The Logimat Recipe for Efficient Warehouse Management

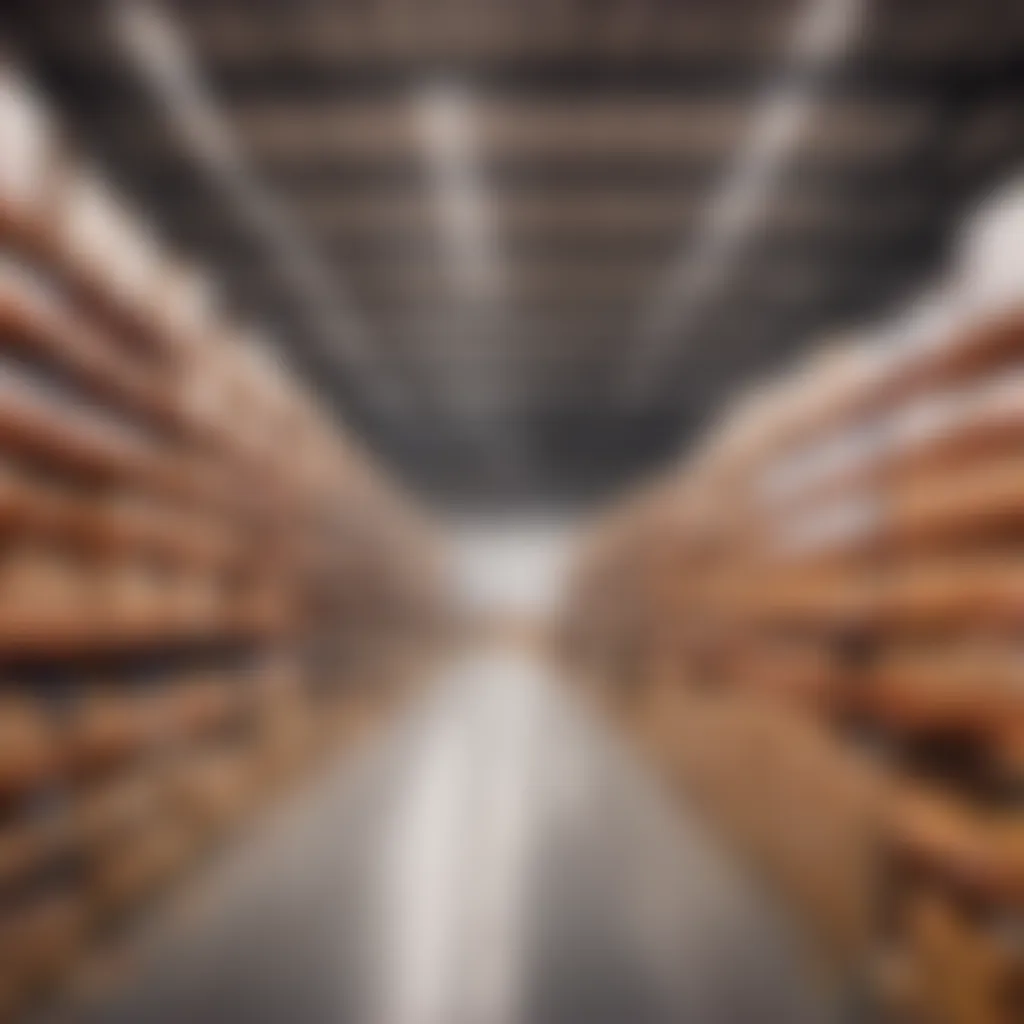
Intro
In today's fast-paced world of logistics and warehousing, the efficiency of operations often hangs by a thread. The challenge for warehouse managers is much like cooking a delicate soufflé: too much movement can make it collapse, while too little can leave it flat. Enter Logimat solutions, a beacon of hope amidst the chaos of inventory management. Much like any good recipe, knowing the right ingredients and methods can set the stage for success.
For those who are navigating the waters of warehousing, it's essential to understand how each element, from technology to human resources, plays a role in streamlining processes. Much can be gleaned from examining the various aspects of Logimat systems and the impact they have on enhancing workflow, optimizing material flow, and effectively managing inventory. This article aims to provide a comprehensive guide, breaking down each fundamental component into digestible parts that can elevate operational standards, just like a well-cooked dish tantalizes your taste buds.
With insights gathered from industry experts and case studies showcasing real-world applications, we're embarking on a journey to discover how to get the most out of your warehouse operations. Let’s take a closer look at the key elements you need to cook up a more efficient and productive warehouse.
Ingredients:
To start our discussion on refining warehouse processes with Logimat solutions, let’s outline the key ingredients necessary for a successful operation:
- Warehouse Management System (WMS): the core software tool that integrates various warehouse functions.
- Automation Technologies: including robotics, conveyors, and advanced picking systems to enhance speed and precision.
- Real-Time Data Analytics: tools that provide insights on inventory levels and performance metrics to drive informed decision-making.
- Employee Training Programs: essential for maintaining a skilled workforce that is adept at utilizing the new systems efficiently.
- Inventory Optimization Methods: practices that ensure stock levels are balanced to meet demand without oversupply.
- Material Handling Equipment: tools such as forklifts and pallet jacks to effectively transport goods.
These components act as the base ingredients, each adding its unique flavor to the recipe of operational efficiency in the warehouse.
Preparation Steps:
Now that we know our ingredients, let’s dive into detailed instructions that will set the stage for an optimized warehouse operation:
- Assess Current Operations: Begin by evaluating existing systems to identify bottlenecks. This is akin to checking your kitchen for expired ingredients before starting your meal.
- Select the Right WMS: Choose a Warehouse Management System that aligns with your operational needs. Look for integration capabilities with existing software.
- Implement Automation Technologies: Introduce automation incrementally, ensuring smooth transitions and minimizing disruptions.
- Train Employees: Invest time and resources in training staff on new technologies and processes to increase adoption and efficiency.
- Monitor and Adjust: Utilize real-time data analytics to continuously track performance and adjust methods as necessary.
By following these preparation steps, you're laying a solid ground for your warehouse operations.
Technical Aspects:
Understanding the technical side is crucial for any aspiring warehouse manager looking to refine their processes. Here are some technical specifications to bear in mind:
- Temperature Settings: Ensure that areas handling perishable goods are set to the right temperature according to guidelines to prevent spoilage.
- Timing Specifics: Evaluate average picking times and aim to reduce them by at least 20% with new technologies.
- Critical Techniques: Implement methods such as ABC analysis for inventory control, which helps categorize items based on importance and turnover rates.
Cooking Process:
As you proceed with optimizing your warehouse operations, consistency is key. Here’s how to incorporate the aforementioned elements:
- Initiate a Pilot Program: Start with a small section of your warehouse to test new technologies and processes.
- Analyze the Results: After a defined period, review performance metrics to gauge the effectiveness of what you implemented.
- Scale Up: Gradually expand successful practices warehouse-wide while ensuring all staff is on board and trained.
Key Techniques and Timings:
- Regularly schedule maintenance of automated systems to prevent downtime.
- Schedule employee shifts to ensure coverage during peak operation hours.
Troubleshooting Tips:
Even with the best laid plans, hurdles may arise. Here are some common issues and their solutions:
- Issue: Integration problems with the WMS.
Solution: Consult with the software provider for updates or patches to ensure better compatibility. - Issue: Employee resistance to new technologies.
Solution: Highlight the benefits through workshops and hands-on sessions to ease concerns.
"Success in warehouse management is a journey, not a destination; constant improvement is the name of the game."
In summary, mastering the logimat recipe demands careful consideration of every ingredient. By systematically implementing the steps outlined, engaging with technology, and fostering a skilled workforce, warehouse operations can become more streamlined and efficient. It’s all about cooking up a strategy that results in a well-oiled operation.
Prolusion to Logimat Solutions
Understanding the dynamics of modern warehouse management is crucial for any operation that seeks efficiency and effectiveness. The role of sustainable systems has become paramount, and that’s where Logimat solutions come into play. They serve as a beacon for organizations seeking to streamline their processes, improve productivity, and ultimately enhance their bottom line. Whether you’re knee-deep in inventory management or grappling with shipping logistics, embracing Logimat solutions can lead to smoother workflows, less waste, and a better grasp of operational metrics.
Overview of Warehouse Challenges
Warehouses today face a myriad of challenges that can make or break an operation. Some of the main headaches include:
- Space Management: With limited square footage, maximizing available space can feel like a game of Tetris.
- Inventory Control: Keeping tabs on stock levels and preventing shrinkage is essential, but it can be quite the uphill battle.
- Labor Costs: Labor inefficiencies add up, affecting both productivity and morale.
- Technology Integration: As new technology emerges, integrating these systems can be confusing and costly.
Each challenge presents a unique obstacle, but each one also offers an opportunity for improvement when approached strategically. This is where Logimat comes in, providing tailored solutions that cater to optimizing storage, processing, and overall warehouse efficiency. It’s the light at the end of the tunnel.
What is Logimat?
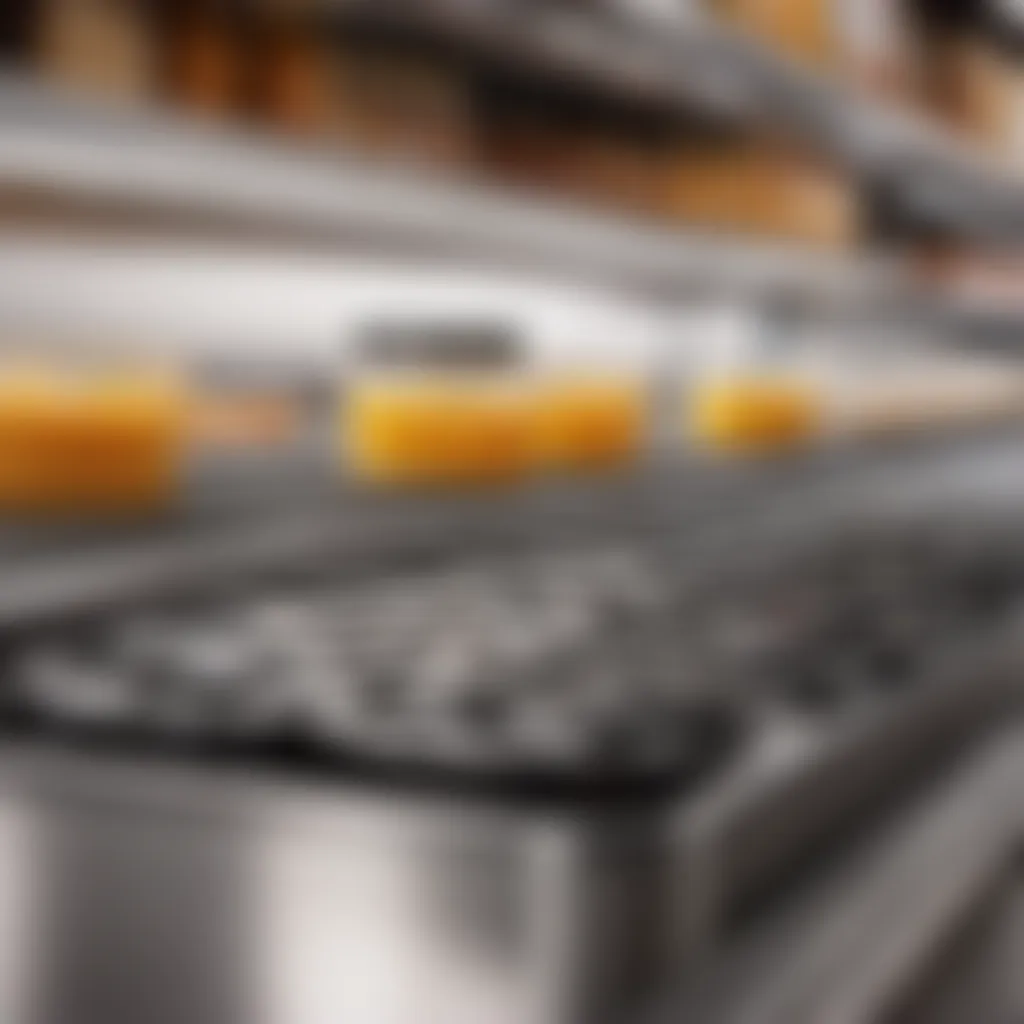
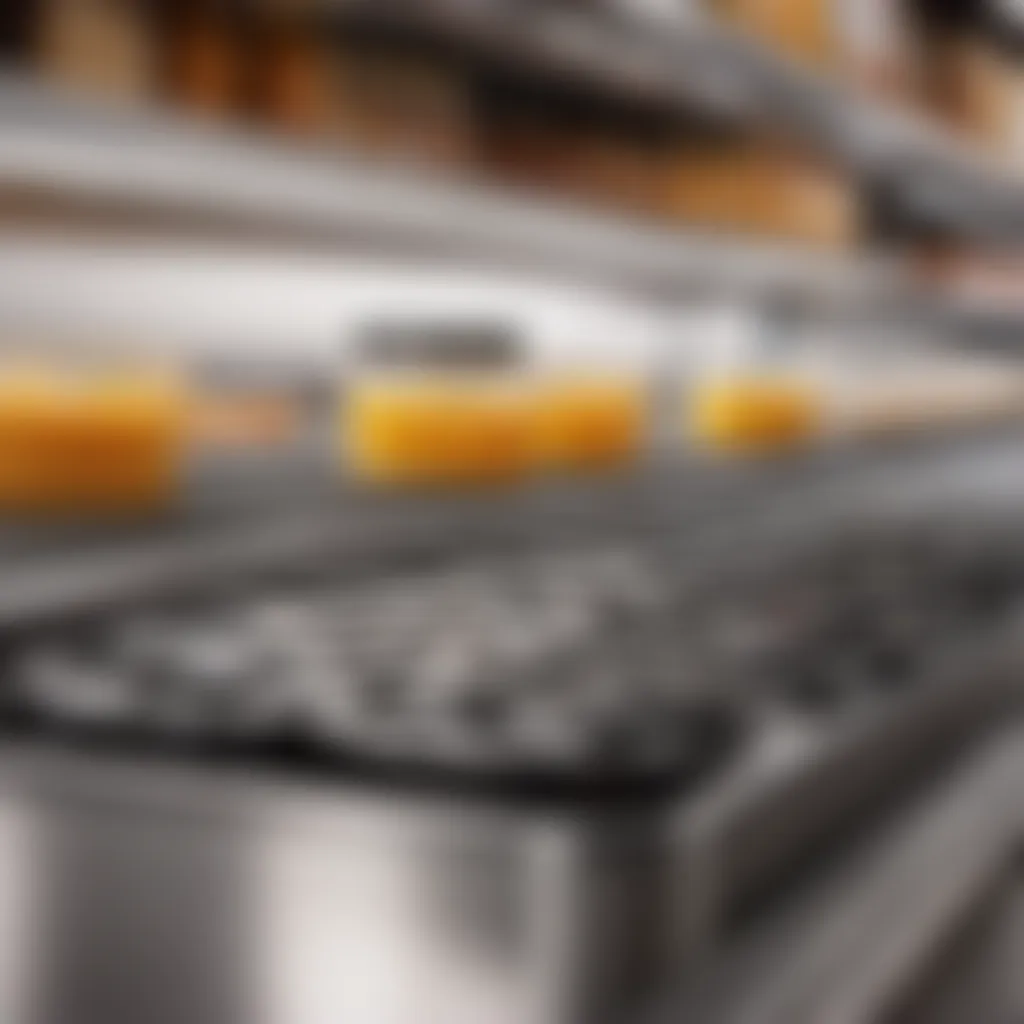
Logimat is a cutting-edge automated storage and retrieval system that aims to transform how warehouses operate. This technology allows for faster access to inventory and optimizes the utilization of vertical space. From compact storage solutions to their sophisticated retrieval mechanisms, Logimat systems help businesses reduce the time and labor costs associated with traditional warehousing methods.
- Key Features of Logimat:
- Modular Structure: Adaptable to different warehouse sizes and layouts.
- High Density Storage: Maximizes vertical space, making the most of cubic feet.
- Real-Time Data Monitoring: Keeps track of inventory levels instantly, reducing errors and improving decision-making.
By prioritizing efficiency through innovative features, Logimat helps companies stay ahead of the curve while wrestling with the everyday challenges of warehouse management. It’s more than just a system; it’s a game-changer in the logistics domain.
Foundations of Warehouse Efficiency
Efficiency in a warehouse isn’t just a nice-to-have; it's the backbone of successful operations. streamlining processes can lead to cost savings, improved customer satisfaction, and a more harmonious working environment. With the explosive growth of ecommerce, the need to optimize every aspect of warehouse management has become essential. The foundations of warehouse efficiency lie in mastering the integration of various systems, processes, and technologies that work in tandem.
When we talk about efficiency, the balance between speed and accuracy takes center stage. Warehouse operations need to maintain a swift pace while ensuring that items are stored, retrieved, and shipped correctly. Without solid foundations, you might as well be running in circles, expending energy without making progress. Here, we’ll explore two crucial facets: the role of material handling systems and how to identify bottlenecks within operations.
The Role of Material Handling Systems
Material handling systems serve as the framework for how products are transported, stored, and managed within a warehouse. Think of these systems as the veins and arteries of your warehouse, ensuring that everything flows smoothly from incoming goods to final delivery. When you set up a strong material handling system, you’re looking at a few critical components:
- Efficiency: Automated systems can increase speed and reduce manual labor.
- Safety: Minimizing the risk of accidents through design and automation helps protect your workforce.
- Accuracy: Proper handling reduces errors in inventory and enhances order fulfillment.
Investing in appropriate material handling equipment—like conveyors, lifts, and automated guided vehicles—can dramatically influence overall efficiency. Something as simple as organizing inventory systematically can save time during order picking.
Identifying Bottlenecks in Operations
Even the best system can grind to a halt if bottlenecks exist. These are the points in the workflow where congestion occurs, slowing down the entire operation. Identifying these pitfalls is critical because they can lead to higher costs and lowered customer satisfaction.
To effectively spot bottlenecks, ask yourself:
- Where do delays frequently occur? Are items sitting idle waiting for processing?
- Are there too many manual processes? Over-reliance on human intervention could slow things down.
- Is the equipment causing hold-ups? If machinery is outdated or breaks down often, it can stall operations.
Once you pinpoint where the snags happen, you can take action. Solutions may vary from training staff better and optimizing layouts to investing in advanced technology. Addressing these issues leads to a smoother operation and better results overall—a far cry from chaotic long workdays and late shipments.
Remember: A stitch in time saves nine. Tackling issues before they escalate can save you a world of headaches.
Implementing Logimat Technology
Implementing Logimat technology in warehouse operations is not just about upgrading tools or software; it’s a strategic maneuver that holds the potential to redefine how goods are managed, stored, and retrieved. By embracing these technologically advanced solutions, businesses can effectively streamline their processes, enhance productivity, and elevate overall performance. For warehouse managers, gaining a solid grasp of how to implement Logimat technology is essential for navigating the complexities of modern logistics.
Assessment of Current Systems
Before diving headfirst into the implementation of Logimat systems, evaluating the existing operations is a crucial first step. This assessment helps in identifying gaps, inefficiencies, and pain points in the current setup. It’s akin to tuning a recipe—we must know what ingredients we have before making a change.
- Evaluate Efficiency: Take stock of the current workflows and observe how items move through the facility. Are there unnecessary delays? Is there a bottleneck at a specific point? Pinpointing these issues allows for targeted improvements.
- Cost Analysis: Understand the financial implications of current operations. What resources are being underutilized? Furthermore, where are the hidden costs that could be trimmed?
- Staff Feedback: Gather insights from employees on the ground. They are the ones interacting with the systems daily and will have valuable first-hand insights about what works and what doesn’t.
Key Takeaway
"Understanding your current systems is the blueprint for progress. Without it, you’re likely just building in the dark."
Integration with Existing Infrastructure
The beauty of Logimat technology lies not just in its advanced features but also in its capacity to seamlessly blend with existing infrastructures.
- Modular Solutions: Logimat systems are designed to be modular, enabling businesses to add technology incrementally without overhauling everything. This flexibility is important for warehouses with limited budgets.
- Software Compatibility: Ensure that the new systems can interface with your current warehouse management software. Compatibility is vital to avoid disruptions and ensure smooth data flow.
- Process Alignment: Map out how the integration will affect current workflows. It’s essential to visualize the end-to-end process, identifying how many steps will remain unchanged and which ones will be enhanced.
Training the Workforce
Equipping a warehouse with sophisticated technology is only half the battle; the other half lies in ensuring the workforce is trained effectively to use it.
- Comprehensive Training Programs: Design practical training sessions that accommodate different levels of tech-savviness. Hands-on practice can help demystify new systems.
- Continuous Learning: Technology evolves at a rapid pace, so ongoing training is important. Creating a culture of continuous learning ensures that employees stay updated with advances in Logimat technology.
- Feedback Loop: Encourage employees to share their experiences using the new system. Their feedback can guide future training sessions and highlight areas where further clarification may be needed.
In summary, implementing Logimat technology is a transformative journey that requires careful assessment, strategic integration, and robust training. By prioritizing these elements, warehouses can enhance efficiency and carve a path toward greater operational excellence.
Optimizing Inventory Management
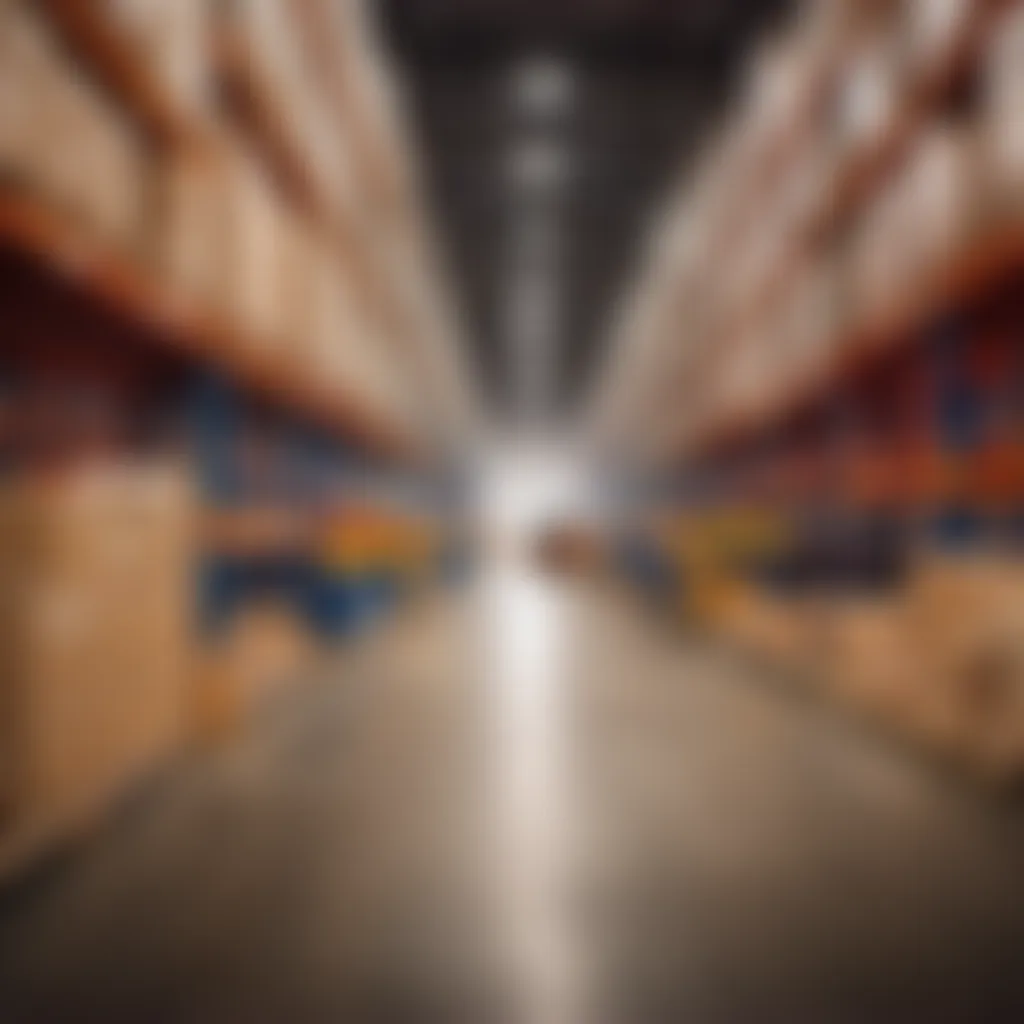
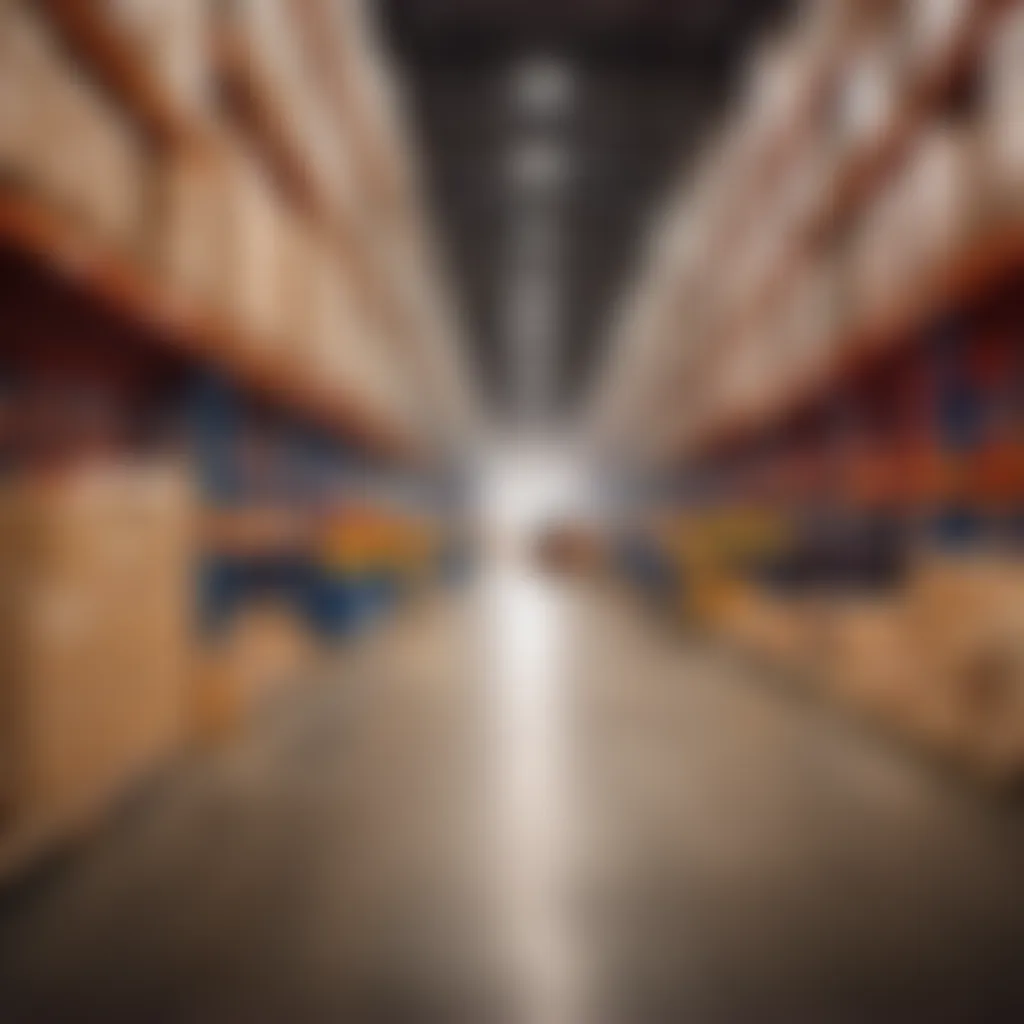
Optimizing inventory management is like fine-tuning a well-oiled machine. In the warehouse setting, this means reducing waste, meeting customer demands, and keeping costs manageable. An effective inventory system acts as the backbone of operations, not just keeping tabs on what you have but ensuring that what you have aligns perfectly with the market needs.
Incorporating Logimat solutions into inventory management doesn’t merely automate tasks; it greatly enhances accuracy and efficiency. For warehouse professionals, it's about streamlining processes to elevate operational standards while focusing on immediate goals, such as minimizing excess stock and maximizing turnover. The need for accuracy goes beyond mere numbers; it ultimately trickles down to customer satisfaction, supply chain effectiveness, and profitability.
Just-In-Time Inventory Practices
Just-in-Time (JIT) inventory practices are fundamentally about timing and efficiency. Rather than storing large quantities of products that can gather dust, JIT encourages warehouses to receive goods only as they are needed in the production process. This practice not only reduces storage costs but also helps to keep inventory fresh.
JIT is particularly advantageous when integrated with Logimat solutions, which can provide data analytics to forecast demand and manage supplier relations. Being able to identify trends can save a significant amount of stress. Imagine going from a scenario of excess inventory that drags down a warehouse to a lean system where products flow in and out smoothly. This shift allows warehouses to react quickly to market changes, minimize carrying costs, and reduce the risk of obsolescence.
Tracking and Transparency Solutions
Tracking and transparency in inventory management cannot be overlooked. Without solid tracking systems in place, businesses might find themselves chasing shadows. The beauty of modern Logimat technology is in its ability to track products in real-time, providing visibility into stock levels, order statuses, and shipping processes.
- Products can be tagged through barcoding or RFID technology, making it easy to pinpoint exactly where everything is located.
- Additionally, visibility promotes accountability, allowing warehouse staff to spot issues before they escalate. Rather than simply reacting to problems, warehouses can ensure that they are proactive.
"A well-implemented tracking system turns data into decisions. If businesses get a firm grip on their inventory status, they can improve workflows significantly."
In summary, optimizing inventory management is a meticulous yet rewarding endeavor. By leveraging Just-In-Time practices and ensuring tracking and transparency, warehouses not only operate more efficiently but also align more closely with the demands of customers and the market.
Enhancing Warehouse Flow
Enhancing warehouse flow is the backbone of efficient logistics and operations. It’s not just about moving products from point A to point B; it's about creating a symphony where every part of the warehouse dances to the same rhythm. When flow is optimized, it directly impacts productivity, reduces costs, and improves customer satisfaction. A seamless flow in the warehouse ensures that products reach customers in a timely manner, thus building trust and loyalty.
Mapping Out Workflow Processes
Understanding workflow processes is akin to mapping out the treasure path on a pirate's map. It is crucial to identify every stage of how goods are received, stored, and dispatched. Start by visually laying out the floor plan of your warehouse. Identify key areas controlling incoming goods, storage spaces, and dispatch points. When these elements are clearly defined, it becomes easier to streamline operations.
- Identify key stages: Understand each step, from receiving to shipping. This highlights bottlenecks, inefficiencies, or redundancies.
- Utilize visual aids: Flowcharts or diagrams can depict the process in a clear manner, facilitating better communication among team members.
- Iterate and improve: Regularly revisit the flowchart. As products, technologies, or processes change, so too should the workflow.
Just as a recipe requires a methodical approach to ensure that each ingredient plays its part, so too does warehouse flow. Each move should connect logically to the next, minimizing unnecessary delays.
Utilizing Automated Guided Vehicles
Automated Guided Vehicles (AGVs) are transforming how goods are moved within warehouses. These are not just toys for tech enthusiasts; they play a pivotal role in enhancing efficiency.
- Consistency and Reliability: AGVs can run continuously, transporting materials without the need for breaks, thus increasing throughput.
- Reduction in Labor Costs: By integrating AGVs into your operations, businesses can decrease reliance on manual labor, leading to potential savings in payroll expenditures.
- Safety Improvements: These vehicles reduce human error, which is often a source of accidents in busy warehouse environments.
Implementing AGVs also requires strategic planning. You must ensure their paths are optimized to prevent collisions and redundancy. Think of it like choreographing a dance—the movements have to be synchronized for quality performance.
"Streamlined warehouse operations are less about speed and more about effective use of capacity."
Data-Driven Decision Making
In the whirlwind of modern warehouse management, the ability to make informed decisions based on solid data cannot be overstated. Data-driven decision-making emerges as a cornerstone for optimizing operations and mitigating risks. Without a clear understanding of the data gathered, decisions can resemble throwing darts in the dark. Each point of data collected serves as a guide, illuminating the path to enhanced efficiency and cost savings.
Warehouse operations are often hindered by guesswork, which can lead to inefficiencies and lost opportunities. By harnessing the power of data, organizations can analyze performance metrics, customer trends, and inventory levels with precision. This analytical approach not only fine-tunes day-to-day activities but also strategically positions businesses for long-term success.
Specific Elements and Benefits of Data-Driven Decision-Making
- Enhanced Forecast Accuracy: Leveraging historical data can significantly improve forecasting. Businesses can better predict demand cycles, helping to maintain optimal inventory levels. When managers know what to expect, they can avoid overstocking or stockouts, keeping the warehouse running smoothly.
- Resource Allocation: Data analysis allows for the optimal distribution of human and physical resources. By understanding which processes consume the most time or energy, companies can shift focus and streamline efforts, leading to increased productivity.
- Performance Monitoring: Regularly analyzing key performance indicators (KPIs) helps in identifying trends over time. It helps management to swiftly adjust strategies to mitigate any negative impacts before they spiral out of control.
- Customer Insights: Understanding customer behavior through data can shape inventory practices. Tailoring stock to what is actually selling can drastically reduce wasted space and resources.
Ultimately, data-driven decision-making cultivates a culture of accountability and continuous improvement within warehouse operations.
Importance of Analytics in Warehousing
The backbone of data-driven decision-making lies in robust analytics. It not only transitions data from mere numbers on a spreadsheet to actionable insights but also empowers warehouse managers to drive informed choices. Analytics tools dissect data, transforming it into narratives that lead to solutions. A good warehouse manager knows not only how to collect data but also how to interpret it.
More than just reporting numbers, effective analytics fosters an understanding of operational inefficiencies. Staff can pinpoint exactly where delays occur and why certain processes stutter. Thus, the old adage “knowledge is power” aligns closely with analytics—equipping managers with the tools to problem-solve effectively. A warehouse that embraces analytics is like a well-oiled machine, capable of fine-tuning operations for maximum benefit.
Real-Time Data Usage
Stepping up the game, real-time data usage presents warehouses with an agile method to operate. Unlike static reports that date quickly, real-time data provides an up-to-the-minute snapshot of the operational landscape. This immediate access can be crucial, especially in industries characterized by rapid inventory turnover.
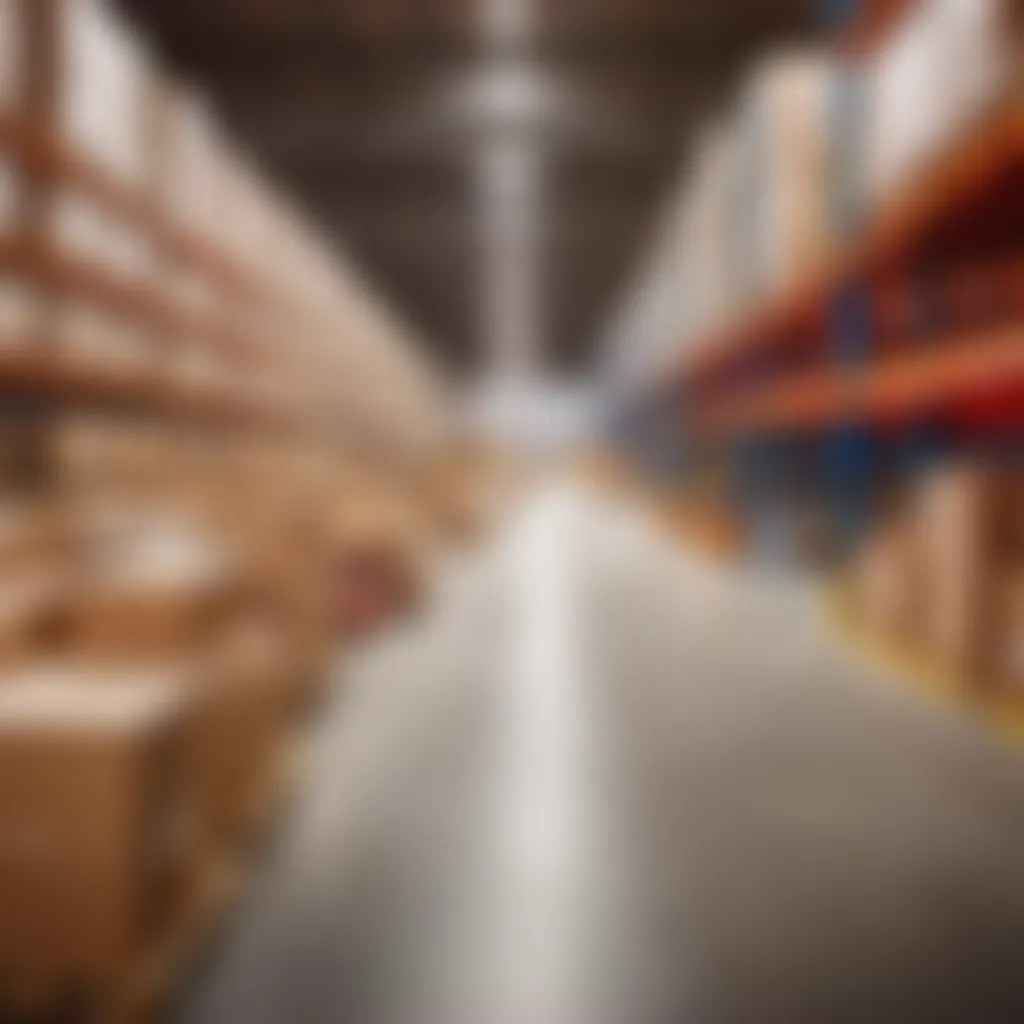
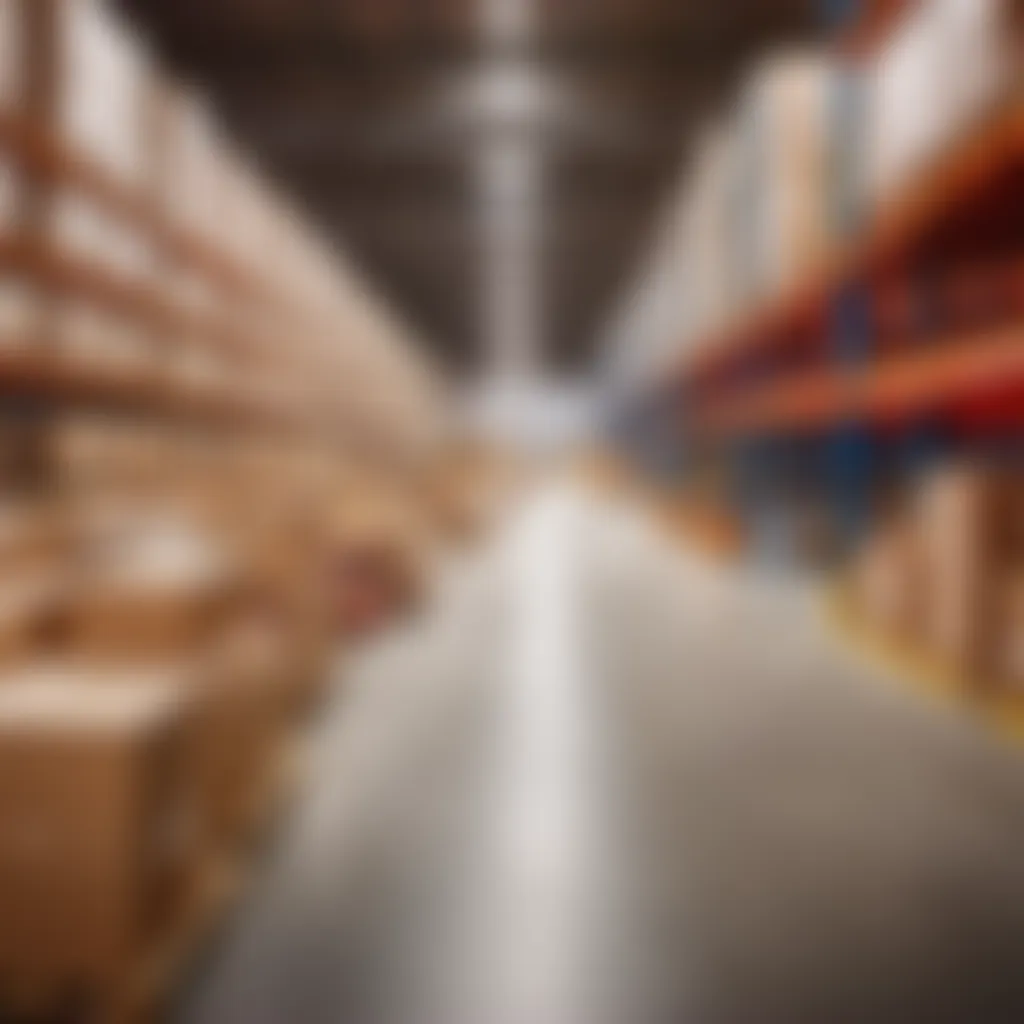
Having the right tools to access real-time information means decisions can be made on the fly, rather than waiting for weekly meetings or end-of-month reports. This swift action can be the difference between capturing a fleeting market opportunity or missing it entirely.
"In the world of warehousing, timing is everything. Real-time data allows us to move from reacting to acting."
The comprehensive integration of real-time data can streamline various processes, such as:
- Inventory Management: Tracking stock as it flows in and out allows for timely replenishment, minimizing the risk of excess or insufficient inventory.
- Order Fulfillment: Knowing immediately when an item is available or delayed significantly enhances customer service and satisfaction.
- Workforce Optimization: Real-time data can illustrate where labor is allocated inefficiently, enabling managers to make instant adjustments.
In sum, data-driven decision-making nurtures an environment ripe for process improvement and strategic growth. By emphasizing analytics and harnessing real-time data, warehouses can navigate the complexities of their operations with clarity and confidence.
Reducing Operational Costs
In the world of warehouse management, cutting operational costs is more than a mere necessity; it’s an essential strategy for survival and growth. The end goal is clear: maximizing profits while minimizing expenses. Every dollar saved can be funneled back into other aspects of the operation, paving the way for upgrades, investment in technology, or even employee incentives. In this section, we will delineate why and how cutting costs is paramount, alongside considerations and benefits that can arise from a shrewd approach towards savings.
Reducing operational costs can dramatically redefine the way a warehouse operates. When costs are aligned with efficiency, it allows for a better inflation-adjusted profit margin, enabling businesses to stay competitive. Furthermore, a focus on cost reduction often yields unexpected benefits like improved employee morale, heightened customer satisfaction, and a more resilient supply chain. As a housewife juggling family expenses, these principles reflect similar tactics used at home to ensure every penny counts.
Evaluating Cost-Saving Techniques
Now let's dive into the nitty-gritty of evaluating cost-saving techniques that can be applied in warehouse settings. Here are a few techniques worth considering:
- Energy Efficiency: An energy audit can help pinpoint areas where consumption can be reduced or optimized. Simple modifications like switching to LED lighting or programmatically managing heating and cooling systems can lead to significant savings.
- Inventory Optimization: Keeping excessive stock ties up capital and incurs storage costs. Techniques such as Just-In-Time (JIT) inventory management help maintain an efficient flow, ensuring you stock only what you need without incurring excessive warehousing expenses.
- Workforce Scheduling: Investing in workforce management software can optimize employee schedules according to peak times, reducing the need for overtime.
- Supplier Negotiations: Renegotiating contracts with suppliers can yield better terms, leading to reduced costs per unit purchased. A conversation that might save a whole lot in the long run.
- Equipment Maintenance: Regular maintenance of machinery prevents costly breakdowns that can halt operations. Investing in preventative maintenance ensures that equipment remains in top shape, protecting the bottom line.
Consider these techniques as spices in a recipe—the right blend can transform your operational costs, making the final dish (your profit) much more palatable.
The Impact of Process Improvements
Process improvements are the backbone of any successful cost-reduction strategy. When systems and procedures are streamlined, waste is minimized, and resources are managed effectively.
To examine this impact further:
- Reduction in Cycle Times: Process improvements can lead to faster order fulfillment, which directly correlates with cost reductions through increased productivity. Think of a canning process at home—it can become a chore if not organized properly. But using assembly line principles ensures efficiency.
- Enhanced Quality Control: By redefining processes, errors can be reduced. Less rework leads to lower costs, much like how a carefully measured family recipe can reduce wasted ingredients.
- Employee Engagement: Streamlined processes often result in a more engaged workforce. Employees appreciate clarity, and when given the tools to make their jobs easier, productivity spikes and error rates tumble.
"Improving processes isn't just about cost savings; it's about creating a culture of continuous optimization that permeates through all levels of the operations."
In summary, when you reduce operational costs through meticulous evaluation of cost-saving techniques and impactful process improvements, it creates a ripple effect that benefits the entire warehouse ecosystem. It enhances productivity, boosts morale, and ultimately puts more dough in the pocket.
Empowering your warehouse operations with these strategies can not only lower operational costs but also set the stage for future growth and success.
Future Trends in Warehouse Operations
The realm of warehouse management is on the cusp of substantial transformation, driven by evolving technologies and shifting market dynamics. The significance of understanding these future trends cannot be overstated. For professionals in the field, staying ahead of the curve means differentiating themselves through agility and adaptability.
As warehouses become more essential in the supply chain, the need to optimize operations while ensuring value for customers is paramount. Thus, the trends we explore not only offer insights into what the future holds but also highlight the strategic moves businesses can undertake to thrive amid ever-changing demands.
Emerging Technologies in Logistics
Emerging technologies are reshaping the logistics landscape in ways that were unimaginable a decade ago. The advent of the Internet of Things (IoT) has brought forth smart devices that can communicate essential data in real-time. Warehouse managers now have the capability to monitor inventory levels, track equipment performance, and streamline communication across teams through interconnected devices.
Robotics is another game-changer. Automated systems, including drones and autonomous vehicles, have started to make their mark. These technologies can handle repetitive tasks—like picking and packing—much faster and with fewer errors than human labor. It’s like having an extra pair of hands that works tirelessly day and night.
Furthermore, artificial intelligence is being utilized to predict trends and demand fluctuations. Imagine having a crystal ball that not just tells you what’s likely to happen but also prepares your warehouse for it. Predictive analytics can enhance decision-making, making operations more proactive rather than reactive, which is a monumental leap forward.
The integration of these technologies into existing operations requires careful consideration of costs and training, but the potential benefits are staggering. Efficient systems can lead to reduced lead times and enhanced customer satisfaction.
Sustainability Practices in Warehousing
As we move forward, sustainability has emerged as a crucial component of warehouse operations. Companies are beginning to realize that adopting green practices is not just good for the planet; it’s also good business.
Implementing energy-efficient solutions such as LED lighting and solar panels can drastically reduce energy consumption and costs. Consider this: a well-lit warehouse with sustainable energy sources not only lowers the electric bill but also projects a positive image to environmentally conscious consumers.
Moreover, recycling and waste management practices within warehouses are becoming more standard. Companies now look to reduce packaging materials and utilize more biodegradable options. Minimizing material waste not only cuts costs but also aligns with a growing public demand for sustainable practices.
Another aspect of sustainability involves optimizing transportation routes to decrease carbon footprints. By strategically planning shipments and reducing the distance traveled, warehouses can significantly lessen their environmental impact.
"Adopting sustainable practices is increasingly seen as a competitive advantage in a crowded marketplace."
These trends reflect a broader commitment to sustainability within the logistics sector, indicative of a shift in consumer expectations. As these practices deepen, they cultivate a culture of responsibility that can resonate with customers.
In summary, future trends in warehouse operations are set to be influenced heavily by technology and sustainability. Recognizing the value in these areas can empower businesses to make informed decisions, ensuring they remain a step ahead in this rapidly evolving industry.