Strategies for Effective Clean Room Organization
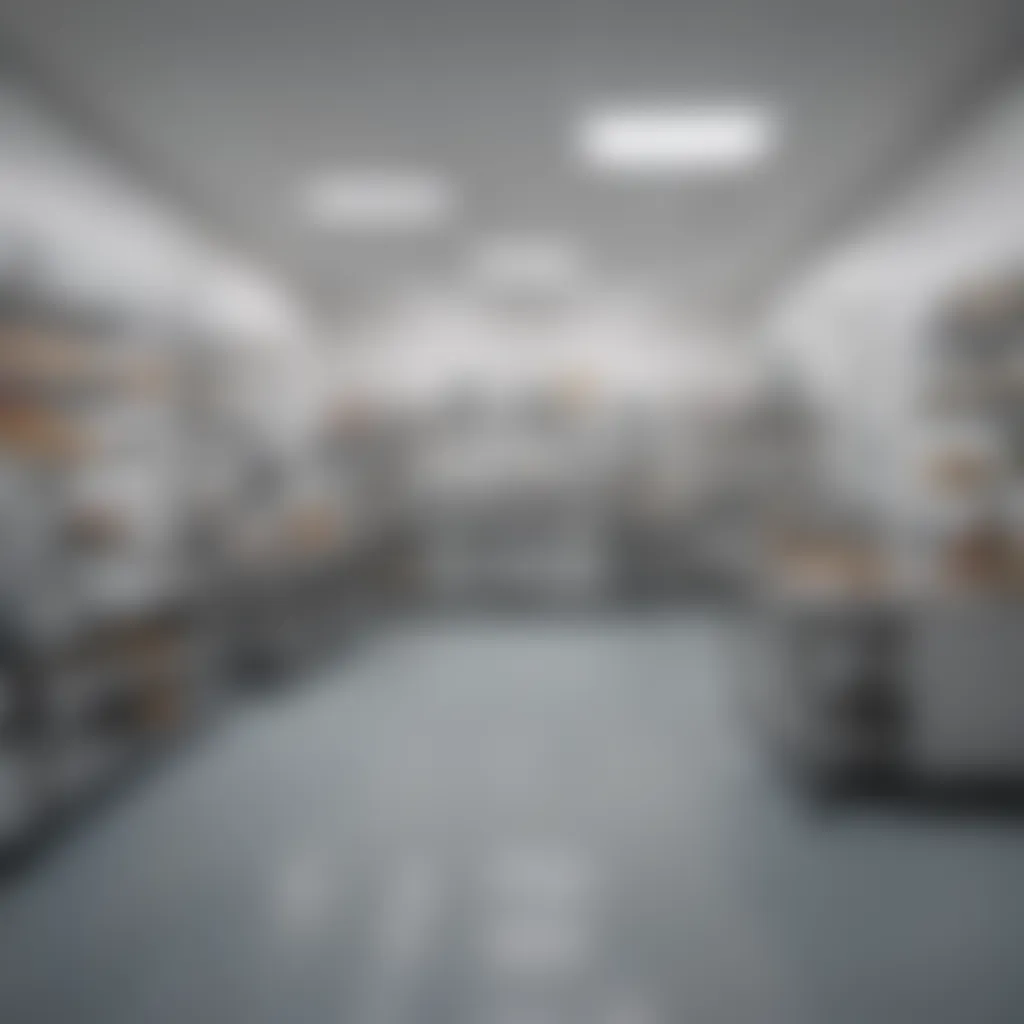
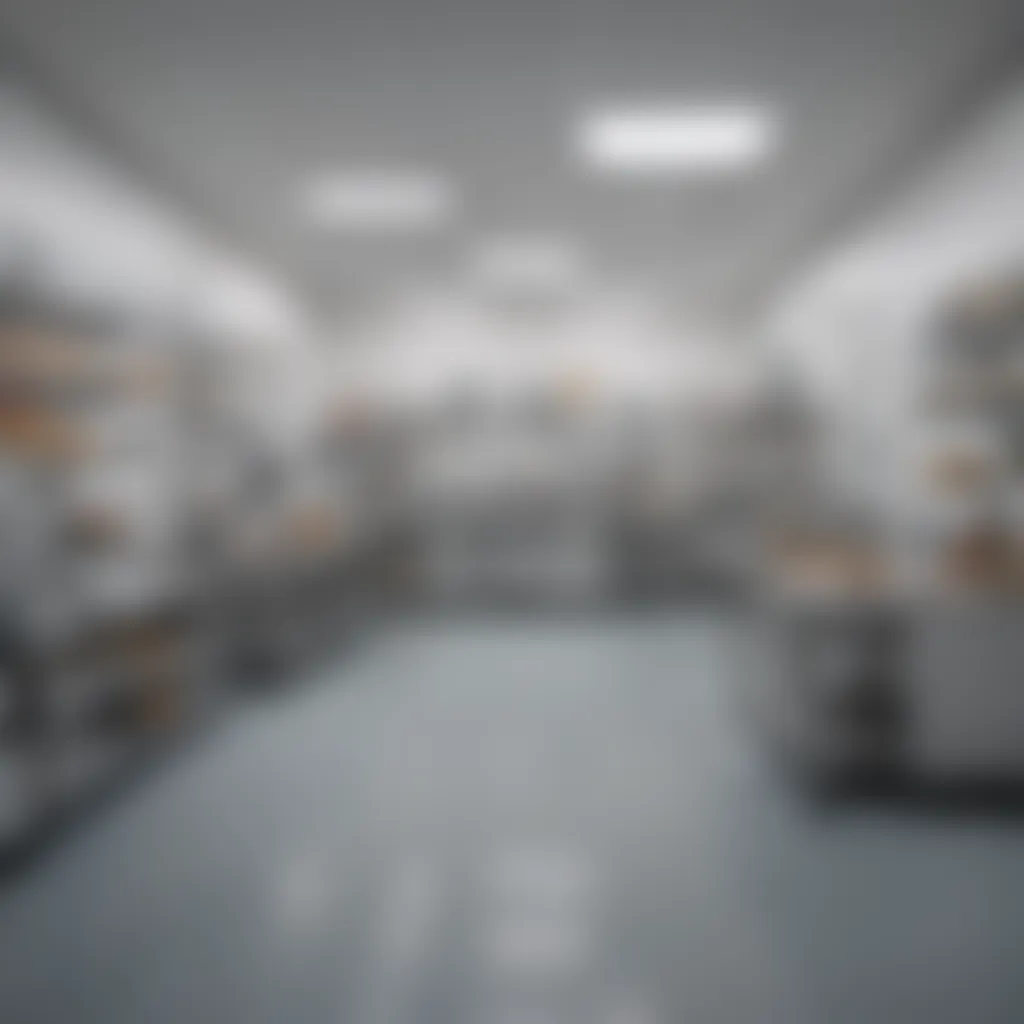
Intro
Maintaining an organized clean room is crucial for many sectors, including pharmaceuticals, biotechnology, and electronics. An effective clean room prevents contamination and assures that sensitive processes can proceed without interruption. A structured approach to organization ensures operational efficiency and compliance with established protocols. This article dissects the strategies for effective cleanup room management, combining theoretical insights with practical applications to foster a sterile environment.
Ingredients:
Here are the fundamental components necessary for creating a well-organized clean room:
- Transparent Storage Bins - Clear bins allow for easy identification of contents while minimizing handling. Use a variety of sizes based on needs.
- Labeling System - A comprehensive labeling system helps in quick identification. Utilize durable labels and a clear font.
- Cleaning Supplies - Ensure to stock appropriate cleaning agents, wipes, and tools that are suitable for a clean room.
- Workstation Layout Plans - Maps or diagrams that specify the placement of equipment and storage can significantly enhance organization.
- Personal Protective Equipment (PPE) - Ensure availability of gloves, masks, and gowns to maintain sterility.
- Access Control Systems - These maintain security and limit entry to authorized personnel only.
Preparation Steps:
Detailed Instructions:
- Assess the Space: Evaluate the current layout of the clean room. Identify any areas that require improvement.
- Develop a Plan: Sketch out a new layout considering workflows, space for equipment, and accessibility. Ensure to incorporate zones for different activities if necessary.
- Inventory Check: Catalog all materials and equipment. Determine what is essential and remove unnecessary items.
- Establish a Cleaning Protocol: Draft step-by-step cleaning procedures including frequency and methods for each area of the clean room.
- Set Up Storage Solutions: Assign storage to each item based on frequency of use and relevance. Clear bins should be used for frequently accessed items.
- Implement Labels: All bins and storage areas should be clearly labeled for quick identification. Include information such as contents, date stored, and safety data sheets if applicable.
Technical Aspects:
When organizing a clean room, it's crucial to adhere to certain specifications:
- Temperature Settings: Maintain temperature according to industry standards, typically between 18-22°C (64-72°F).
- Humidity Control: Aim for a humidity level of 30-60%. Use dehumidifiers if necessary.
- Critical Techniques: Implement HEPA filters and UV lights for air quality control. Regularly check these systems for efficiency.
Cooking Process:
Sequential Steps:
- Initial Setup: Ensure PPE is worn before entering the clean room.
- Cleaning: Use appropriate cleaning supplies to wipe down all surfaces prior to organizing.
- Storage Arrangement: Follow your previously mapped layout to organize workstations and storage areas systematically.
- Review Organization: Once everything is in place, perform a walkthrough to ensure everything is as planned. Make adjustments where needed.
- Final Cleaning: After setup and organization, perform another round of cleaning to ensure sterility.
Troubleshooting Tips:
- If areas seem cluttered, review your storage solutions and adapt as necessary.
- For persistent contamination issues, consider increasing the frequency of cleaning cycles.
"A clean room is not only about cleanliness, it's also about precise organization and control over the environment."
Adopting these strategies will not only enhance the efficiency of your clean room but will also extend the longevity of your materials and equipment.
Understanding Clean Room Standards
Understanding clean room standards is essential for maintaining an environment that meets rigorous cleanliness and operational needs. Clean rooms are controlled environments where the presence of pollutants such as dust, airborne microorganisms, and chemical vapors are minimized. Failure to adhere to clean room standards can lead to product contamination, compliance failures, and safety hazards.
In clean room management, standards are integrated processes that guide the operational practices. These standards include proper protocol adherence, cleanliness measurement, and the specifications for equipment and materials used within these environments. An organized clean room not only protects sensitive projects but also enhances efficiency, ensuring the space remains conducive to scientific or industrial processes. The exploration of clean room standards in this article underlines the importance of systematic organization and compliance with industry guidelines.
Definition of Clean Rooms
A clean room can be defined as a controlled environment designed to reduce the introduction, generation, and retention of airborne particles. It is characterized by a specific air cleanliness level, determined by the maximum allowable particle concentration at a defined size. Clean rooms maintain air quality through high-efficiency particulate air (HEPA) filters and a tightly controlled air flow system. This setup ensures that the environment is suitable for activities involving sensitive materials and components.
Types of Clean Rooms
There are several types of clean rooms, categorized based on their cleanliness levels and intended uses.
- ISO 1 to ISO 9 Clean Rooms: The International Organization for Standardization (ISO) classifies clean rooms from ISO 1 (the cleanest) to ISO 9 (the least clean). Each classification defines the maximum allowable particle counts per cubic meter.
- Drug Manufacturing Clean Rooms: These rooms are specifically designed for pharmaceutical production, requiring strict adherence to contamination control standards.
- Electronics Clean Rooms: These facilities support the manufacturing of semiconductor devices and other electronics, where even minimal contamination can be detrimental.
- Biotechnology Clean Rooms: These environments need to meet specific standards for biological safety, often conforming to Good Manufacturing Practices (GMP).
Having a clear understanding of these types helps identify specific practices tailored to the operational requirements of different industries.
Industry-Specific Standards
Different industries adopt specific clean room standards that align with their operational needs. For example:
- Pharmaceuticals: Adhering to Good Manufacturing Practices (GMP) is vital in the pharmaceutical industry to ensure product safety and efficacy.
- Biological Safety: Clean rooms in biological research must comply with biosafety standards, which dictate stringent controls to prevent exposure to biohazards.
- Microelectronics: This industry follows standards set by SEMI, which govern the cleanliness levels necessary for the production of semiconductors and other sensitive electronic components.
Understanding these industry-specific standards enables organizations to ensure compliance, streamline operations, and enhance the quality of their outputs.
The Importance of Clean Room Organization
An organized clean room is not merely a matter of aesthetics or preference. It is a foundational element that heavily impacts product quality, ensures compliance with industry standards, and upholds safety measures. The implications of effective clean room organization extend beyond neatness or order; they directly contribute to operational success in sensitive environments such as laboratories and manufacturing facilities.
Impact on Product Quality
The relationship between clean room organization and product quality is clear. When a clean room is well-organized, it minimizes the risk of contamination and errors. Products intended for sensitive applications, like pharmaceuticals or microelectronics, demand the highest levels of cleanliness. Lack of organization can lead to misplaced materials or tools, resulting in cross-contamination or compromised quality. Each item in the clean space should have a designated place, facilitating easy access and reducing the time spent searching for essential tools. This systematic approach fosters a culture of quality among personnel, emphasizing that every action has an impact.
Compliance and Regulations
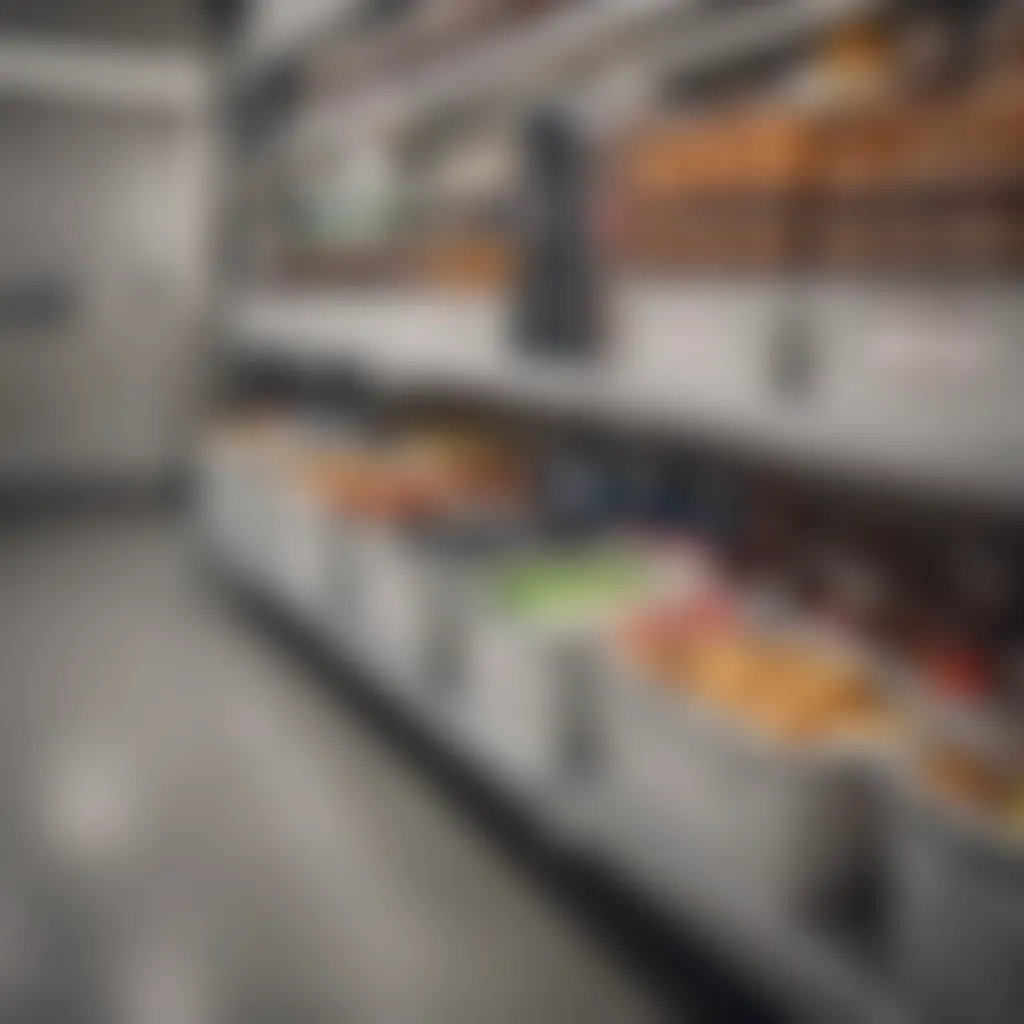
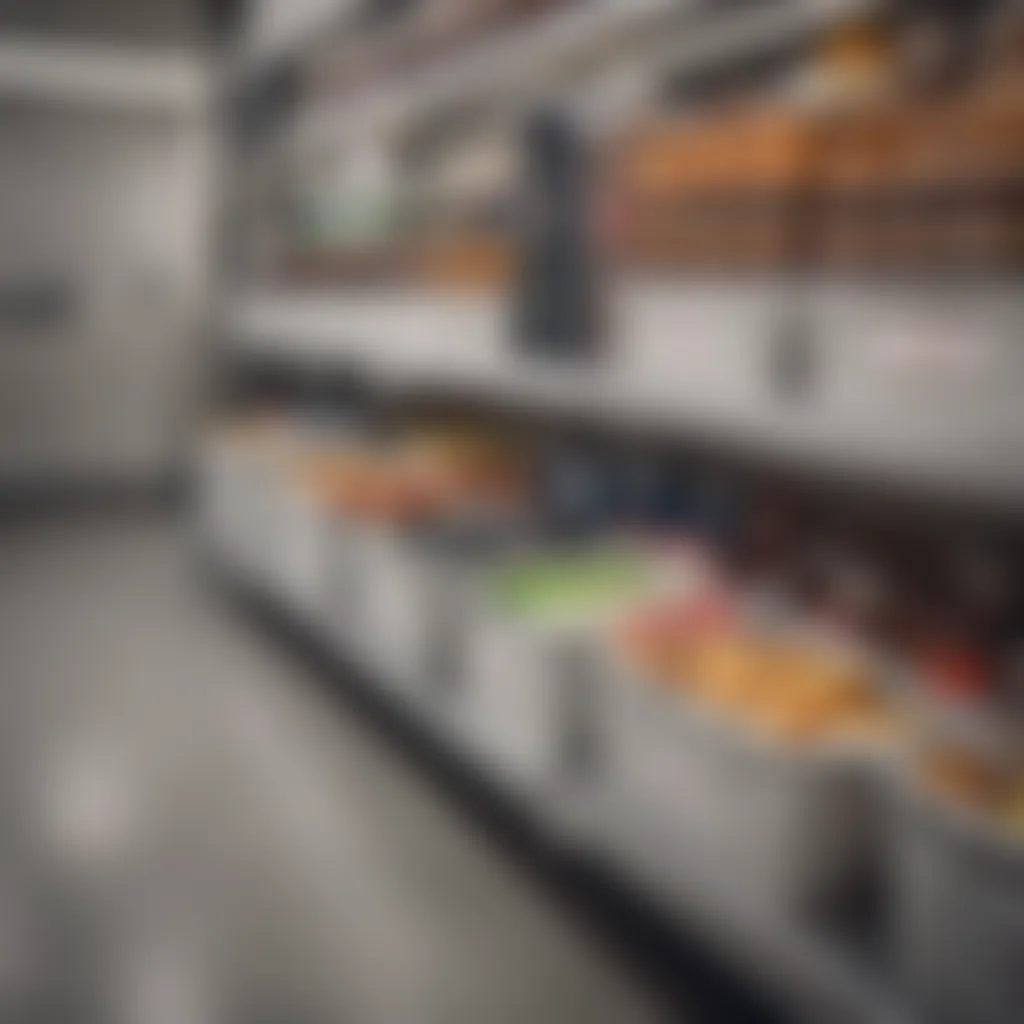
Adherence to compliance and regulations is imperative in settings that require clean rooms. Regulatory bodies like the Food and Drug Administration (FDA) or the International Organization for Standardization (ISO) set strict guidelines for clean room environments. A well-organized clean room shows diligence in meeting these requirements. Documented protocols for organization not only prepare facilities for audits but also establish accountability among staff. Clear organization directly aligns with compliance measures, as it reassures that processes are predictable and traceable, avoiding potential legal challenges due to oversight.
Safety Precautions
Safety in clean rooms cannot be overstated. An organized environment significantly reduces risks associated with accidents and exposure to hazardous materials. Clear pathways and defined areas for specific tasks prevent accidental spills or injuries. It is crucial for personnel to easily navigate the space without distractions. Additionally, proper labeling and storage solutions help safeguard chemicals or delicate equipment important in clean room settings. This proactive approach to organization builds a safety culture, where staff members are more aware of their surroundings and the implications of their actions.
"A clean room is not just a place, but a structured approach to achieve precision in every operation."
The importance of clean room organization resonates through quality assurance, compliance, and safety measures. By fostering a well-organized environment, professionals can enhance overall operational efficacy, ensuring that every task performed operates at the highest standard.
Initial Assessment of the Clean Room
Conducting an initial assessment of the clean room is crucial for understanding its current state and developing an effective organization strategy. This evaluation serves as the foundation for optimizing clean room operations. By identifying existing strengths and areas for improvement, a well-structured plan can be implemented. Key aspects of this assessment include a thorough inventory of current assets, evaluation of space utilization, and identification of problem areas that may hinder efficiency. Understanding these elements assists in enhancing both compliance and productivity.
Inventory of Current Assets
An inventory of current assets provides a detailed account of all materials, equipment, and resources within the clean room. This includes ensuring every item is accounted for and properly categorized. Consider the following points when conducting the inventory:
- List all equipment and materials: Include everything from specialized machinery to small consumables.
- Verify condition and maintenance: Regular checks on equipment conditions can prevent last-minute failures.
- Categorize items: Group items based on usage frequency or type, which aids in future organization efforts.
- Document locations: Make notes of where items are stored to improve retrieval efficiency.
An accurate inventory also facilitates compliance with clean room standards and regulations. Understanding what is present ensures that all materials meet required specifications and safety guidelines.
Evaluating Space Utilization
Space is often a limiting factor in clean room environments. Evaluating how space is utilized can uncover areas where efficiency can be improved. Observe the following aspects during evaluation:
- Layout analysis: Check if the current layout allows for smooth workflow and movement.
- Accessibility: Ensure that frequently used items are within easy reach.
- Unused space: Identify areas that are underutilized or cluttered; these can be optimized further.
- Compliance with clean room standards: Confirm that aisles and emergency exits are not obstructed, keeping safety protocols in mind. Maximizing space usage not only improves productivity but also supports a clean room's classification by regulatory standards.
Identifying Problem Areas
Identifying problem areas is essential for implementing targeted improvements. Some common issues might include:
- Clutter accumulation: Determine if there is an excessive build-up of items that obstruct workflow.
- Inadequate storage solutions: Assess if the storage systems in use meet the needs of the clean room environment.
- Workflow interruptions: Look for points in the flow where processes are delayed, indicating inefficiencies.
- Compliance failures: Notice if there are items that do not comply with regulations or standards.
"Identifying problem areas is not only about fixing issues but also about preventing future ones." Addressing these problems can help streamline operations and enhance overall organization. By making informed changes, the clean room can become a more effective working environment.
In summary, the initial assessment of the clean room lays the groundwork for a systematic and effective organization strategy. Proper inventory, space utilization evaluation, and identification of problem areas are key steps in fostering an organized and efficient clean room. This approach will improve compliance, productivity, and ultimately, the quality of the work conducted within the clean room.
Developing a Clean Room Organization Plan
Creating a clean room organization plan is a critical step for maintaining the integrity of sterile environments. This plan lays the foundation for effective storage, workflow, and compliance with industry standards. An organized clean room not only enhances productivity but also minimizes the risks of contamination and ensures a safe space for operations. A well-structured organization plan provides a blueprint for everyone to follow, offering clarity and purpose to each task undertaken within the clean room.
Setting Objectives and Goals
When establishing a clean room organization plan, setting clear objectives and goals is essential. These objectives should be specific, measurable, achievable, relevant, and time-bound. For example, a goal could be to reduce contamination incidents by a certain percentage within the next six months. This clarity helps in assessing the effectiveness of the organization strategies over time. Furthermore, involving team members in this goal-setting can foster collaboration and improve adherence to the plan. Consider factors like workflow efficiency and inventory management when defining these objectives.
Creating a Floor Plan
A thoughtfully designed floor plan is vital for showcasing the spatial organization of the clean room. Each zone should be mapped out based on the intended functions, ensuring optimal flow of materials and personnel. For instance, areas for gowning, storage, and workstations should be distinct yet integrated to minimize unnecessary movement. Traditional layouts may not suffice; thus, creative adaptations based on the clean room’s specific needs may be required. This planning not only aids in physical organization but also promotes adherence to cleanliness protocols.
Designating Areas for Specific Tasks
Each area within the clean room should have a designated function to maximize efficiency while minimizing contamination risks. Clear demarcation of zones for specific tasks prevents cross-contamination and organizes workflows effectively. For example, ensure that spaces for preparation, experimentation, and post-experiment cleaning are appropriately situated and labeled. This organization helps staff know where to operate without confusion, saving time and reducing errors. Additionally, visible labels and signs can aid in maintaining clarity around which materials belong in which areas, further enhancing communication about cleanliness protocols.
"A methodical approach to organizing tasks in clean rooms prevents contamination and boosts productivity."
Methodologies for Clean Room Organization
In the realm of clean room management, methodologies serve as foundational pillars guiding the organization and maintenance of these specialized environments. Effective methodologies ensure that clean rooms not only meet stringent health and safety standards but also operate efficiently, minimizing waste and enhancing productivity. By implementing structured approaches, professionals can maintain compliance with regulations, thus safeguarding the integrity of sensitive processes and products.
5S Methodology
The 5S methodology is a critical framework used in clean room organization. It stands for Sort, Set in order, Shine, Standardize, and Sustain. Each of these steps plays a vital role in promoting a systematic approach to organization:
- Sort: This initial step involves the elimination of unnecessary items from the workspace. It is crucial to identify which supplies and tools are essential for the clean room functions. This reduces clutter and allows for easy access to necessary materials.
- Set in order: Once unnecessary items are removed, the next step is arranging all tools and materials in a logical manner. This can involve placing frequently used items in easily accessible locations and ensuring that everything has a designated spot.
- Shine: Regular cleaning and maintenance are essential for clean room environments. This phase emphasizes the need for cleanliness to prevent contamination, which could compromise sensitive operations.
- Standardize: Developing standard operating procedures (SOPs) helps maintain the organization achieved in the previous steps. This includes guidelines on how items should be stored and maintained.
- Sustain: Finally, sustaining these practices is key to long-term success. Regular training and audits can help ensure adherence to the established methods, preserving the clean room's integrity over time.
Implementing the 5S methodology not only optimizes organization but also fosters a culture of discipline among team members. This approach is adaptable and can be tailored to the specific needs of any clean room setting.
Lean Principles in Clean Rooms
Applying lean principles in clean room environments focuses on eliminating waste while maximizing value. In essence, the goal is to streamline processes to reduce unnecessary steps and enhance overall efficiency. Key aspects include:
- Value Stream Mapping: This technique involves analyzing workflows to identify bottlenecks and inefficiencies. By visualizing the entire process, teams can pinpoint areas for improvement.
- Continuous Improvement: Encouraging a culture of continuous improvement means regularly assessing processes and embracing feedback. Small, incremental changes can lead to substantial improvements over time.
- Just-In-Time Inventory: Maintaining a lean inventory system helps reduce storage needs and minimizes the risk of contamination. This method ensures that only the necessary materials are available when required, fostering a more organized clean room.
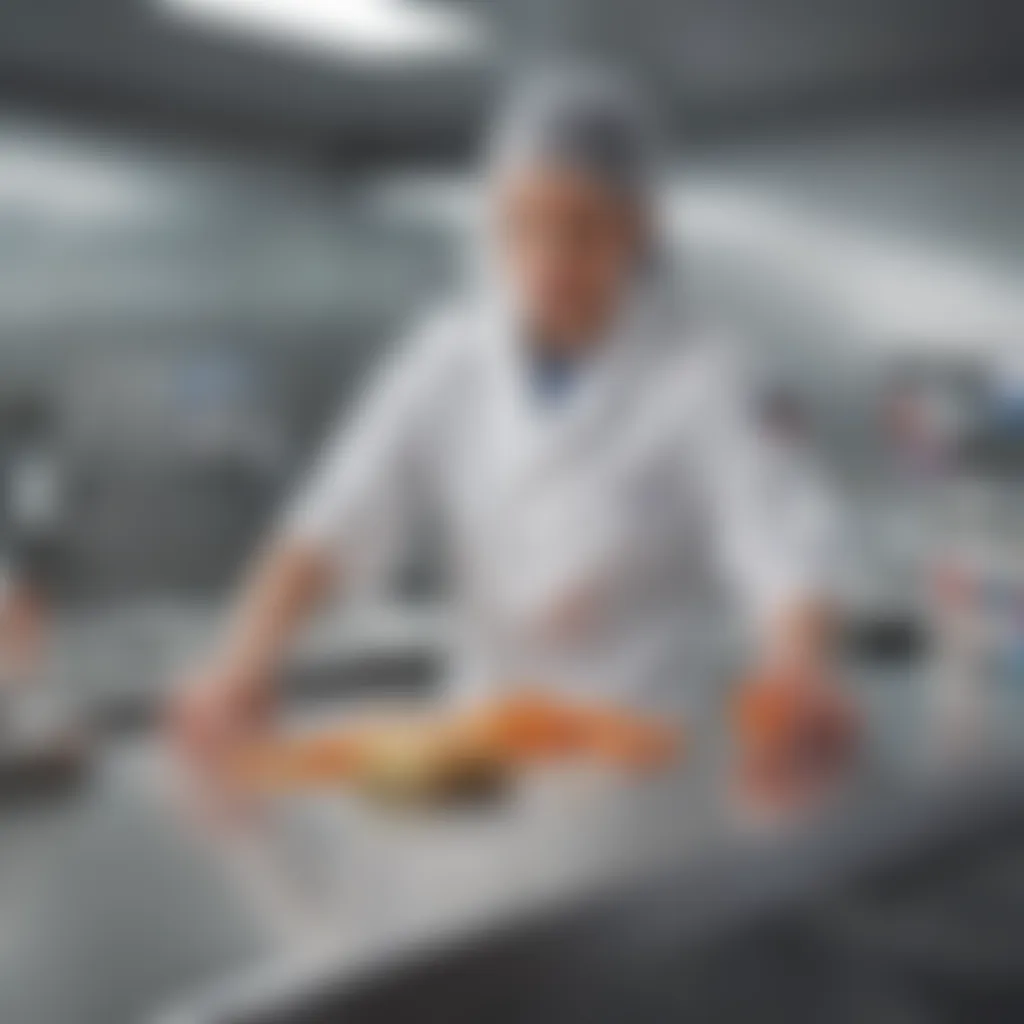
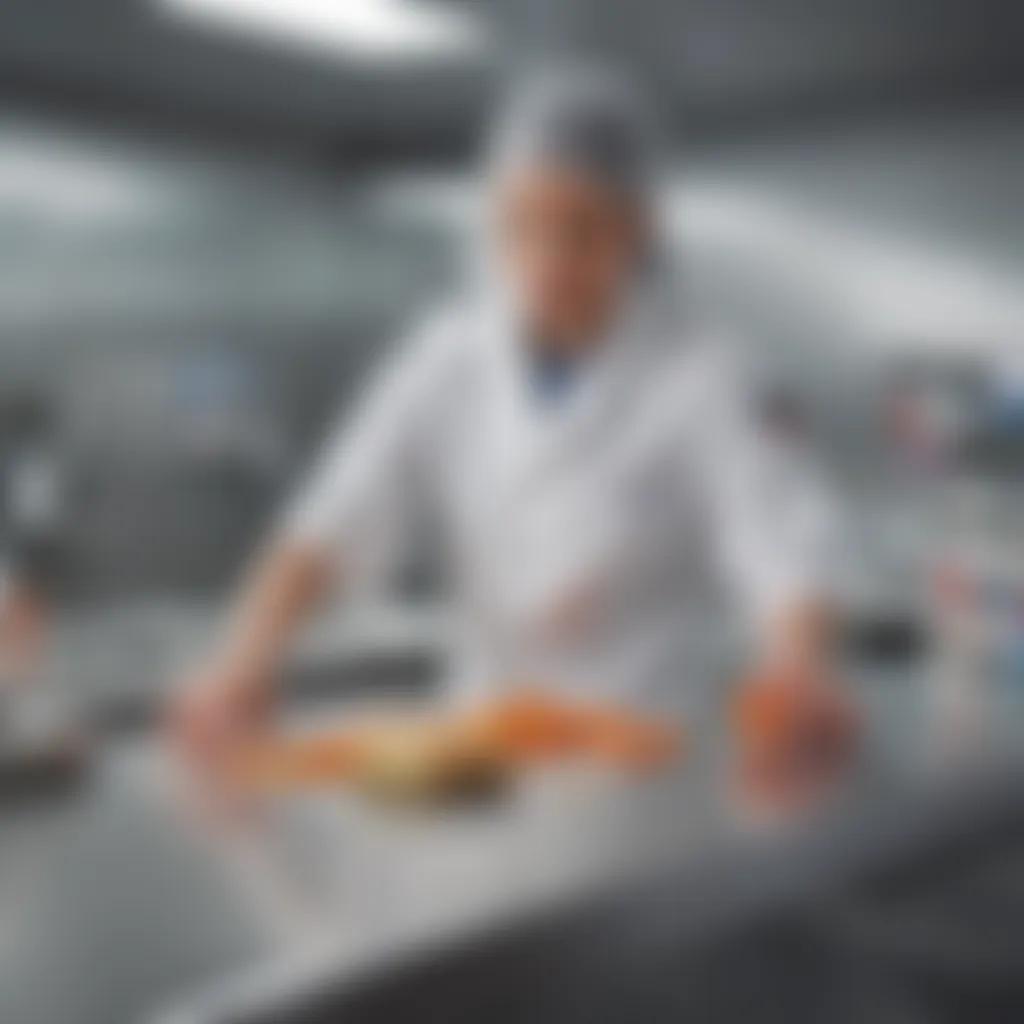
Incorporating lean principles into clean room management not only enhances productivity, but also ensures a safer environment. The emphasis on efficiency naturally aligns with clean room standards, making it easier to uphold crucial industry regulations.
Visual Management Techniques
Visual management techniques are important tools used to enhance clarity and communication in clean room settings. These methods rely on visual cues to convey information quickly and effectively. Notable techniques include:
- Color Coding: Using colors to differentiate between equipment, tools, or materials can help create an organized system. This allows individuals to quickly locate what they need and recognize potential hazards.
- Signage: Clear, informative signs can aid in communication regarding protocols, equipment usage, or restrictions within the clean room. Proper signage reduces confusion and ensures compliance with operational procedures.
- Visual Aids: Charts, diagrams, and flowcharts can serve as helpful references for employees. This visual documentation can guide users through processes and highlight critical control points.
By employing visual management techniques, clean rooms can foster an environment of transparency and accountability. Visual cues reduce reliance on memory, making it easier for team members to adhere to established guidelines.
"Incorporating structured methodologies into clean room organization is not merely a matter of efficiency, but a fundamental requirement for maintaining safety and compliance in sensitive environments."
Storage Solutions for Clean Rooms
The organization in clean rooms is critical for ensuring product integrity and maintaining safety standards. Effective storage solutions are a vital aspect of this process. They help minimize clutter, enable easy access to necessary materials, and maintain a sterile environment. With appropriate storage solutions, clean rooms can operate efficiently, further supporting their specific requirements.
Choosing Appropriate Storage Systems
Selecting the right storage systems is essential in clean rooms. Organizations should evaluate the types of items that need storage and their frequency of use. For instance, elements like modular shelving units can allow flexibility, while drawers can keep smaller items neatly organized. Moreover, storage systems must be resistant to the cleaning agents used in clean rooms.
- Consider the size and weight of the items to determine what type of storage can hold them effectively.
- Keep in mind any industry-specific requirements when choosing materials for your storage systems.
- Evaluate accessibility, as systems should allow staff to quickly obtain materials without disrupting the clean room environment.
Utilizing Vertical Space
Vertical space in clean rooms is often underutilized. Using wall-mounted shelves or racks can maximize storage efficiency. These approaches free up floor space which can help reduce the risk of contamination.
- Install shelves at various heights to accommodate different types of equipment and supplies.
- Consider stackable bins for smaller items, enabling a compact and organized presentation.
- Ensure that all items stored vertically are stable and securely placed to prevent accidents.
Labeling Systems for Clarity
A clear labeling system replaces confusion with understanding. Labels help staff quickly identify items, facilitating access and organization. Well-structured labeling can contribute directly to compliance and efficiency in clean rooms.
- Use color-coded labels to categorize items based on their purpose or contamination level.
- Ensure labels are resistant to chemicals and easy to read, even from a distance.
- Include relevant information on labels, such as expiration dates or specific usage instructions, to prevent misuse of materials.
"An organized storage system is not just about aesthetics; it directly contributes to the efficacy of clean room operations."
Maintaining Clean Room Organization
Maintaining clean room organization is vital for a range of industries, particularly those where stringent cleanliness requirements exist, such as pharmaceuticals, biotechnology, and electronics. The ramifications of neglecting this aspect can be severe, leading not only to compromised product quality but also to potential regulatory infractions. Clean rooms are designed to limit contamination. Thus, maintaining organization within these spaces is as crucial as the initial setup.
Regular checks and protocols create an environment conducive to productivity and safety. One of the main benefits of consistent organization is the reduction of time spent searching for tools or materials. When each item has a designated place, processes become smoother, and workflows more efficient. Furthermore, organizing a clean room regularly helps uphold cleanliness standards, which is critical for compliance with industry regulations.
Regular Maintenance Schedules
Establishing regular maintenance schedules is the backbone of effective clean room organization. These schedules should include daily, weekly, and monthly tasks. Daily tasks might involve wiping down surfaces, checking filters, and ensuring that all cleaning supplies are stocked. Weekly tasks could encompass more thorough cleaning practices, such as equipment checks and calibrations. Monthly evaluations should focus on assessing the overall layout and organization of the clean room to identify any changes that may be necessary to improve efficiency.
Benefits of a maintenance schedule include:
- Consistency: Following a routine ensures that nothing is overlooked.
- Increased Productivity: Workers know what to expect, preventing time wastage.
- Regulatory Compliance: Regular checks help to meet stringent industry standards.
Ongoing Training Programs
Continuous training is essential for all staff members working within the clean room. Regular training helps employees understand the latest cleaning practices, the rationale behind them, and the importance of maintaining organization. Ongoing education ensures that everyone is familiar with protocols and efficient use of storage systems. Staff should be encouraged to ask questions and share insights on improving practices.
Key components of an ongoing training program include:
- Hands-on Sessions: Allowing staff to practice techniques in real scenarios helps reinforce learning.
- Feedback Mechanisms: Encouraging input from employees can lead to better organization strategies.
- Updates on Procedures: Regular updates ensure staff stays informed about best practices and emerging technologies.
Feedback and Continuous Improvement
Establishing a culture of feedback is critical in maintaining clean room organization. Regular evaluations should be conducted to assess both the physical layout and organizational practices. Gathering input from employees highlights areas that may require adjustment and promotes a sense of ownership in the clean room environment.
Feedback can be collected through surveys, meetings, or informal discussions. Using this information, continuous improvement processes can be initiated, directing attention to:
- Problem areas: Identifying issues that hinder organization can lead to strategic changes.
- Emerging Trends: Staying current with evolving practices and technologies enhances efficiency.
- Employee Satisfaction: Listening to staff can yield a more cooperative and committed team.
"Continuous improvement is better than delayed perfection."
To conclude, maintaining clean room organization is not merely about keeping surfaces clean. It involves a comprehensive approach that includes regular maintenance schedules, ongoing training, and an open feedback loop. By implementing these strategies, facilities can uphold stringent standards while fostering an organized, productive workspace.
Role of Technology in Clean Room Organization
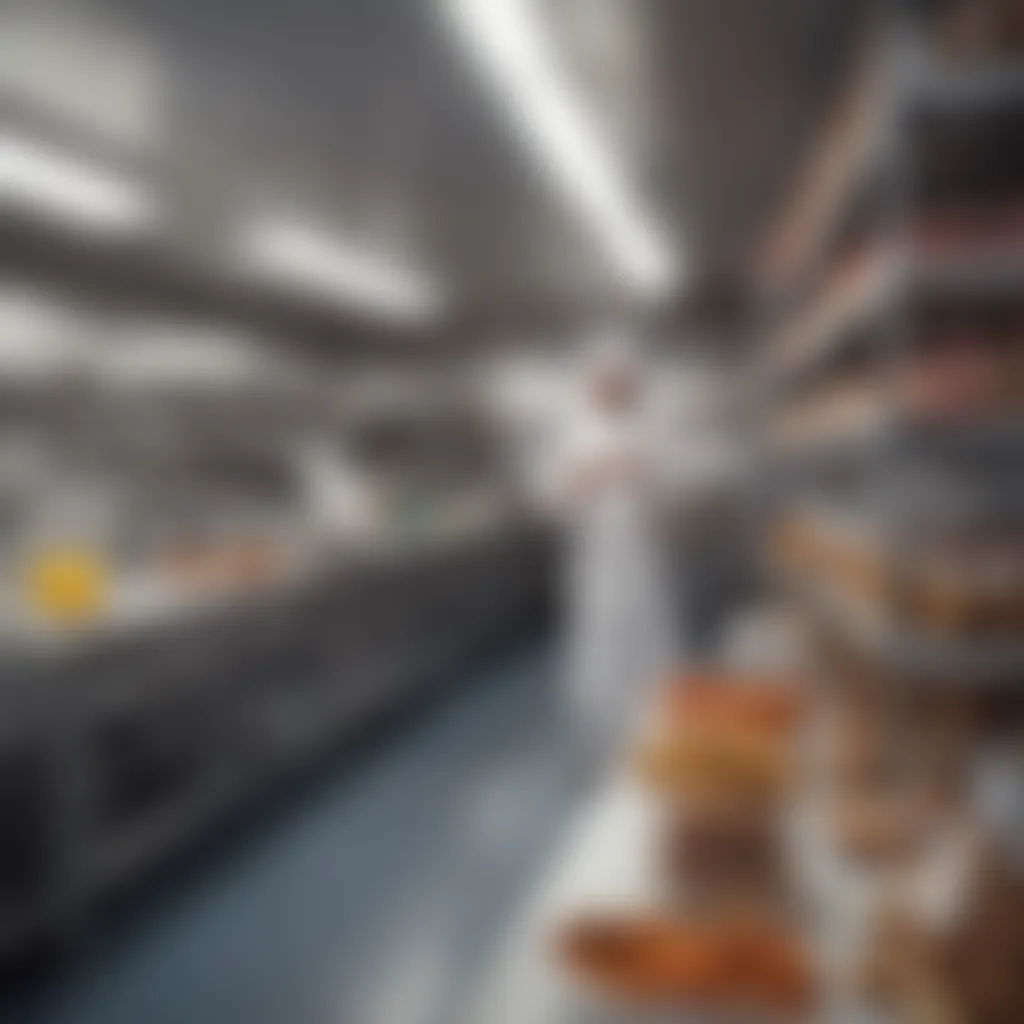
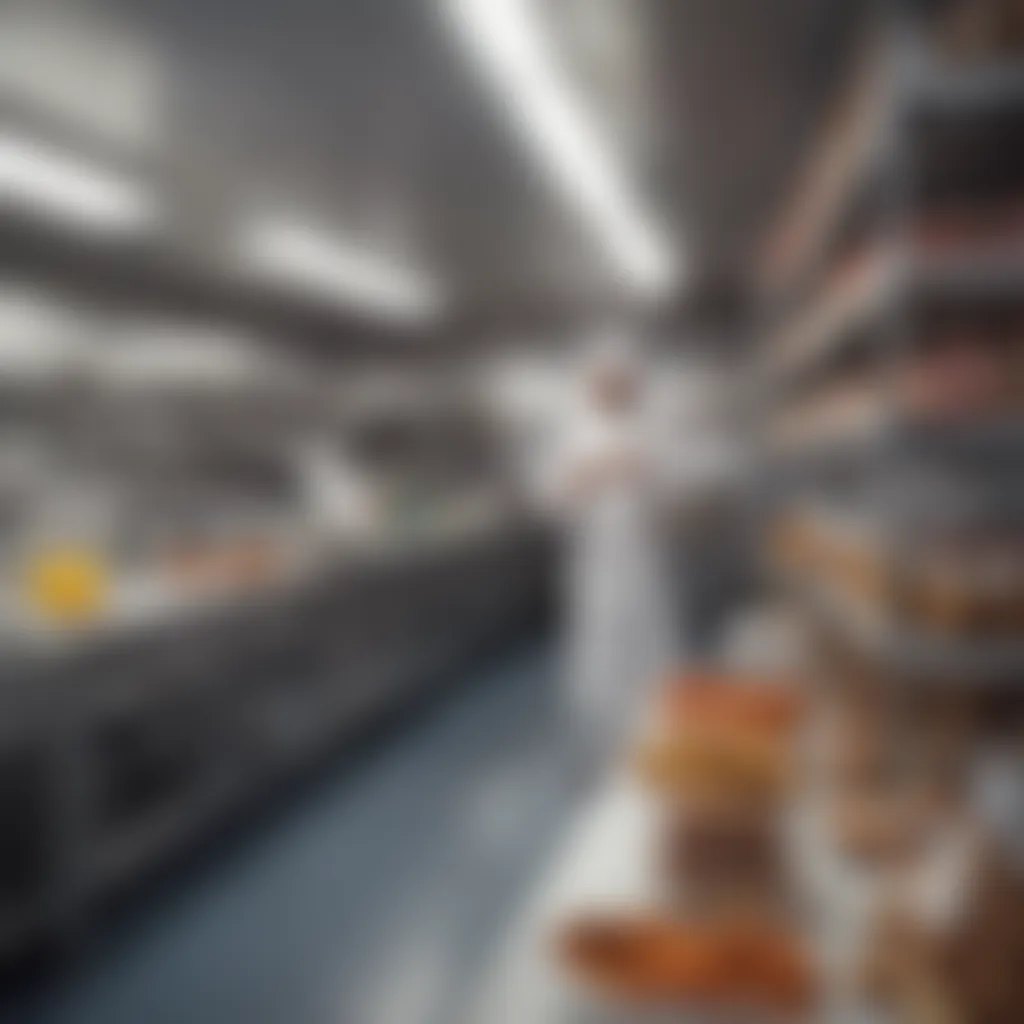
Technology plays a crucial role in ensuring clean rooms are organized and operate efficiently. It enhances the capability to maintain stringent standards of cleanliness and compliance. Many organizations benefit from integrating modern tools and software that simplify processes and minimize human errors. These advanced solutions promote effective organization, streamline workflows, and ultimately bolster product quality and safety.
Software for Inventory Management
Efficient inventory management is vital in clean room environments where regulation and precision are paramount. Software solutions specifically designed for inventory management help track materials and equipment. Programs like Fishbowl or Sortly provide real-time data on stock levels, usage patterns, and reorder points. This information minimizes wastage of supplies and ensures that essential items are always available. By using software, staff can easily categorize and locate items, which enhances overall workflow and reduces the time spent searching for materials.
- Improved accuracy in stock counting.
- Automatic alerts for low inventory.
- Streamlined order processes and receipt of goods.
Automation in Clean Room Processes
Automation reduces labor-intensive tasks in clean rooms. Utilizing robotic systems or automated machinery enhances productivity and ensures high precision in tasks such as cleaning or material handling. For instance, systems like Cleanroom Robot can handle sterilization without human intervention. Automating repetitive processes not only improves efficiency but also reduces the risk of contamination associated with manual handling. Moreover, automation provides a constant monitoring system for environmental conditions like particle counts and air quality.
- Increased efficiency through repetitive automation.
- Consistent environmental monitoring.
- Reduction in human error during cleaning and organization.
Data Collection and Analysis
Data collection and analysis contribute significantly to continuous improvement in clean room operations. Advanced sensors and monitoring tools collect data on various parameters like temperature, humidity, and particulate levels. Software platforms can analyze this data to identify patterns or anomalies. Teams can use this information to proactively address potential issues before they escalate. Furthermore, analytics can help in optimizing workflows and improving overall clean room layout.
By adopting a data-driven approach, organizations can make informed decisions that enhance the integrity and functionality of their clean rooms.
- Enhanced decision-making through analytics.
- Proactive identification of failures.
- Continuous improvement of procedures.
The integration of these technological tools not only streamlines operations but adds value to clean room management. As industries evolve, the role of technology becomes more prominent, driving efficiency and ensuring that clean rooms meet and exceed the necessary standards.
Challenges in Clean Room Organization
Understanding the challenges involved in clean room organization is crucial for maintaining both compliance and operational efficiency. Clean rooms serve highly sensitive environments where any contamination can lead to severe consequences. Thus, recognizing and addressing common obstacles becomes necessary to ensure successful implementation of organization strategies. This section outlines various obstacles that can arise, examines ways to overcome these hurdles, and showcases real-world examples of effective clean room organization.
Common Obstacles
There are a variety of challenges that can hinder effective clean room organization. Some of the most common obstacles include:
- Limited Space: Clean rooms often have strict dimensions, making it difficult to manage a large inventory of materials and equipment.
- Strict Regulatory Compliance: Adhering to industry standards can complicate organization efforts. Non-compliance can lead to penalties or even operational shutdowns.
- Contamination Risks: Any slight misstep in maintaining cleanliness can lead to contamination, jeopardizing sensitive processes. This can stem from improper storage or handling of materials.
- Inadequate Training: Staff may lack the necessary training and understanding of clean room procedures, leading to inefficient organization.
- Inconsistent Practices: Variation in organization practices across personnel can create confusion and disorder within the clean room.
Strategies to Overcome Challenges
Addressing challenges in clean room organization requires a methodical approach. Some strategies that can be effective include:
- Implementing Standard Operating Procedures (SOPs): Developing clear SOPs for every aspect of clean room operation ensures compliance and consistency.
- Maximizing Storage Efficiency: Utilize vertical space and modular shelving systems to optimize storage and free up room on the floor for essential processes.
- Regular Training and New Employee Onboarding: Ensure all personnel are adequately trained to handle clean room protocols. Ongoing training ensures that all staff understand the latest procedures and standards.
- Routine Audits: Conduct regular organization audits to identify problem areas and areas of improvement. This can also help ensure compliance with regulatory standards.
- Emphasizing Communication: Clear lines of communication among staff members can reduce errors caused by inconsistent practices. Encourage regular discussions about organization and cleanliness.
Case Studies of Successful Implementation
Reviewing successful implementations of clean room organization provides insights into effective strategies. For instance:
- Pharmaceutical Company X adopted a rigorous training program that included virtual reality simulations for staff. This method greatly improved the understanding of cleanroom protocol and reduced contamination incidents by 30% within six months.
- A biotech firm, Company Y, faced issues with material storage clutter. They introduced a new visual management system that incorporated color-coded bins and labeling. This change led to a 40% increase in operational efficiency as personnel could easily locate materials.
- Laboratory Z implemented a digital inventory management system, enhancing tracking precision. This reduced the risk of overstocking and minimized expired materials within the clean room.
Successful clean room organization hinges not only on proper practices but also on the ability to adapt and learn from both successes and failures.
Ultimately, overcoming challenges in clean room organization is an ongoing process rooted in strategy, training, and communication. Understanding these elements leads to a more effective clean room environment.
Closure and Future Directions
In the realm of clean room management, an effective organization strategy is not merely beneficial but essential. It serves as a cornerstone for maintaining high standards of cleanliness and operational efficiency. The Conclusion and Future Directions section consolidates the fundamental ideas presented earlier while providing a path for continual advancement in clean room practices.
Summary of Key Points
The main principles of clean room organization are vital for anyone looking to optimize their environment. Key points include:
- Functionality: Each area within the clean room serves a specific purpose. Understanding these functions leads to better organization.
- Regulatory Compliance: Following industry standards is crucial to ensure product safety and effectiveness.
- Use of Technology: Integrating software for inventory and data management refines processes, making them safer and more efficient.
- Training: Continuous training for personnel guarantees all team members are well-versed in protocols and importance of cleanliness.
These points form a solid base upon which further strategies can be built. They encourage a proactive approach to clean room organization.
The Evolving Landscape of Clean Room Practices
Clean room practices are not static. They respond to advancements in technology, regulatory changes, and evolving industry standards. The integration of automation and data-driven management tools has revolutionized the way we approach clean room operation. New software options allow for real-time monitoring of environmental conditions. This not just helps in maintaining the required clean room standards but also facilitates swift corrective actions when deviations occur.
This evolving landscape presents several opportunities:
- Innovation: Emerging technologies provide new methods for efficiency.
- Regulations Adaptation: Changing guidelines necessitate constant review and improvement of processes.
- Best Practices Sharing: Collaboration among professionals allows for shared insights and methods, enhancing overall sector standards.
Staying updated on these trends is crucial for anyone responsible for clean room management.
Recommendation for Continuous Learning
The journey toward effective clean room organization does not conclude with the implementation of strategies. It is essential to embrace a mindset of continuous learning. This can be achieved in various ways:
- Attend Workshops: Regular workshops can enhance skills and knowledge about latest practices.
- Industry Journals: Subscribing to relevant publications keeps one informed about new developments.
- Professional Networks: Joining professional organizations like the Institute of Environmental Sciences and Technology (IEST) fosters connections with peers in the industry.
- Online Platforms: Websites like reddit.com and facebook.com may provide community support and exchange of ideas on clean room management.
Cultivating a habit of learning can significantly impact both individual performance and overall organizational success. This proactive approach propels clean room practices into the future, making them more effective and compliant with current standards.