Master the Art of Forging: Anvil Mastery Revealed
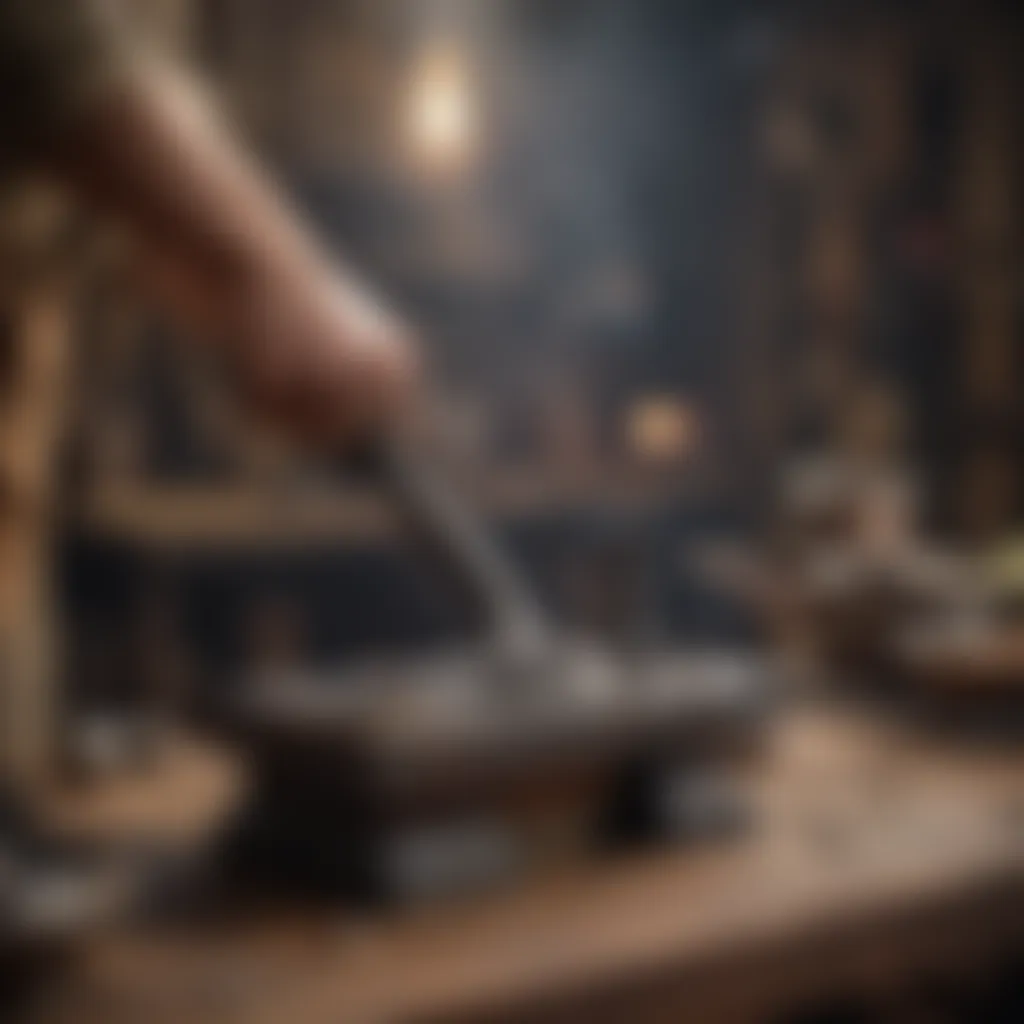
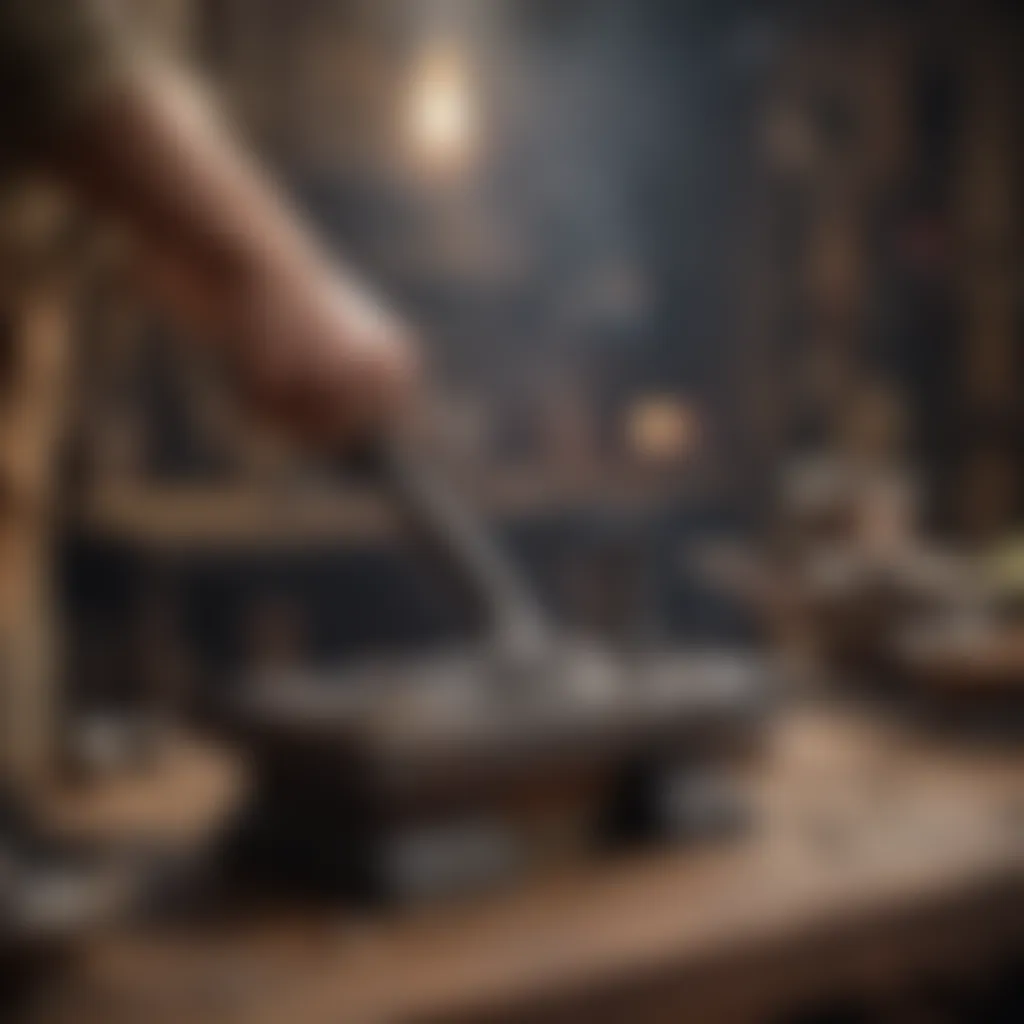
Ingredients:
To embark on the journey towards mastering anvil forging, one must first gather the necessary components. This list outlines the essential materials you'll need, ensuring you have everything in place to create stunning metalworks:
- Anvil: A solid, heavy piece, preferably wrought iron or steel with a flat surface for working.
- Hammers: A ball-peen and a cross-peen hammer are ideal for different striking needs.
- Tongs: A pair of sturdy tongs to handle hot metal safely.
- Steel rods: Low carbon steel is a good starting material, about 1/2 inch thick.
- Forge: A coal forge or propane forge, whichever fits your access and needs better.
- Quenching Oil: An oil specifically formulated for quenching, like canola oil, for hardening the metal.
- Safety Gear: Gloves, goggles, and a thick apron to protect yourself during the process.
- Flammable Material: Kindling for starting the forge fire, such as small sticks or newspaper.
Gather these items, and youâll be laying a solid foundation for your blacksmithing adventure.
Preparation Steps:
Having the right tools and ingredients is only half the battle, however; the heart of forging lies in preparation. Hereâs a detailed walkthrough:
- Set Up Your Workspace: Ensure your workspace is clean and organized. Place the anvil at a comfortable height for striking.
- Prepare Your Forge: Load the forge with coal or establish the propane flow. Ignite it using your kindle material. Aim for a consistent temperature, ideally around 1,500°F (815°C).
- Choose Your Steel: Select a steel rod from your gathering. If youâre new to this, sticking to low-carbon steel can help reduce the potential for mistakes during your first few attempts.
Technical Aspects:
Understanding the technical aspects of forging is vital for success. This includes not just knowledge of your materials but also the critical techniques that differentiate an amateur from a master:
- Temperature Settings: Maintain your forge temperature around 1,500°F to get your steel red-hot, making it malleable.
- Timing: From the moment you insert your steel into the forge, keep an eye on the color. The steel should glow bright orange-red, which is a signal it is ready for work. This usually takes 6-10 minutes.
- Critical Techniques: Ensure you strike with purpose and the right force. Avoid excess pressure that could warp the metal. Learn to listen to the sound of the steel; a clean strike will produce a ringing sound, whereas a dull thud may indicate improper contact.
Cooking Process:
Now that we've laid the groundwork, itâs time to dive deep into the cooking process of forging:
- Heating the Steel: Insert your chosen steel rod into the forge, monitoring the heat closely. Aim for that bright orange hue.
- Removing the Steel: Once heated, use your tongs to remove the steel. Be cautious of any sparks that might fly.
- Striking: Place the hot steel onto the anvil and begin striking. Start with the flat side of your hammer to flatten it before using the peen side to shape the edges.
- Reheating as Needed: If the steel cools down and becomes unworkable, simply return it to the forge, watching the temperature occasionally.
- Quenching: Once you have achieved your desired shape, submerge your piece in the quenching oil to harden it.
Troubleshooting Tips:
Even seasoned blacksmiths encounter hurdles. Hereâs how to solve some common hiccups:
- Steel Won't Heat Properly: Try adjusting airflow in your forge if the steel isnât heating up quickly.
- Metal Warping: Ensure youâre striking evenly and not applying too much pressure on one side.
- Dull Edges After Quenching: If the edges appear dull, consider reheating the steel slightly and re-striking.
"Blacksmithing is not just a craft; itâs an expression of artistry forged in fire."
By following these steps and understanding the intricate balance of temperature, techniques, and timing, you'll be well on your way to becoming not just a practitioner, but a craftsman in the art of anvil forging. Dive in and relish the journey!
The Foundations of Blacksmithing
The world of blacksmithing is a rich tapestry woven from various threads of knowledge, skill, and tradition. To truly excel in forgingâespecially when mastering the use of an anvilâitâs critical to grasp the foundational elements that guide this craft. This foundation does more than just support the physical act of blacksmithing; it also lays the groundwork for creativity and innovation. Without a strong understanding of the basics, one could easily find themselves lost in a sea of molten metal and fire.
Anvil mastery begins with knowing the key components involved in blacksmithing. Itâs not merely about hitting a piece of iron with a hammer. Instead, it embodies a blend of artistry and meticulous technique. Engaging with the anvil is akin to a dance where rhythm, timing, and precision come together to create something beautiful.
With that in mind, letâs delve into the intricacies of this world.
Understanding the Role of the Anvil
The anvil isnât just a hefty piece of iron sitting in the corner of the forge. It is a pivotal tool on which the magic of blacksmithing unfolds. Think of it as the steadfast companion of the blacksmithâthe right-hand partner that bears the weight of the creative process.
Key Roles of the Anvil:
- Stability: A solid, heavy anvil provides a stable surface that can withstand the force of hammer strikes. Any wobble or instability can disrupt the whole workflow.
- Shape: The anvil comes with different shapes and forms, each designed for specific tasks. Whether itâs a flat area for general shaping or a horn for bending, understanding these features increases your versatility.
- Heat Distribution: The material of the anvil distributes heat effectively, allowing for adjustments as metal cools down. Manipulating this aspect can greatly influence the outcome of the forging process.
Mastering the way you use the anvil can streamline your work and elevate the quality of your output. As you get comfortable with the various forms and functions, it transforms from just an object into an extension of your will.
Historical Context of Blacksmithing
Blacksmithing is an ancient discipline, steeped in history and tradition. Understanding this context is not only fascinating, but it also informs your practice. This craft has roots stretching back thousands of years, tying together cultures and communities through a shared need for tools, weapons, and ornamental design.
From ancient civilizations to the modern age, blacksmithing has adapted but retained its core essence.
Significant Historical Points:
- Roman Innovations: The Romans advanced blacksmithing techniques, leading to better iron implements. They perfected the smelting process, which allowed for the mass production of high-quality tools.
- Medieval Fusion: During the Middle Ages, blacksmiths played crucial roles in society. They transformed metal into necessary goods, often becoming vital to local economies.
- Renaissance Revival: This period saw a resurgence in craftsmanship and artistry, where blacksmithing included ornate designs alongside functional work, elevating the smith's status in society.
The legacy of blacksmithing reinforces its importance in todayâs crafting endeavors.
"A blacksmith is not only a laborer but a storyteller, crafting histories with each strike of the hammer."
Selecting Mastery Materials
Selecting the right materials forms the backbone of any blacksmithing project. Not only do the materials dictate the quality and durability of the final piece, but they also shape the forging process itself. Each metal type has its unique properties, handling characteristics, and aesthetic qualities. This necessitates that the craftsman pays meticulous attention to the selection phase, as the right choices can significantly influence one's success or failure.
Types of Metallurgical Origins
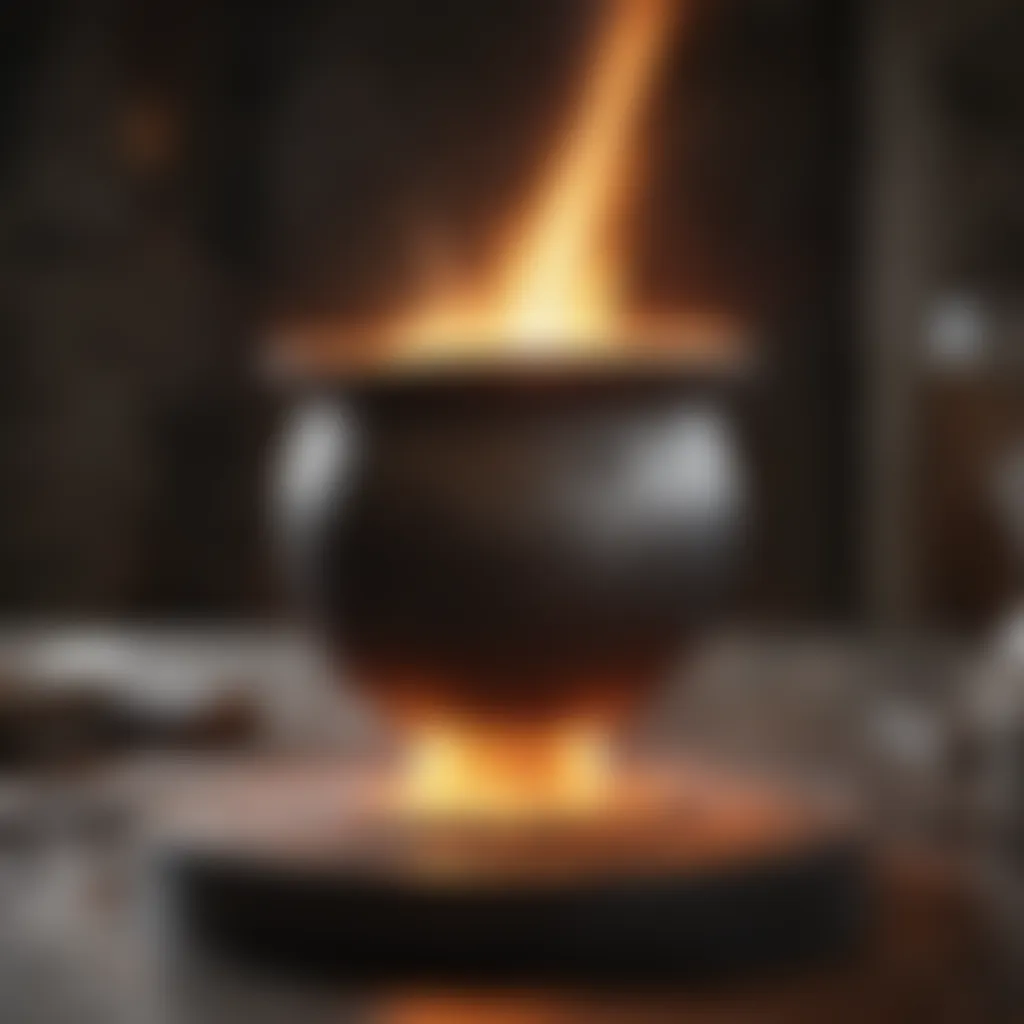
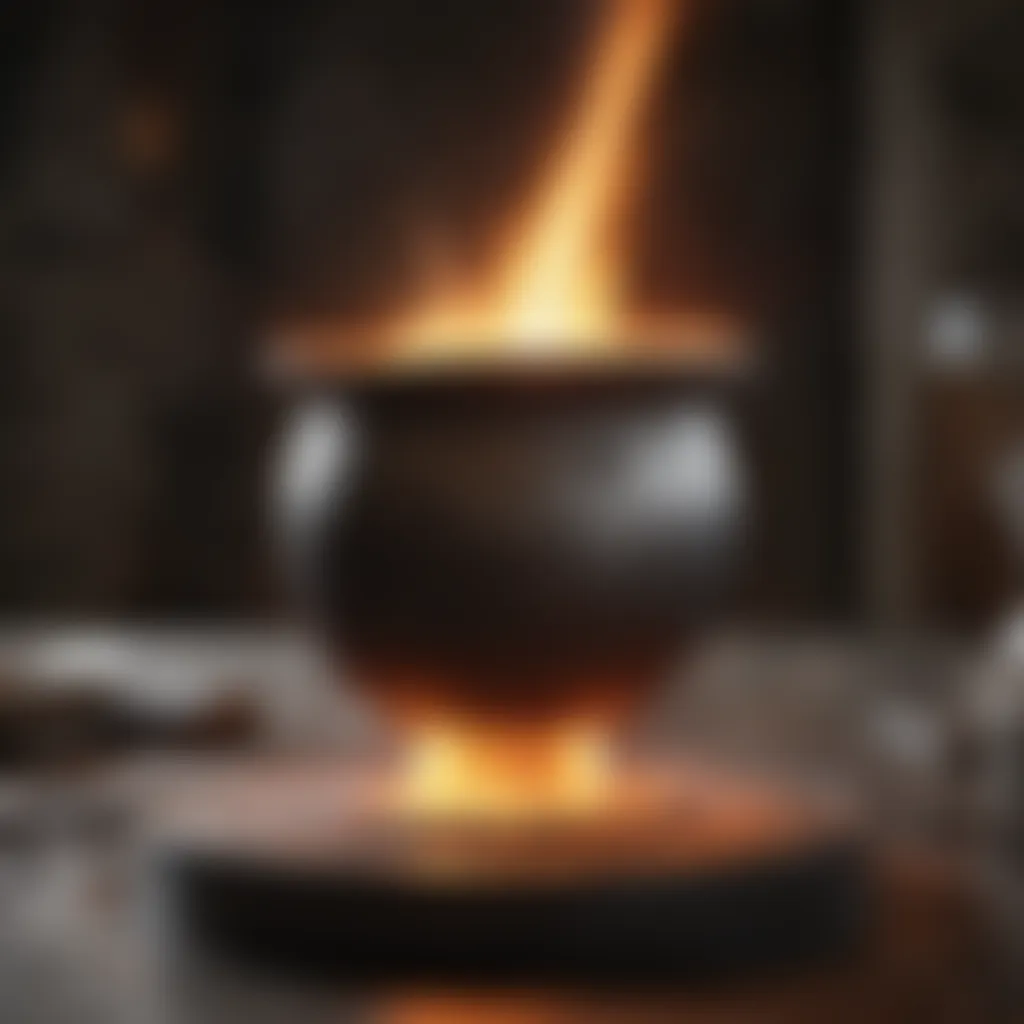
When we talk about metallurgical origins, we reference the different sources and types of metals that can be utilized during forging. Letâs dive into this important detail:
- Steel: This is often the primary material of choice for many blacksmithing tasks. Steel is a blend of iron and carbon, and its characteristics can be modified further through different processing techniques. High-carbon steel offers sharper edges, while low-carbon steel allows for ease of manipulation.
- Cast Iron: This has a higher carbon content and is more brittle compared to steel. While it is suited for certain applications like cookware, it is not the best for tools or weapons where resilience is necessary.
- Aluminum and Bronze: Though less traditional, these metals can be used in modern blacksmithing. Aluminum is lightweight but not as strong, making it useful for specific applications. Bronze, with its corrosion resistance and aesthetic appeal, is fantastic for sculptures or decorative works.
- Alloy Metals: These bring together the benefits of multiple metals to enhance properties like strength, durability, and resistance to wear. However, they may require more specialized techniques in their handling.
Choosing the right type of metal sets the stage for what follows, and a solid understanding of metallurgical origins can save one from mishaps down the line.
The Importance of Quality Materials
When embarking on a blacksmithing journey, it cannot be stressed enough how vital the quality of materials is. Quality materials foster better results and contribute to your overall reputation as a smith. Hereâs why:
- Durability: Quality materials lead to products that stand the test of time. Poor-grade metals will yield poor results, resulting in a product that may chip, crack, or bend under stress.
- Forging Ease: High-quality metals are easier to work with. They require less effort to shape and mold, which can mean a smoother forging experience for the smith.
- Aesthetic Appeal: Quality materials usually have superior finishes. Whether itâs through inherent qualities of the metal or the ability to receive a nice polish, a well-crafted item made from quality material often garners more admiration.
- Safety: When forging tools or items that will endure significant stress, using quality materials ensures safety. Low-quality materials can fail unexpectedly, leading to potential injury.
In essence, the mantra of "you get what you pay for" rings true in blacksmithing. Investing time and care into selecting great materials not only benefits the craftsmanship but elevates the final product, ultimately paving the way for an exceptional forging experience.
"The better the materials, the stronger the craft. Quality should never be an afterthought."
In moving towards the next section, itâs critical to appreciate how material selection lays down the groundwork for everything that follows in the blacksmithing process. Taking the time to understand and choose thoughtfully will lead to exquisite creations in the long run.
Critical Techniques for Forging
When it comes to mastering the art of forging, the adage "practice makes perfect" couldn't ring more true. The techniques employed during forging significantly influence the quality and durability of the final product. Every smith, regardless of experience level, must have a firm grasp of several critical techniques that are foundational to producing high-quality pieces. These methods not only refine skills but also foster creativity and an understanding of metalwork in a practical setting.
Basic Hammering Techniques
The essentials of hammering serve as the building blocks of effective forging. Hammering isn't just about swinging a heavy object at a piece of metal; it's a finely-tuned skill that requires precision, rhythm, and an innate feel for the material at hand. To get started, it's essential to master a few basic hammering techniques that can make the forging process smoother.
- Grip and Stance: First off, a solid grip on the hammer with a comfortable stance is crucial. Hold the hammer near the end of the handle, allowing for maximum leverage while distributing your weight evenly between both feet. Your knees should be slightly bent to maintain balance and mobility.
- Swing and Strike: Focus on controlled swings. Start slow to appreciate the weight of the hammer and gradually increase your speed while striking the metal at an angle. Aim for the center of the metal piece to create even spreading, which is vital for consistency in shape.
- Rhythm and Timing: Establishing a rhythm is not just about the mechanics of hammering but also about listening to the resonance of the metal. Each strike should produce a distinct sound, indicating the necessary adjustments you may need to make. As you develop a keen ear, youâll learn to adjust your force and precision accordingly.
"Your hammer is an extension of your hand. Listen to it, and it will guide you through the art of blacksmithing."
These fundamental techniques not only pave the way for better craftsmanship but also make the work enjoyable. As any seasoned blacksmith would tell you, honing your hammering skills can mean the difference between a merely functional piece and an absolute masterpiece.
Advanced Forming Techniques
Once youâve got the basics down, itâs time to elevate your skills with advanced forming techniques. These techniques allow a smith to manipulate metal in more complex ways, fostering creativity and innovation in designs.
- Drawing Out: This technique involves elongating a piece of metal without losing its overall mass. By repeatedly hammering at the ends while maintaining a steady heat, a smith can create elegant shapes, perfect for decorative pieces or handles.
- Upsetting: The process of upsetting thickens the metal in a specific area, which is particularly useful for creating a more robust section, such as a hammer head or a anvil face. It involves heating and then hammering downwards to compress the metal rather than stretching it.
- Bending and Twisting: With the right amount of heat and hammer control, bending and twisting can lead to unique structural designs. By working with varying heat levels and applying gentle, graduated pressure, intricate curves, spirals, and other forms can be achieved.
- Tapering: This technique allows for a graceful transition from a wider section of metal to a thinner point, crucial for creating sharp edges on tools or elegant filigree on jewelry. To taper effectively, focus on hammering just the edges, allowing the center to stay thicker, thus creating the desired form.
The advanced forming techniques are not just about altering the shape of metal but about expressing creativity through craftsmanship. They give an artist-like quality to smithing, where each hammer strike adds character to the piece, resulting in a work of art that stands out among the rest.
Mastering these skills will elevate your work and enable you to approach projects with greater assurance. As with any craft, time and patience will yield the greatest rewards.
Heat Management in Forging
Heat management is a crucial pillar in the landscape of blacksmithing. Properly controlling heat not only ensures that the metal works effectively but also directly impacts the quality of the finished product. A well-managed heat profile can spell the difference between a forged piece that lasts generations and one that crumbles at the first sign of stress. If you're diving into the world of forging, grasping how to manipulate and maintain heat will undoubtedly arm you with the tools necessary for an exquisite outcome.
One important aspect to consider is the temperature range specific to different metals. Steel, for instance, can be deformed effectively at temperatures between 1,300 to 2,400 degrees Fahrenheit, depending on the specific type of steel. Too little heat can lead to difficulties in shaping, while too much can cause oxidation or even ruin your creation altogether.
In this sense, heat management becomes an intricate dance that requires attention and awareness. Mastery of this skill implies not only understanding the properties of materials being worked on but also the environment in which you're forging. Factors like wind, humidity, and ambient temperature can play a huge role in how heat behaves in your workspace.
"When you grasp the art of heat management, you don't just shape metal; you mold destiny."
Understanding Temperature Impact
Temperature impacts metal more than you might realize. Think of it as a simmering pot of soupâthe right temperature transforms raw ingredients into a delightful dish. Similarly, in forging, the correct heat determines how the metal's crystalline structure aligns, which in turn influences the durability and appearance of the final piece. Heating metal causes it to expand; different metals expand and contract uniquely and in varying degrees. For example, the expansion rate of aluminum is higher than that of carbon steel, affecting how you manipulate these two materials in tandem.
Moreover, the cooling process is equally pertinent. A slow cool can lead to a softer final product, ideal for tools and knives, while quenching hot steel in water leads to hardening, making it ideal for blades. This vital step can dictate the way your creation will serve its purpose.
One thing to keep in mind is that overexposure to heat can lead to undesirable effects known as "burnt" areas, signaling that part of the metal has been weakened. When forging, always remain vigilant of heat application and movement.
Tools for Maintaining Heat Consistency
Keeping a steady temperature while forging is akin to maintaining the perfect oven temperature when baking; a slight fluctuation can alter the desired outcome.
- Forges: The heart of any blacksmithing operation, forges come in various forms, each serving a unique purpose. A coal forge uses solid fuel, while gas forges are more manageable. Both should be operated with focus to maintain consistent heat.
- Thermometers: Digital thermometers or infrared pyrometers allow for instant readouts, giving precise temperature readings without guessing. This technology helps gauge the heat accurately without the need to touch the metal.
- Firebricks: These insulate heat, ensuring that the forge reaches temperatures needed for effective shaping. They help maintain an ambient temperature thatâs crucial for a consistent working environment.
- Heat Reflectors: Using reflective materials around your working area can help retain heat and direct it to the metal piece without the use of excess fuel or alarming fluctuations.
- Water Quenching Tanks: Having a shoulder-wide container filled with water or oil for quenching allows blacksmiths to quickly adjust temperatures post-heat application. However, using these requires careful methodology to avoid thermal shock.
Ultimately, it is a blend of technique, experience, and the right tools that allows a smith to weave magic with metal. With practice and attentiveness to heat management, the craftsmanship will resonate through the clarity of the finished piece.
Safety Precautions and Practices
In the realm of blacksmithing, a craft that marries art with endurance, prioritizing safety cannot be underscored enough. Engaging with fire and heavy metals, every smith must adopt safety precautions and practices that serve not just to protect, but to enhance oneâs creative journey. Without a solid foundation in safety, the riveting experience of forging could quickly spiral into a hazardous ordeal.
These precautions encompass everything from the right gear to establishing a workspace that promotes diligence and care. A thoughtful approach minimizes risks, fostering not just your health but also allowing your artistry to shine through a worry-free engagement with your craft.
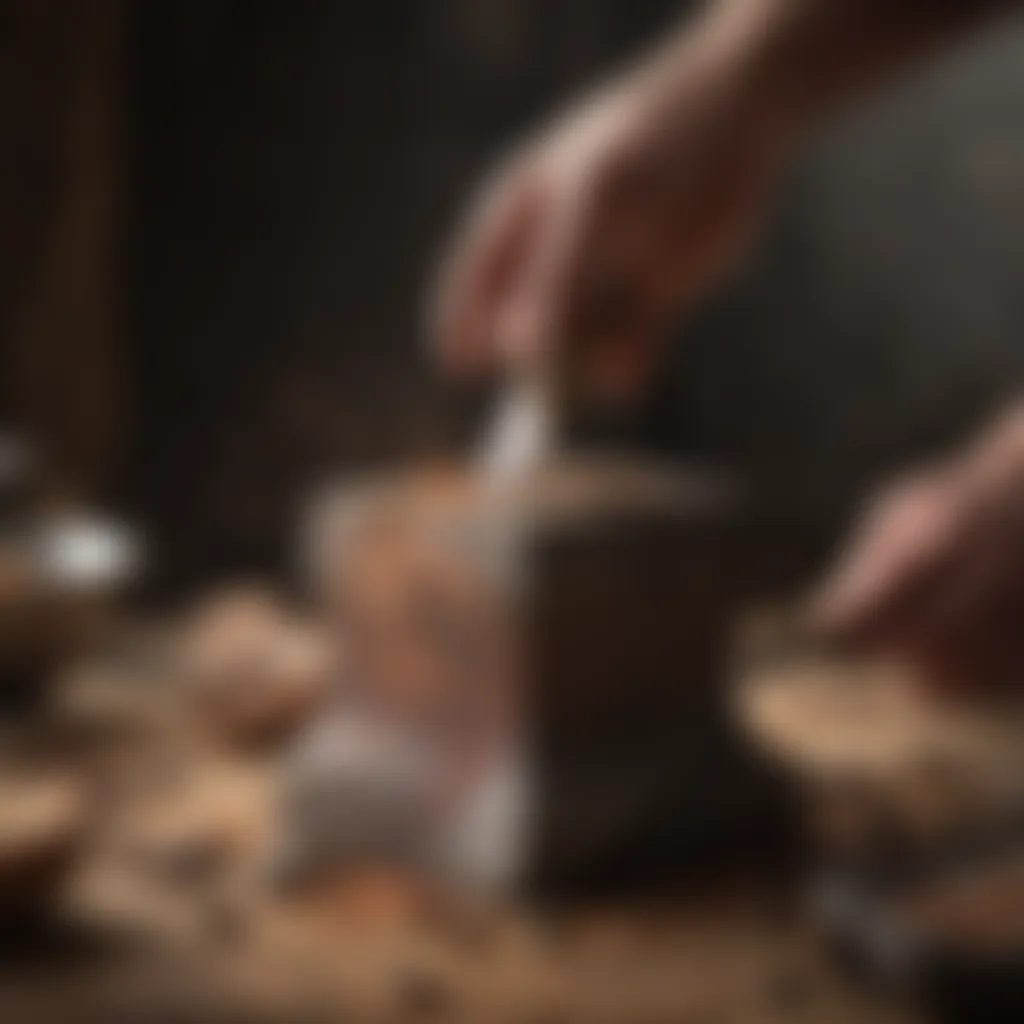
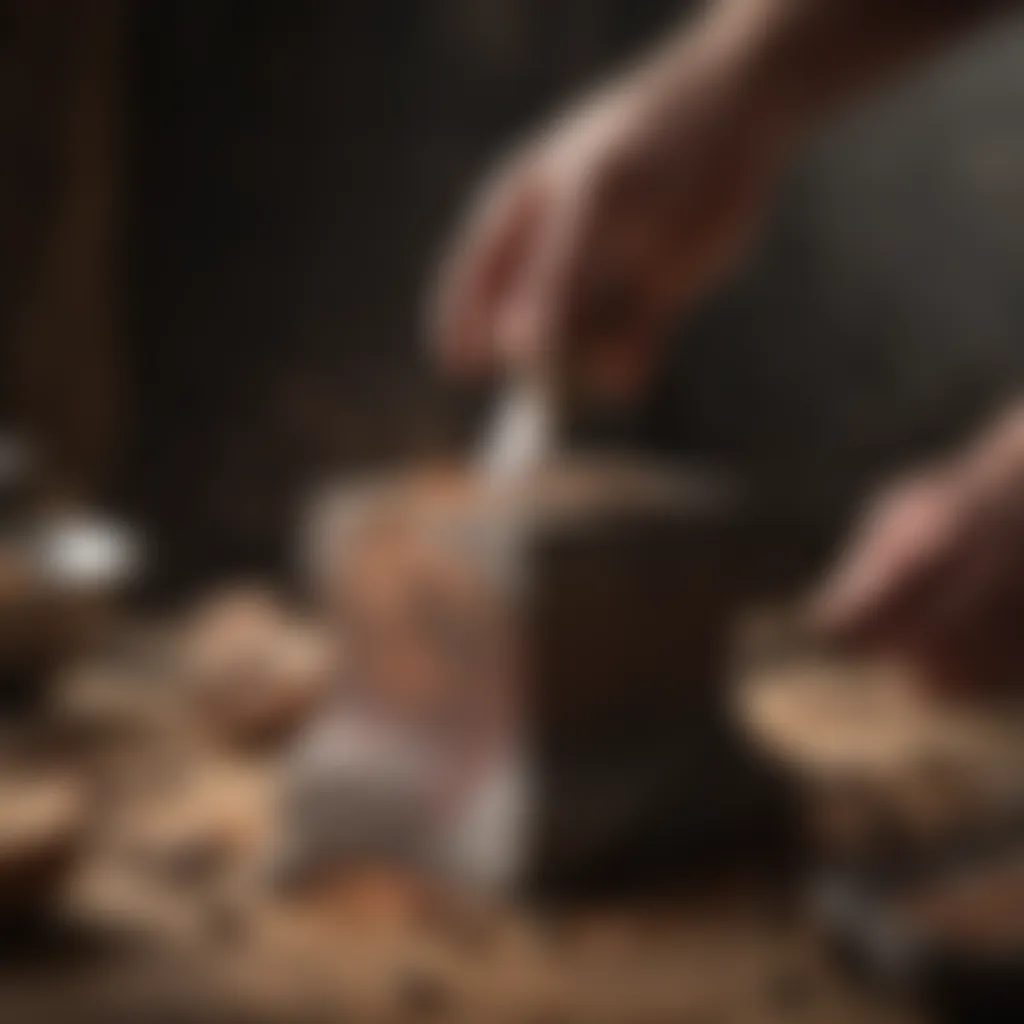
Essential Safety Gear
When it comes to blacksmithing, the importance of essential safety gear cannot be overstated. Just like a painter needs brushes and a musician requires instruments, a blacksmith must arm themselves with protective equipment that safeguards against the myriad hazards of the forge.
Here are key pieces of gear you should splurge on:
- Safety glasses: Protect your eyes from flying sparks and debris. Opt for tinted ones if youâll be working with bright flames.
- Heat-resistant gloves: These will shield your hands from burns while still allowing you to manipulate hot metal with some dexterity. Avoid those flimsy cotton ones.
- Steel-toed boots: Heavy pieces of equipment can take a toll if they drop on your feet. Steel-toed boots help prevent injuries in such instances and add grip on slippery surfaces.
- Apron: A leather or flame-retardant apron can safeguard your clothing and skin from sparks and sharp edges. Choose one that fits comfortably.
- Respirator: When grinding metal, a high-quality respirator will help protect your lungs from harmful dust and fumes. Donât take this lightly.
Investing in this protective equipment not only enhances your safety but also improves your confidence at the anvil.
Best Practices for a Safe Workspace
Creating a safe workspace is akin to laying the groundwork for any successful project. The forge shouldnât just be a place of workâit ought to be a haven for creativity and safety. Here are several practices to cultivate the workspace you can rely on:
- Decluttering and Organizing: Maintain a clean work area. Clear any debris that could trip you up and keep essential tools and materials within armâs reach.
- Proper Ventilation: A crowded workshop with standing fumes can lead to long-term health issues. Ensure adequate airflow, be it naturally through windows or using fans.
- Emergency Preparedness: Have fire extinguishers and first-aid kits accessible. Know the layout of your workspace like the back of your hand. Think through the worst-case scenarios and plan accordingly.
- Lighting Considerations: Good lighting helps prevent accidents. Ensure that every corner of your workspace is well-lit, particularly near hot zones or where fine work is required.
- Regular Maintenance of Tools and Equipment: Inspect your tools regularly. A worn hammer or cracked tongs can lead to disaster. Replace them before they let you down.
Implementing these best practices translates into a workspace that respects the delicate balance of forging art and safety, enabling you to hammer away the day without a second worry.
"Safety is not a gadget but a state of mind."
This sentiment rings true in blacksmithing. To hone your craft effectively, itâs essential to integrate safety into every aspect of your forging practice, from how you equip yourself to how you organize your environment.
Understanding Design Principles
Crafting with an anvil is not merely about heating, hammering, and shaping; itâs also about understanding the design principles that govern every project. The beauty of blacksmithing is that it intertwines functionality with artistry. A thoughtful design not only enhances the practical use of the forged piece but also its visual appeal. When you approach a forge project with a keen eye for design, you not only elevate your own workmanship but also respect the rich tradition passed down through generations of blacksmiths.
Functionality vs Aesthetics
Striking the right balance between functionality and aesthetics is key. Think of a simple nail. It must hold together materials with strength and reliability. Yet, even the simplest item can be crafted with flair. An oddly shaped nail, perhaps with an intricate head, becomes more than just a utilitarian object; it turns into a piece of art. Prioritizing functionality means focusing on how well it serves its purpose, while focusing on aesthetics means paying attention to lines, shapes, and finishes that make the piece appealing to the eye.
When designing, consider the following elements:
- Purpose: Define what the item is intended for and how it will be used.
- Shape: The silhouette should communicate its function while maintaining an artistic appeal.
- Textures: Distinct finishes can add depth; rough or smooth varied textures can evoke different feelings.
- Proportions: Keep in mind that balance is essential; that one element may dictate the presence of another.
A forged item can be a tool, a decorative piece, or a blend of both. A good design process asks the question: "How can this be beautiful and useful simultaneously?"
Planning Your Forge Project
Before you strike your first blow, thoughtful planning sets the stage for a successful forge project. Diving in without a clear direction could lead to wasted materials and unproductive time. Start by making sketches. Visualizing your ideas on paper can clarify your aim and highlight potential design flaws early on. Follow these steps for effective planning:
- Research: Gather inspiration from various sources, including books and online platforms like Reddit or Facebook.
- Sketches: Create rough drafts of your envisioned piece, considering both its shape and usage.
- Select Materials: This ties back into selecting master materials, ensuring you're using the right kind for your desired outcome.
- Prepare Tools: Ensure all your toolsâfrom hammers to tongsâare ready for action before you start.
- Safety First: Always keep safety precautions in mind.
Careful planning paves the way for avoiding mishaps and encourages creativity. Each project teaches a lesson, and reflecting on what works versus what doesn't will only sharpen your skills further.
"Designing a piece is a conversation between its purpose and its form, a meeting of mind and material."
Cultural Significance of Forging
Understanding the cultural significance of forging effectively unravels the role blacksmiths play across various societies. It transcends mere metalwork; it's about tradition, communal ties, and a way to channel creativity. From ancient days to modern times, forging has often been regarded less as an occupation and more as an art form vital to the community's fabric.
Blacksmithing in Different Cultures
Across diverse cultures, blacksmithing has carried different meanings and values. For instance, in Japan, the craft of sword-making has deep roots that go back centuries. The katana, known for its beauty and craftsmanship, symbolizes honor and bravery. Artisans use unique techniques passed down through generations, showing that blacksmithing isnât just about making tools; itâs about creating cultural artifacts that reflect historical significance.
In contrast, in many African communities, blacksmiths are revered as the gatekeepers of technology. Their ability to craft tools used in agriculture or weaponry resonates deeply within these societies. They often hold ceremonies that celebrate their craft, highlighting the communal respect and recognition they receive.
- Japanese Culture:
- African Cultures:
- Katana making as a revered art.
- Symbolizes honor and craftsmanship.
- Blacksmiths as technological leaders.
- Craft celebrated through communal ceremonies.
Thus, blacksmithing can be seen as a custodian of collective memory, preserving the stories, beliefs, and norms of each culture, while adapting to the changing tides of time and technology.
Mythology and Folklore Surrounding Smiths
Blacksmiths occupy a unique place in mythology and folklore around the globe. They are often portrayed as magical figures with an intimate relationship with fire and metal. In many cultures, stories abound about gods or legendary heroes who forge powerful weapons. For example, in Greek mythology, Hephaestus is the divine blacksmith who created weapons for the gods, signifying the raw power associated with metalwork.
In Norse tales, Wayland the Smith stands out as a character with incredible skill, embodying themes of revenge and creation. This suggests that blacksmiths are not mere tradespeople; they are interwoven into the narrative of human existence, representing authority, creation, and even transformation.
"To forge is to create; it binds a craftsmanâs soul to the very metal he shapes, linking generation with generation through shared stories and legends."
Through these narratives, we see how blacksmiths are not only important for their tangible outputs but also for what they represent symbolically in their respective cultures. They teach us about resilience, creativity, and the magical connection between humanity and craftsmanship. Their art is, therefore, steeped in layers of meaning that extend far beyond the blacksmith shop or forge.
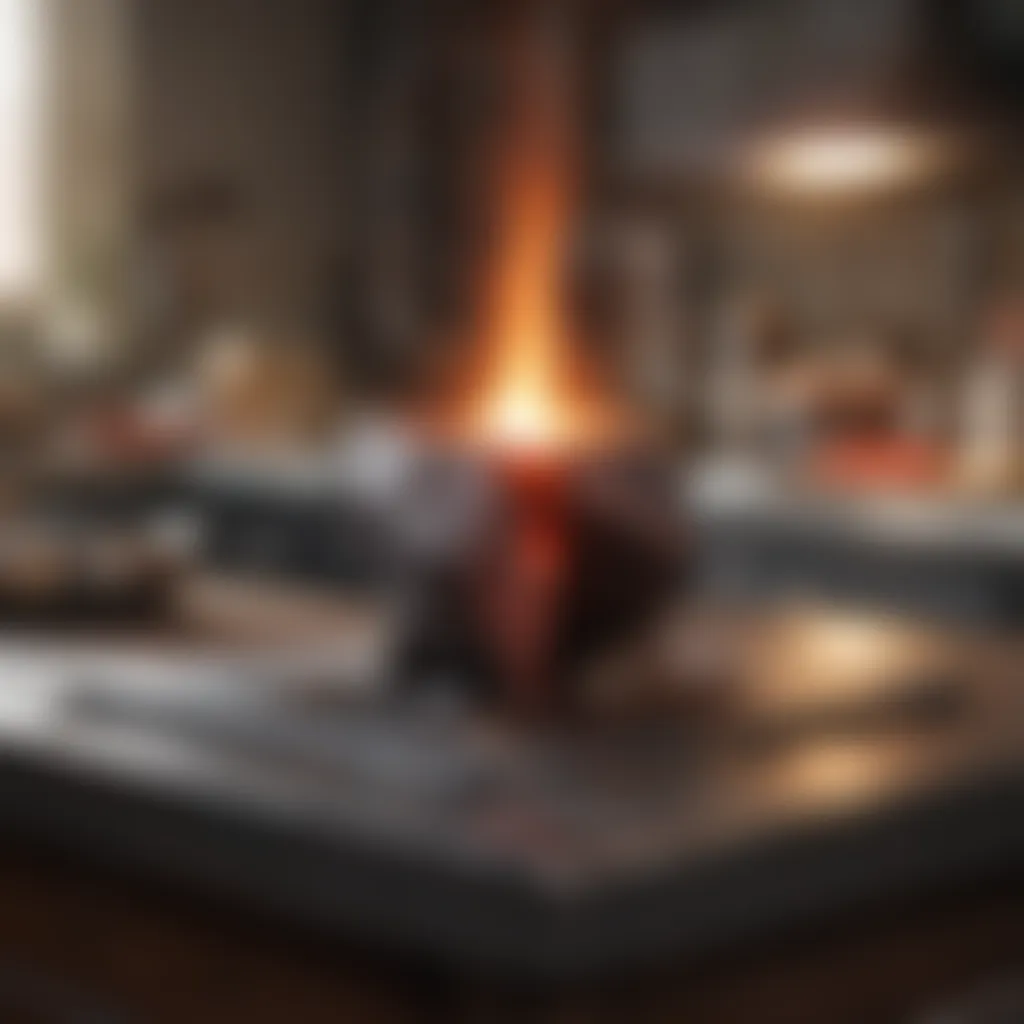
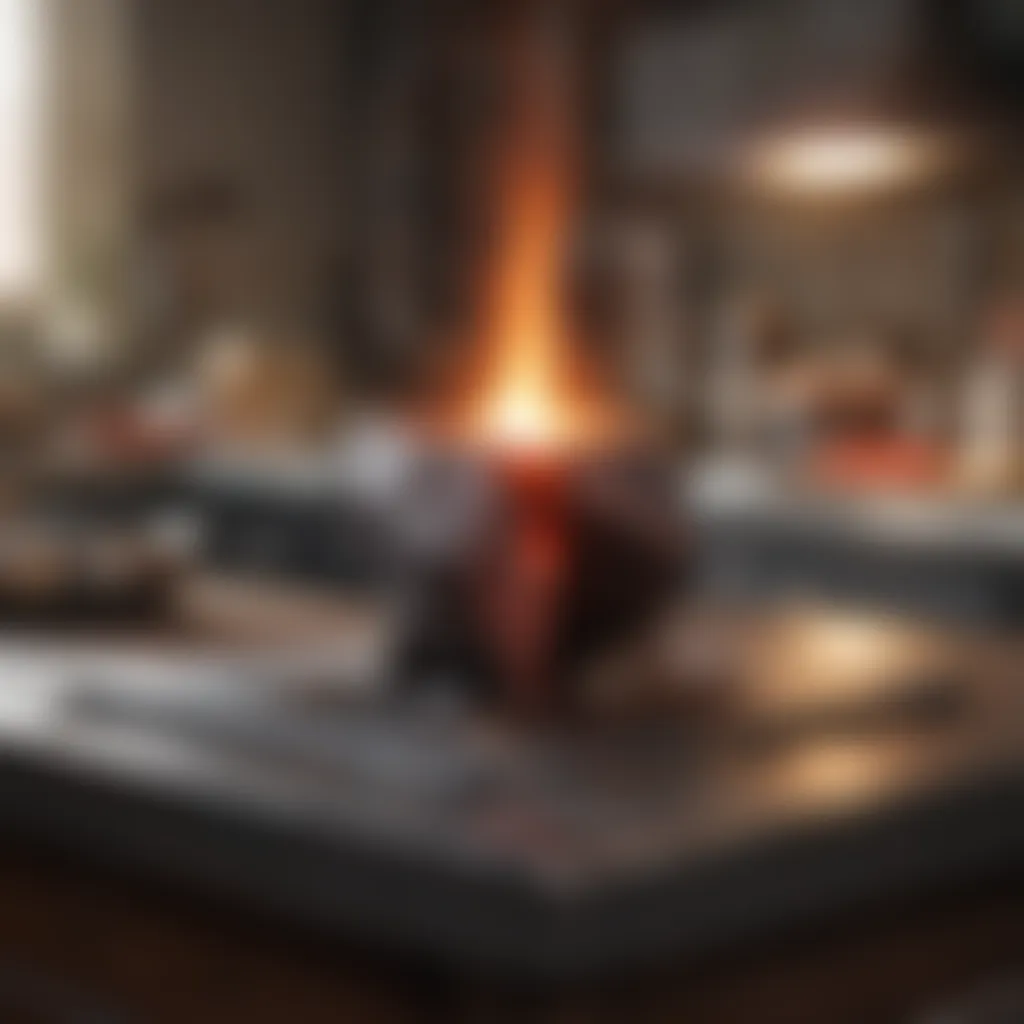
Evolving Techniques and Innovations
In the world of blacksmithing, just like in any other craft, remaining static is not an option. The realm of forging is one of constant evolution, marked by innovative techniques that push the boundaries of what can be created with an anvil. Evolving techniques and innovations are not merely whims of the craft; they embody the spirit of improvement and adaptation. As materials change and methods advance, blacksmiths must be poised to refine their skills and embrace tools that enhance their artistic expressions.
Adapting Modern Tools
To navigate the seas of modern blacksmithing, mastering the use of contemporary tools can make a world of difference. Todayâs blacksmiths have access to technology that past artisans could only dream of. For example, power hammers can increase production speed significantly while reducing physical strain. This is not to say that traditional hand tools should be cast asideârather, the blending of both old and new enriches the blacksmithâs arsenal.
Benefits of Adapting Modern Tools:
- Increased Efficiency: Fast-paced work environments demand tools that can keep up without sacrificing quality. Modern tools cater to this need, like the propane forge, which heats metal quicker than a traditional coal forge.
- Reduced Physical Toll: Tools such as hydraulic presses lessen the strain on a blacksmithâs body, allowing for longer hours of creation without the fatigue associated with manual labor.
- Improved Precision: CNC machines, when integrated into the forging process, facilitate high levels of precision that would be nearly impossible when relying on handwork alone.
However, itâs vital not to lose the essence of blacksmithing. Combining the old-world craftsmanship with new technology captures the spirit of innovation while preserving the heart of the craft.
Sustainability in Forging Practices
The conversation around sustainability is not a fleeting trend; it is a call for responsible practices that preserve our environment. As the blacksmithing world evolves, sustainability also needs to find its footing within the forge. The very materials used in crafting, as well as the method of creating them, have significant implications on our ecosystem.
Key Considerations for Sustainable Forging Practices:
- Materials Selection: Opt for recycled metals when possible. This reduces the need for mining, which can be ecologically harmful. Moreover, utilizing local suppliers helps lower the carbon footprint associated with transportation.
- Energy Efficiency: Investing in energy-efficient forges and tools not only reduces electricity bills but lessens the environmental impact. Gas-forged systems can be a great alternative to traditional coal forges, helping to minimize emissions.
- Waste Reduction: Employ methods to recycle scrap metal into new projects. Implementing practices like this not only economizes but also fosters creativity by encouraging blacksmiths to think outside the box.
"The responsibility of a blacksmith today lies not just in creating but also in conserving."
The shift toward sustainability isnât just beneficial for our planet; it also resonates with consumers who are becoming increasingly conscious of where their products originate. Embracing these evolving techniques, both in tools and sustainable practices, ensures that blacksmithing not only survives but thrives in the twenty-first century.
Community and Collaboration in the Craft
In the world of blacksmithing, the adage "it takes a village to raise a child" holds true, but in this case, the child is a craft, and the village is a bustling community of forge enthusiasts. The importance of community and collaboration in blacksmithing cannot be overstated. It shapes the learning environment, influences creativity, and ultimately fosters mastery. Those who tap into these communal resources often find themselves reaching heights they might not have attained solo.
Building connections with other blacksmiths can unveil a trove of knowledge. Whether you're a novice or a seasoned smith, engaging with fellow artisans allows for an exchange of experiences, techniques, and ideas. Each conversation can spark a new idea or solve a pressing issue at the forge. This exchange is not just beneficial; itâs essential. Through collaboration, blacksmiths can innovate, bringing old techniques into the modern age or merging styles from various cultures.
Networking Opportunities for Blacksmiths
Networking holds tremendous power in the journey of becoming a master blacksmith. Finding like-minded individuals who share the same passion can often lead to collaborative projects and ventures. Here are some notable points on networking:
- Local Guilds and Associations: Joining organizations like the Artist Blacksmith's Association of North America (ABANA) can provide a platform for networking. These groups often hold events, exhibitions, and competitions, which naturally become fertile grounds for forging new relationships.
- Online Forums: Communities such as r/Blacksmith on Reddit serve as digital hearths where blacksmiths gather to exchange advice. Participation in discussions can fill knowledge gaps and offer fresh perspectives on challenges faced by your peers.
- Social Media Groups: Facebook groups tailored to blacksmithing provide a virtual space for connection, whether you're asking for a technique or sharing your latest creations. Engage by commenting on posts or even live demonstrations that some members conduct.
Networking shouldnât be one-sided. Offering help to a peer or demonstrating a skill can solidify your place within the community. Think of it as a dance; mutual respect and acknowledgement only enhance the experience.
Workshops and Learning Environments
Workshops and learning environments are pivotal in shaping the skills of both emerging and established blacksmiths. Participating in workshops can offer hands-on experiences that are often hard to match in solitary practice. These gatherings foster a supportive atmosphere, where learners of all levels can explore the intricate nature of forging.
Hereâs why engaging in workshops is vital:
- Structured Learning: Unlike self-directed learning, workshops provide guidance and structured learning paths. Skilled instructors can tailor lessons based on participant levels and common pitfalls attendees might encounter.
- Access to Tools and Resources: Many workshops are hosted at established forges, which allows participants to use high-quality equipment that they might not have access to at home. This hands-on experience is invaluable.
- Community Building: Beyond sharpening skills, workshops serve to create bonds among participants. The shared experience can translate into long-lasting friendships, with attendees continuing to meet after the workshop concludes.
Attending workshops amplifies creativity, fuels inspiration, and often leads to collaborative projects after the initial class ends. Think of it like planting seeds of knowledge and connection; over time, those seeds grow into a lush garden of innovation.
"The forge can be a lonely place, but when we gather, sparks fly vastly brighter."
Through community engagement and collaboration, the journey into the realm of blacksmithing becomes far more enriching and fulfilling. In every hammer strike, in every conversation, there lies potential for growth, artistry, and mastery.
Documenting Your Craftsmanship
In the world of blacksmithing, where art meets function, the craft transcends mere creation. Every artisan has a story, an evolution, and documenting that journey is crucial. The act of keeping track of oneâs work is not just about recording achievements; it is a gateway to reflection, innovation, and marketing. It ensures that every painstaking blow of the hammer, every moment spent at the anvil, is captured in a manner that speaks to the heart of craftsmanship.
The Importance of Keeping Records
Documenting your work has profound implications for personal growth and skill enhancement. Keeping meticulous records allows a smith to:
- Track Progress: By maintaining a journal, one can see how techniques evolve over time. It is often astonishing to look back and see how far you've come, how your grip on that hammer has strengthened, or how your design choices have become bolder.
- Identify Patterns: Recognizing what worked and what didnât is essential. Maybe that particular heat treatment yielded the perfect hardness in steel. Without notes, such valuable insights could be lost in the fog of memory.
- Facilitate Sharing Knowledge: For those who aim to teach or share their craft with others, a well-documented history of techniques, designs, and failures can serve as a teaching tool, fostering a sense of community among fellow artisans.
You might wonder, how best to keep these records? Several approaches can be taken:
- Journals: A simple yet effective method. Writing down daily activities, sketches of designs, or thoughts on new techniques can make a big difference.
- Digital Documentation: Using apps or software geared toward crafting can streamline this process. They often come with features allowing photographs and detailed descriptions to be saved in one place.
- Blogs or Online Platforms: Sharing your journey through blogging can connect you with others in the community. Platforms like Reddit or Facebook can also serve as great spaces for sharing ideas and getting feedback.
Photography and Portfolio Development
A picture speaks a thousand wordsâor so the saying goes. In forging, a well-captured photograph can mean the difference between a piece being lost in obscurity and being celebrated as a hallmark of craftsmanship. Thus, investing time in photography becomes paramount for a blacksmith.
To build a compelling portfolio, consider:
- Lighting: Natural light works wonders. Position your pieces in areas where soft sunlight can illuminate their finest features.
- Background: A cluttered backdrop can detract from your work. Aim for simplicity; a neutral backdrop lets your craftsmanship shine.
- Detail Shots: Close-up shots that capture intricate detailsâlike the texture of the metal or the finish of the surfaceâcan convey more than the best words ever could.
When showcasing your work, using platforms like Instagram or Pinterest can widen reach and draw appreciation. Regularly updating your portfolio not only showcases your evolution but can attract possible customers or collaborations within your crafting circle.
âCraftsmanship is a journey, not a destination. Documenting it allows us to cherish every step.â