local recycling programs to see if they accept those types.
By taking precautions and genuinely considering where your dye goes after use, you’re contributing to a cleaner and safer environment.
Cleaning Equipment and Workspace
Now that the dye materials are disposed of correctly, it’s time to focus on cleaning your tools and workspace. Having a clean space sets the stage for your next dyeing adventure:
- Rinse Immediately: After finishing with your dyes, rinse your equipment promptly. This will prevent materials from drying and sticking, which can create a headache later.
- Use Hot Soapy Water: A mixture of hot water and dish soap can do wonders. Scrub the tools thoroughly, paying close attention to any nooks and crannies where dye may be hiding.
- Don’t Forget Surfaces: Wipe down all surfaces where dye might have splattered. A damp cloth soaked in soapy water works wonders here.
- Dry Everything Well: Make sure all equipment is thoroughly dried after washing. This reduces any risk of rust or residue, making it ready for your next dyeing project.
Maintaining your workspace in tip-top shape doesn’t just keep everything tidy; it also preserves your tools, allowing them to last longer and perform better. A little time spent cleaning can save a ton of trouble down the road.
Exploring Advanced Techniques
Exploring advanced techniques in cyan dyeing is not just a path to creativity but also a way to achieve customized results that stand out. This section dives into the methods of achieving varied shades and combining dyes, each adding to the richness of the dyeing experience. Understanding these advanced techniques can elevate a simple dyeing project into a compelling artistic statement.
Creating Varied Shades of Cyan
When you're working with cyan dye, the process doesn’t have to end with a single shade. By tweaking the concentrations of your dye solution or manipulating the soaking time, you can achieve a spectrum of hues ranging from soft sky blues to deep teal. This control allows for creativity; for instance, if you desire a lighter pastel shade, simply dilute the dye further with water before soaking your fabric.
One effective method to achieve various shades is by following a straightforward recipe adjustment:
- Lighter Shades: Mix one part cyan dye with two parts water and soak the fabric for a shorter duration, perhaps only 10 minutes.
- Darker Shades: Work with a higher concentration, like two parts dye to one part water, and let the fabric soak for as long as 30 minutes or until the desired color sets in.
Moreover, the fabric itself can play a role in how the dye settles. Natural fibers like cotton absorb dye differently than synthetic fibers, which might lead you to experiment with various materials for your next project. Each fabric type has its quirks, prompting you to adjust your approach accordingly.
"Experimentation is the mother of creativity. Try different approaches and adjust based on results."
Combining Dyes for Unique Effects
The magic of dyeing also lies in the possibility of combining cyan with other colorants to produce unique effects. Layering or mixing dyes can lead to extraordinary results that catch the eye. For instance, mixing cyan with a splash of yellow could yield stunning green tones, while pairing it with magenta might result in richly dynamic purples.
Here are some tips for combining dyes effectively:
- Start Small: Always test on a scrap piece before committing to a project. This ensures that the mixed colors yield the desired result.
- Focus on Ratios: Experiment with the ratio of your cyan dye to the second dye. Sometimes, just a hint of another color can bring an exciting twist.
- Create Patterns: Use techniques like tie-dyeing or ombre to create an interesting visual effect with combined dyes. This not only adds depth to your work but also personalizes each piece in a way that factory-made items simply cannot match.
By understanding the chemistry behind these techniques and the interaction between different dyes, you can unlock a whole new world of possibilities in your fabric art. Whether it's a family project or a venture into small business, exploring these advanced methods could truly enrich your results.
Cyan Dye in Art and Fabrication
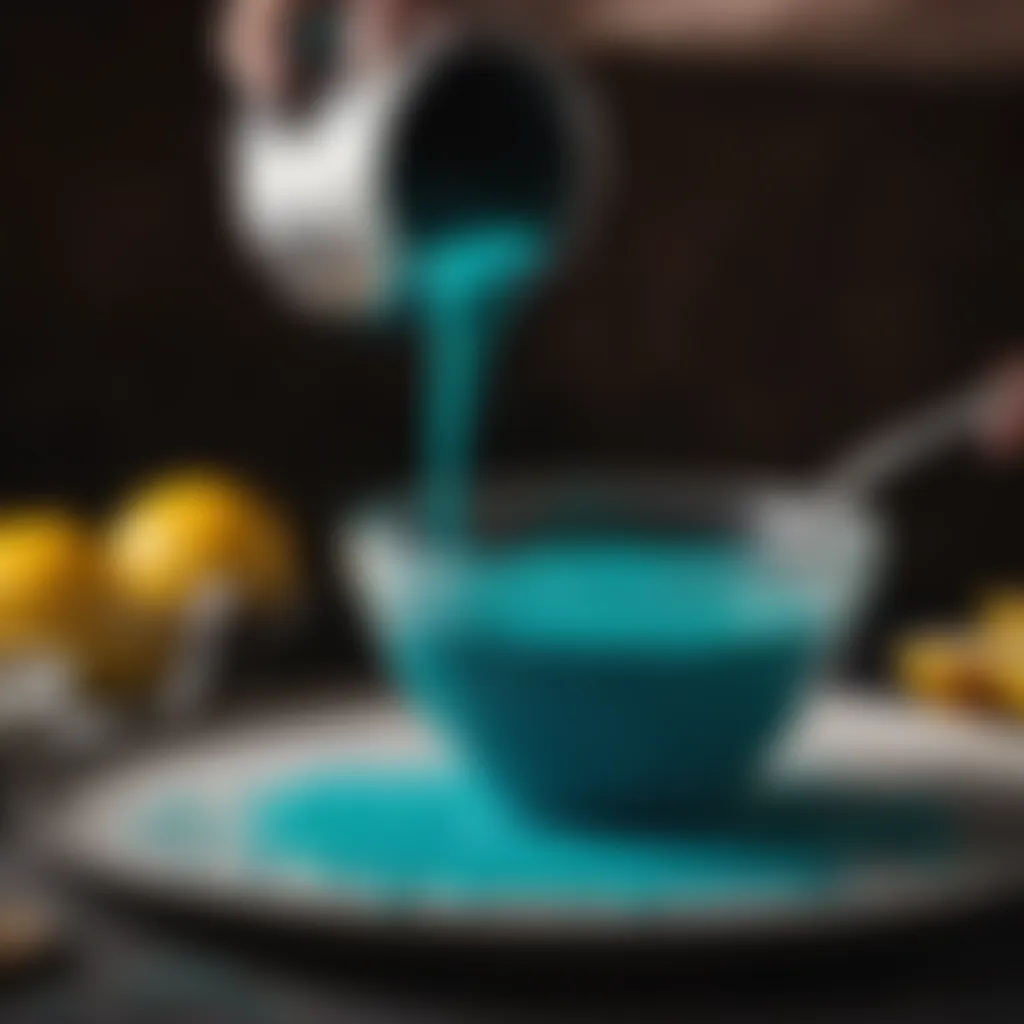
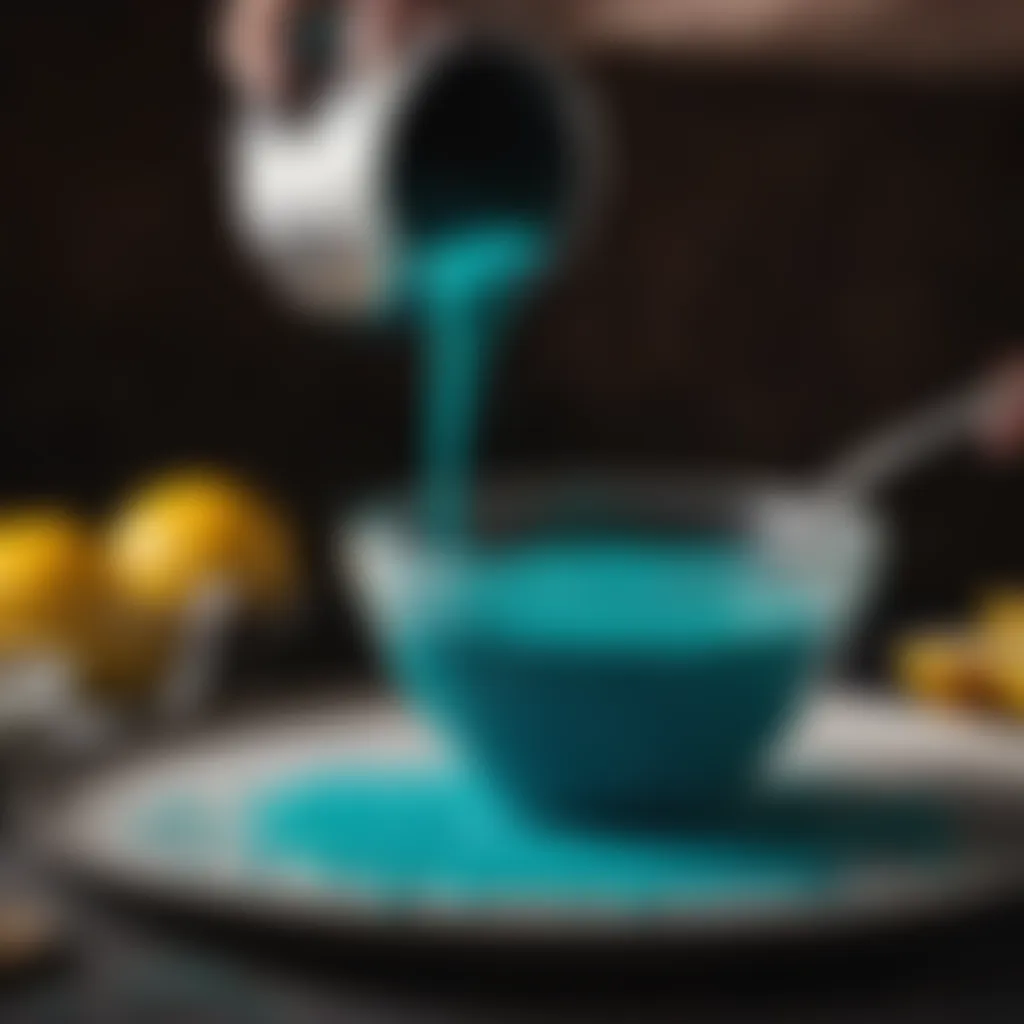
Cyan dye plays a significant role in the world of art and fabrication, offering unique aesthetic and functional benefits. When creative minds venture into dyeing fabrics, they often discover that the interplay of colors can spark inspiration, turning ordinary materials into stunning visual statements. Cyan, in particular, has a knack for catching the eye and can evoke emotions ranging from tranquility to freshness. By harnessing the vibrant nature of this color, artisans are able to express their individuality and creativity.
One of the appealing attributes of cyan dye is its versatility across various mediums. Whether it's fabric, paper, or materials for crafts, cyan serves as a perfect base or highlight for designs. This dye can create vivid contrasts or seamless blends, depending on the artist’s intention. It’s like having a chameleon at one’s disposal; it adapts to different styles and projects beautifully. In textile artistry, incorporating cyan can elevate the entire piece, drawing viewers in with its captivating depth.
"Cyan can transform mundane materials into conversation starters, reflecting the personality and taste of the creator."
Role in Textile Artistry
In the realm of textile artistry, cyan dye occupies a prime seat, breathing life into fabrics used in garments, home décor, and more. Artists often find that using cyan can communicate specific themes or feelings in their work. For instance, when utilized in a light shade, cyan evokes serenity, while darker tones can usher in a more intense emotional landscape.
Furthermore, the application methods influence the final effect. Techniques like tie-dye or gradient dyeing can further enhance the beauty of cyan. Many artists may choose to layer cyan over other colors, achieving intricate patterns that suggest depth and movement. When approaching fabric dyeing, it’s imperative to consider how the chosen methods can influence the final appearance.
Some joyous factors that come with using cyan dye in textile work include:
- Ease of Mixing: Cyan blends well with various colors, making it an ideal choice for creating ombre effects.
- Visual Impact: It can stand out boldly or complement an entire scheme with subtlety.
- Experimentation Friendly: This dye encourages artists to experiment without fear, as its vibrancy usually yields stunning results.
Cyan Dye in Crafting Projects
The crafting world is a playground for creativity, and cyan dye fits right in. From card-making to home accessories, the potential applications are vast. Using cyan in crafting not only catches the eye but can also elicit joy in the process of creation. One of the significant benefits of using cyan for crafting is its accessibility. Many crafters can create their own cyan dyes from natural materials, allowing a personal touch to their projects.
Here are some crafting ideas where cyan dye can take center stage:
- Hand-dyed Paper: Crafting greeting cards or invitations using cyan-dyed paper can add a unique flair.
- DIY Home Décor: Creating cushion covers or wall hangings with cyan accents can enliven any space.
- Personalized Gifts: Gift wraps and tags dyed in attractive shades of cyan can make presents stand out.
When engaging in these crafting projects, it’s beneficial to remember a few tips:
- Always test dye on a small swatch to determine how the final shade will appear.
- Think about combining cyan with other colors to extend the color palette and personalize the outcome.
- Don’t shy away from using fabric and paper with textures, as they can capture the dye in fascinating ways.
In summary, cyan dye serves as an enabling force in the artistic and crafting worlds. It inspires creativity, fosters self-expression and can elevate projects from the ordinary to the remarkable. Embracing it in both textile artistry and various crafting ventures not only enriches the visual landscape but also offers a rewarding hands-on experience.
Sustainability Considerations
Sustainability considerations play a pivotal role in the realm of dye production, particularly cyan dye, where the intersection of artistry and environmental consciousness becomes essential. With rising awareness of environmental issues, many individuals are reevaluating their crafting practices to minimize detrimental effects. This article will delve into the vital aspects of sustainability relevant to cyan dye creation, shining a light on how thoughtful choices can lead to positive outcomes for both creators and the planet.
Environmental Impact of Dye Production
The environmental imprint left by dye production is significant yet often overshadowed by the allure of vibrant colors. Traditional dyeing processes frequently involve toxic chemicals that not only pose health risks to those handling them but also seep into waterways, endangering aquatic life. The production of synthetic dyes, widely used in many industries, raises serious concerns about waste and pollution.
In a world increasingly affected by climate change, considering the environmental impact is vital. For instance, the runoff from dye factories can contain heavy metals and toxic substances that contaminate local ecosystems. As a result, careful management and eco-friendly practices are paramount. To mitigate harmful effects, consider these points:
- Wastewater Management: Implementing proper filtration systems can drastically reduce pollutants.
- Energy Consumption: Opting for methods requiring less energy contributes to lower carbon emissions.
- Regulatory Compliance: Abiding by local environmental regulations ensures that production aligns with sustainability goals.
Sustainable dye production not only benefits the environment but enhances the reputation of artisans and industries committed to conscientious practices.
Choosing Eco-Friendly Alternatives
When it comes to crafting dye, selecting eco-friendly alternatives can be both rewarding and beneficial. With myriad options available today, it’s easier than ever to create stunning colors without compromising our ecosystems.
Consider these viable alternatives for a more sustainable approach to cyan dye production:
- Natural Dyes: Derived from plant sources or minerals, these dyes are less harmful and often biodegradable. They can yield beautiful shades of cyan and offer unique characteristics that synthetic options may lack.
- Low-Impact Dyes: Many manufacturers now produce dyes specifically marked as low-impact, which cause less harm during the dyeing process, making them ideal for conscientious crafters.
By utilizing eco-friendly materials and methods, the dyeing community can push back against the environmental consequences associated with traditional dye practices. It’s all about making informed decisions that harmonize creativity with ecological responsibility.
"Sustainability is no longer a niche market; it is a necessity that artists can embrace to create a better future for our planet."
Taking sustainability into account is not simply an obligation; it’s an opportunity. Through mindful choices and understanding the implications of our craft, we can infuse meaningful change into our projects while producing vibrant cyan hues.
Cyan Dye in Industry
Cyan dye plays a crucial role in various industrial applications, far beyond the confines of artistic endeavors. Its significance stretches across sectors like textiles, printing, and even food production. Understanding the specific elements and benefits of cyan dye in industry helps illuminate its larger impact and underscores the necessity of good practices and innovations in its application.
Applications in Various Sectors
- Textile Industry: One of the most prominent sectors utilizing cyan dye is textiles. From fashion to home decor, cyan serves as a vibrant choice for materials ranging from cotton to synthetic fabrics. The ability of cyan to blend well with other colors is a key reason for its popularity. It offers an exciting array of shades, bringing life to apparel and furnishings alike.
- Printing: Cyan is a fundamental color in color printing, particularly in digital and lithographic processes. It’s often part of the CMYK color model, allowing designers to achieve high-quality prints while maintaining color accuracy. This is especially important in marketing materials where brand colors must be consistent.
- Food Industry: Interestingly, cyan dye finds its niche in food applications, especially as an artificial coloring agent. While its usage is regulated, certain products, like candies and beverages, may include cyan shades to enhance visual appeal. Here, understanding the safety protocols becomes vital for consumer health.
- Art Materials: In the world of art and craft supplies, cyan dye is heavily favored for its intense hue. Artists use it in fabric paints, inks, and marker formulations. Its versatility allows for a great range of creativity in artwork, thus appealing to both hobbyists and professionals.
"Cyan is one of those versatile colors - it’s everything from tranquil to vibrant, depending on how it’s used. Its applications are only limited by the imagination."
Market Trends and Innovations
As industries evolve, so too does the market for cyan dye. A few trends worth noting include:
- Sustainability Initiatives: There is growing pressure on industries to adopt sustainable practices. Innovations in eco-friendly cyan dyes—such as those derived from natural sources—are emerging as alternatives that reduce environmental footprints.
- Technological Advances: From improved dyeing techniques to the integration of digital technologies in design applications, manufacturers are continually finding ways to enhance the efficiency and quality of cyan dye production. These advancements result in reduced waste and lower costs, making cyan dye more accessible.
- Custom Blends: The demand for customization has sparked a trend in creating tailored cyan dyes that can meet specific requirements. This is increasingly important for brands aiming to stand out in a saturated market.
- Regulatory Changes: Continual scrutiny over the safety of synthetic dyes, including cyan, is pushing for more stringent regulations. Manufacturers are adapting by reformulating products, ensuring compliance while still meeting customer demands.
Future Directions in Dye Technology
The field of dye technology is evolving at a rapid pace, and understanding the future directions in this domain is vital for enthusiasts and professionals alike. The innovations enhance not only the effectiveness of dyes but also address critical matters like sustainability and safety in the dyeing process. In a world increasingly focused on ecological impacts, advancements in dye technology present an excellent chance to innovate while being mindful of our planet. The key areas of focus will include:
- Accessibility to safer dyes
- Development of biodegradable colorants
- Improvements in efficiency and procedural simplicity
Emerging Colorants and Innovations
As we look at the horizon, one can't help but notice the trailblazing pathways taken by emerging colorants and innovations. Various industries are tapping into the potential of natural dyes, derived from fruits, vegetables, and even waste materials. These organic alternatives not only offer a palette of unique hues but also present fewer health risks compared to synthetic counterparts. For instance, indigo dye, traditionally used for centuries, is back in the spotlight with a modern twist.
Furthermore, brands are now diving into the use of technologies like nanotechnology and biotechnology. These methods may lead to the creation of more vibrant, long-lasting dyes that are safe for both fabric and skin. Think about biomimetic colorants, which mimic natural processes in the environment. Their development may redefine the sustainability narrative within dye production.
"The colors we use are reflections of our innovation, but it’s also about understanding our responsibility toward the environment."
Research and Development Trends
The landscape of research and development in dye technology is ripe with possibilities. One key trend is the focus on dyeing processes that minimize water use. Conventional dyeing often calls for copious amounts of water, often leading to wastage. Emerging methods like digital printing or waterless dyeing are gaining traction. These techniques are designed not just to conserve resources but also to cut costs.
Moreover, research is steering towards recyclable materials that can be dyed multiple times with minimal environmental impact. Scientists are exploring new binding agents that may reduce the amount of dye needed while enhancing fixation to the fabric. This balance is critical for maintaining the vibrancy of color while countering any adverse side effects on nature.
As a result, the future of dye technology looks promising, filled with exciting avenues for creativity and sustainability. For anyone passionate about dye-making, embracing these trends can mean more than just producing beautiful colors; it’s about making informed choices that resonate with a greener future.
Ending and Final Thoughts
In the journey of creating cyan dye, it’s essential to wrap up not just the process, but also the rich tapestry of experiences that come with it. At its core, the development of a cyan dye recipe is not merely a methodical task; it celebrates creativity and a deeper understanding of the science behind colors. This article has showcased the significant stages— from gathering materials to the application techniques that breathe life into fabrics.
With each step, you’ve also learned about the importance of safety and precision in handling chemicals, a crucial aspect that cannot be overstated. Delving into the world of cyan dye offers not just aesthetic satisfaction but also a substantial appreciation for the intersection of art and chemistry. Designer shades and vibrant projects await those who dare to embrace the complexities involved.
This exploration encourages artisans, be it in a professional or hobbyist capacity, to consider every detail. You don't just walk away with skills to dye— you step into a community of creators and innovators who cherish the subtleties that colors bring to life.
Recap of Key Points
- The significance of cyan dye spans historical and contemporary realms, enhancing fabrics and art.
- Understanding the chemistry behind dyeing unveils the complexities of color creation.
- Essential materials and tools set the foundation for successful applications.
- Safety precautions train you not just to craft, but to do so smartly and securely.
- Testing methodologies ensure quality results, giving confidence as you display or sell your dyed creations.
- Exploring advanced techniques fosters ongoing learning, fueling creativity and innovation.
Encouragement for Experimentation
The world of dyeing is expansive, waiting to be explored. There’s a joy in mixing, adjusting, and tweaking your cyan dye to achieve that perfect hue. Don’t shy away from deviating from the recipe! Whether it be experimenting with dilution ratios or trying out new binding methods, every trial could lead to unexpected delights.
Consider incorporating other colors to see how cyan interacts and shifts— you might just stumble upon an eye-catching explosion of shades. Besides, experimenting is what sets apart a standard project from a breathtaking masterpiece. Every mistake carries a lesson worth learning, so embrace them wholeheartedly. After all, the real beauty lies not merely in the outcome, but in the adventure of creation itself.
Remember, you are embarking on this creative journey not just to decorate your fabric, but to express yourself fully. The colors of the world await your unique touch.